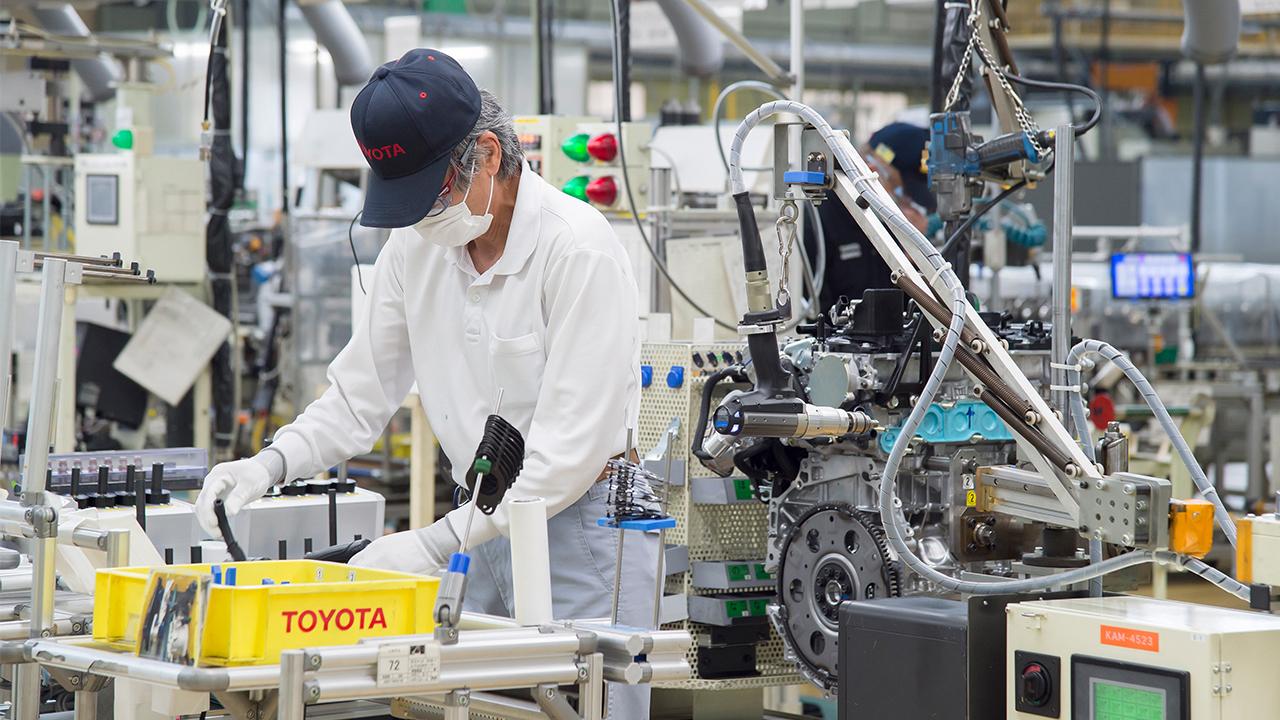
At Toyota's engine plant that is taking on challenges toward carbon neutrality, driving their effort is the concept of kaizen that has long made Toyota, Toyota.
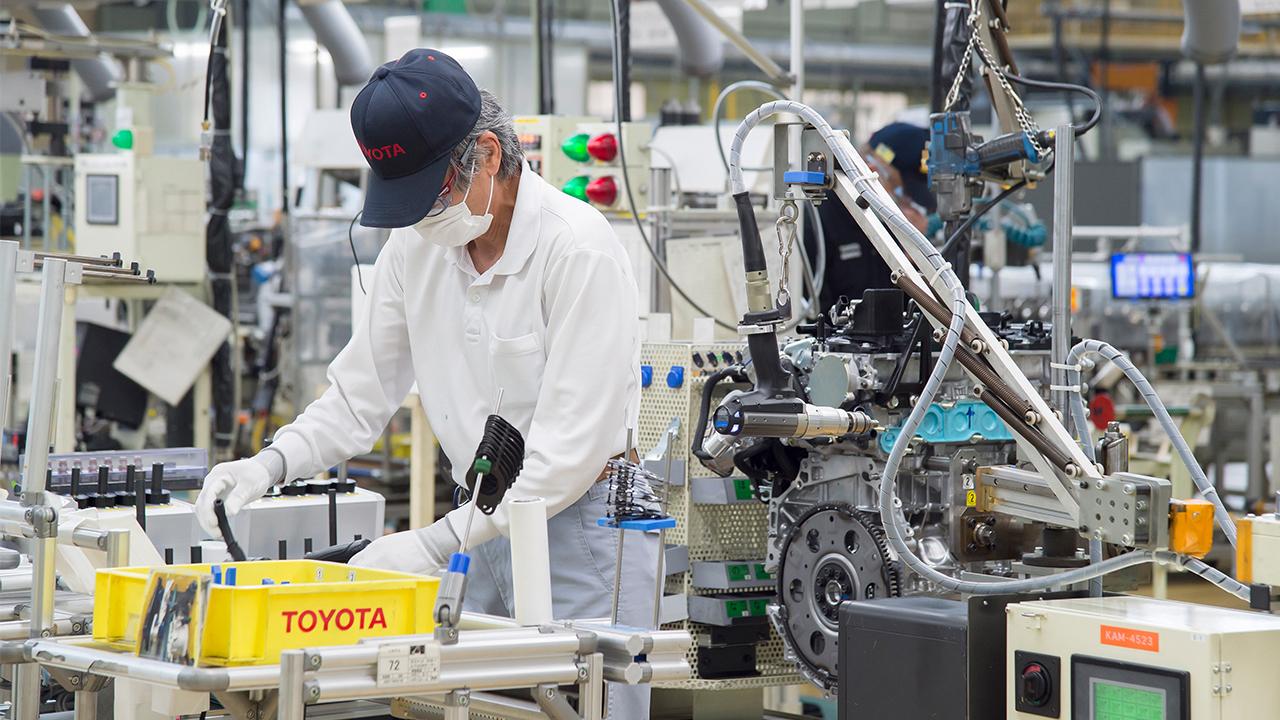
At a press briefing on June 11, Masamichi Okada, Toyota’s Chief Production Officer (CPO) announced that Toyota plants would be accelerating CO2 reduction initiatives, bringing forward the target timing for plant carbon neutrality from 2050 to 2035.

Expecting that various improvements are already being implemented for the schedule to have been brought forward so drastically by 15 years, the Toyota Times editorial team visited engine-producing Kamigo Plant in Toyota City, Aichi Prefecture, to learn of their latest efforts.
Engines have long been rumored to be “on their way out” as fossil fuel-consuming relics that have no place in a carbon neutral society. So, how is this plant preparing for such a future? What the Toyota Times editorial team witnessed was a number of improvements that are transforming the plant’s landscape.
Engine plant producing 1.33 million units annually
Hirofumi Matsuoka, Department General Manager of the Engine Production & Manufacturing Engineering Division responded the following when he was first approached about this interview, and asked how the people at Kamigo Plant perceive trends in the automotive industry to move away from combustion engines.
“Until only recently, everyone here was engaging steadily in various kaizen (continuous improvements) activities while thinking, ‘This is a job that at some point is likely to disappear.’
However, we were all greatly encouraged by the news about the vehicle fitted with a hydrogen-powered engine completing the 24-hour endurance race. We all felt excited that this engine and the improvements we have implemented on the production line here could together take us into the future.”
Kamigo Plant is about one hour away from Nagoya Station by expressway, situated 5 km southwest of the Toyota headquarters.

For more than half a century since its opening in 1965, it has been dedicated to engine production. There are currently 3,441 employees at the plant as of June 2021, all of whom are involved in producing a broad lineup of engines from the 1.5L units installed on the Toyota Yaris and JPN Taxi, right up to the 3.5L units fitted in Lexus LS and IS models.
Since 2017, they have also produced engines developed based on the Toyota New Global Architecture (TNGA), a development framework aimed at making ever-better cars. The plant now produces 1.33 million units annually.
As examples of how the company is contributing to the realization of carbon neutrality, Matsuoka showed a manual production line that makes full use of karakuri, a process that does not rely on electricity, and a casting site that has successfully eliminated the need for large-scale equipment.
Human-friendly manual production lines
First stop on the visit was the manual production line known as the “Super Skill” (SS) Line.
Back in 2013, in anticipation of 2020 and the aging of the plant’s workforce, this line was built with the aim of creating a workplace where rehired elderly workers could return to work with enthusiasm and vigor.
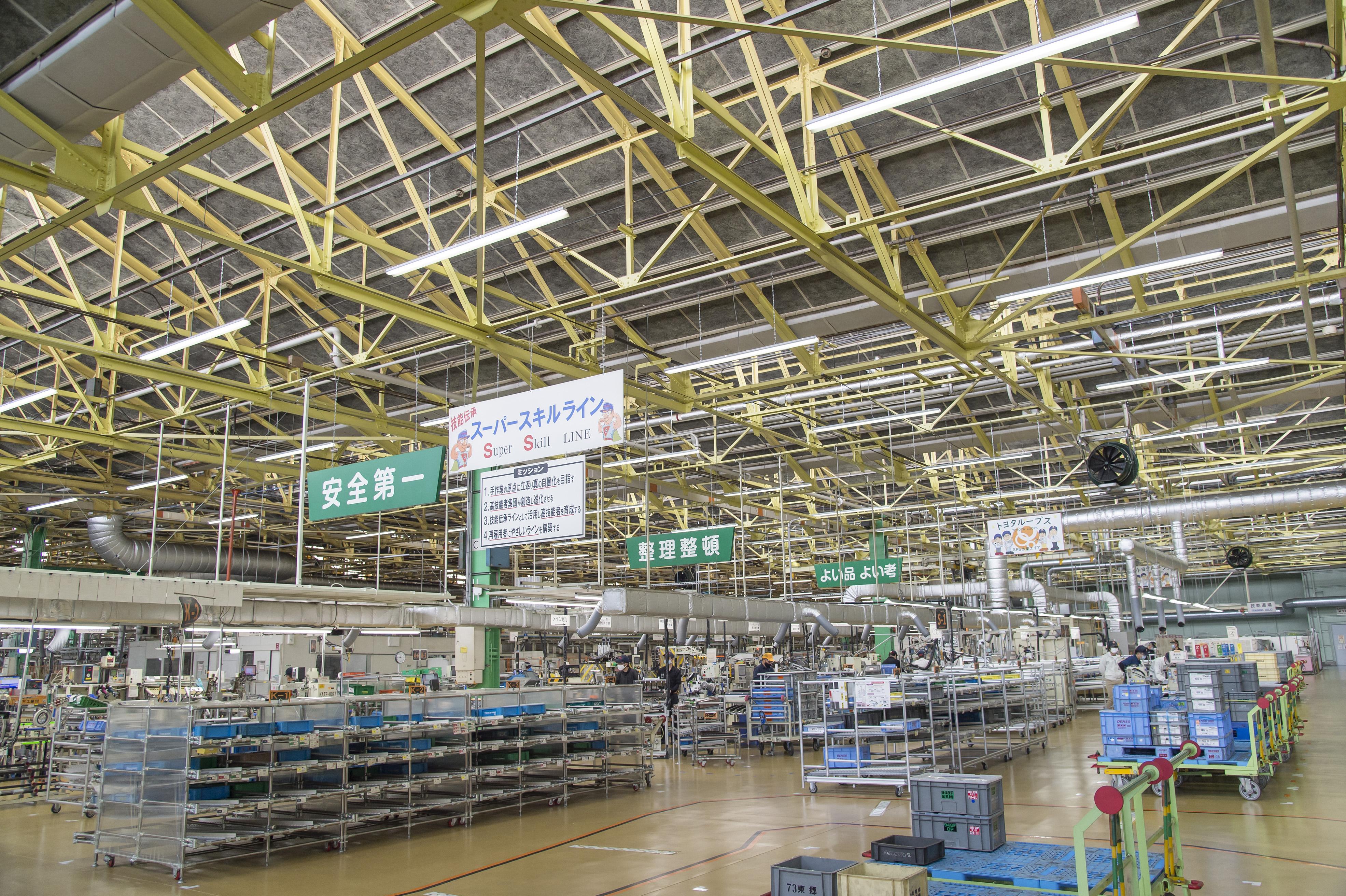
According to Chief Expert Akira Kitada at Engine Manufacturing Division 1, as people get older their physical strength declines, making it harder to work in positions directly connected to the production line. In most cases, therefore, rehired elderly workers would often be transferred to desk-based jobs in the plant in areas indirectly connected to the production line.
The SS Line was devised in order to enable people to work without having to rely on physical strength or electricity, but instead use karakuri mechanisms, which move by using the weight of objects. In so doing, the SS Line sought to ensure that the skills, knowledge, and experience of veteran workers could be utilized to the fullest extent.
When launching the line, kaizen professionals from various divisions at the plant, known as “highly skilled technicians” were brought together to plan and setup the layout for the entire process themselves, from engine assembly to quality inspection prior to shipping. Jigs (auxiliary tools for positioning and fixing components and tools) and tools were also arranged in a way that facilitates line operation.

There are always up to three highly skilled technicians stationed on the line to oversee operations and make improvements to any work processes that appear to be causing difficulty.
The important thing is not to blindly add machines or equipment, but rather to replace them once with simple mechanisms that are based on manual operations.
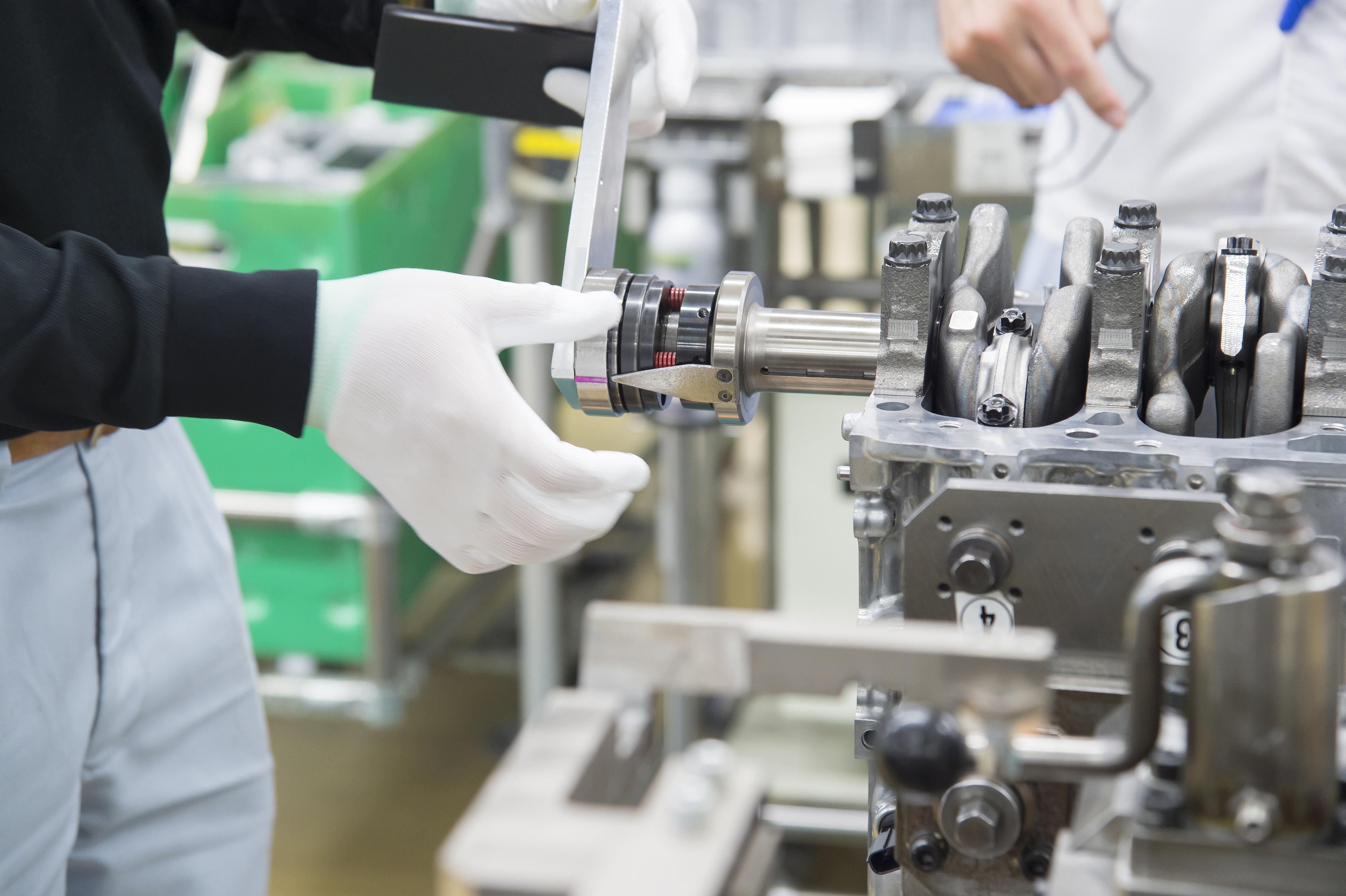
Kazuyuki Nishio, Manager at Engine Manufacturing Division 1, explains the significance of this initiative: “People’s actions are the simplest and least wasteful of all. Having simplified a process and automated it helps to reduce the cost and also makes something less likely to break down, and even when it does break, it is easy to repair.”
Although initially this project was intended for rehired elderly workers, today it is making it easier for a variety of people with physical challenges to work, and it also plays a role in the diversity of the plant.
The line can be said to truly embody the objective of President Akio Toyoda’s Toyota Production System (TPS) to “make someone else’s work easier.”
Improving the “view”
What also makes a lasting impression on the SS Line is the fact that there are few things hanging from the ceiling, which makes for a “better view.” Chief Expert Kitada explains the importance of the view in this way.
“A cramped line leads to lower motivation among the people working there. That is why on this line we have adjusted the heights of chutes so that everyone can see each other’s faces. We can immediately see if there are any processes that have stopped, if the work is flowing properly, and if everything is working normally or if there is an anomaly.”

Another aspect that helps to improve the view is the coverless equipment and machinery.
Engine components are heavy. The cylinder block and cylinder head, which form the framework of the engine, weigh about 20 kg and 10 kg, respectively.

When you need to transfer such parts to another jig, or change their height or direction and then move them to the next process, you usually need equipment capable of applying a large force.
However, this means that lines of sight are blocked by the use of machines with wires to hoist them up, and covers are also required to prevent injuries.
By incorporating karakuri mechanisms, it has been possible to improve these operations so that they can be done with a single touch. Since they can now be moved without applying a large amount of force, safety issues are also solved, meaning that covers are no longer needed.
The “automation trap”
A final example of a kaizen initiative that attempts to simplify and streamline through karakuri mechanisms is a technique to eliminate missing washers on head bolts.
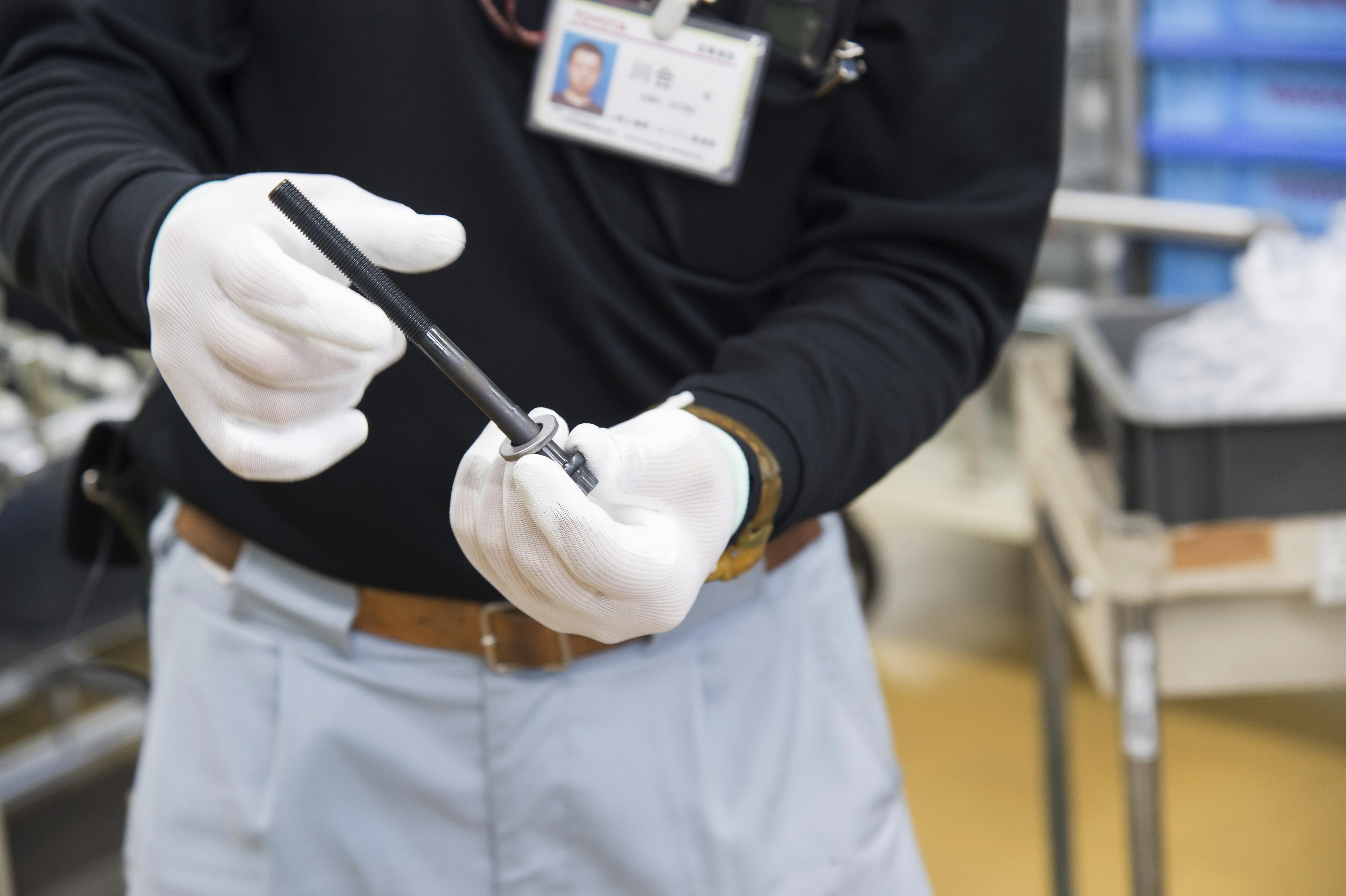
Head bolts are a component used to join the cylinder block and cylinder head, but if someone forgets to attach the washer, the head bolt loosens easily, resulting in an engine that may not run properly.
The jig in the photo below solved the problem of forgetting to fit the washer.
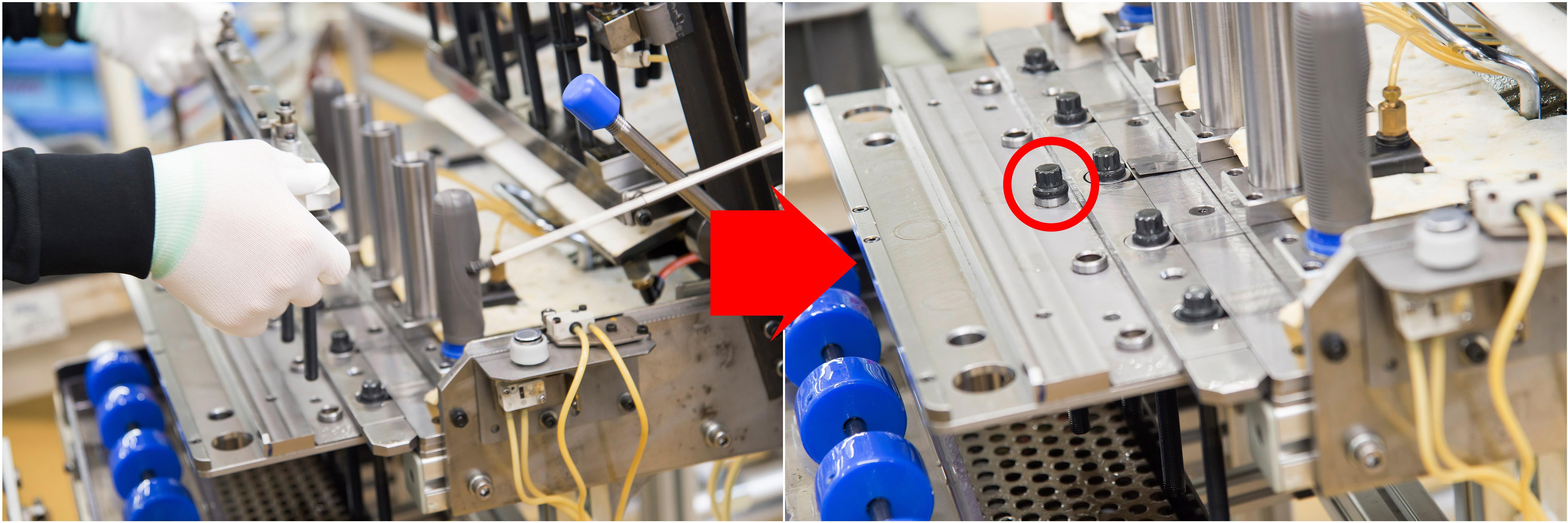
The mechanism is one where the washers and head bolt are set, lifted and fixed on the engine, but if there are no washers it is not possible to grasp the bolts and instead, they remain where they were.
It’s an extremely simple mechanism, but it easily makes anomalies clearly apparent, enabling to prevent mistakes. Matsuoka explained the importance of this mechanism in this way:
“If we tried to do this with devices or equipment it would need either a laser or camera to confirm whether the washer is in place. You would then also need sensors to check that the laser or the camera are also working properly. In other words, it creates a situation where we need to ‘check the checks.’”
Once you start with automation there is no end. The more you do, the more complex something becomes, and both costs and electricity consumption tend to rise. If karakuri mechanisms can be used instead like in this example, it eliminates the need for such checks.
Rather than immediately trying to automate something, sometimes it is better to take a step towards making it simpler or more streamlined. On the SS Line you get a real sense that the knowledge and wisdom of the Toyota workplace is helping to progress towards carbon neutrality.
A process responsible for one-quarter of CO2 emissions
Next on the visit is the casting line, where hot, molten metal is poured into molds and shaped.
In 2020, Kamigo Plant was the third-largest emitter of CO2 among all domestic Toyota plants, after vehicle production Tahara Plant and Tsutsumi Plant.
The reason behind these emissions is because Kamigo is home to the main raw materials shops (processes), which produce metal components using the application of heat, such as casting and heat treatment.
Looking at CO2 emissions in 2018 by process, it can be seen that raw materials actually account for one-quarter of emissions among all Toyota plants. Among all raw materials, the process that is responsible for the largest emissions is casting.
Although casting is a process that uses large volumes of energy in electric heaters and gas, for example, improvements have actually been achieved that have reduced annual CO2 emissions by approximately 1,800 tons, or the equivalent of annual emissions of 600 households.
Tackling the challenge of high-performance engines leads to dramatic reduction in CO2 emissions
It was in 2016 when Kamigo Plant began efforts to launch production of TNGA engines.
In order to realize both high fuel efficiency and high power output, it is essential to achieve world-class thermal efficiency. This required improvements in the cylinder head* cooling functions.
*A major component that affects engine performance and reliability, and which creates the shape of the parts used for intake and exhaust and the combustion chamber.Specifically, this means that the water jacket, through which coolant passes, must pass extremely close to the combustion chamber and exhaust port, where temperatures are highest.
For this purpose, a thin, intricately meshed sand mold (or core) was required. However, using the conventional shell molding process* it was not possible to fill every corner of the metal mold with sand in order to make the cores.
*A process where sand mixed with resin (organic material), which acts as an adhesive, and hexamine, which is a hardening accelerator, is placed in the mold and then baked hard to make the core.
What is more, in this production process the resin mixed into the sand melts as the cores are being made, creating smoke, dust, and a strong pungent odor. These waste materials are carried away via ducts and collected in a deodorizer adjacent to the building to be cleaned, but the height of the deodorizer is equivalent to that of a four-story building.
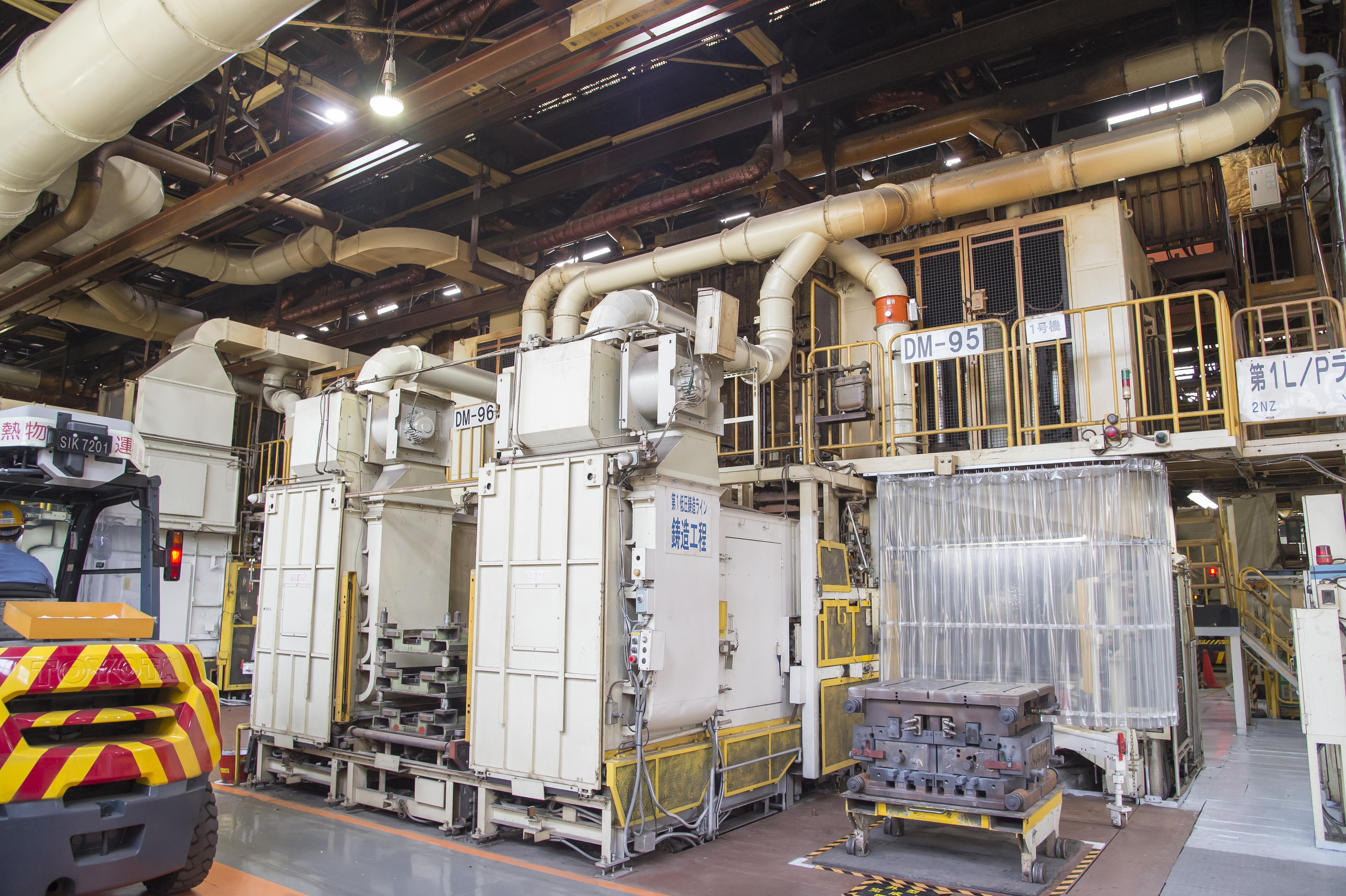
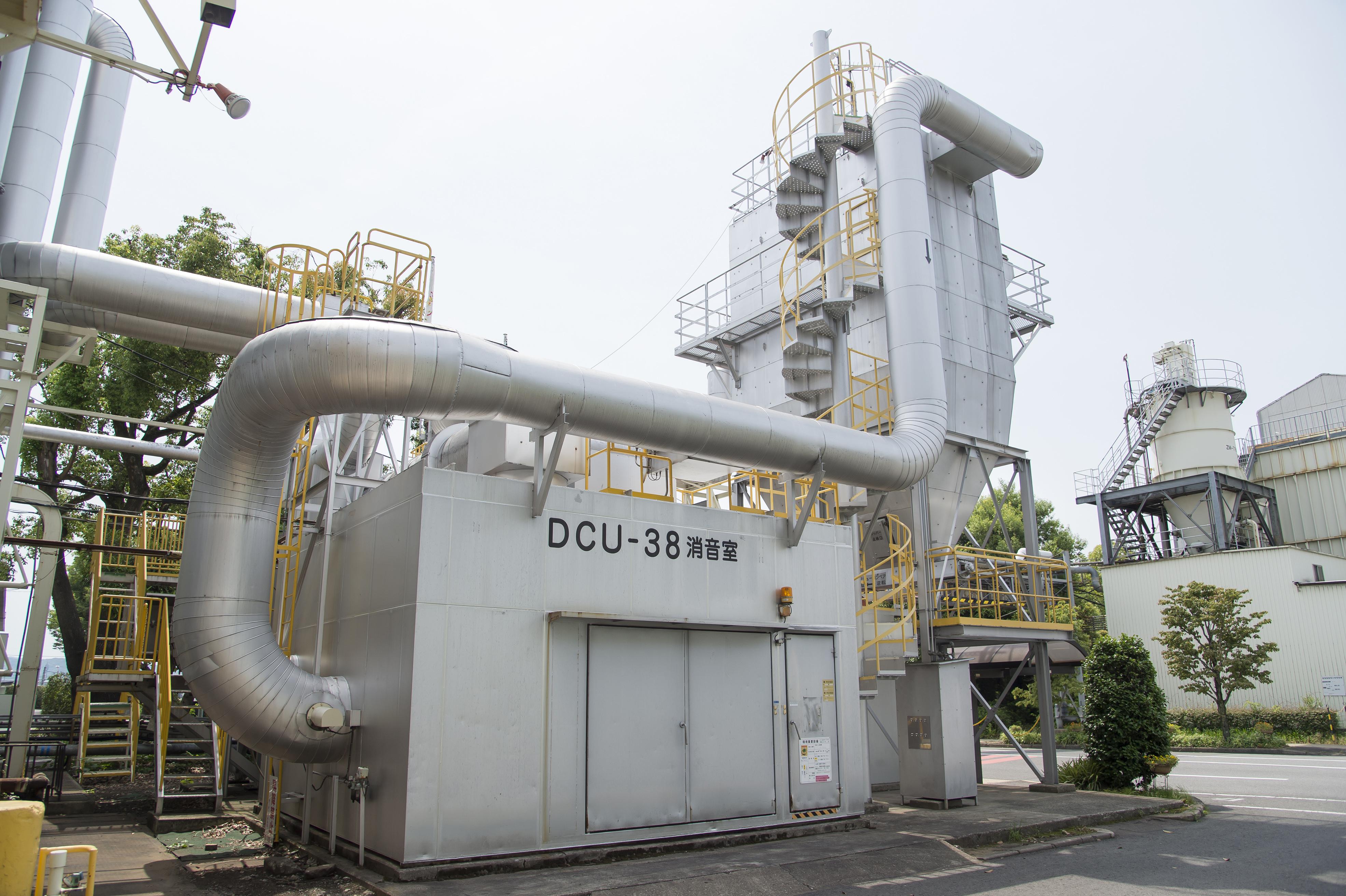
The pumps and fans of this deodorizing equipment require annual electricity usage amounting to 1.2 million KWh.
This is where the method of using inorganic “water glass” as a binding agent for cores was identified for use.
When this water glass and surfactant, a substance that is also used in shampoo, are mixed in with sand, together they create a mousse-like fluffy finish.
Developing a new process that leveraged this property made it possible to spread the sand right through to the very edges of the mold, even in thin, complex-shaped molds. This was the breakthrough that fulfilled the performance requirements for TNGA engines.
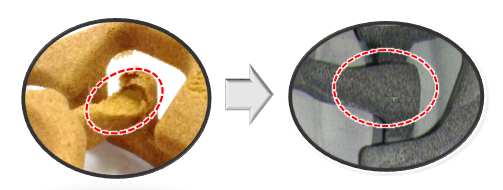

By changing the material used as a binding agent, the amount of smoke generated could be drastically reduced to 1/100th of previous levels and odors reduced to 1/115th. This also eliminated the need for deodorizer ducts, and the amount of CO2 required to produce a single cylinder head could be reduced by approximately 1.8kg.
This new process is being used to produce 1 million cylinder heads for use in TNGA engines manufactured at Kamigo Plant, resulting in an annual reduction of approximately 1,800 tons* of CO2 at Kamigo Plant alone, which is equivalent to the annual CO2 emissions of 600 households.
*Combined value including the effect of casting sand regeneration furnace described below.
Adding the effect in other plants around the world, with the 2.7 million cylinder heads that were produced with this approach, CO2 reduction volume would be 4,800 tons.
Given the dramatic reduction of CO2 emissions, this process is not only being implemented in Toyota plants, but the technology has also started to be deployed outside the company.
Regeneration furnaces capable of being deployed overseas where necessary
The change to the binding agent used in core production has also brought about another change, in the regeneration furnaces used to recycle sand.
These furnaces generally use gas to burn off the organic materials attached to the sand. However, water glass can be separated from sand by simply heating it at low temperatures using electricity, which reduces the amount of energy used.
Until now each building at the plant had required its own enormous 12 m high furnace, but using this new method means that that equipment is a compact 1.5 m in height and one unit can be installed on each production line.
This change has further reduced annual CO2 emissions by 45 tons per line, but the advantages go further than just emissions.
Group Manager Hiroaki Matsuoka of the was the guide to the casting facilities at the plant, and he added this comment about the effects of the changes.
“Until now we always had to collect sand from around the plant in one location, but as the regeneration facilities have been reduced in size it is possible to locate one unit next to each line, which saves on transportation. Also, in the past, it was necessary to build a huge regeneration furnace, even if production scale was not particularly large. However, thanks to now being able to reduce the size of the regeneration facilities, even when deploying them to overseas plants we can just increase the facilities to the extent that processes require, in line with production activities. This also helps us to keep costs down.”
Eliminating smoke transforms plant appearance
As touched on above, simply by changing the binding agent that is mixed with the sand made it possible to eliminate various equipment from the casting line that until then had been considered a standard and requisite feature.
In particular, as a result of the disappearance of the ducts that used to cover the plant ceiling, the new line has become much brighter compared to its previous iteration.
Also, as making the sand into a mousse-like substance means that there is no more flying sand dust and smoke, and pungent odors have also been eliminated, this has made the working environment more comfortable, without the need for masks previously required because of the smoke and smell.
Miyu Okada, an employee who has been working at Kamigo Plant for four years, speaks about her impression of the changes. “Before I was assigned here, I was told that the casting line was dark, dirty, and hard work. However, I have found it to be much brighter and cleaner than I ever expected,” she said.

A change of materials can transform impressions of an entire plant. Initiatives towards carbon neutrality of the casting plant have been accompanied by tangible changes that can be both seen and smelled.
Toyota’s unique philosophy leading to carbon neutrality
This article has shown the wide range of approaches adopted at Kamigo Plant to reduce CO2 emissions, from improvements using karakuri mechanisms to address plant-specific challenges, to innovations in materials and production technologies.
However, none of these initiatives were initially aimed at achieving carbon neutrality.
They were implemented initially to create a “people-friendly” line for people working at the plant, and to realize “cost-friendly” improvements for both the company and customers alike. Each of these initiatives has resulted in an “environment-friendly” approach that will also lead to carbon neutrality.
You could say that the philosophy of kaizen that permeates all areas of Toyota’s production sites is connecting through to carbon neutrality.
Kamigo Plant is the mother plant for global engine production and has a mission to drive global kaizen initiatives, which continue ceaselessly towards an envisioned carbon-neutral future.