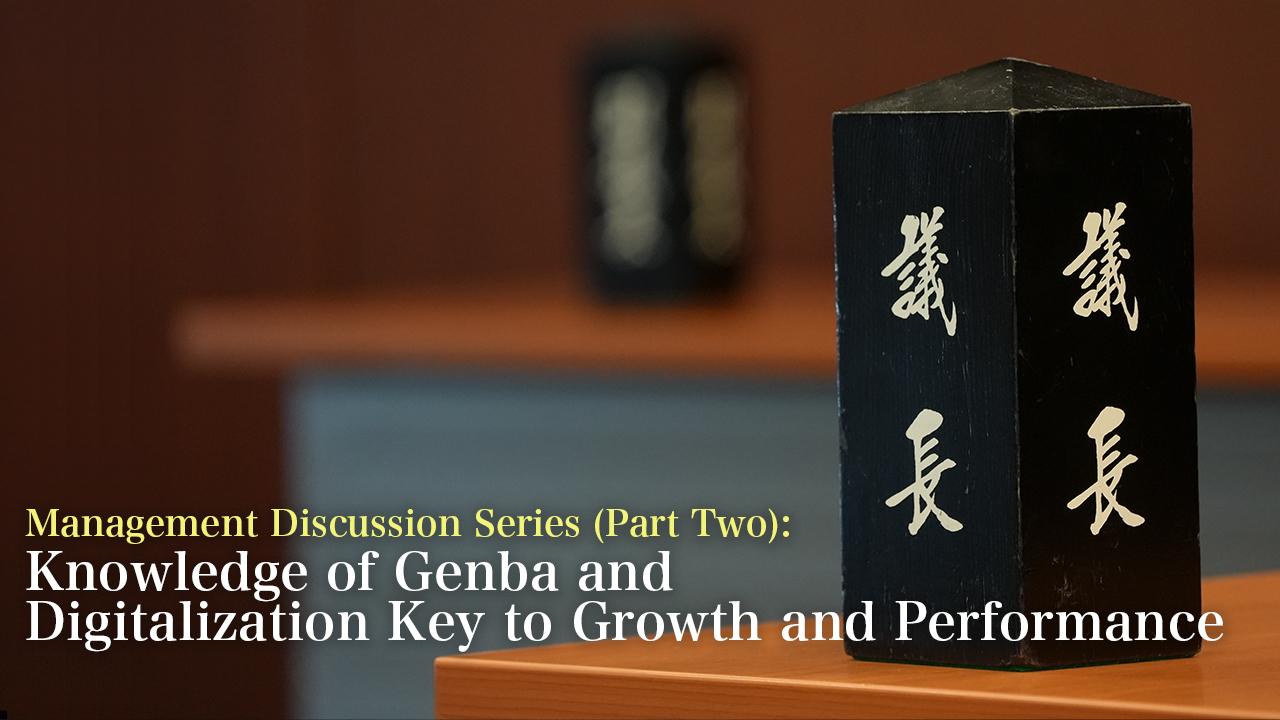
People grow by taking on challenges, whether at the genba where work is done or transforming the way a company operates. This discussion between management and employee representatives highlights the keys to growth and performance, bridging gaps, and combining efforts and wisdom to continue to improve.
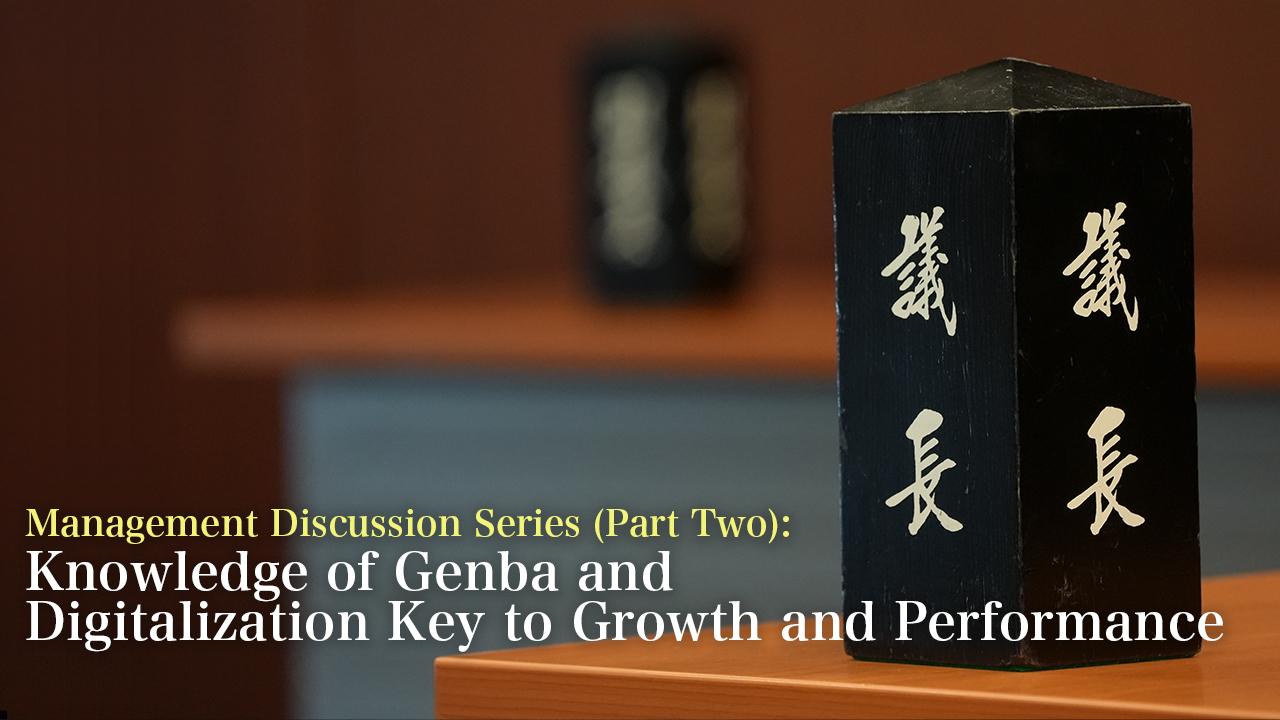
Every spring, TMC hosts discussions between company management and employee representatives. The year’s second session, held on March 3, focused on the topic of ‘growth and performance’. Participants shared workplace initiatives and examples of how to enable everyone at Toyota to grow and find fulfillment in their work. The topics of discussion even extended to TMC’s long-standing challenge of promoting digitalization.
More direct opportunities for growth
To begin the discussion, the workplace concerns of young workers in technical/production fields and office staff (engineers and administrative members) were presented.
They painted a vivid picture of the situation workers faced:
- Across-the-board training policies and job assignments make it difficult to advance in their careers
- Information gaps between departments slow down work progress
- A feeling of being unable to contribute to customer happiness due to having to coordinate so many tasks
- With parts development being increasingly outsourced, Toyota’s ability to get ideas down on paper in-house is lagging behind suppliers.
Many less experienced team members looking to grow and take on greater challenges sometimes find that they are prevented from doing so by job circumstances. There were calls to move beyond traditional frameworks and offer people more opportunities to tackle new challenges on their own initiative.
In response, Yoshihiro Nakata, Toyota’s Senior General Manager in charge of overseas sales and business, spoke from a management perspective.
Senior General Manager Yoshihiro Nakata
Since last year, as part of efforts to streamline our operations, we have been working to eliminate coordination tasks aimed at obtaining upper-level approval, and shifting towards a framework in which decision-making is based on direct dialogue between in-house company presidents and regional CEOs.
We have begun speeding up overseas assignments for team members to encourage growth and improve their knowledge of customers and genba.
Although the process is still underway, we want to clarify back-office roles for local and regional operations, implement TPS (Toyota Production System) for office positions and streamline their work, and further promote overseas assignments for less experienced team members.
Particularly in emerging countries, there are still many fields where our team members play an active role locally. We want to add more such opportunities, and combine these well with training and rotation.
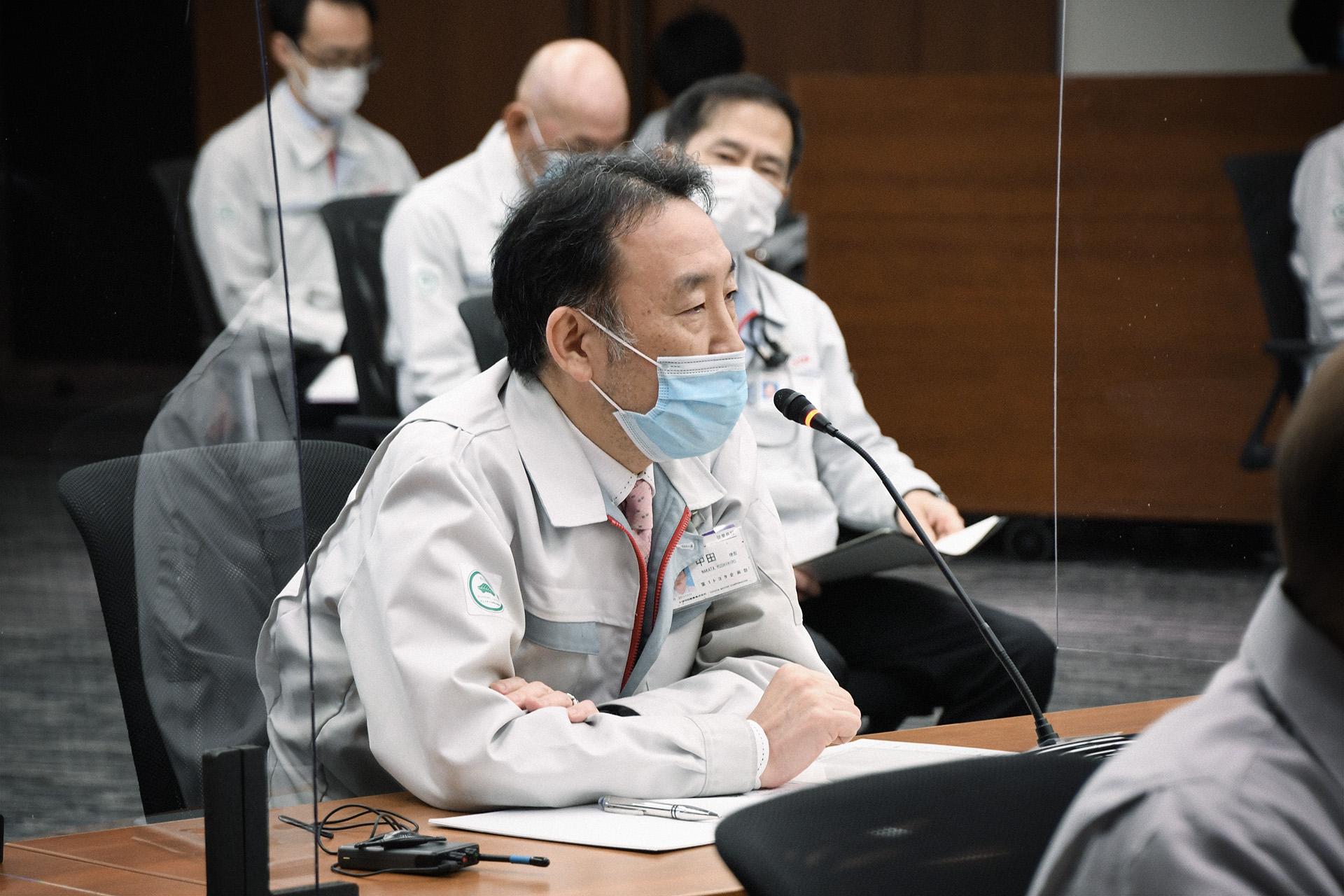
These remarks were followed by Operating Officer Koji Sato, president of GAZOO Racing Company. Using real examples, he emphasized the importance of taking a comprehensive view of car making, rather than subdividing processes, in order to make ever-better cars.
Operating Officer Koji Sato
I feel as though the number of jobs that can be completed within a single workplace or company is decreasing.
Car making itself is becoming increasingly complex. I think we have entered an era where even experienced engineers cannot be certain about the best way forward.
Against this backdrop, the development of the GR Yaris offers an instructive example. “Refine through racing, break, fix, and repeat”. This approach is completely different from what we’ve done before.
In the past, we would stop at proving that something didn’t break, but now we go until breaking point, then we fix. In doing so, we come to see issues which TS (Toyota Standards, design standards set by Toyota) cannot protect us from. I view this as a new approach to development, which President Toyoda has demonstrated concretely by putting his own life on the line.
Things happen in a race that we never imagined. In many cases, the cause of a problem is not apparent on the spot.
Unlike the preset patterns of problem-solving along TS guidelines, issues without a clear cause require all team members to directly confront the challenge.
I believe this kind of car development is one of the directions we must pursue going forward.
Even if the job or car you are working on is not directly linked to racing, confronting challenges with this mindset and working together as a cross-functional team allows us to face the unknown and move forward.
I believe that such approaches can bring our anxious team members together with experienced colleagues, who may be uncertain how to proceed, allowing them to address challenges and move forward as one.

The discussion was continued by Masahiko Maeda, the Operating Officer in charge of technology.
Operating Officer Masahiko Maeda
I think the past decade or so of consistent growth was a period in which, above all else, we prioritized getting as many cars out there as possible.
To supplement our own workforce, we also shifted to outsourcing technologies over which we had complete control at the time. Designs through the approval paperwork also increased. At the same time, the organization became increasingly fragmented and, without realizing, we began to lose control over our processes.
This situation came about precisely because we operated in a privileged environment, with ample funds for development. The result of blithely outsourcing was that we lost our competitiveness, including the ability to reduce costs.
The shift to the outside happened slowly over time. Now we are seeking to reverse that course, which I believe will be difficult to achieve in the short term.
On the ground, however, we are gradually making moves to regain control.
One example is the development of engine control units. Veteran staff who previously worked on in-house software development have teamed up with inexperienced team members to bring the production of ECUs for certain models in-house.
Naturally, those team members learned a lot.
Their efforts strengthened our competitiveness by reducing development lead time – software that previously took 5,000 hours to build was completed in 1,000 hours, with debugging time cut down from two weeks to one day.
I see this "internalization" as a key factor in making us more competitive.
The team members involved looked extremely pleased. Having done the job entirely by themselves, they felt the joy of contributing to the company and our customers.
I believe that greater emphasis on such approaches to work would benefit society and our customers.
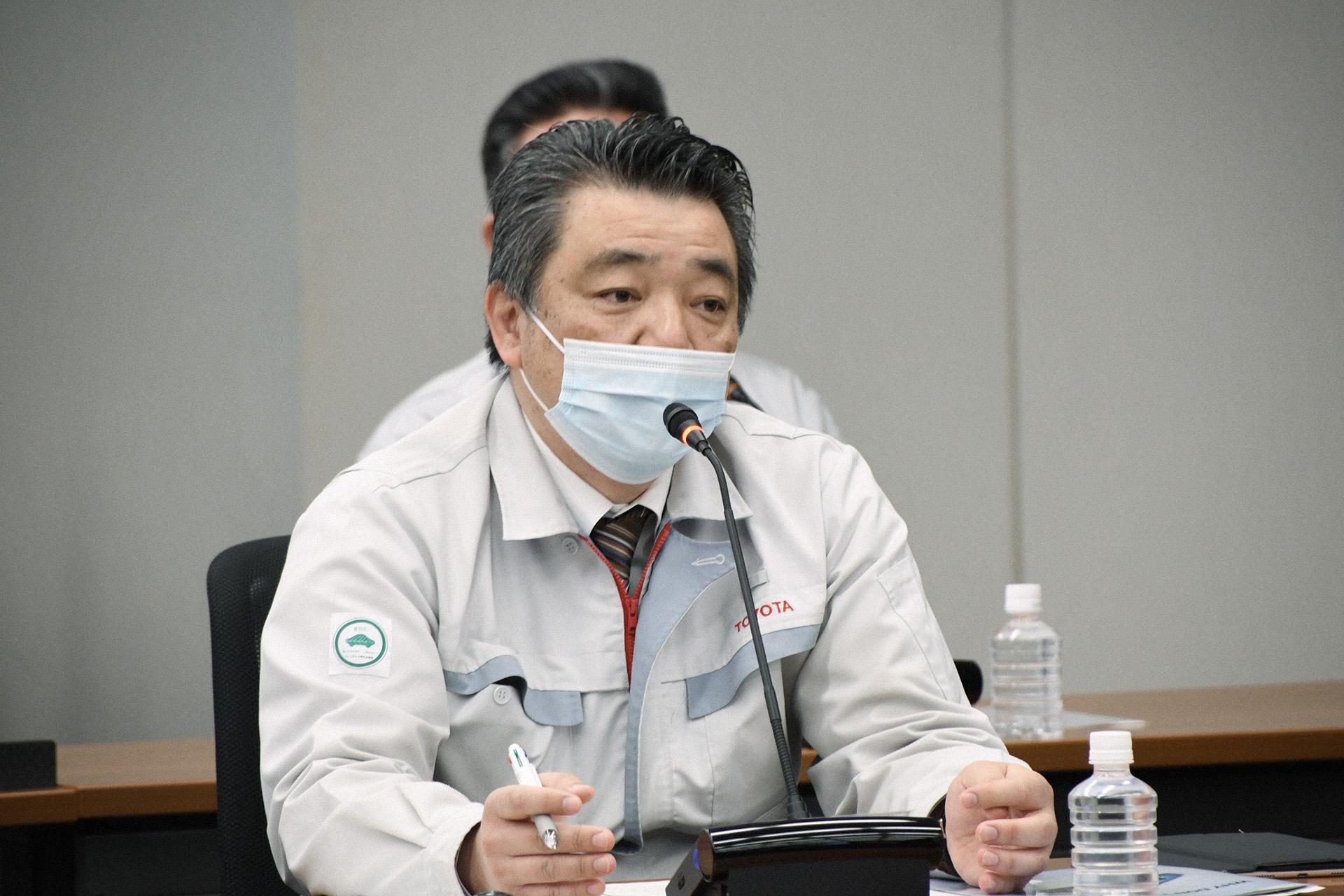
In the interest of giving every employee the opportunity to shine, the discussion then shifted to the topic of digitalization.
Creating world-leading work environments through digitalization
Team members conveyed the challenges that Toyota is facing in the digital domain.
They shared feedback from the genba, highlighting some additional areas for possible improvement, such as:
- IT infrastructure for better communication with external parties
- A way to share schedules among group companies
- An overall IT/digital working environment that facilitates work with both group companies and partners.
Responding to the feedback was Operating Officer James Kuffner, who serves as Toyota’s Chief Digital Officer.
Chief Digital Officer James Kuffner
We realize that there’s still more potential to improve especially at Toyota.
Within Woven Planet, we are experimenting to develop state-of-the-art processes and security policies. One of the principles of digital transformation that we are working on closely with Yamamoto-san, Maeda-san and Kitaaki-san is to promote what we call “cloud-first”.
This type of approach will allow much more seamless integration, and the new network architectures provide endpoint protection for both laptops and smartphones in the company. Many IT giants have already changed from traditional security protocols. This is going to be the future.
It will take some time to implement these changes, but we will do our best to accelerate them. You should not feel that IT infrastructure is slowing you down. It should be the opposite. It should be that IT infrastructure is supporting you, helping you be more productive, but I understand that we have many legacy systems that need to be replaced.
Some people are unhappy when things change. But please be patient as we try new systems to make it better and much more efficient for everyone. Woven Planet is able to deploy those changes and the goal is to use what works as the template and expand it across Toyota group companies.
If you can share specific stories on what experiences are the most difficult, then we will make a priority list to tackle them efficiently, concentrating on the biggest areas of concern. We have many, but we should prioritize the ones with biggest potential impact to improve people’s experience.
Security is the biggest problem in the world right now, but cloud technologies and new network architecture is evolving to be much more secure. We are going to transform, and I want Toyota to be the first automaker who successfully transforms digitally. Many other competitors are trying but it’s very difficult. If we work together, we can do it.

Upgrading IT tools is essential for communicating and sharing information in a timely way. Working to promptly address the most pressing issues, the conversation moved on to discuss the next steps forward.
As a proponent of ‘software first’ initiatives, Operating Officer Keiji Yamamoto vowed to make ‘bold investments’ in IT tools.
Operating Officer Keiji Yamamoto
Today’s generation of young people are known as ‘digital natives’. They were born into an internet-driven environment and grew up around IT tools.
Many of our new recruits and mid-career hires now fall into this category. Given their high level of IT literacy, I see it as only natural that they would have opinions about Toyota’s IT environment.
At the same time, IT tools are extremely varied. The tools that young people and older colleagues find easy to use may not necessarily be the same. A company-wide push to improve the IT environment takes a great deal of time and effort.
As a company, we want to consider what IT tools are appropriate for the younger generation of digital natives and make bold investments, rather than simply continuing along the same trajectory.
Naturally, gaps will emerge between younger and older generations. To bridge these gaps, we also plan to provide support akin to the role played by interpreters.
The important thing is not only merely building a better IT environment for Toyota, but also having a positive impact on the entire automotive industry, including dealers and suppliers.
Doing so would enliven communication throughout the industry, and I believe that is the mindset we need to have.
By putting forth our combined efforts and wisdom, we can create something good, and then expand it beyond Toyota. That is the approach I would like to take.

Regardless of success or failure, people grow by taking on challenges
During this session, the discussion focused on the growth and success that all those who work at Toyota are striving for. It concluded by reaffirming the importance of taking on challenges.
Chairperson Mitsuru Kawai
People feel happy when a challenge they tackled at work receives praise from colleagues, or the boss smiles and says, “This is great, you’ve made things a lot easier”.
Regardless of age, education or qualifications, giving each individual the opportunity to challenge themselves and feel recognized by those around them naturally makes workplaces more dynamic.
When production halted due to COVID-19, I was stunned to see that productivity exceeded expectations even as production fell, as everyone moved quickly to reduce costs and focus on kaizen. Workplaces have undergone great changes in recent years, and I feel that the resulting trend has been positive.
Regardless of success or failure, people grow by taking on challenges. I believe that taking on challenges leads to job satisfaction and happiness, and wins the trust of everyone working in the automotive industry.
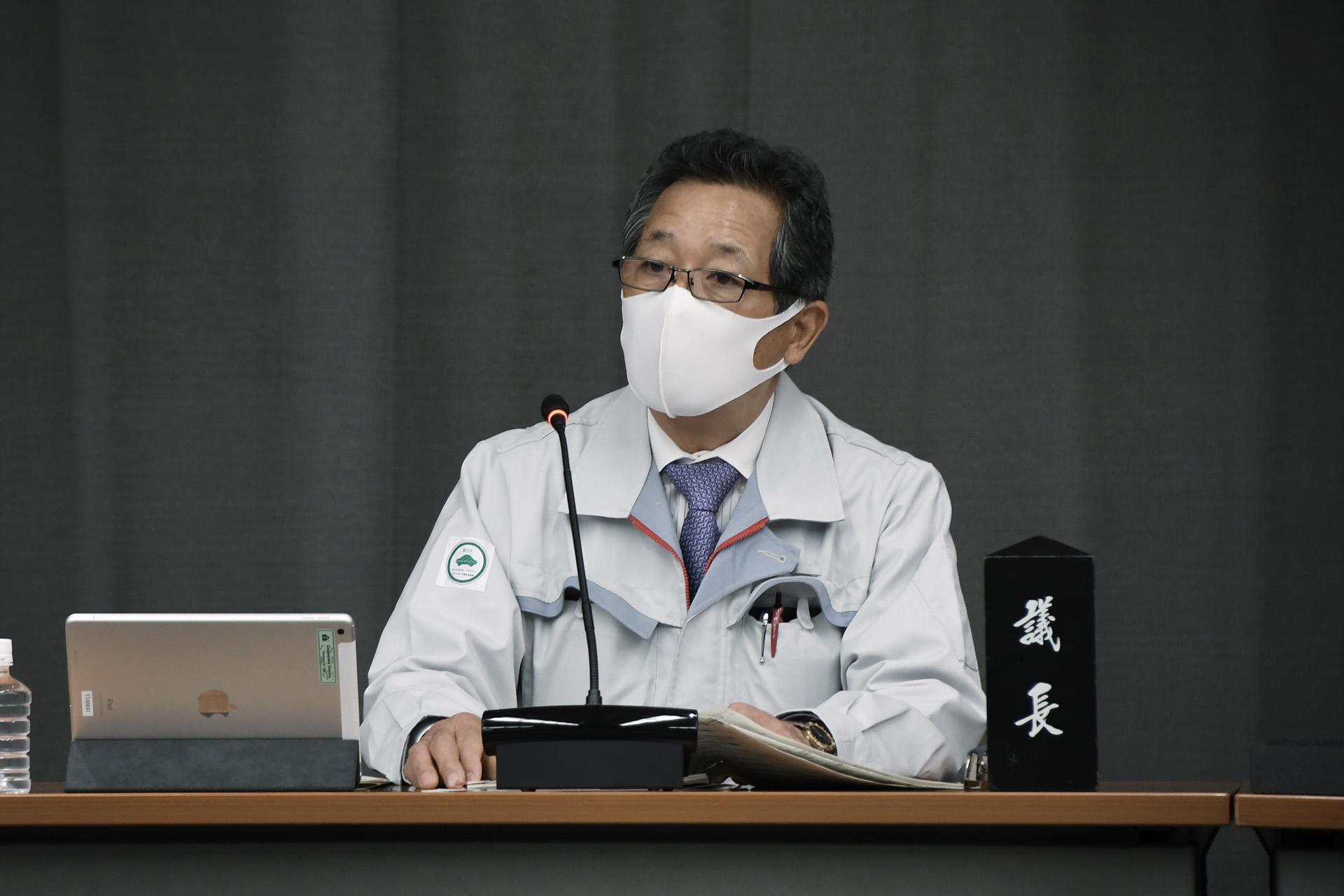
In Part 3 of our management discussion series, the discussion surrounds the Toyota Production System (TPS), where Toyota Times will share management’s response and explanation regarding skills and concepts central to all Toyota employees.