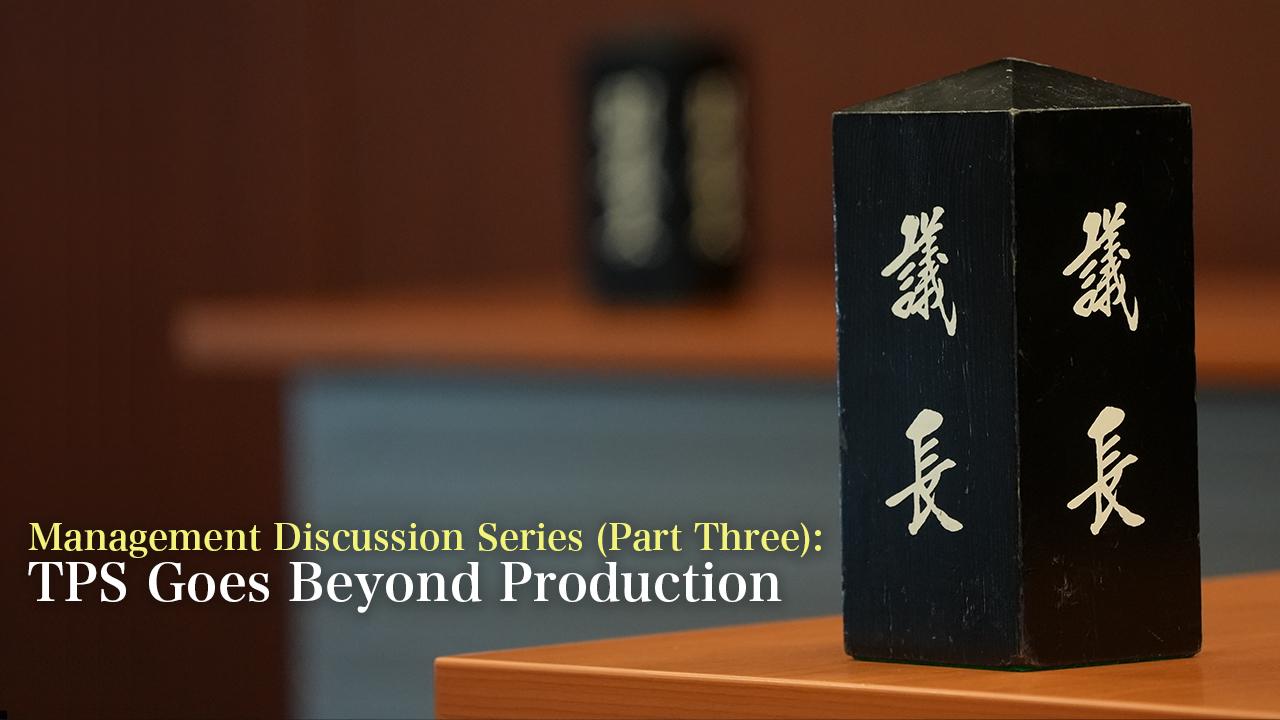
TPS is the shared language of Toyota's global operations, and management explains to employee representatives how it goes beyond production as people understand it on a deeper level.
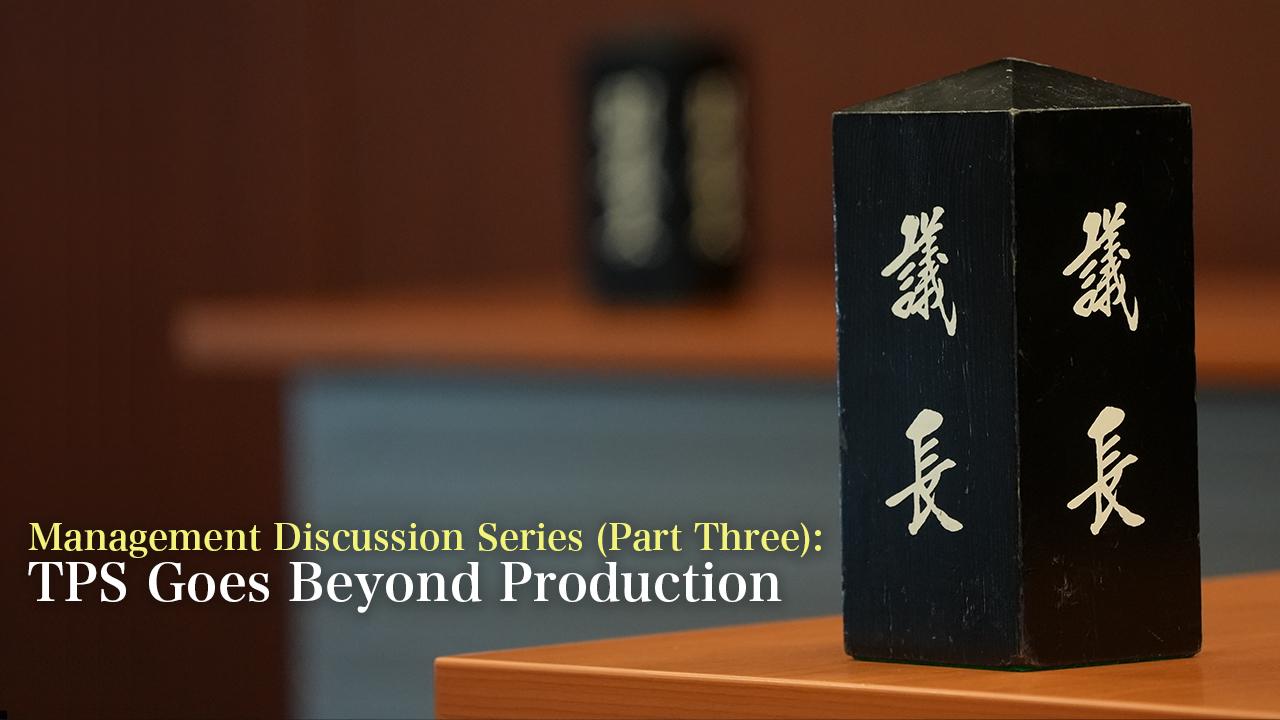
Every spring, TMC hosts discussions between company management and employee representatives. At this year’s third session, held on March 10, the topic of how to grasp and utilize the potential of the Toyota Production System (TPS) was the focus. Although efforts are still underway, in recent years the company has been working to ensure that all employees embrace TPS as the core of ‘what makes us Toyota’. The discussions began with presentations of example initiatives.
Don’t waste the efforts of valued colleagues
The results of some specific instances where TPS was implemented were presented at the meeting, and included:
- Halving the lead time needed for a part by going to visit a partner’s genba in person to review specifications- Supporting a company that began manufacturing medical gowns during the pandemic, helping to reduce initial production lead-time by 84%
- Working with a logstics company in an attempt to streamline the process of delivering parts to the plant, improving transport efficiency and safety.
Team members who had experienced the visible results of TPS noted that putting the system into practice changed their mindset. Comments from these team members were:
“I realized that I had been making things more difficult for downstream processes,” and, “Even small improvements can benefit someone, and contribute to job satisfaction.”
In response to these comments, Masahiko Maeda, the Operating Officer in charge of technology, outlined a major policy for the company’s R&D – with TPS implementation to extend across organizational boundaries to pursue greater efficiency throughout all processes.
Operating Officer Masahiko Maeda
When President Toyoda spoke at the launch of the TPS training program (a voluntary practice program focusing on TPS-driven kaizen activities) for office positions, what resonated most with our members was the comment that TPS was rooted in ‘thinking about how to make people’s work easier’.
When we set out to select a model workplace, some initially told us that their workplace was too busy at that time. Once they saw it as making someone else's work easier, however, we had no trouble gaining approval.
When they first started, I think many members considered only how the training applied to their own workplaces. But they came to realize that this alone does not yield radical solutions – to find solutions, you have to expand the scope of your activities beyond your own workplace.
I think the perspective of making someone else's work easier really came to life as well.
In a fragmented organization, I feel that we often worked with the attitude that we should not burden other departments, that we have to solve all the problems by ourselves.
By applying TPS, I think one instinctively learns how to grasp the essence of a problem across all adjacent processes, instead of just your own role.
It also clarifies where wasteful activity exists between processes, without contributing to end results. This helps with clearing up time for handling integral work and optimizing the timing of tasks.
A customer-focused approach must form the very core of ‘making ever-better cars’. Unfortunately, we may have lost sight of that importance as we focused on operational efficiency in our own workplaces.
I feel that we are now laying the foundations that will allow us to go back to basics and consistently make cars in a way that brings the most joy to our customers.

Having dedicated more than fifty years of his life to manufacturing, Mitsuru Kawai, who chaired the discussion, offered actual examples of TPS efforts by team members as a way to illustrate the importance of starting with something attainable.
Chairperson Mitsuru Kawai
Speaking with team members in office or administrative positions, I get the sense that they see TPS as abstract or difficult. The first thing they say to me is, “I don’t know what I’m supposed to do”.
Last week, President Toyoda and I visited Toyota Motor East Japan and saw new employees being trained in TPS. When speaking with President Toyoda, one of the recruits referred to TPS as ‘cost reduction’.
President Toyoda responded to this by saying that “TPS is about making everyone’s jobs easier.”
When our plants stopped operating due to COVID-19, office workers from each facility and athletes who could no longer practice met up in gymnasiums to make masks.
By setting up an assembly-line system, timing processes, and eliminating downtime, they were able to raise efficiency and each day increase the number of masks made.
They provided feedback, along with comments like “That was fun” and “So this is what TPS is all about”. I think this is a great example of how to grasp TPS.
I hope that people will take it up, even if that’s just finding ways to make work easier in their own area or for those involved in downstream processes.
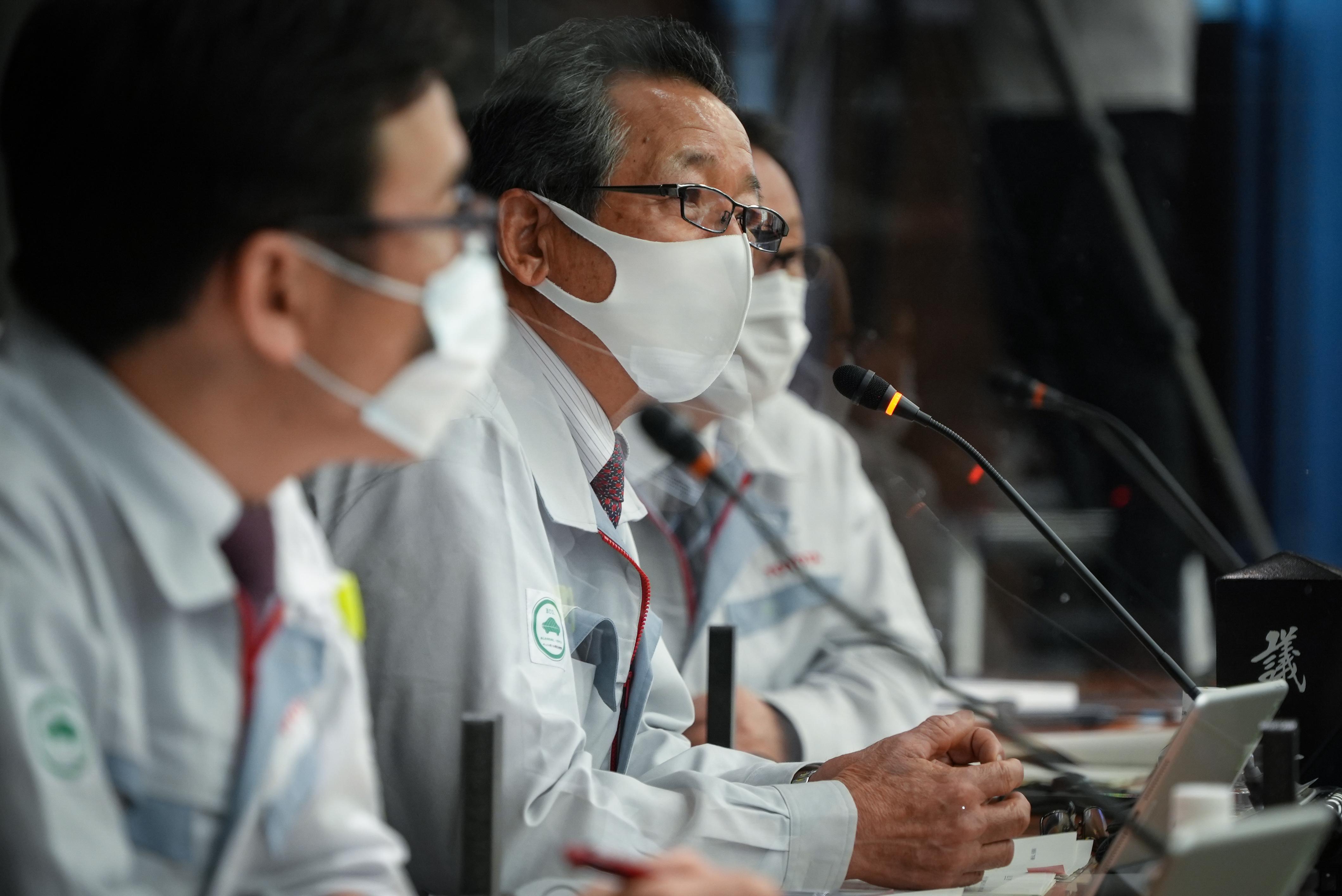
Chief Officer Kyogo Onoue, who is tasked with promoting TPS, spoke about the system’s origins.
Chief Officer Kyogo Onoue
As mentioned earlier, simply put, TPS is about ‘making people’s work easier’.
I’ve been involved with TPS for a long time, but I haven’t seen anything like that written in TPS books. The two pillars of TPS are Kiichiro Toyoda’s concept of ‘Just-in-Time’ and Sakichi Toyoda’s ‘Jidoka’, or “automation with a human touch” (according to the books).
That said, Jidoka itself traces back to young Sakichi’s desire to make weaving easier for his mother. This links to the idea of wanting to make someone else’s work easier.
Currently, all 24 groups and in-house companies are conducting the TPS training program for office staff. Officers also take part.
In practice, we make sure to clarify work according to ‘monojo’ (Material and Information Flow Diagram).
This shows us what is happening in adjacent processes, and we can see whether we are causing difficulties downstream. We also learn that, by doing so, we are creating more work for ourselves.
In many areas, kaizen has resulted in changes that make work easier and reduce lead time.
On top of that, managers have begun to voice a desire to assign their teams meaningful work, to ensure that their efforts are not wasted. This ties in to ‘Respect for People’ (which is valued at Toyota).
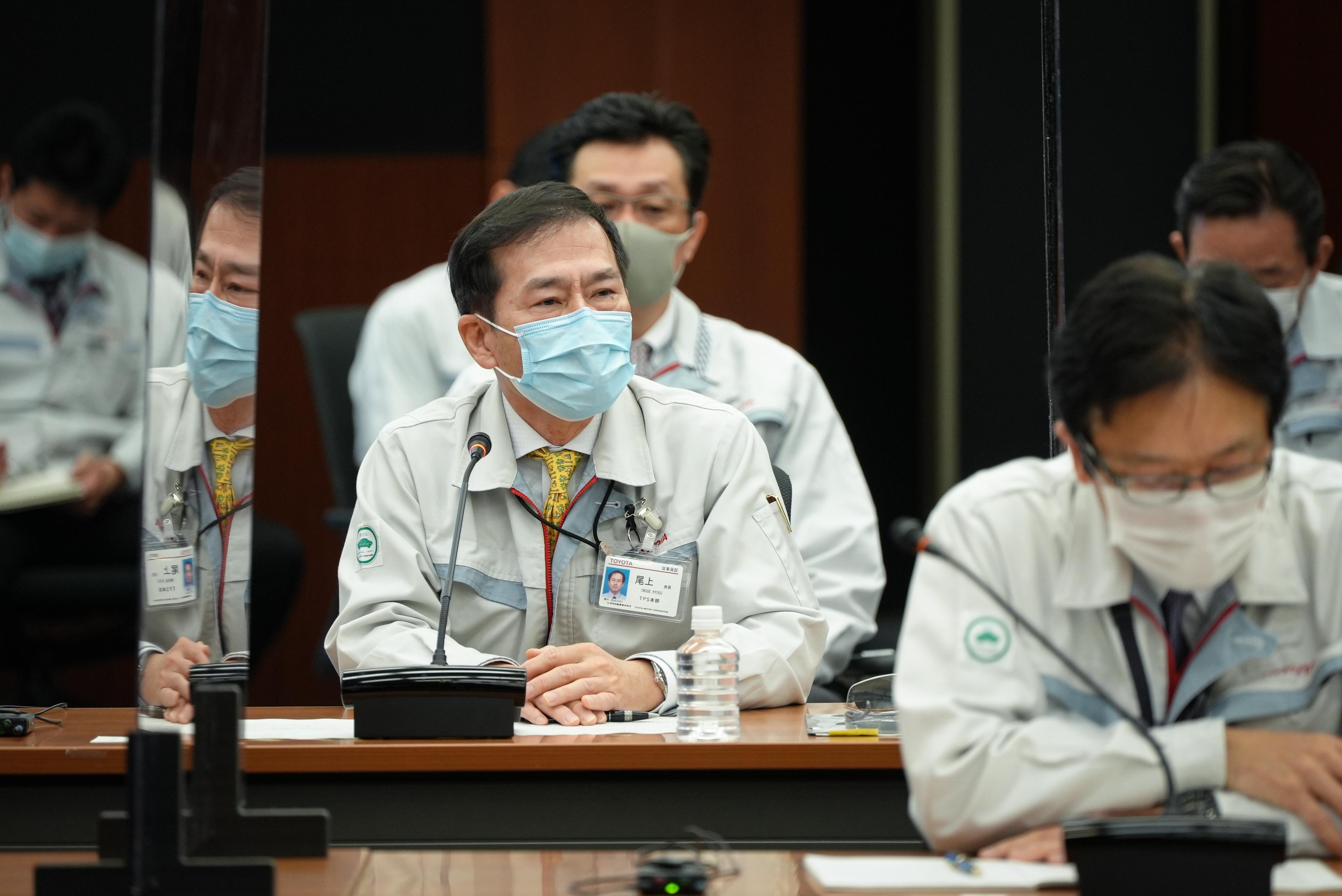
Don’t view results as the goal, but the starting line
At this point, Akio addressed everyone in attendance, speaking about the ‘essence of TPS’ that must not be overlooked to ensure that efforts yield results.
Akio
You may feel as though the idea of ‘doing things for others’ and ‘making someone else’s work easier’ is well established.
However, as we have only just begun improving TPS among office positions, it is important that we view this as a ‘work in progress’, rather than ‘established’.
As mentioned, TPS books may not say anything about ‘making work easier’, but it does contain the words ‘after kaizen is the state of before kaizen’, or ‘continuous improvement’.
The Japanese word for improvement, ‘kaizen’, has been adopted by Toyota to the point that it is now used in English. So here we are talking about ‘continuous kaizen’, continuous improvement.
The two pillars of the Toyota Production System are ‘Just-in-Time’ and ‘Jidoka’, automation with a human touch. Jidoka is very much about ‘working for others’ and ‘respecting people’.
Even in Woven City, we talk about a ‘human-centered’ city of the future precisely because it is being built by Toyota, with our Jidoka philosophy.
We don’t just say this because we are creating future cities, but because we have applied the idea to our hardware manufacturing for a very long time.
The other pillar is Just-in-Time. To put it another way, pursuing a Just-in-Time approach is about shortening lead times to the utmost limit – zero. The ideal Just-in-Time result is when the task itself ceases to be necessary.
There is a possibility that we cannot reach zero. Even so, we try to eliminate downtime and reworking. If we reach zero, we can stop working on that task and do something else. We continue the process until that point.
Instead of talking about establishing, or making progress in your own workplace, our office personnel need to see and think in terms of TPS.
This time, you have invited kaizen advisors from the TPS Group to come and explain that perspective and mindset.
You may achieve results, in the form of cutting some waste, but this is only the start. Please make sure that you don’t let it end there. I want us to be driven to keep going beyond that point.
Over the years, the way we look at and think about things changes. And our day-to-day work changes as well. If the way we work changes, the results are sure to change too.
With that in mind, I hope that all of you will be prepared to keep the process going.
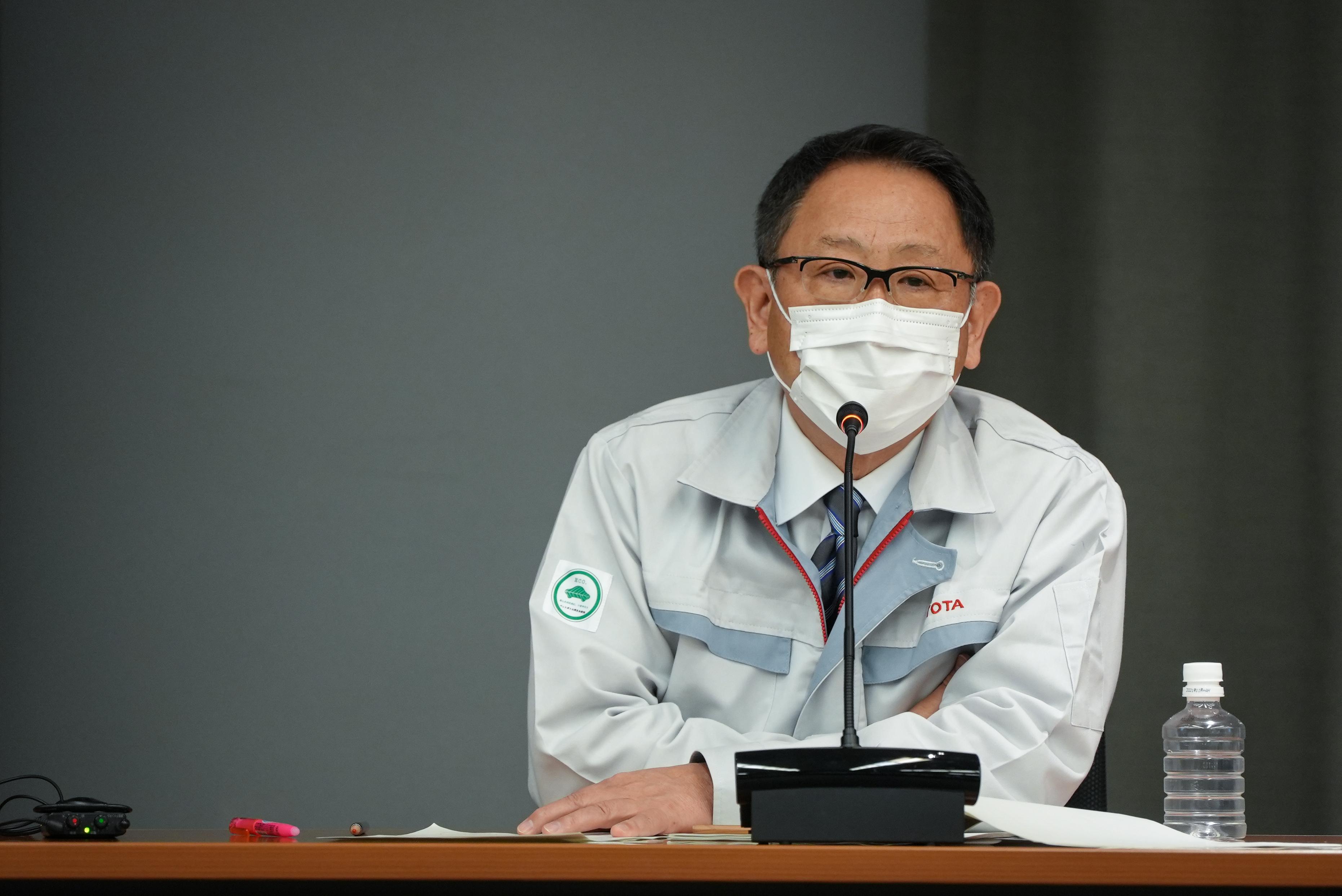
TPS goes beyond the production genba
As Masamichi Okada, Operating Officer in charge of production, explained, TPS is a strength that Toyota has cultivated through manufacturing, but it can be applied to many other areas beyond the production genba.
Operating Officer Masamichi Okada
Over generations, TPS has been handed down through Toyota’s genba, and I believe this has created an approach to manufacturing that is unique to our company.
The results of this shared mindset and language have also been demonstrated in various other situations, from transport for the Olympic and Paralympic Games to agriculture, the underground logistics of Woven City, and the operation of COVID-19 vaccination sites.
I think this is what President Toyoda has in mind when he says that TPS goes beyond the production genba.
As more of our office personnel engage in TPS activities, they find new ways of looking at the daily tasks they had taken for granted, and see for themselves that this mindset leads to kaizen.
I believe these activities help to identify the starting point, and give people the drive to continue forward.
Everyone is beginning to understand that TPS is universally applicable, that it goes beyond the production genba and beyond Toyota as well.
I am certain that it can do more to help those working in the automotive industry.
Building on the shared foundation and source of strength that is TPS, I want to work together to create an automotive industry where everyone can thrive alongside each other.

Besides being the key to boosting competitiveness and making work easier for colleagues, TPS is also the shared language of Toyota’s global operations. Everyone present recognized anew that, regardless of individual work, whether in the plant or the office, understanding and applying TPS is critical, and must be our advantage.
In Part 4, Toyota Times will look at the continued discussion, focusing on Toyota’s approach to carbon neutrality.
(Continued in Part 4)