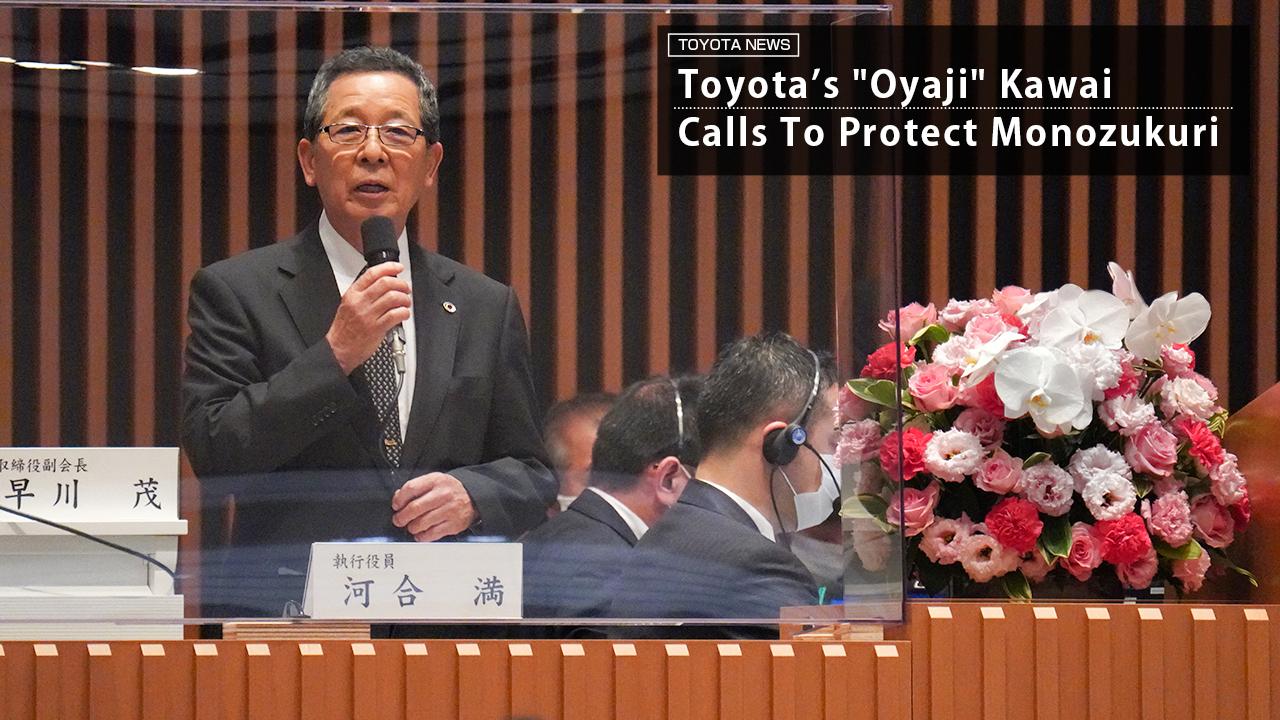
In response to a shareholder question, Toyota's champion of monozukuri, Mitsuru Kawai, shares thoughts on Toyota's commitment to continuing production in Japan and the importance of skilled workers.
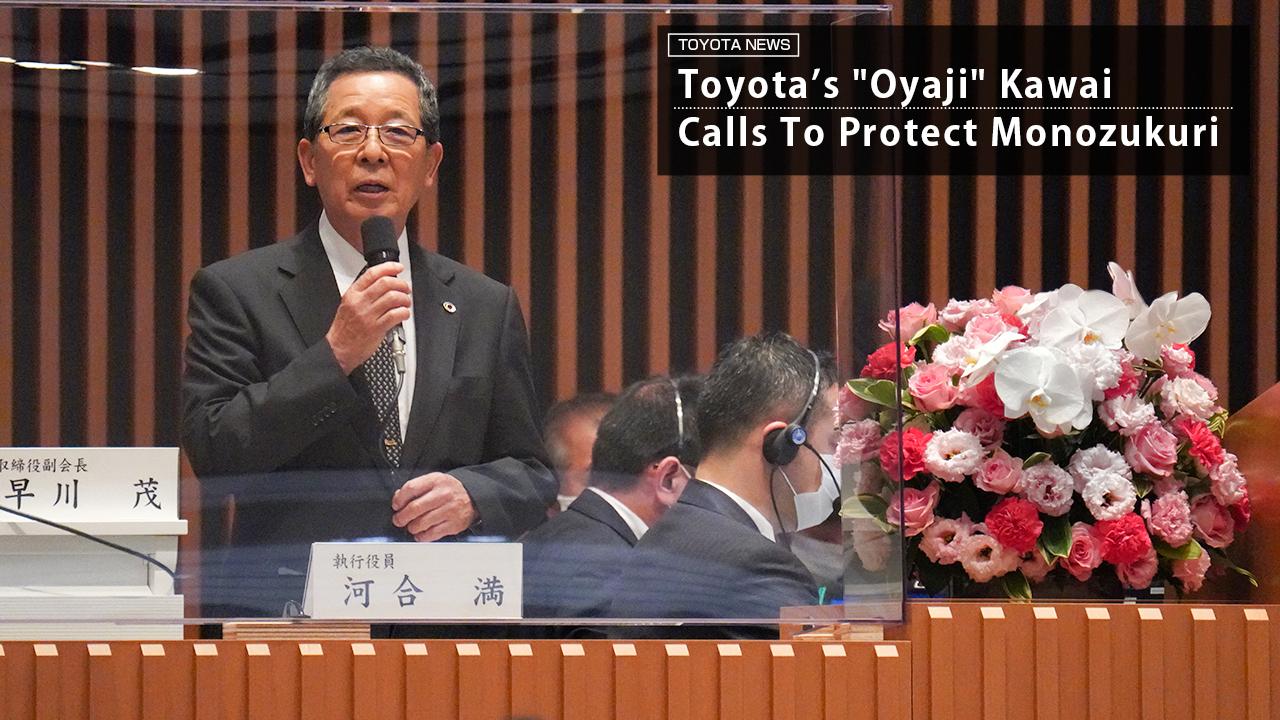
Welcome back to continuing coverage on Toyota Times on the 116th Ordinary General Shareholders’ Meeting that took place in Japan on June 11, 2020. In this article, the focus is on one question asked at the Q&A session that referred to Toyota’s stated commitment to retain a production of up to three million vehicles in Japan.
The following includes both the question from the shareholder, who was attending the meeting for the first time, and the response that was provided. Since it was the first time for this shareholder to attend, the assumption made was that Akio would answer all the questions asked at the Q&A session. Here is the question:
<Shareholder>
This is the first time for me to attend this shareholder meeting. I wasn’t sure at first whether or not I should attend, but, with the economy faltering so much due to COVID-19, I decided to attend because I absolutely wanted to hear directly from President Toyoda.
Related to the recovery of Tohoku, you explained your thoughts that Toyota would use monozukuri to become a force in the recovery of the Tohoku region. Even looking at the current situation of the economy of the region and the speed of recovery, it was brought home to me anew the large contributions made by Toyota.
However, in the midst of confronting a new crisis, Toyota says that it will defend to the very last an annual domestic production of three million vehicles. But, even as the domestic market slumps, I hear that things are also down overseas. In such a situation, can you really protect domestic production of three million vehicles a year? And, if so, what will be your measures for doing so?
When the shareholder finished asking the question, Akio responded, saying:
“Thank you for your question. I will have “Kawai, our ‘oyaji’, answer this question.”
He decided to defer the question to Operating Officer Kawai, and for good reason.
Kawai, our “oyaji”?
Some of the attending shareholders most likely felt a little discomfort with the reference Akio made to Operating Officer Mitsuru Kawai, calling him “oyaji” (Japanese for “father’). However, Kawai took the reference in stride.
Kawai took the microphone, and started talking as though nothing strange had happened.
“Hello, I am Kawai, the ‘oyaji’.”
Until just this past March, Kawai had the title of executive vice president. However, now his business card has the title “oyaji”, followed by “operating officer”. Just like making how Akio changed Kobayashi ‘s Executive Vice President title to “banto”, Akio lovingly gave Kawai the title of oyaji.
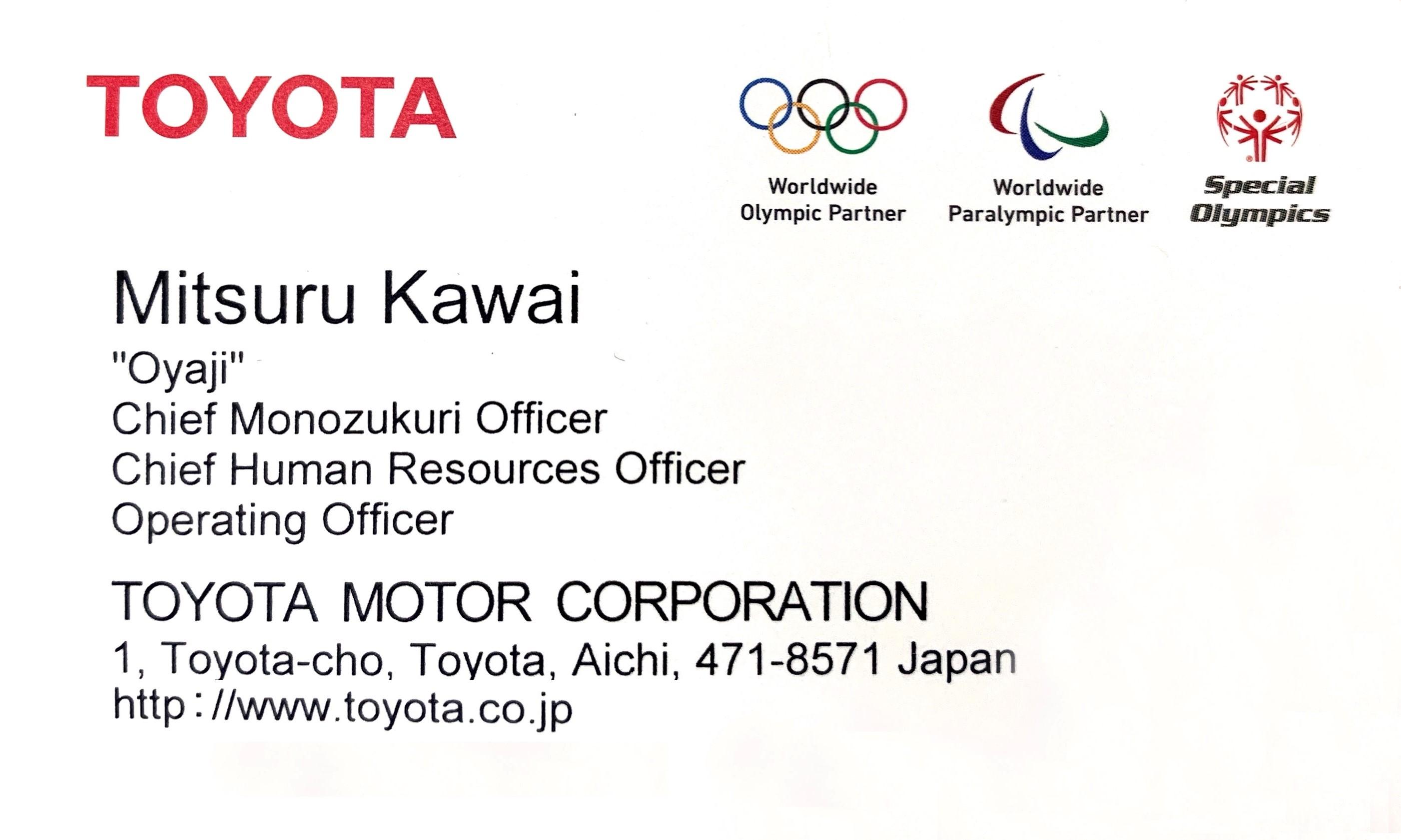
To help the reader better understand the meaning that is behind this title for Mr. Kawai, it behooves the editorial staff at Toyota Times to relate a story entitled “Oyaji” that Akio wrote four years ago as he thought about Father’s Day. The following will include excerpts from that article.
There are many names that can be given to those who take care of you, at Toyota those types of people were at one time called “oyaji” by their friends.
For example, Advisor Fujio Cho called Taiichi Ohno “oyaji”, with the best of intentions in a friendly way. For me, Cho san and Naruse san are people who I similarly and lovingly call “oyaji.”
Of course, the Honorary Chairman Toyoda is my actual “oyaji”!
I wonder if I’m the only one who when I hear the words “oyaji” and “ofukuro,” I imagine someone with a caretaker/supportive nature?
If you do something wrong, you will be scolded.
If you cause problems for others, they will apologize alongside you.
Although they may not speak very much, they will always protect you.
I hope that the number of such “oyajis” and “ofukuros” will increase in our workplace as well.
The title that Akio gave Kawai was an expression of his expectation for Kawai to become an “oyaji” to all employees. With that explanation covered, it is time to return to how Toyota’s oyaji answered the question from the shareholder last week.
< “Oyaji” Kawai >
In Tohoku, where we have Toyota Motor East Japan, we have been working hard as Toyota’s third domestic production base. We have every intention to keep on doing so. Regarding your question about a committing to the domestic production of three million units a year, although there are instances of necessary suspension depending on the vehicle model due to COVID-19, just as we have so far been adamant about defending to the very last such a system, we will not change our thinking or direction going forward.This statement from Kawai showed the resolve the company has to continue to maintain a domestic production level of three million vehicles, especially under the current circumstances. But he didn’t stop with this statement; he continued, sharing his own thoughts.
We produce and sell about 10 million vehicles globally every year, [and] all of that stems in one way or another from what we do in Japan. We believe that it is necessary to have production sites with a certain volume of production in Japan, which, collectively, should serve as the “mother plant”.
Providing automobiles involves quality, manufacturing, production technology for mass production, and cost considerations. We want to thoroughly build into our vehicles the required quality, volume, and costs considerations. We must continue to steadfastly cultivate the technologies and human resources needed for such and we must pass down the making of ever-better cars.
Our suppliers make approximately 70 percent of a single vehicle’s 30,000 parts. We want to pass down a skilled workforce that can steadfastly build quality into our vehicles. For that, we believe that having a domestic production level of three million vehicles a year is necessary. Doing so is, I think, also important in protecting employment in Japan.
To put it simply, Kawai words reflected the same ideas that Akio had been saying on many separate occasions.
Additionally, Oyaji Kawai took some time to introduce what kind of activities the employees have been doing at the manufacturing front, during the current COVID-19 pandemic.
On non-operation days last month and the month before, our employees showed up for work to find ways to improve productivity, thoroughly implement the Toyota Production System, overhaul old equipment, and improve quality, under the banners of “Let’s at least strengthen our composition during this period!”, “Let’s be ready to start up all in one go after COVID-19 recedes!”, and “Let’s do what we can now!” That’s what we have been thoroughly doing.
Using this opportunity as a lesson, we just so happen to now be working on workplace innovation and are thinking about various reforms.
As for social contribution, we have used 3D printers in the United States to start making medical face shields, and such efforts spread to Europe and Japan, with more than 100,000 medical face shields now having been sent to medical professionals around the world as of yesterday.
Our plants have made face masks and provided them to people in their vicinities, while the athletes of our athletic clubs have also taken part in such activities as they were not engaging in their normal practices and games.
Such efforts are providing good places to learn about the Toyota Production System’s contribution to help make as many masks as possible by eliminating waste.
Members have also gone to out-of-session elementary schools, junior high schools, nursery schools, and kindergartens to cut the grass/weeds and make other contributions to local communities.
For automobile manufacturers, to not be able to produce vehicles on a daily basis makes the company feel a bit “out of the water”. However, despite not being able to operate the plants, Toyota’s team members are diligently and continuously preparing so that they will be ready to restart operations as quickly as possible when the right time comes. Some of the activities those manufacturing teams are engaged in now may not be about cars, but Oyaji Kawai showed how Toyota is still making things and trying to be useful to others.
Then, Kawai continued to offer examples of how the company’s partners and colleagues were trying to be of use to others.
Also, we learned of the members of seven small-to-midsize businesses wanting to make the protective gowns used on the medical front lines and send them out as soon as possible. Thinking that there must be some way that we could help, we went to support them. We provided support by thoroughly applying the Toyota Production System to eliminate waste, promote kaizen, and overhaul old equipment that was worthy of being thrown out.
At one of those companies, which could only produce 500 gowns a day even after working all day long, within a few weeks, their productivity rose by more than eight fold, resulting in daily production of more than 4,000 gowns.
The president of that company expressed his appreciation and said: “We could really apply the Toyota Production System, and our employees were able to learn.”
While sharing the procedures with other companies, today, the company is now expected to produce two million gowns by the end of September which it promised to send to the Ministry of Health, Labour and Welfare. That’s how well along things have come. This is the kind of support that we have provided.
In the above example, Kawai was referring to a story that was published on Toyota Times on May 27.
That story was about how the Toyota “Avengers” went to a rain wear factory to kaizen, or improve, its manufacturing process.
Kawai had a chance to “go and see” the rain wear and swim wear factory sites that had switched to attempt to make protective gowns. With the unique opportunity to visit and observe factories he would not normally have a chance to see, he came away with some unique feelings.
We will protect monozukuri, so as to prevent the transferring of production sites to the outside simply due to costs, just as we have done with face masks.
Most of the people working at those seven companies are from Vietnam. Currently, these are those who are performing the type of detailed work for which Japan is well-known for.
I believe that it is important to bring together the skills and technologies that are available to make what is needed when the world needs it. As a place for honing competitiveness, we are ready to do our best while protecting to the last, after all, our system of domestic production of three million units a year.
The goal of Toyota to protect the domestic production of three million cars…specifically the decision to keep factories in Japan has been said in the past to have been a mistake, at least from the point of view of economic rationality. The decision has been criticized many times – until now. That is not to acknowledge that a company can make profit by manufacturing something in a country that is less costly (at least in the short-term).
However, Akio in particular has been a staunch supporter and defender when it comes to protecting monozukuri sites. His feelings on this topic are not a secret, as he has shared his feelings boldly on the subject on many occasions. To share a recent example of his outspoken nature with regards to domestic production, please see the following, which he stated during a press conference for the year-end financial results in May:
What we have been defending to the very last has not been “3 million vehicles.”
What we have been continuing to protect have been people who have acquired the techniques and skills that enable them to make what is necessary when the world needs it.
We are proud that we have been continuing to protect in Japan places in which such human resources can work and be cultivated.
Even as we are now facing the COVID-19 crisis, there is not the slightest bit of distortion or wavering in this belief.
It is widely believed that as a company makes higher profits, shareholders might also be able to receive higher dividends. It is not surprising then that shareholders that think this way, often make a comment such as, “Why don’t you move the manufacturing plants abroad?”
If the shareholder feels that this type of feedback and thinking is not well-received, then the shareholder may consider letting go of any Toyota stock they hold.
However, for the long-term shareholders, these are the ones that have stuck by the management, and they are also more likely the ones who concur with Akio’s business judgement, determined to let him lead.
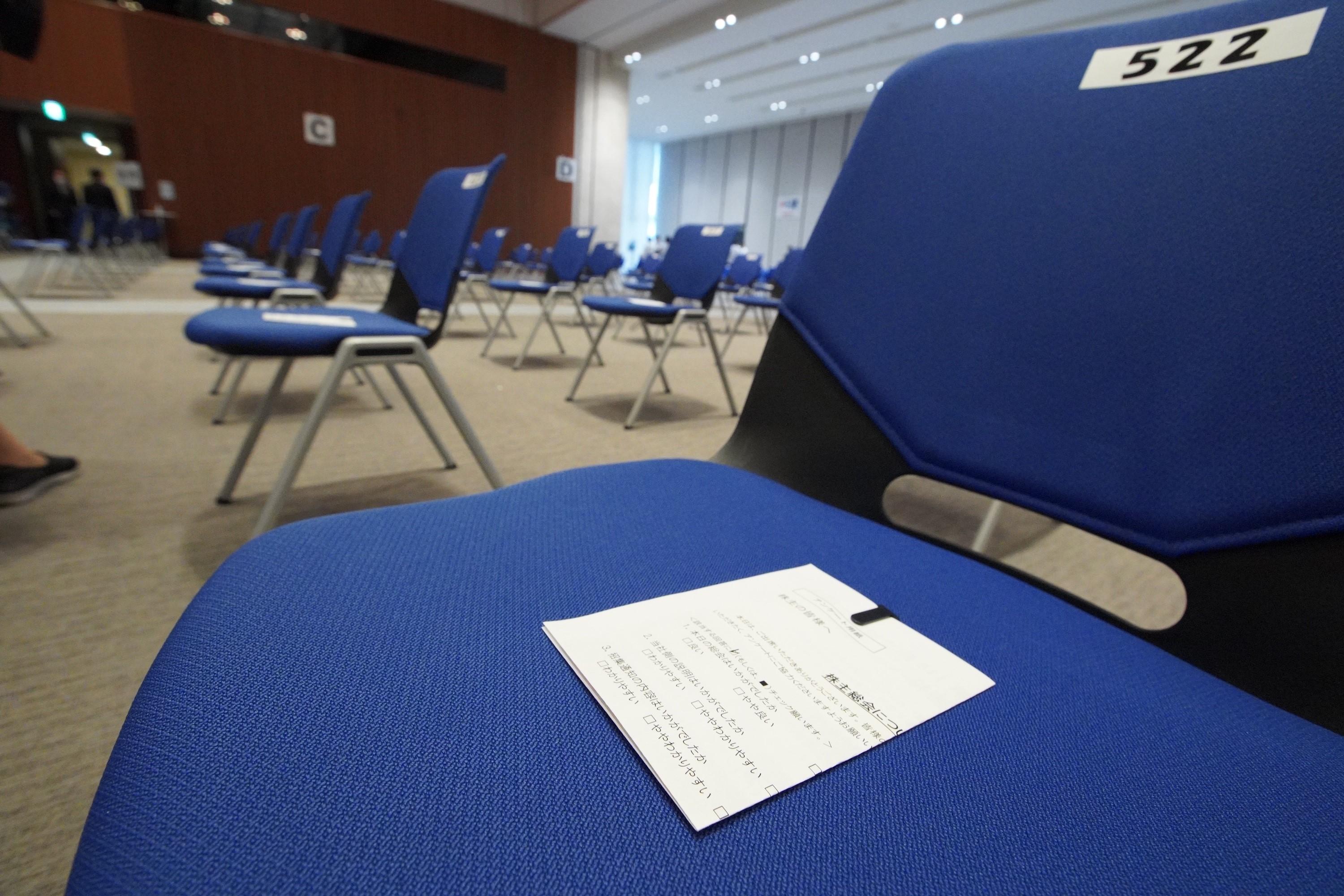
For some additional background, Mr. Kawai started working at Toyota in 1963. Since then, he has lived for monozukuri and given his all for the job sites for over 50 years.
Even with promotion after promotion, eventually rising to the level of executive vice president, Kawai kept his office not at the Toyota headquarters, but inside the factory.
Thus, when asked by the shareholder about whether or not production of three million vehicles is something that truly can be protected, Kawai took yet another opportunity to once again offer his view of Toyota’s thoughts toward monozukuri, with the aim to help foster greater understanding and reaffirm that direction to those who have chosen to hold onto the company’s stocks.
Although Akio was perfectly capable of sharing the thoughts that he had shared on numerous such occasions in the past, he knew that “Oyaji” Kawai understood this thinking well enough that he could entrust him to answer. Akio knew Kawai was a man who has lived for monozukuri and the work sites.
Therefore, Akio, as chair, made the decision to defer to the oyaji to represent the monozukuri response and share the company’s gratitude for the support the shareholders have given until now and for him to also express the company’s determination moving forward.
This concludes this article; however, the coverage of the Q&A session from the Ordinary General Shareholders’ Meeting will be continued in the next Toyota Times article, “Akio on Winning: Toyota Uses Strength in Doing Things for Others.”