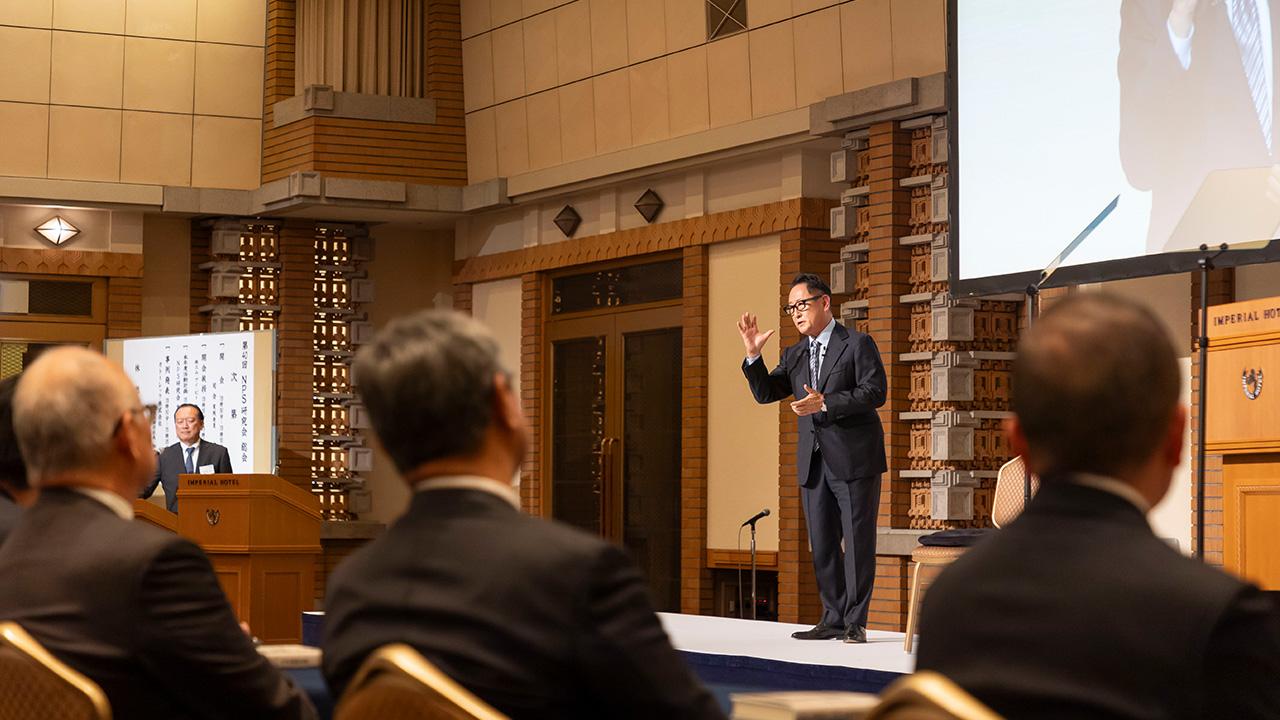
Chairman Akio Toyoda gave a lecture on the Toyota Production System to an audience of 200 corporate managers and executives. During the Q&A session, he answered questions on leadership and management decisions.
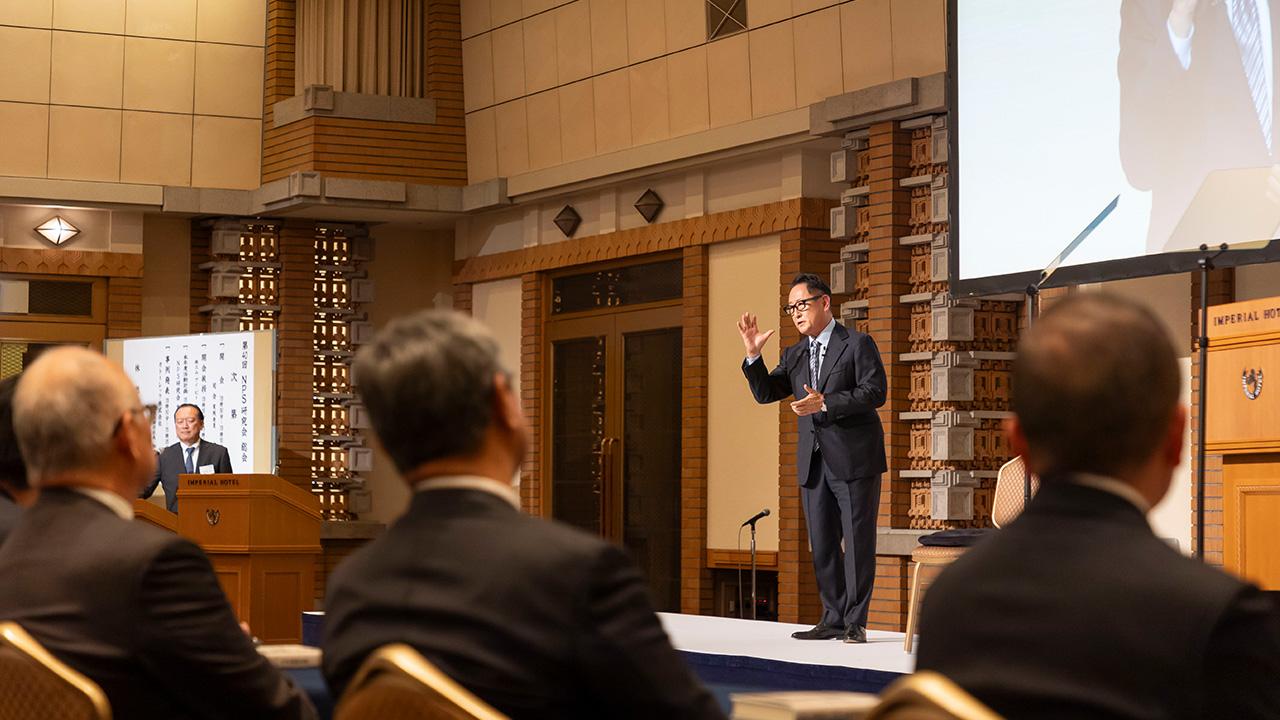
At the NPS Management Institute’s 40th general meeting held on January 13, Chairman Akio Toyoda gave a lecture on the Toyota Production System (TPS) to 200 corporate managers and executives.
Over the course of 45 minutes, he explained how a TPS-driven perspective had underpinned the numerous management decisions made during his presidency.
In the Q&A session that followed, Akio answered questions from the assembled heads of various manufacturing companies.
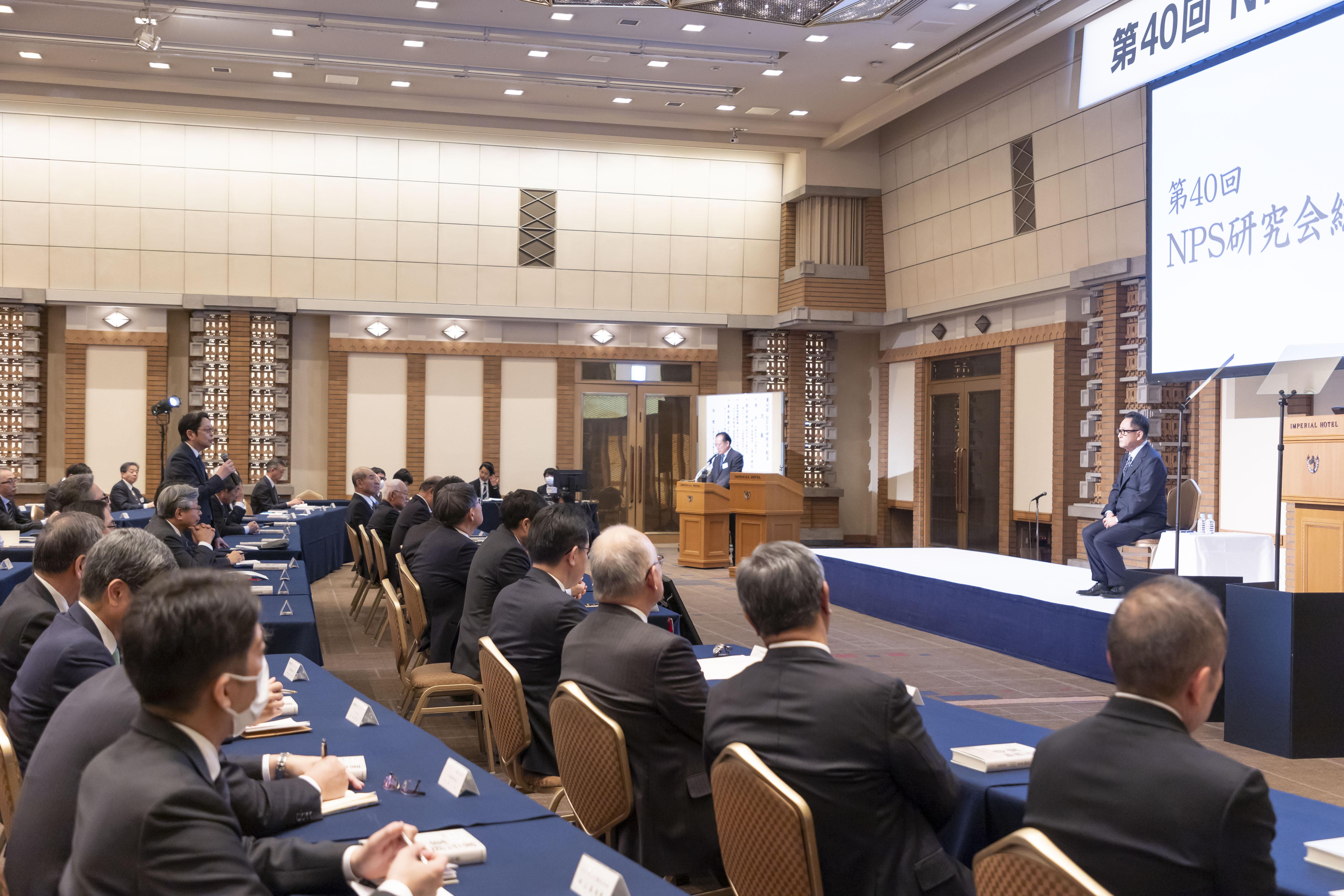
As managers running their own companies, the attendees naturally asked questions about leadership and management decisions.
While taking the time to share various anecdotes from his own experiences, Akio explained the “two roles” of a manager.
Here are Chairman Toyoda’s responses to five questions from Japan’s manufacturing leaders.
*An overview of the NPS Management Institute can be found at the end of this article.
The problem with PDCA
Amid all these shifts in the business environment, what aspects of the company should you change or not change? What is your perspective in making these decisions?
Chairman Toyoda
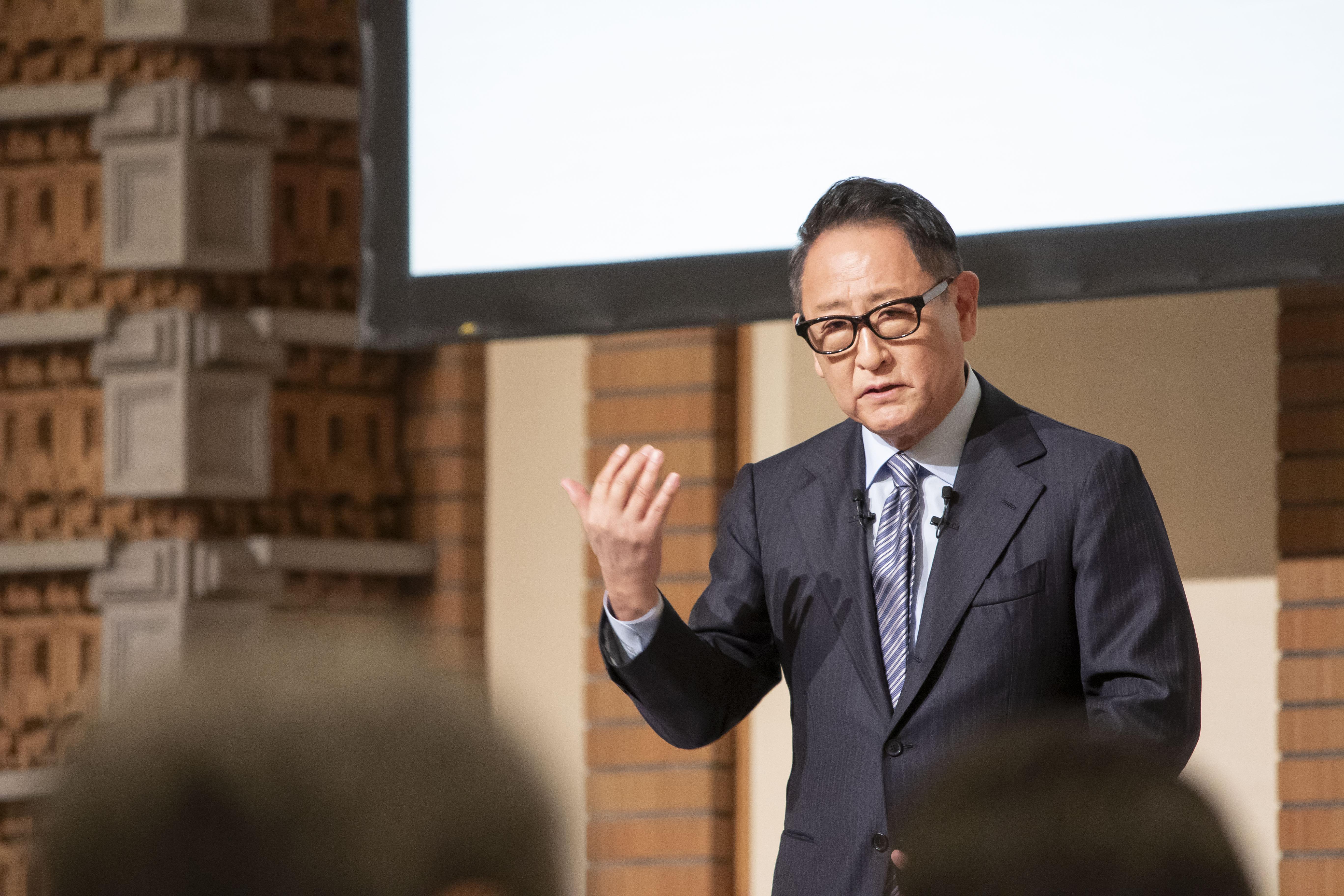
I started by clarifying the things that I must not change and the things I must never do.
Aside from that, I base my decisions on what I feel is necessary for adapting with the times, to ensure the company can continue growing sustainably over the long term.
That said, the situation has now changed somewhat. Right now, there is no right answer. What do you do when there is no right answer, such as with carbon neutrality?
In the auto industry, the U.S. and Europe used to lead the way, and we competed by trying to outdo them.
But now, as we started to pull ahead, Toyota is not necessarily on the right track when it comes to major turning points such as CASE. Yet, if we do not make changes, we are sure to fall behind.
In the past, people talked of PDCA—Plan, Do, Check, Act—but putting “Plan” first gets the order wrong. That’s why we start by “doing.”
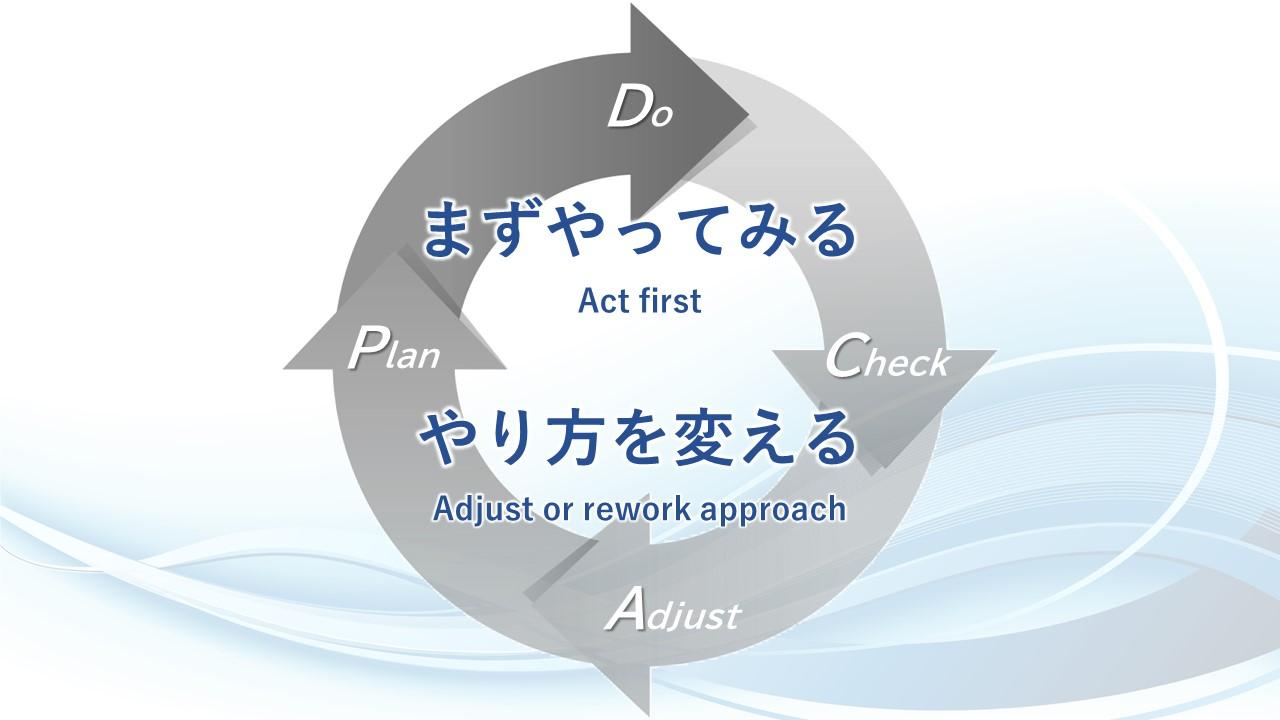
I said that GAZOO was about change, yet that transformation took the 14 years of my presidency.
Every day, employees have the chance to come and consult me about various things. I visit various genba and make comments. By repeating this process, gradually and gradually, people get a better idea of what must not be changed under this president and what must keep up with the times.
Hence, it took 14 years to build up. But I think it can fall apart a lot faster.
Why Toyota people are unfamiliar with TPS
A few years ago, I heard that you set out to make Toyota’s white-collar staff more familiar with TPS. Could you share the difficulties you encountered?
Chairman Toyoda
When trying to introduce TPS in the sales division, together with Shigeki Tomoyama (Chief Officer of Toyota Japan Sales Business Group and Chief Advisor at NPS Management Institute), I established a team to improve operations.
We saw TPS as a corporate philosophy, not merely a means of boosting efficiency in the production genba.
But the attitude of white-collar staff was, “We do the planning and thinking, which is nothing like the process of making things in a plant.” We constantly struggled to get our foot in the door.
However, when I remarked that I had “never felt so much distance” during a conversation with employees (at labor-management discussions), this sent a shockwave through the company, with some asking, “What in the world is the president talking about?”
People tend to assume that everyone at Toyota is a TPS expert, yet in reality, it is those inside the company who have little knowledge of TPS.
Things don’t happen by me telling people what to do, so instead, I created opportunities for employees to put TPS into practice, capturing the aspects they wanted to learn and going through them one by one.
First, I went into the Accounting Dept. and observed the processes. In doing so, I found areas where information piled up. Just by eliminating some of that congestion, the work became much easier.
In Japanese, the words “easy” and “fun” are written with the same character (楽). So, I first set out to make work easier and more fun.
TPS and kaizen are about making work more efficient, but those who see themselves as “knowledge workers” seem to be extremely resistant to such concepts.
I, therefore, wait for the moment when they feel compelled to do it themselves. I think that was the period you were referring to.
However as you are aware, once you embark on TPS initiatives, you must keep them going. I believe this is what builds the TPS philosophy, skills, and conduct.
The moment management overlooks a genba that is out of step with the TPS philosophy, that’s when the unraveling begins. You need to keep pointing out when things aren’t right.
In that sense, a company that embarks on TPS has a tough road ahead. It’s hard work, but that’s how things change.
And if you can foster a mutual sense of pleasure in increasing the amount of time employees spend doing more valuable work, I think the TPS mindset will endure.