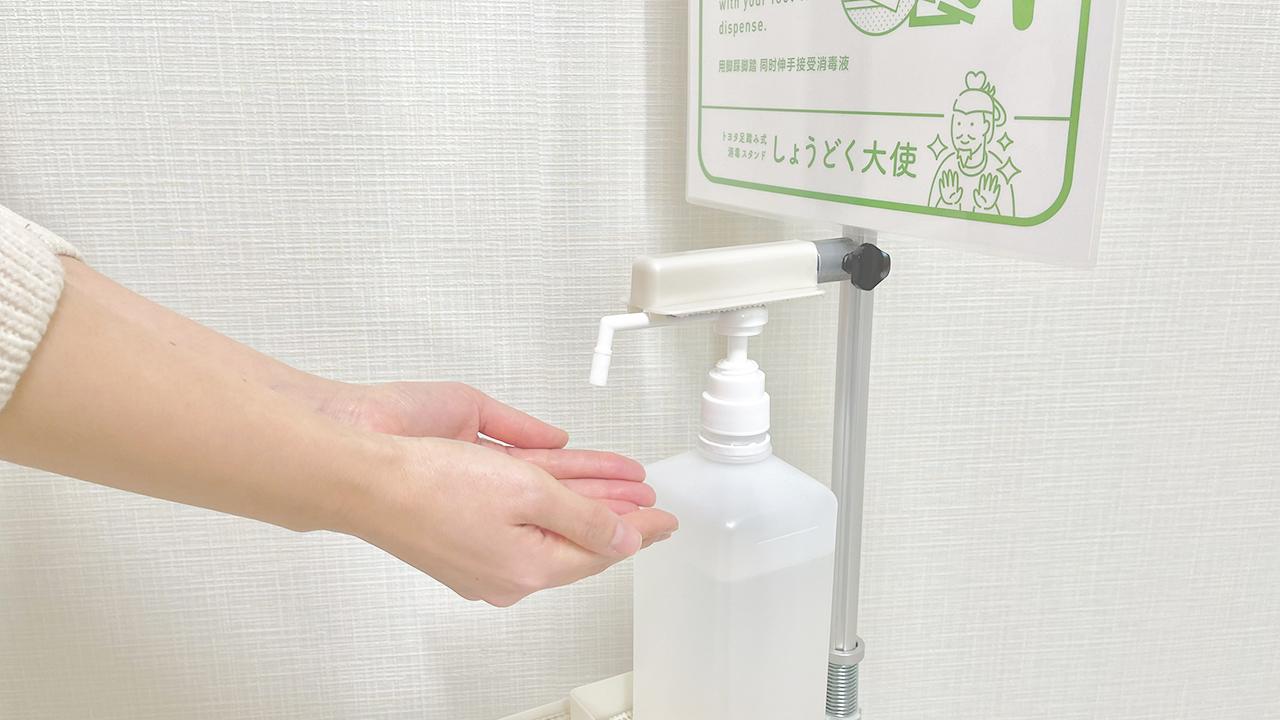
Toyota makes and sells a foot-operated hand sanitizer dispenser stand? Toyota Times was on the trail to find out why.
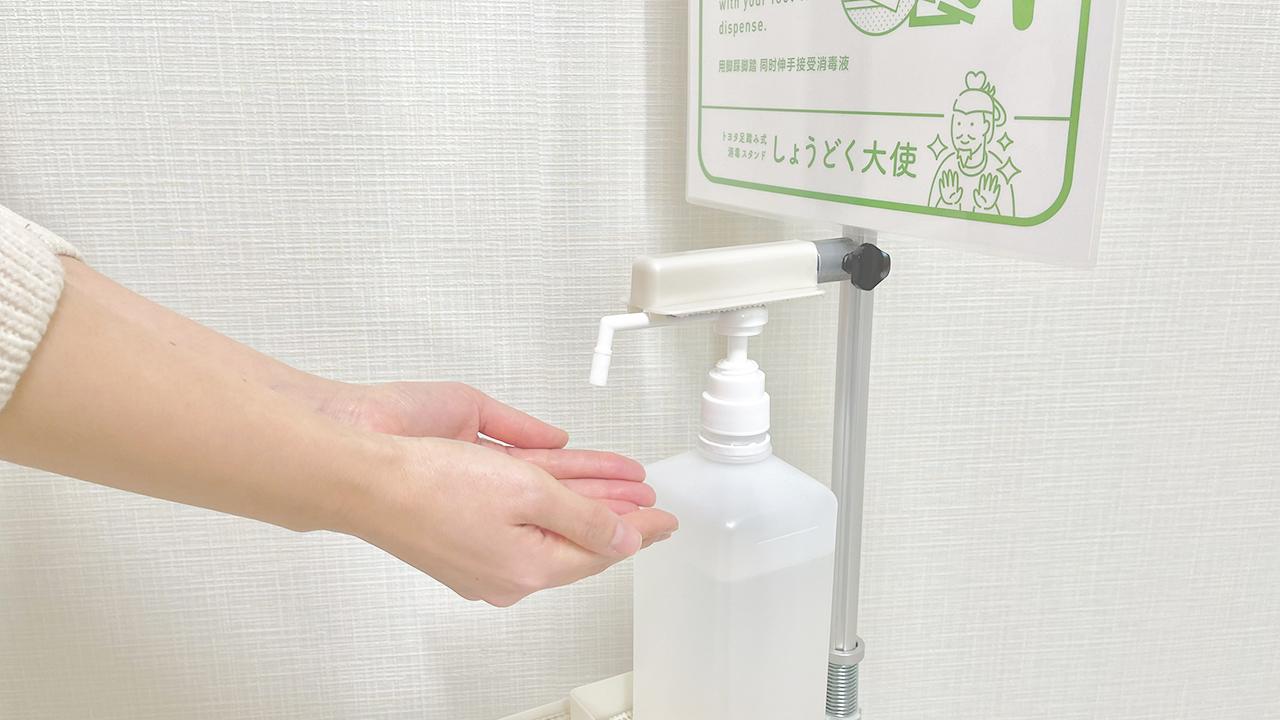
In working to combat COVID-19, Toyota has manufactured face masks and face shields, and also helped increase the availability of much needed items like those of medical protective gowns using its knowledge of the Toyota Production System (TPS), together with other companies, to improve production processes.
Now, Toyota announced the sale of a foot-operated hand sanitizer dispenser stand it has named "Shodoku Taishi". (Find out later in the article what it was named after and why.) Starting from December 2020, the stand is being offered through its retail network in Japan that includes Toyota dealerships and Toyota Rent-a-Car stores. There are many variations of hands-free dispensers available, so why did Toyota think it needed to also make one? Toyota Times was on the trail to find out.
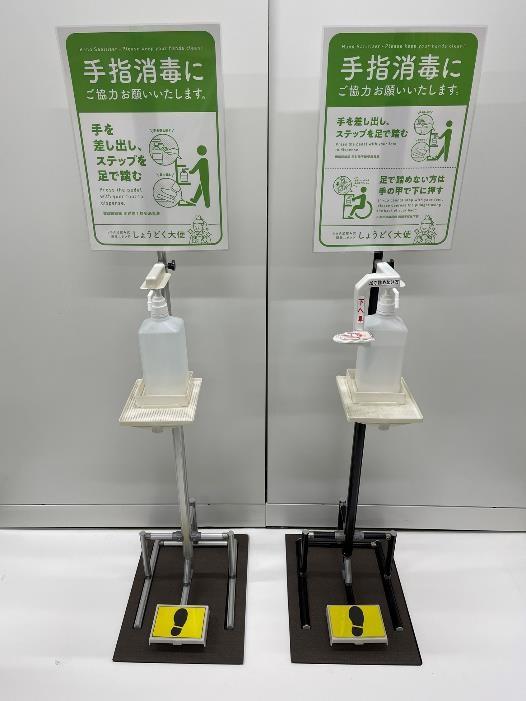
Designed with a desire to protect colleagues and families
In spring 2020, even before the full-scale spread of COVID-19 in Japan, Toyota employees were already producing foot-operated sanitizer stands at each of Toyota’s plants in Japan.
When asked about how the idea started, the response was universal – no one knew who first created the sanitizer stand.
The stands were not produced based on orders from a manager, nor was it from a competition with other plants. It was an idea that came naturally from a genuine and strong desire to protect colleagues and their families, and the stands were already being made at various places inside the company.
Later, when plant production lines were halted across Japan (and most of the world) due to COVID-19, each Toyota employee thought about what they could do to help. Among the employee-generated ideas, there were various different versions of a sanitizer dispenser stand.
After receiving the initial design ideas, the TPS professionals made repeated improvements (following the philosophy of kaizen) which eventually led to the stand’s completion.
All are at risk; must be easy for everyone to use
In order to help prevent COVID-19, it was important that the sanitizer dispenser stand was both easily accessible and could be installed anywhere. For this reason, numerous improvements were made to its height, weight, and stability, resulting in 30 different prototypes.
The finished product is height-adjustable so that it can be used by children. There is also a hand-operated lever for accessibility for wheelchair users.
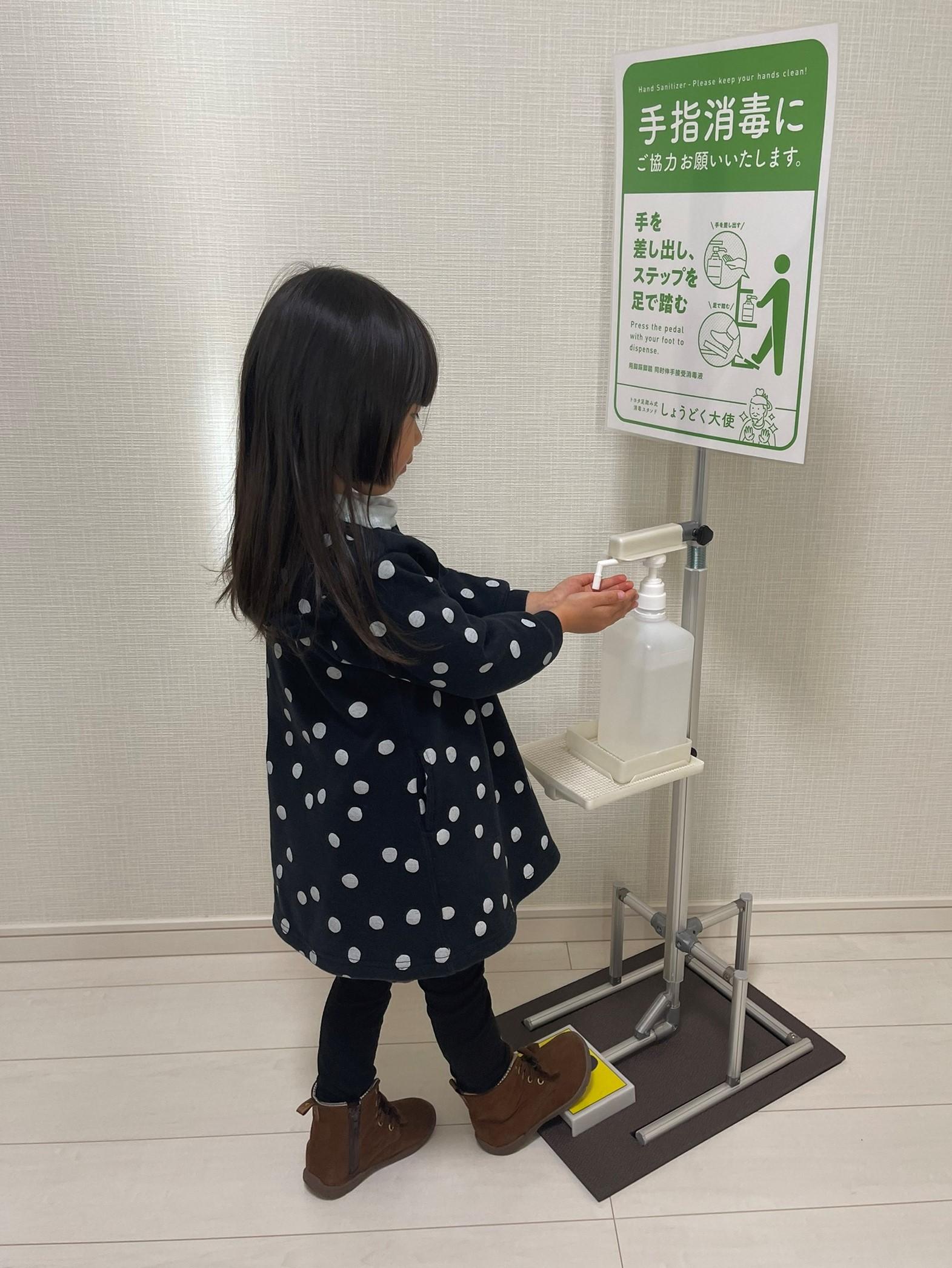
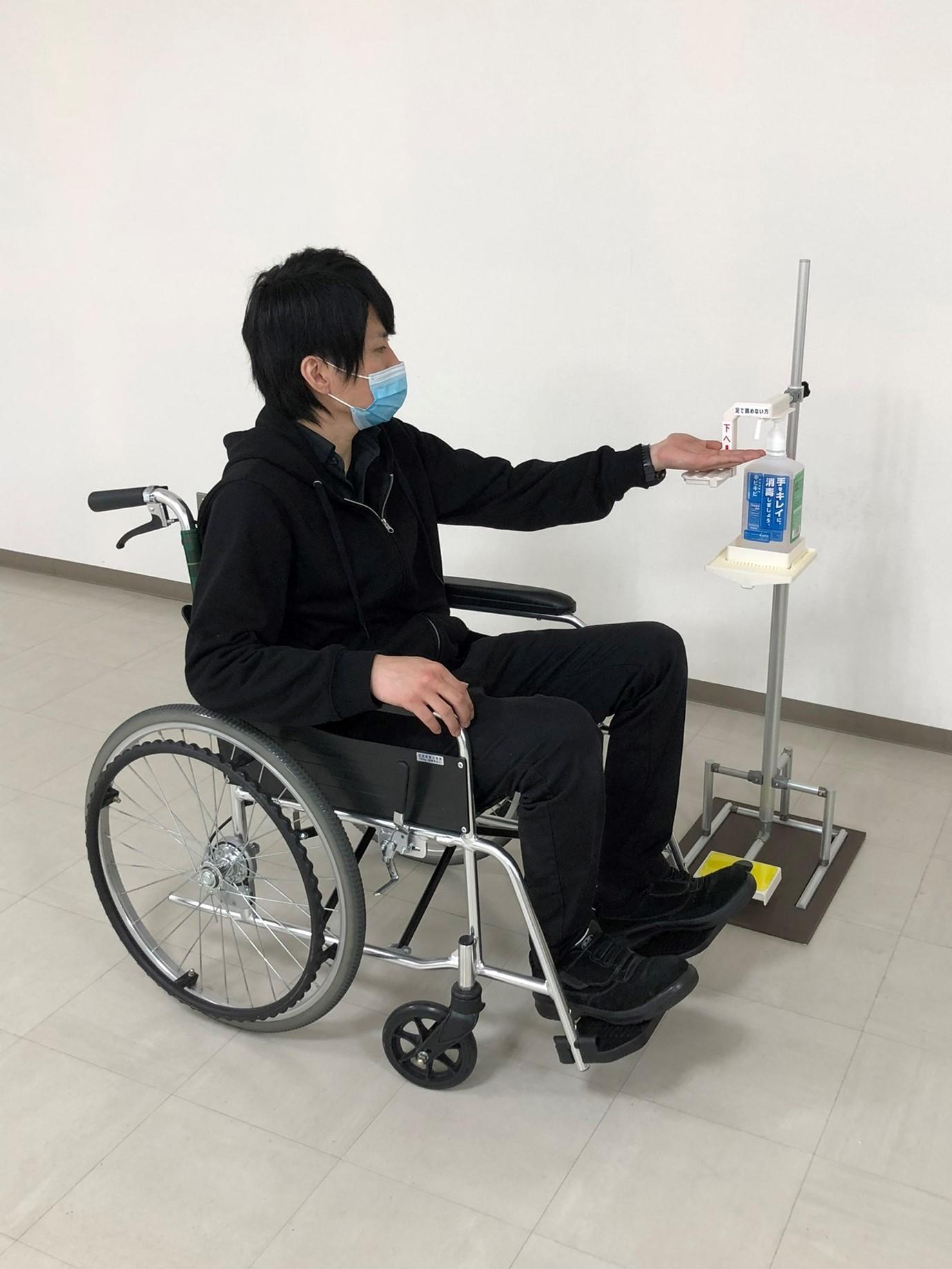
While the initial weight of the stand was 6kg, this has been reduced to 3.2kg, with no loss in stability. With a number of color variations available, customers should be able to find a stand that will match their needs.
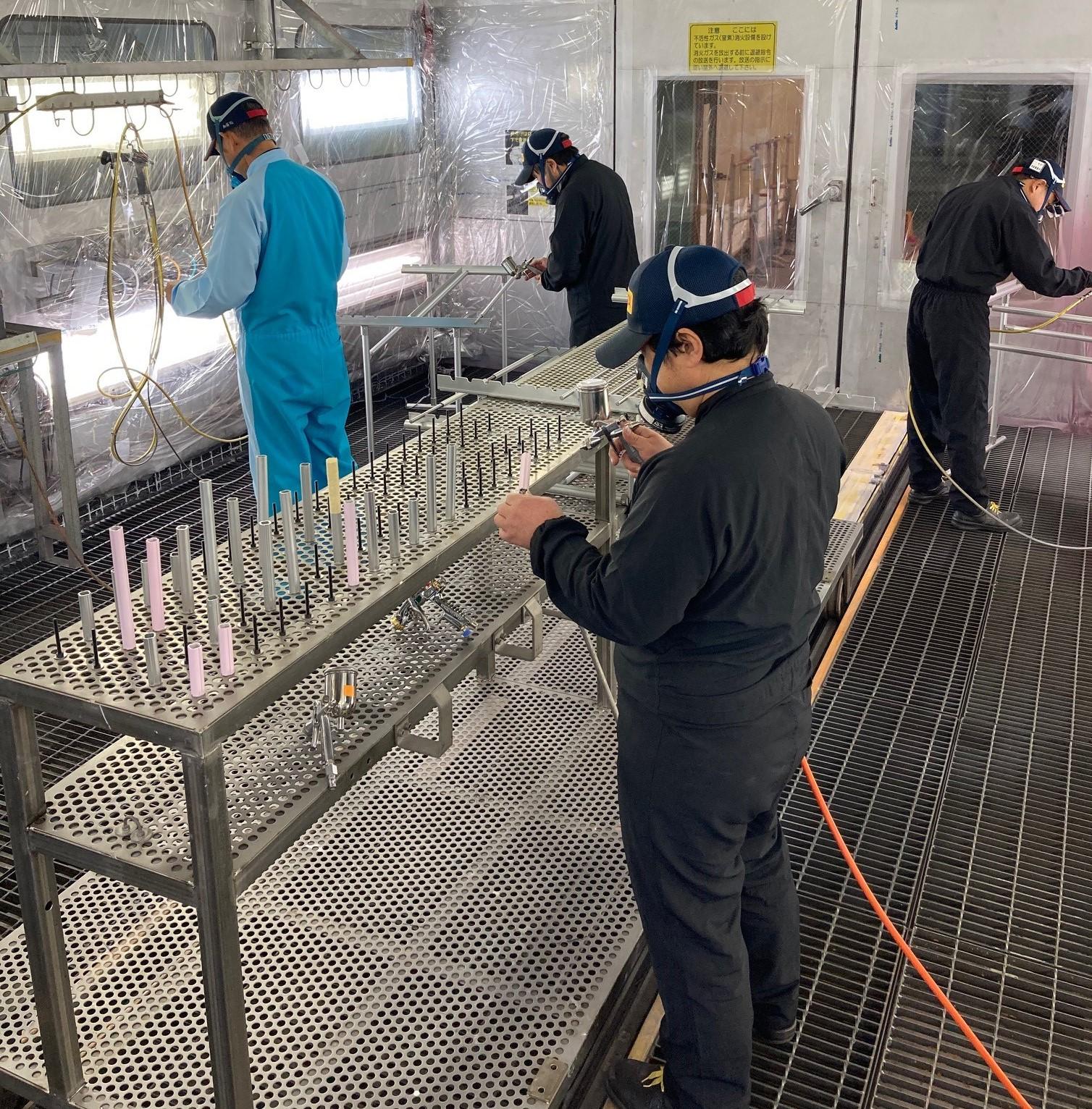
Trials of the stand were conducted in 64 locations, including at hospitals and commercial facilities. These trials provided feedback from doctors and other general users on how to improve the sanitizer. To make the device easy to use by any and all people, Toyota leveraged its know-how cultivated in car manufacturing based on the spirit of genchi genbutsu (going to the source to get the facts).
Hospitals and commercial facilities sincerely hoped to protect their patients, customers, colleagues and families. That is why they suggested various ideas for improvement. It was a joint effort by the manufacturers and users of the stands, as they faced the pandemic together.
It should come as no surprise that Toyota also used TPS in determining the manufacturing process for the stands.
The stand is created using materials that already exist in the plants, and the only processing of parts involved is the cutting and painting of materials. Because it uses readily available materials and simple processes, the product can be mass-produced without the need to develop or create any new equipment. While this helps reduce costs, it also means that there will be no obsolete equipment left over once demand for the sanitizer dispenser stands decline.
In addition, production efficiency has been thoroughly improved.The production workbench layout enables the work to be done, either vertically or horizontally, with all the parts conveniently placed. Unnecessary movement has been minimized with an instruction board for the assembly installed at eye-level height.
During a visit to the plant by the Toyota Times editorial team, it was surprising to see how small adjustments to the production process made a big difference in efficiency.
In fact, it had originally taken 20 to 30 minutes to produce one stand, but the process was reduced to only take 6 minutes in December.
After start of sale in December, as the order increased, the production process was improved further, which shortened the lead time to only 2.5 minutes per stand. By applying improvements to other assembly lines, the company is now able to manufacture more than 800 units per day.
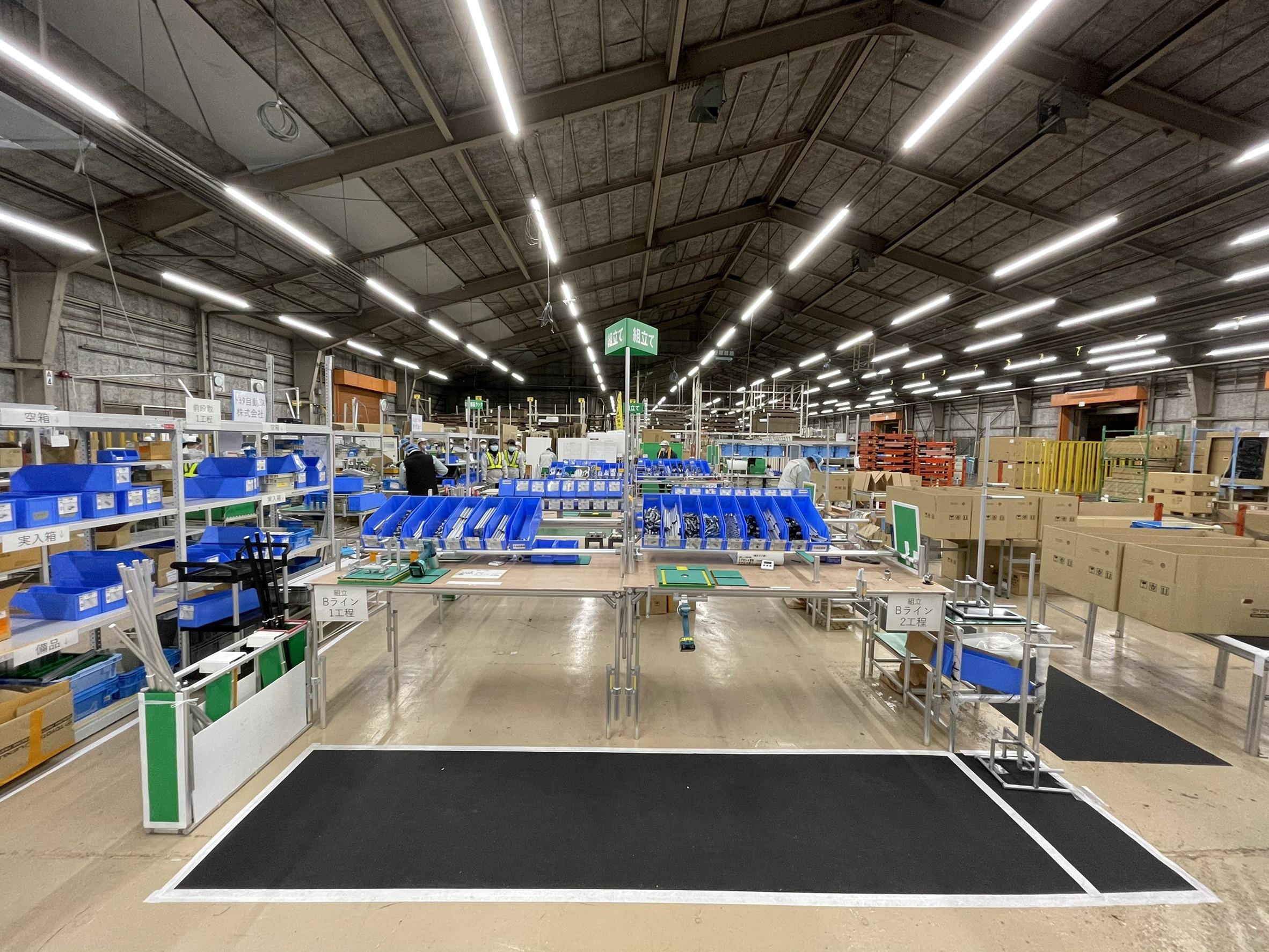
One root of monozukuri: make yourself useful to society
While many types of foot-operated sanitizer dispenser stands were already on the market, many were considered as neither affordable nor easy for everyone to use.
A key difference with Toyota’s stand is that by being made using the TPS, the stands could be made at a low cost. Toyota president Akio Toyoda told the team working on the stands:
"If you can offer it at an affordable price, why not put it on the market?"
By making it widely available, the company hopes to help slow or prevent the spread of COVID-19 infection. If this concept is viewed from a perspective of manufacturing cars, it carries the same intent as a concept of "making a widespread contribution to the environment" by popularizing, or helping drive widespread adoption of electrified vehicles, or so-called “eco-cars”.
Mr. Isobe, manager of the Service Parts Logistics Division in charge of the stand’s development, concurred with the aforementioned line of thinking, saying:
"We made [the sanitizer dispenser stand] with the goal of it being affordable and multifunctional. We want to help popularize the habit of disinfecting hands."
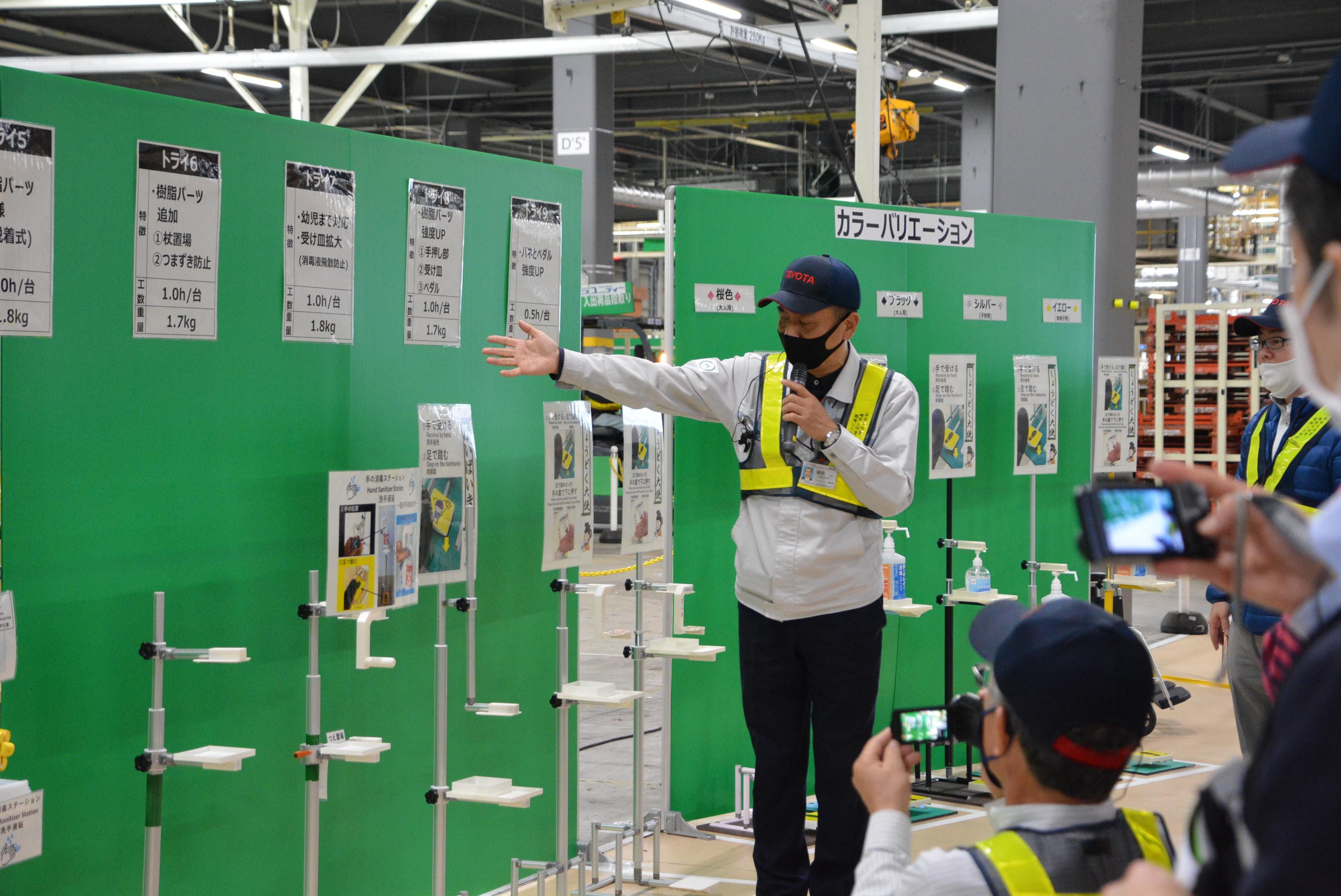
Many Toyota dealers who take responsibility in selling the stand share the same thoughts.
At Toyota Corolla Nagoya’s Toyokawa store, all members have made efforts in selling the stand to prevent COVID-19 infection from spreading further in the community, led by the store manager who explained the meaning of why “Shodoku Taishi” was developed and introduced to the market.
People shared their feedback at supermarkets and hospitals in the community, saying that they are "afraid to touch the hand-pressed sanitizer” and “the foot-operated sanitizer is useful because replacing batteries is unnecessary.” The dealer members told that more and more customers have now decided to buy the stand.
In addition, cooperation has expanded among Toyota suppliers to meet the increasing demand for orders.
For example, Kimura Unity, a logistics service provider, now supports the cutting of materials, pre-processing, and assembly of the stands, while Kojima Industries Corporation, who manufactures automobile interior and exterior parts, helps to produce and supply resin-made parts.
Additionally, SUS Corporation, who manufactures and sells structural materials for factories and construction, supports by providing the frame materials for the sanitizer stands by fully operating the plants in Japan and overseas.
With the shared goal of providing customers with products as quickly as possible, in as many units as possible, and with as much ease of use as possible, all companies are working together to improve productivity every day, based on the knowledge and ideas that exist at the frontlines.
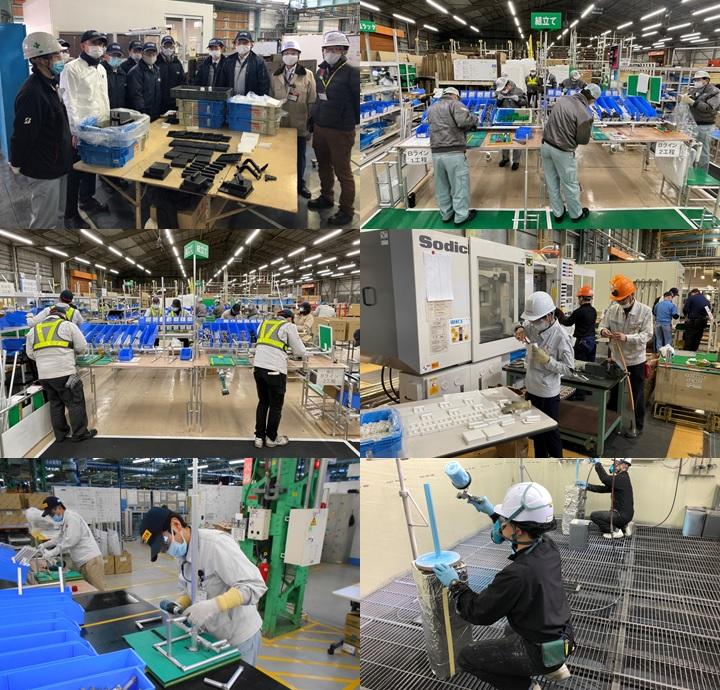
Sometimes it is said that "the frontlines of Toyota are strong". But Toyota’s real strength comes from how the TPS is incorporated in all production efforts. The system’s emphasis is on how to be more time-efficient through the complete elimination of things like waste, unreasonable demands and inconsistencies in processes.
The point is that the system not only makes work easier, but it also helps create the types of processes and standards that help deliver what customers need both quickly and at a reasonable cost.
The true strength of the company’s frontlines can be seen in emergency situations where something out of the ordinary is required. The foot-operated sanitizer dispenser stand production is a good example of this.
For Toyota, as a supporter of Sustainable Development Goals (SDGs), the level of accessibility for this product may also be linked to the idea promoted in SDGs to make sure no one is left behind.
One must not always be commanded, but should take initiative to see and fill needs, making one’s self useful to society.The sanitizer dispenser stand is a shining example of how Toyota will never forget the origin of monozukuri (making things) and will continue to work on “Producing Happiness for All” in everything it does.