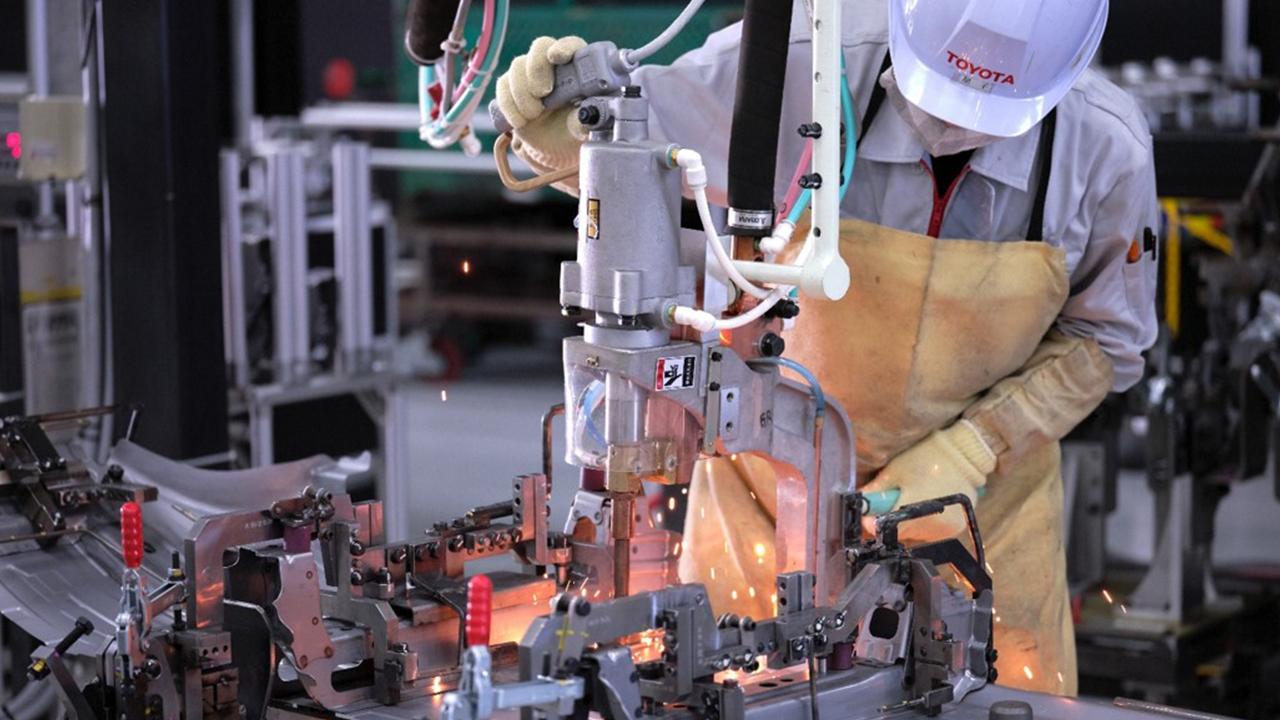
"Does Japan need manufacturing?" Such was the question posed by Toyota's top person in charge of manufacturing during a recent presentation for the media. What was he really trying to get at?
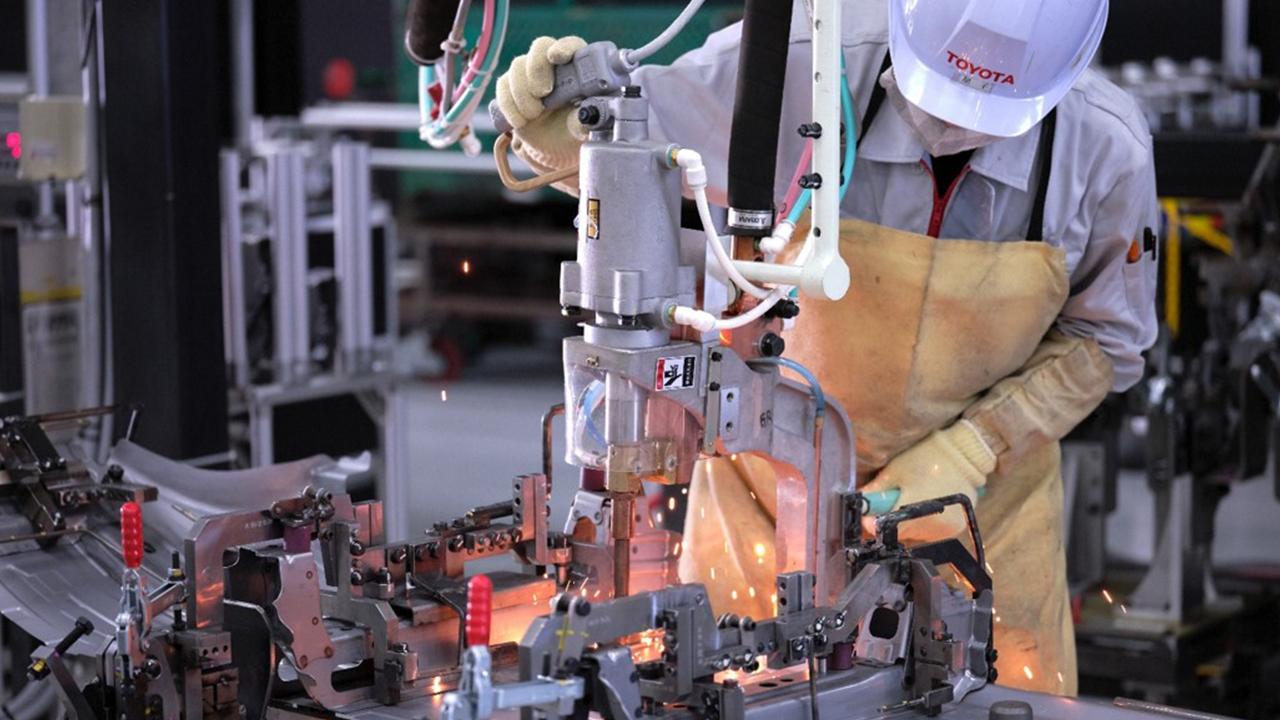
“Manufacturing is my life itself.”
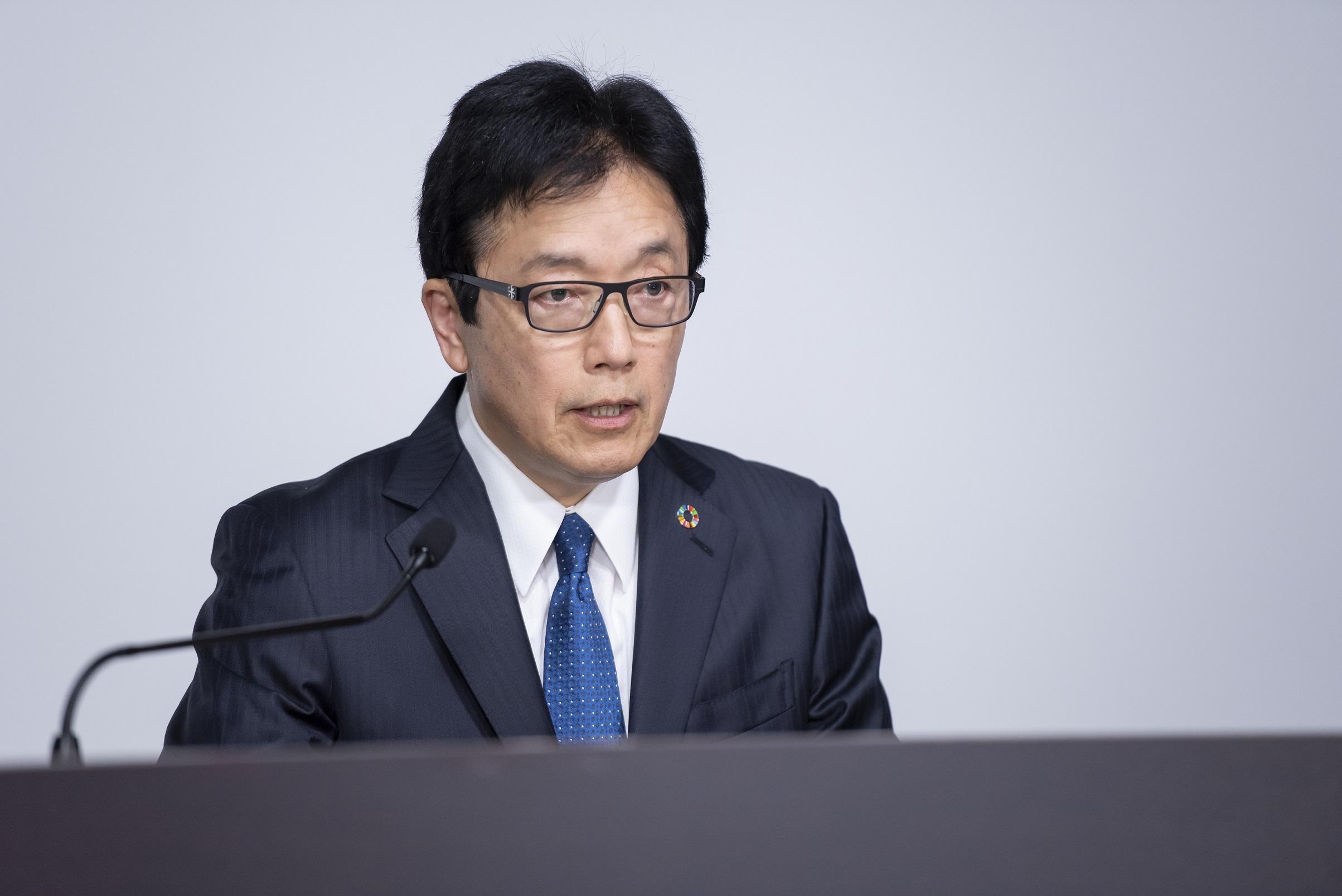
At a press briefing titled “Skilled Manufacturing Key to the Future” on June 11, Chief Production Officer Masamichi Okada put his heart into explaining the continued importance of manufacturing.
The biggest point featured in news about this briefing was that Toyota has revised its targeted timing for plant carbon neutrality forward from 2050 to 2035.
However, the main point that Okada wanted to make was that, rather than being past its prime, manufacturing was gearing up for continued growth.
With production bases moving overseas, it used to be said that Japan’s manufacturing industry was hollowing out. Even now, the situation is still tenuous due to moves to tax manufacturers for the amount of CO2 generated from production to disposal, as prompted by the inclusion of life-cycle assessment toward achieving carbon neutrality.
Against this backdrop, CPO Okada, who has been consistently involved in production since joining Toyota in 1984, strove to underline the competitiveness of Japan’s world-class manufacturing and the importance of manufacturing in Japan.
Toyota Times presents to its readers Okada’s passionate message in its entirety.
Does Japan need manufacturing?
During his presentation, Okada pointed out certain stereotypes about manufacturing in Japan and then went on to try to set the record straight.
Okada
Today, I would like to talk about how interesting the world created by manufacturing is, and about how manufacturing is helping to develop this country.
At the same time, manufacturing’s existence and strengths, which have been built up over many years, are not to be taken for granted. Once lost, they can never be recovered.
By sharing the essence of such manufacturing with everyone and cherishing manufacturing, we hope you will accept our invitation to open the way to the future together!
That is why we arranged this occasion.
First, let me raise the following as the first issue.
Does this country need manufacturing? Is manufacturing appealing?
Some people think that manufacturing is old-fashioned.
Shown here are examples of Toyota’s involvement in providing people freedom of mobility and joy. Even by looking at just a few examples, you can see that manufacturing has the power to create happiness, smiles, and joy.
Is manufacturing still viable in Japan?
Next, on to the second issue.
Can manufacturing survive in earthquake-prone Japan? Isn’t a series of disasters a sign of merging weakness? Isn’t Japan no longer a country in which manufacturing is viable?
I think that such questions are misguided. From long ago, Japanese manufacturing has always leveraged trials and tribulations, overcome them and become stronger.
When the Great East Japan Earthquake struck in 2011, plants and equipment unexpectedly suffered extensive damage, and recovery took a considerable amount of time.
In overcoming that ordeal, we have learned how to take equipment-related measures and appropriate initial actions to minimize damage as much as possible even in emergencies.
Last year, when COVID-19 spread and production became impossible, team members voluntarily started to produce masks, face shields, and foot-operated disinfectant application devices and to support the production of medical gowns. Our initial response to such emergencies has become more prompt and proactive.
In terms of disaster recovery support immediately after the 2011 earthquake, our parts procurement and equipment manufacturing teams brilliantly coordinated to achieve the feat of producing equipment in only two months, compared to the usual seven months.
That was the result of no one doing it for oneself and of working with the united purpose of protecting Japan’s manufacturing.
Just as we have long said, making things means making people.
I think it is safe to say that Japan, which turns hardships into strengths, is an optimal place for manufacturing.
Manufacturing is a growth field
This brings me to the third issue.
Can manufacturing, which is often called old-fashioned, create new solutions?
Let’s take the example of whether it is possible to make cars that do not emit CO2, other than battery electric vehicles.
Ten years ago, it was kind of like this:
“Impossible. The most that can be done is to reduce CO2 emissions using hybrids,” or “I’ve heard of fuel cells, but[haven’t seen anything practical.]”
Well, how about now? As evidenced by comments like “The Mirai is in its second generation”, and, with people talking about a car with a hydrogen-powered engine, something few had heard about 10 years ago, having completed a 24-hour endurance race, things have changed.
What new creations will come about over the next 10 years? New creations will sure come to life even beyond that. That’s truly something to look forward to.
Manufacturing is, without a doubt, a field of growth that creates new possibilities. Purposeful passion and action can change the landscape of the future.
Car-making supervised by a master driver and professional drivers
The focus then shifted to the development of the GR Yaris and a hydrogen-powered engine as specific examples. Okada explained the underlying strength and potential of Japanese manufacturing.
From here, I would like to share with you real-life, Toyota stories about the possibilities created by manufacturing with purposeful passion and action.
First of all, I would like to talk about “building in” a car's driving performance at the production site. During the development of the GR Yaris, Master Driver Morizo, or President Toyoda, and professional drivers requested various settings for the car. This point ties in with the “flavor” of cars.
Master Driver Morizo, is, so to speak, the executive chef of a high-class restaurant.
He prepares his offerings while paying attention to the taste before the customer arrives, the taste during the meal, and the taste after the meal. To evaluate beyond the limits of a car means bringing out the hidden secret sauce and ultimate dashi (or “soup stock”).
Drive until it breaks. When a broken part is made stronger, the next weakest part breaks. The repetition of this and sharpened sensors in the body of a master driver create a taste that cannot be measured by measuring instruments or only conscientiously created by design.
This is about an exceptional product that could never be served in a restaurant without an executive chef, that is to say, a master driver.
Now, returning to the point...
The master driver made requests during the development of the GR Yaris. However, the car was not to be a kind of “one-dish” race car. We’re talking about a mass-produced car.
The development team, production engineers, and technicians worked together to figure out how to make this car a reality on the mass production line, and the challenge of creating driving performance during the process began.
How the GR Yaris is changing Toyota’s car-making
Let me show you what we were able to accomplish on the GR Yaris production line at the Motomachi Plant.
Sports cars require a high level of body rigidity. To achieve this, more welding points are used than usual, and adhesives are carefully applied. Neither is possible with ordinary mass-produced cars. But this is how a high level of rigidity was achieved.
The GR Yaris is the first step in changing the way cars are made, and we are now entering the challenging phase of applying this approach further in mass production.
Here are some processes that go into building a well-balanced car. Elaborate technologies are used to pre-measure manufacturing deviances and to assemble in unison optimal combinations of parts. This ensures the best possible accuracy in the finished vehicle.
This was how the driving performance of a car can be “built in” on a production line.
Hydrogen-powered engine—a combination of steady challenges
Next, I would like to touch on how the much talked about hydrogen-powered engine was created through a combination of steady challenges.
Replacing gasoline with hydrogen gave rise to various difficulties. The engine engineers and prototype technicians worked hard to overcome those difficulties one by one.
Hydrogen tanks require a completely different level of safety than is needed in the case of gasoline. The injectors, which are parts used to inject gasoline into the cylinders of a gasoline engine, were of no use as they were. These are just a couple of examples of the obstacles that stood in the way. Such obstacles were overcome through the strengths of manufacturing.
We were also supported by our suppliers. The technology that had been cultivated in machining engine parts was applied to achieve micron-level hole drilling by way of special machining.
For fuel injectors, we used materials and machining technology to overcome the challenges that arise when gasoline, a liquid, is replaced by hydrogen, a gas.
Next are the challenges that were faced within Toyota.
Machining technology for “building in” fuel efficiency, electric motor assembly technology for creating a high level of efficiency, and hydrogen tank manufacturing technology for ensuring safety were all originally developed by refining their respective power units and accumulating the related know-how.
And through these challenges and efforts, the hydrogen-powered engine was created by combining FCEV and engine manufacturing technologies.
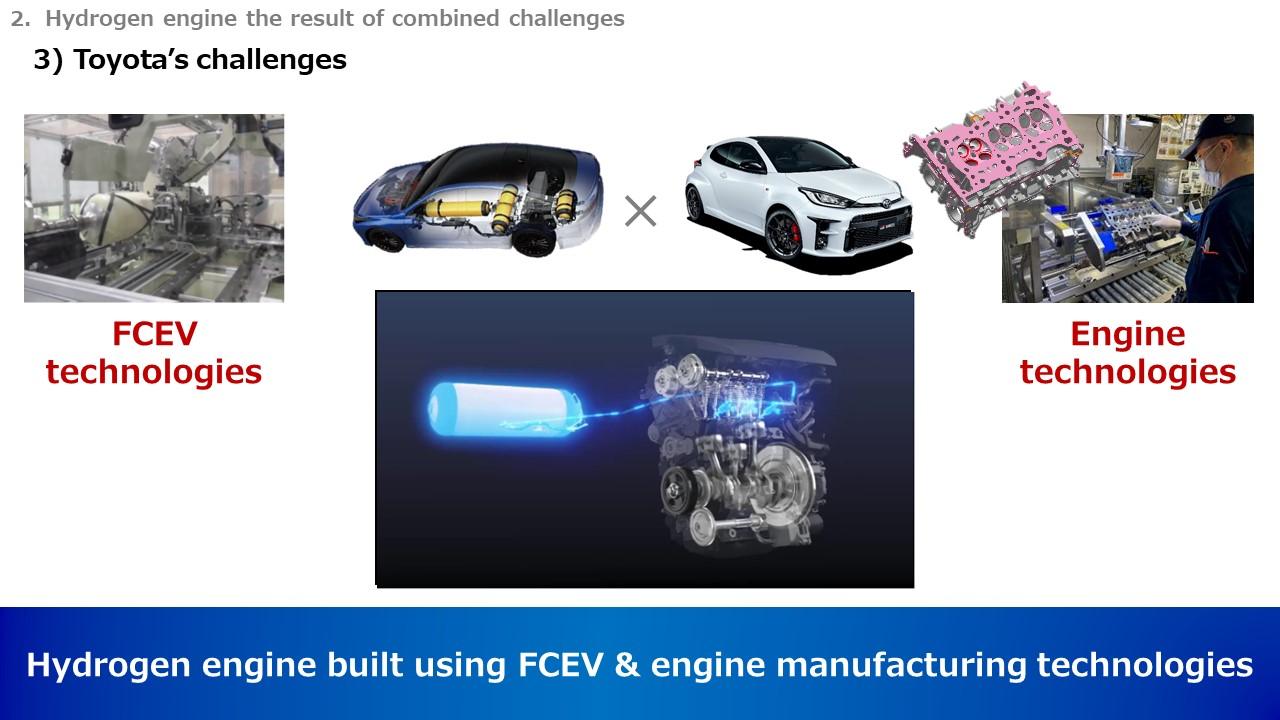
President Toyoda, a.k.a. Morizo, drove in a 24-hour endurance race in the hydrogen-powered car created in this way and was able to demonstrate to the world the potential of the hydrogen engine.
By expanding the options for electrified vehicles, Toyota has opened the door to the possibility of making customers who need engines smile and protecting the jobs of the people who make engines, while achieving carbon neutrality.
It can be said that this has opened the door to possibilities not only for cars but for all vehicles and equipment with internal combustion engines and devices that involve combustion, in other words, the whole of industry.
Aiming for carbon neutrality by 2035
As mentioned at the beginning, the biggest point featured in news about this briefing was that Toyota is now aiming to achieve plant carbon neutrality by 2035. Below, we take a look at some of the ways Toyota intends to do so.
Among vehicle manufacturing processes, painting process emits the most CO2, followed by casting. As part of his presentation, Okada introduced technological innovations in the painting process as well as steady continuous improvements, such as by using karakuri, as examples of Toyota’s efforts to reduce CO2 emissions.
Next, let’s talk about advanced manufacturing for a new era.
We are striving to achieve green factories. Carbon neutrality provides us with an opportunity to fundamentally rethink manufacturing. Toyota has taken on a variety of challenges to make its factories carbon neutral by 2035.
One of them is the development of technologies that make full use of new ideas.
First, I would like to introduce our painting, or coating, technologies. If you compare the left and right images, the difference is obvious. By combining the concepts of static electricity and rotation, we aimed to achieve maximum application efficiency with minimum paint. The equipment is compact and power consumption has been greatly reduced.
The next technology is for completing resin molding and paint coating within the metal mold used for resin molding. This is a technology undergoing verification that might make it possible to eliminate the need for the painting process altogether.
Replacing the painting process with adhesive film
Next is a technology that replaces painting with adhesive film. Adhesive film can be customized to make it special, and it can also be replaced for fun.
There is a car subscription service called KINTO, and the service is trying out renovating used KINTO cars and offering them as cars that excite.
We would like to contribute to a recycling-oriented society while providing customers with their own, unique cars by offering textures that are unlike used cars, or appearances and interiors that cannot be found anywhere else.
The recently announced GR Yaris “Morizo Selection” indicates that the functionality of cars will go on to be updated, as well.
Using karakuri to achieve the ultimate in carbon neutrality
Next, I would like to introduce the use of karakuri.
A karakuri mechanism is a device that moves without power by combining gears and shafts.
At Toyota’s Honsha Plant, there is this area called the Toyota Production System (TPS) basic line that uses wisdom and ingenuity to create automated machines that do not use sensors or control devices by going back to mechanical-action karakuri.
The use of karakuri develops human sensibilities and equipment because, for example, a karakuri mechanism must properly work for the next action to occur, and because such mechanisms make it easy to detect problems without relying on sensors.
This is an actual piece of karakuri-based equipment. It is an example of an ultimate carbon-neutral piece of equipment that is capable of unmanned operation, as it uses non-powered operation to replace pallets, which contain production parts, and is combined with an automated conveyance cart.
Collaboration between the latest technologies and TPS
Lastly, I would like to talk about collaboration between the latest technologies and TPS.
The first is about automated conveyance. At Toyota, transporting, itself, is considered wasteful. The starting point is trying to not transport at all. But, as that can often not be done, if something needs to be transported from point A to point B, as shown in the diagram, the layout is changed to reduce the distance, and the base units of measure, such as cargo volume, are also reduced. And then what remains gets automated.
This concept will also be applied to the underground logistics and others of Woven City.
The second is automated inspection using AI. There are many examples in the world of automated inspection of defective products using machine learning to reduce the amount of needed human labor. But our goal is to use the vast amount of data we are collecting from this process to make essential improvements that will prevent defects from occurring in the first place.
The third has to do with digital transformation and IoT. Toyota believes that there is meaning in attaching sensors to be able to see on a monitor every little detail of the status of equipment and production lines.
However, we have had some bitter experiences. We spent a lot of effort just trying to be among the first to catch the IoT wave.
But for Toyota production lines for which we had raised the equipment utilization rate to 98 percent by pursuing continuous improvement and applying TPS, there remains the problem of how to secure the last two percent. It is a real problem that can only be solved by the power of people.
Toyota believes that people should not be turned into machine-keepers. To get that final two percent, we aim to simplify equipment and create equipment that does not break down.
By combining this unique, human-centered, Toyota thinking with digital transformation and IoT, we hope to create the next generation of advanced production lines.
For your reference, the line shown here is a vehicle production line that was built in Mexico in 2019.
“Manufacturing is my life itself.”
In his conclusion, Okada, who has experienced 37 years at production worksites, expressed his passion for manufacturing.
I grew up in the world of manufacturing. I, myself, am rather clumsy, and no matter what I make, it doesn’t seem to turn out that well. But I like working with my colleagues at the genba, or manufacturing worksites.
When I was young, I once got my head covered with hydraulic oil from a machine in an accident [as I tried to be deeply rooted in the genba], and I would even argue with assistant managers at the genba many times. Manufacturing is my life itself.

Now, we are facing a wave of new challenges such as digital transformation and carbon neutrality, and I am excited to be in an environment in which I can take on these challenges together with my colleagues.
We at Toyota have manufacturing colleagues around the world. But we try things out first in Japan. There are many times when we fail. Because Japan is earthquake-prone and has very little natural resources, things aren’t always easy here.
However, because we can turn our situation into strength, if we can make something that works in Japan, it will surely work overseas as well.
On top of that, in line with the actual conditions of our overseas manufacturing sites, we incorporate, apply, and spread among them that which is good.
Through the accumulation of such efforts, we hope to become the “best-in-town car company” and one that is engaged in the production of happiness for all, region by region.
Although the briefing provided the media with news by announcing Toyota’s new intention to achieve plant carbon neutrality by 2035, Okada dedicated most of the time toward explaining the importance of manufacturing in Japan and the future possibilities of manufacturing.
To let all be known, before the briefing, President Akio Toyoda made his expectations clear to Okada.
Akio
I have sometimes been called “outdated” for my strong commitment to Japanese manufacturing and jobs. But if the light goes out on manufacturing, it will be a dark day for Japan for sure.
While being humble is important for those of us in manufacturing, I want you to be thinking about Japan when you deliver your message. I want you to thoroughly convey that, rather than being a thing of the past, manufacturing is a growth industry. Present manufacturing as something to which young people can aspire.
At this briefing, Toyota’s top person in charge of manufacturing, who was reared on manufacturing since joining the company, spoke with abundant affection for the wonderfulness that he has experienced in manufacturing.
Although beyond the screen were reporters, Okada seemed to be reaching out further to the future bearers of manufacturing.