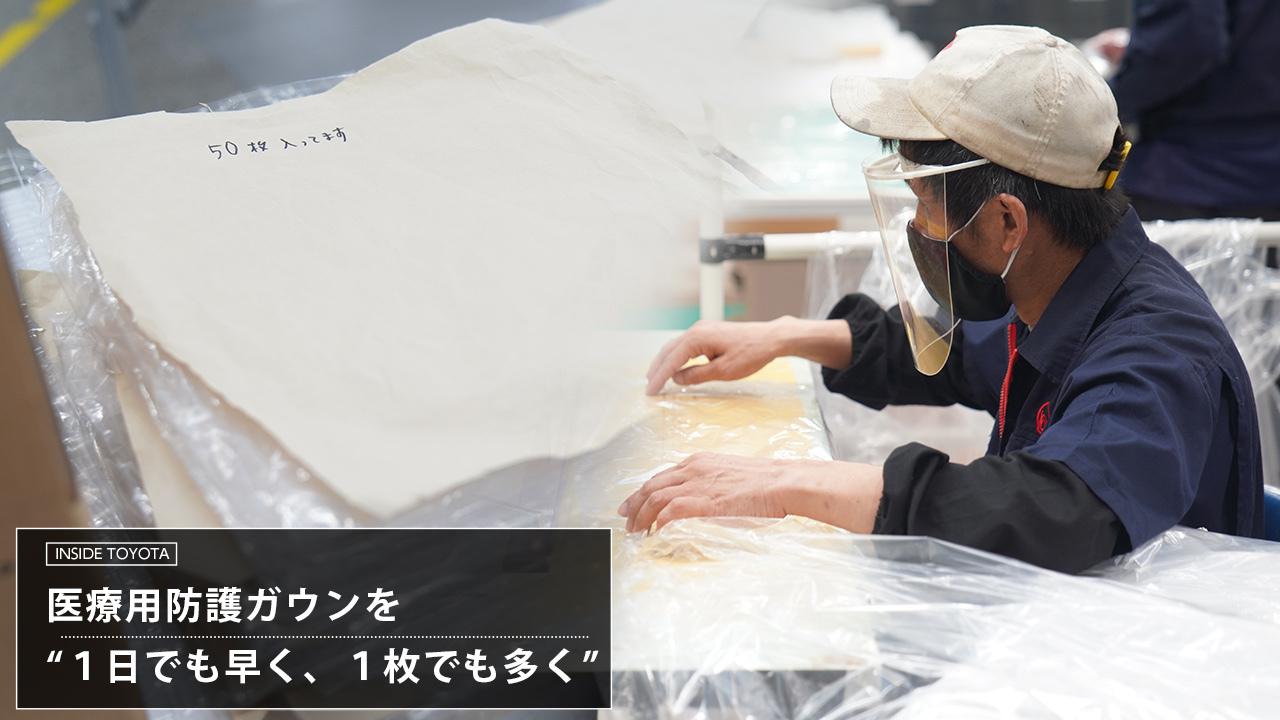
医療用防護ガウンを1枚でも多く作ろうと頑張る現場に入った"改善"とは?
5.船橋に入った改善メンバー達
防護ガウン生産は、大きく4つの工程に分かれる。
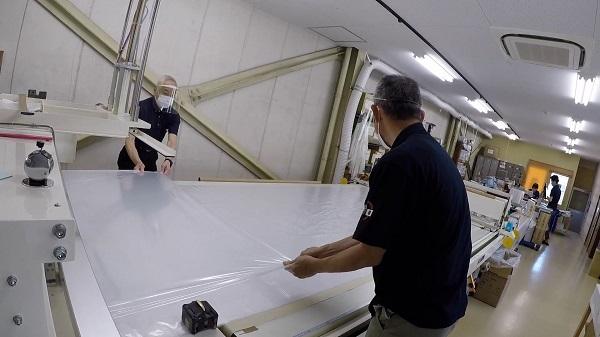
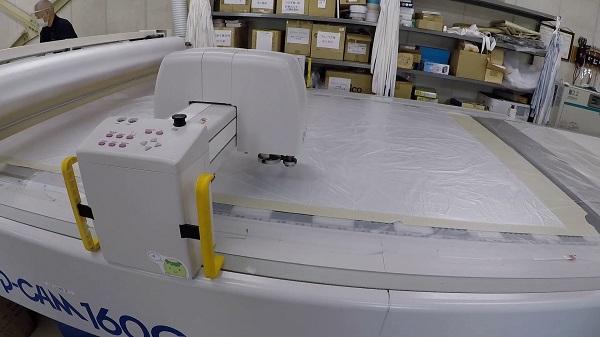
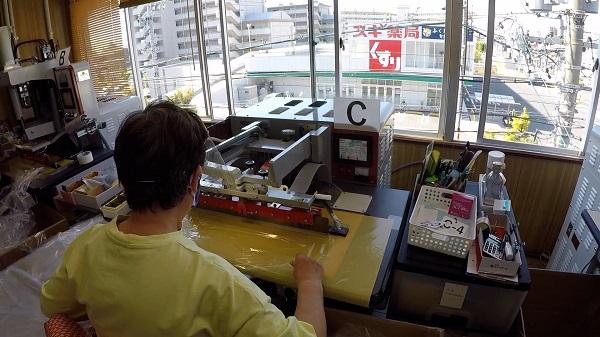
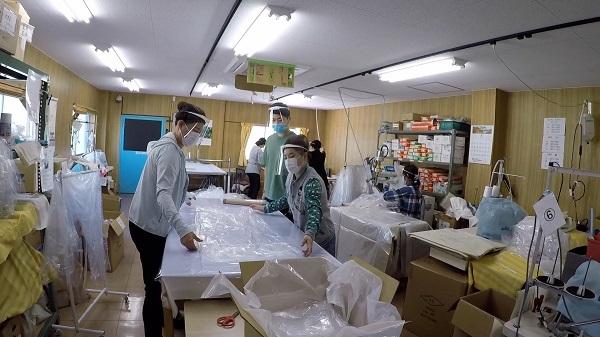
船橋に入った改善メンバーは、初日から現場作業を手伝いはじめた。
トヨタイムズが取材に入ったのは、一緒に作業を始めて4日目であったが、作業風景を見ていると、ずっと一緒にやっているかのような“和気あいあい”な雰囲気があった。誰が船橋社員で、誰がトヨタか?全く分からないほどである。
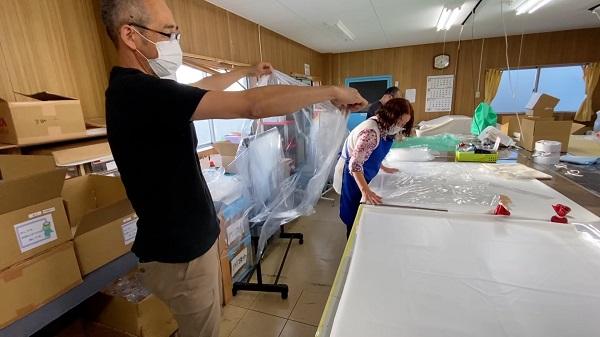
少し余談になるが、船橋の人たちは“トヨタが協力にくる”と聞いた時、そこまでの期待はしていなかったと言う。「どうせ大企業から来るのは、せいぜい若い担当者ひとりだけだろう」と思っていたらしい。
トヨタがやってきた初日、舟橋社長が、少し離れた駐車場に迎えにいってみると、車から降りてきたのは“8人の熟練そうなおっちゃん達”だった。予想以上に頼りになりそうな面々の姿に「アベンジャーズかと思った」と舟橋社長は笑いながら語っていた。
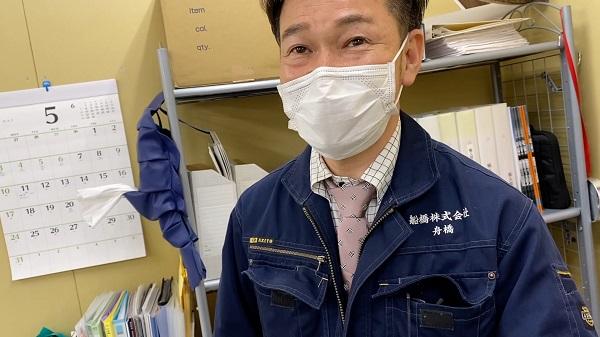
アベンジャーズの改善の一歩目は“実際に作業にはいる”ことだった。「どこがやりにくいのか?」「何がネックとなって滞るのか?」を一緒に作りながら見つけ出す。
はじめに見つけた“最大のネック”が「工程間の能力のアンバランス」だった。
最初の工程(工程1)では一度に10枚しか作れないのに、次の工程(工程2)は30枚を一気に作れる。
これだと、30枚作れる工程2に、流し込める材料が10枚しか揃わない。その差の20枚分の生産能力が無駄になっている。
そこに目をつけ「どうしたら工程1を3倍の速さにできるか?」を考えていくことになる。
6.どんな改善で差を埋めたのか?
工程1に新しい機械を導入したわけではない。一緒に作業をしながら「こうした方がやりやすい」という細かな工夫を探し出していった。
この工程1は、大きく2つの作業が行われる。
キッチンにあるラップの大きい版をイメージしていただけると分かりやすい。
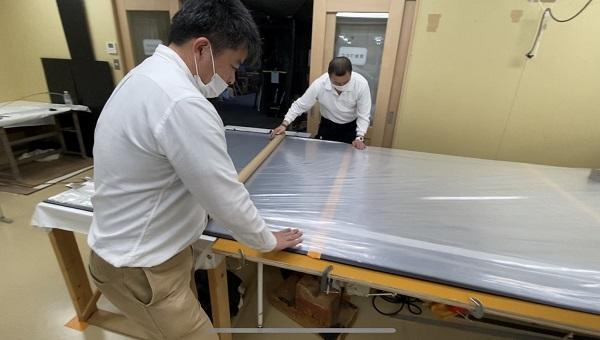
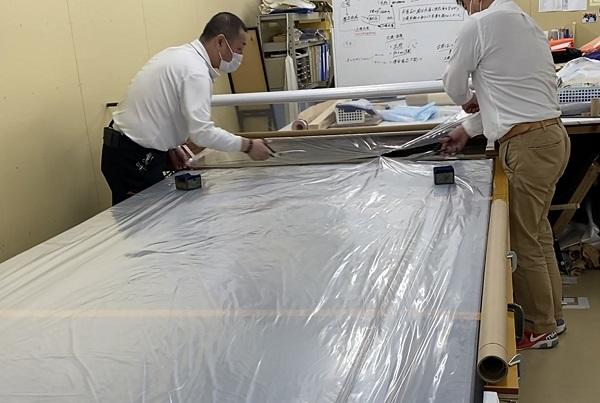
アベンジャーズ達は、この作業(1)(2)の中にある“やり難さ”を探した。
(1)では、作業台の上で、ロールから素材(ポリエチレン)を正しい位置まで引っ張り出す必要がある。
当初、作業台の盤面は白色だった。そこに透明な素材を引っ張り出しても、白い台との境界は見え難い。そこで盤面を黒に変えた。それによって、どこまで引っ張り出したかが見て分かるようになる。
また、引っ張り出した素材を固定するクリップや重りも用意した。更には、スッとハサミを手に取れるように、特製のハサミホルダーも手作りした。こうした、工夫を積み重ねるだけで作業性は驚く程上がっていった。
他にも、作業をしていて気づいたところを、どんどん改善していった。結果、10枚しか切り出せなかった工程1は、4日後には30枚切り出せるようになっていた。
袖の部分を溶着する工程では、使われていなかった半世紀前くらいの設備が使えることに気がついた。眠っていた設備だったが、メンテナンスしてみると見事に動き出した。
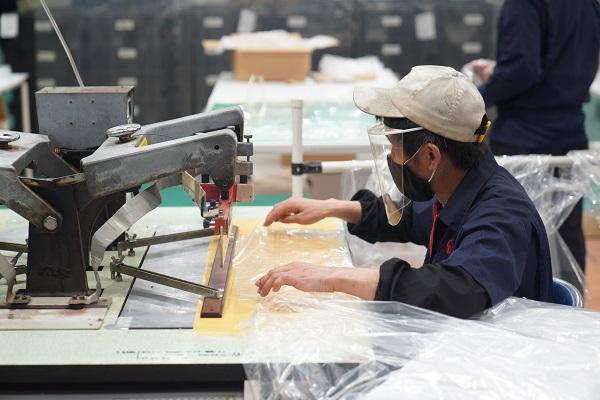
道具や設備を増やしただけではない。作業時間の短縮にも取り組んだ。
当初は1着分の溶着をするのに、ベテラン社員でも70秒、未経験者なら90秒の時間がかかっていた。しかし、作業のコツをみんなで出し合い、それらをまとめた映像を作った。コツを共有した結果、現在は、速い人なら30秒、慣れない人でも60秒を切れるくらいになっている。
7.1分の改善が生み出す価値
作業そのものの改善の他に「工程間のモノの流れ」の改善というのもある。
工程3「袖の溶着」が完了したら、防護ガウンとしては完成である。しかし、そのままでは出荷できないので、工程4で“たたんで、梱包”する。
従来、工程3では袖の溶着が終わると、横に置いてある箱に、クシャクシャのまま、落とすように入れていっていた。
その箱を運び、工程4の作業者は、シワの寄った製品を「取り出して→広げて→前後表裏を確認して→シワを伸ばして→畳んで→箱詰めする」という作業をする。
こうやって書き出すと「なんで箱に入れる必要があるんだっけ?」「クシャクシャに入れたら、わざわざシワを伸ばさないといけない」と簡単に気がつく。こういうところの “ムダ”に改善が入る。
このように“改善”とは“聞いてしまえば、とてもシンプル”なものである。
「シワを伸ばさないといけないなら、はじめからクシャクシャにしなければいい」
ただ、それだけと言われれば、“ただ、それだけ”である。
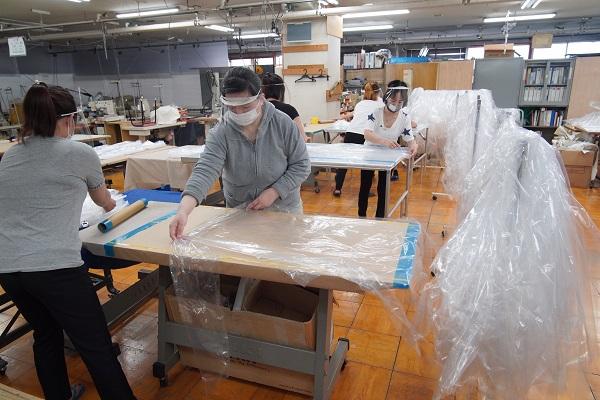
この改善のために持ち込まれたのは市販のハンガーラックだった。
工程3でクシャクシャにせずハンガーラックに掛けていく。ハンガーラックは、そのまま次の工程までコロコロと運ばれていく。
これならシワは寄らない。前後も、表裏も、わざわざ確認しなくていい。これで作業時間は“1分”短縮された。
1分と言われると、その効果はわずかに感じる。しかし船橋が、納入先である政府に話した生産量目標は40万着/月であった。
1分の短縮はトータルで40万分の短縮になる。これは6666時間であり、277日である。1分の積み重ねが“1日でも早く、1枚でも多く”の実現に繋がっていくのである。
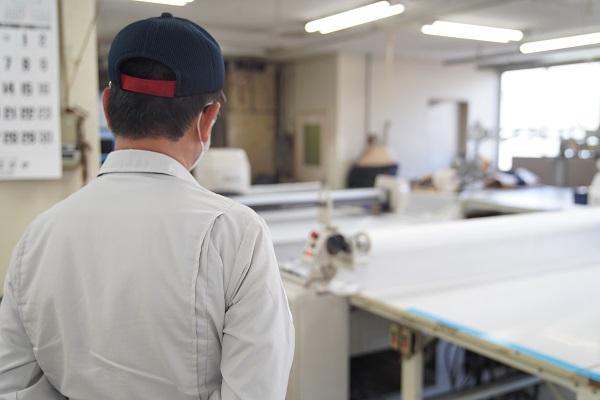
これらの改善は、知恵と工夫で行われたものばかりである。
「やり難い」と思ったことが改善の種となる。それらひとつひとつに向き合って“ムダ・ムラ・ムリ“を無くすための知恵を出し合っていく。そして簡単には、自動化に頼らない。
前述の改善に大きな投資(コスト)は伴っていない。今後、こんなに大量の防護ガウンが要らなくなる日が、きっとやってくる。その時に不要になる設備は極力入れてはいけないという考えでもある。
原点に返ることで多くを学び、活き活きと支援させて頂けている。自分達にとっても“トヨタ生産方式の実践教育の場”だと思った。
アベンジャーズも、そう話していた。
8.月産40万着の約束
船橋でつくる防護ガウンは一旦、政府が買い取って、そこから各医療機関に渡っていく。(一般販売は行なっていない)
そうした流れが決まる前、納入方法や数量についてのテレビ会議が行われていた。そこには省庁の担当者、舟橋社長に加え、アベンジャーズの1人も出ていた。
省庁の担当者から「どれぐらい作れますか?」という質問があった際、その問いにアベンジャーズも答えた。
船橋さんの製品と工程は判り易いので、ここで改善したノウハウを希望する数社に拡げれば、各社5-10万着/月で40万着/月ぐらいは可能と思われます。
舟橋社長は一瞬耳を疑ったという。そもそもの船橋の生産能力は1万枚/月(日当たり500枚)である。生産性向上を入れるとはいえ40倍である。
現場での改善ぶりとアベンジャーズの真摯な取り組みが他社に展開されれば、自分の想いが更に実現し、医療現場を大きく助けることになる
驚きながらも、掲げられた目標に奮い立った時の想いを、舟橋社長はそう振り返っていた。
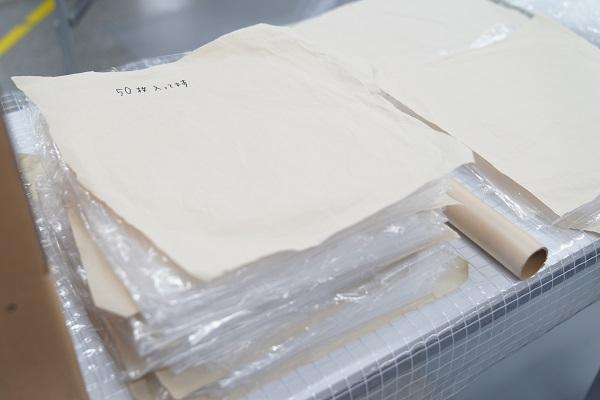
トヨタイムズが船橋に最初に取材に行ったのはアベンジャーズが入って4日目である。その時、すでに生産能力は日当たり2000枚(4万枚/月)と当初の4倍まで生産能力は向上していた。
その後ゴールデンウィークを挟んで、さらに2週間が経った時の再取材…。
船橋の工場長 森さんが朝礼で前日の生産実績報告をしていた。
裁断4104枚、加工4262枚、たたみ4199枚。
全部門で4000枚を達成できました。特にたたみの部門では、毎日毎日、前日の実績を超えてくれています。また皆さん、力を合わせて大きな目標に向かってやっていきましょう。
生産量は日当たり4000枚と当初の8倍に増えていた。月産に換算すれば8万枚。生産性向上の結果は確実に出ていた。
ただ、船橋1社では約束の月産40万枚には、まだまだ届かない数量である。
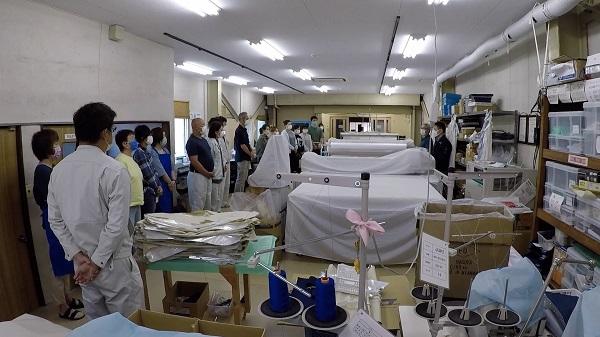