
The new KINTO Unlimited subscription service upends the notion that the latest cars must be expensive. Behind the service lies a change in Toyota's approach to carmaking.
Starting with unprecedented modifications
“I saw it as a challenge to transform the very nature of carmaking,” says Project General Manager Nariaki Amano, who leads the project and has experience launching new businesses and designing services. “Until now, our job entailed planning, designing, and building new cars, then shipping them off. We had no way of upgrading our customers’ vehicles after they were sold.”
As their first task, the ten-member team set out to retrofit a sunroof onto a used Alphard.
This turned out far more difficult than imagined. Installing the sunroof on an existing car required modifications, such as making unplanned holes in the body and installing new parts.
While Toyota Group dealerships do handle assembly and parts replacement, modifications that require a huge amount of additional work were almost unheard of.
“We had only developed new cars, so we had no idea of the difficulty involved,” recalls Project General Manager Yukinori Ii, who spent many years working on car body design. “Only when we got to work did we realize how much effort was necessary.”
Creating unprecedented products and services with a team of just ten also required close collaboration beyond individual specializations.
The team sought to establish a hands-on atmosphere where all members joined in genba discussions without being bound by their former roles. This approach was not limited to manufacturing.
For Ii, who had built his career as an engineer, selling products and services at a dealership was an eye-opening experience.
“Until now, as an engineer I tended to get fixated on trying to be the best in my field. But standing on the sales floor gave me many ideas for features that could make the cars even easier to sell.”
Throughout their trial-and-error process, the project team remained committed to a genchi-genbutsu approach. Firsthand experiences on the frontlines of manufacturing and sales led to the insight that upgrades could be made easier by integrating the necessary parts and designs into vehicles from the outset.
Such lessons culminated in KINTO Unlimited’s Upgrade Ready Design.
Failure after failure
The new project was literally a series of failures.
KINTO Unlimited was preceded in January 2022 by KINTO FACTORY, which attracted attention as an innovative service offering timely software and hardware upgrades for cars already on the road. Initially, however, the project also committed the basic mistake of stocking insufficient parts.
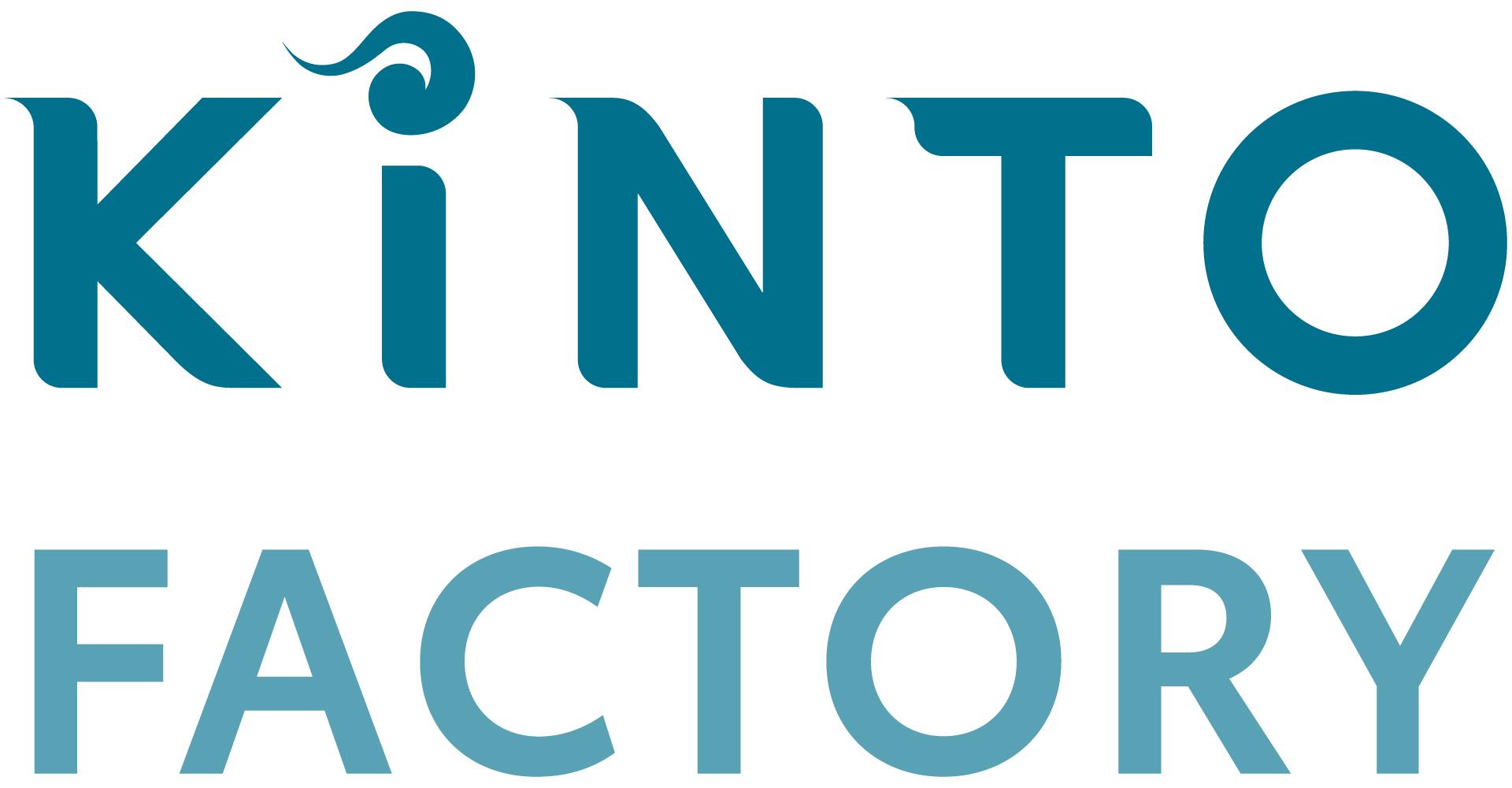
Given Toyota’s long-established work practices and focus on meticulous planning, this was an inexcusable error.
However, for a small team tackling tasks they had never done before in a bid to launch an entirely new service, failure was inevitable. And as failure followed failure, there was little to be gained in finger-pointing.
Instead, having shared the experience of selling services, the members naturally coalesced around the idea of doing everything possible to avoid inconveniencing customers.
This entailed making calls on the fly and hopping on the shinkansen with parts in hand to get them where they were needed within the day.
The speed needed to launch the new service within two years involved a dizzying transformation in the way things were done. Regardless, the members all agree that “every day was a thrill.”
KINTO speed
The project members are also unanimous in pointing out that this speed was only possible by collaborating with KINTO.
While KINTO began as a car subscription service, it has continued to announce new offerings, including KINTO FACTORY and “peelable body paints” that allows drivers to change the color of their vehicles.
Going beyond subscriptions, KINTO has played a key role in bringing Toyota’s new services into the world.
Similarly, for KINTO Unlimited, the project team pursued agile service development, going live as soon as possible and making improvements based on user feedback.
One example is the development of a dedicated app for delivering the service’s core Upgrade and Connected features. Working with KINTO’s IT engineers, the team completed the app within six months of giving it the green light.
Accomplishing the same thing within Toyota would be vastly more time-consuming, involving paperwork for system investment and coordination with relevant departments. On the other hand, partnering with KINTO enabled a high-speed PDCA cycle.
The fact that KINTO President Kotera served as the project team owner also spurred agile development.
Since the reporting line for both sides led straight to President Kotera, any unforeseen issues could be discussed at their respective weekly meetings.
Instead of dwelling on problems, members made quick decisions toward a solution, allowing the project to move swiftly forward.
Signs of change at Toyota
Although KINTO Unlimited has just kicked off its first phase with the Prius, there is already interest for other cars and from overseas plants.
Within Toyota, there are signs of a shift towards considering a vehicle’s long-term value during the development stage.
“We want to incorporate the lessons from the genba—how far we can push the possibilities of upgrades, and how customers respond—into Toyota’s next initiatives,” says Amano with sights set on greater prospects.
In fact, at the project kickoff two years earlier, Akio had shared another hope with the team members: “I want you to spark a change in the way we work at Toyota.”
“Looking back on the past two years, for me this was a new approach to work,” tells Amano. “It doesn’t matter what department you come from or what position you filled there. I think it reflects the vision of getting closer to Toyota’s origins as a venture company.”
KINTO Unlimited marks the first step in addressing the 20-year lifespan of a vehicle and ongoing engagement with the customers who drive Toyota cars.
Can this project, which made waves in Toyota’s carmaking with a game-changing service, generate a groundswell that will take the company beyond its limits? The team members have their sights set on the coming decades.