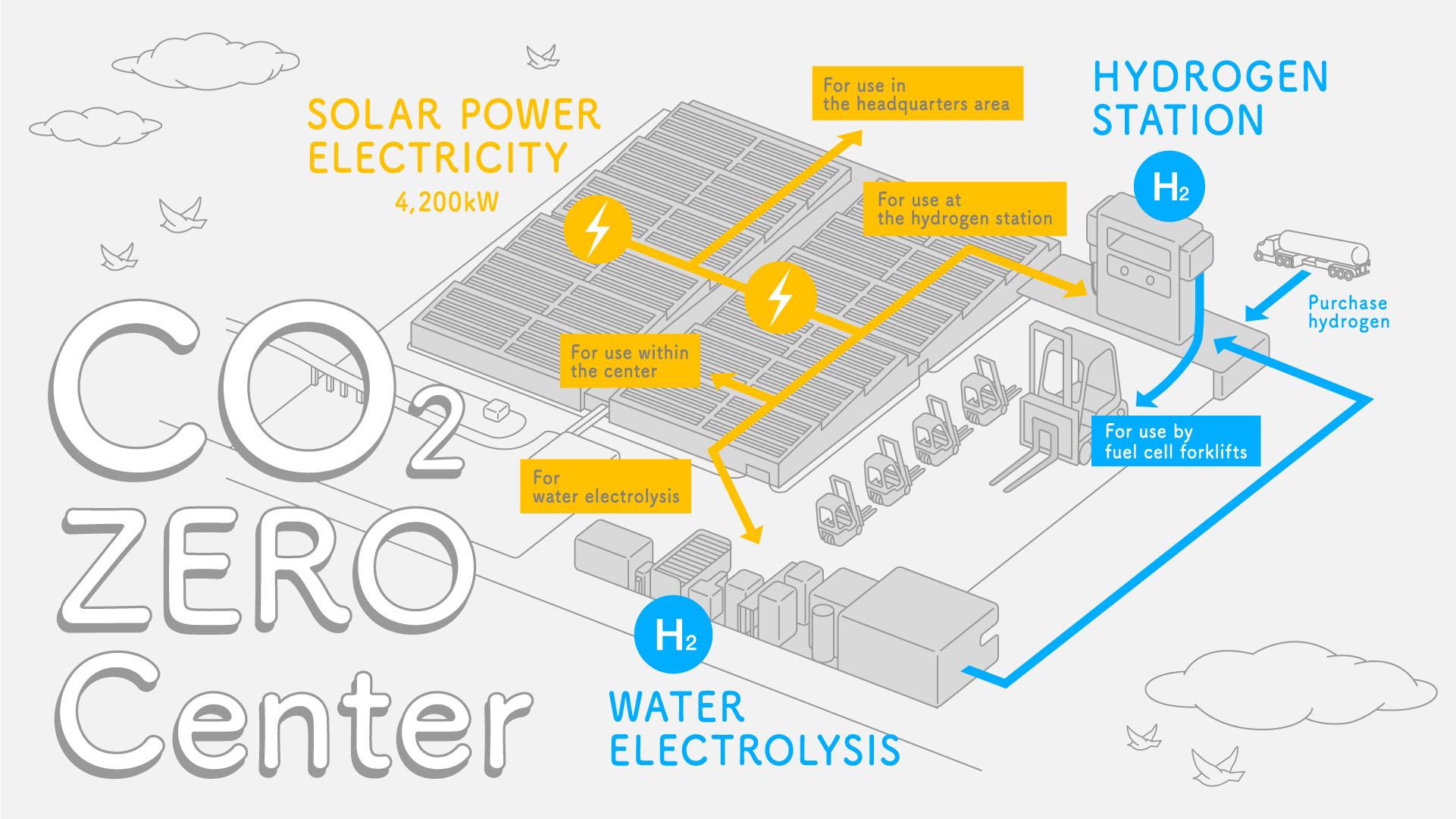
As part of its commitment to achieving carbon-neutrality, Toyota has recently opened a new CO2-free parts logistics center in Japan. How can it achieve zero emissions? Toyota Times visited the center to learn about their efforts.
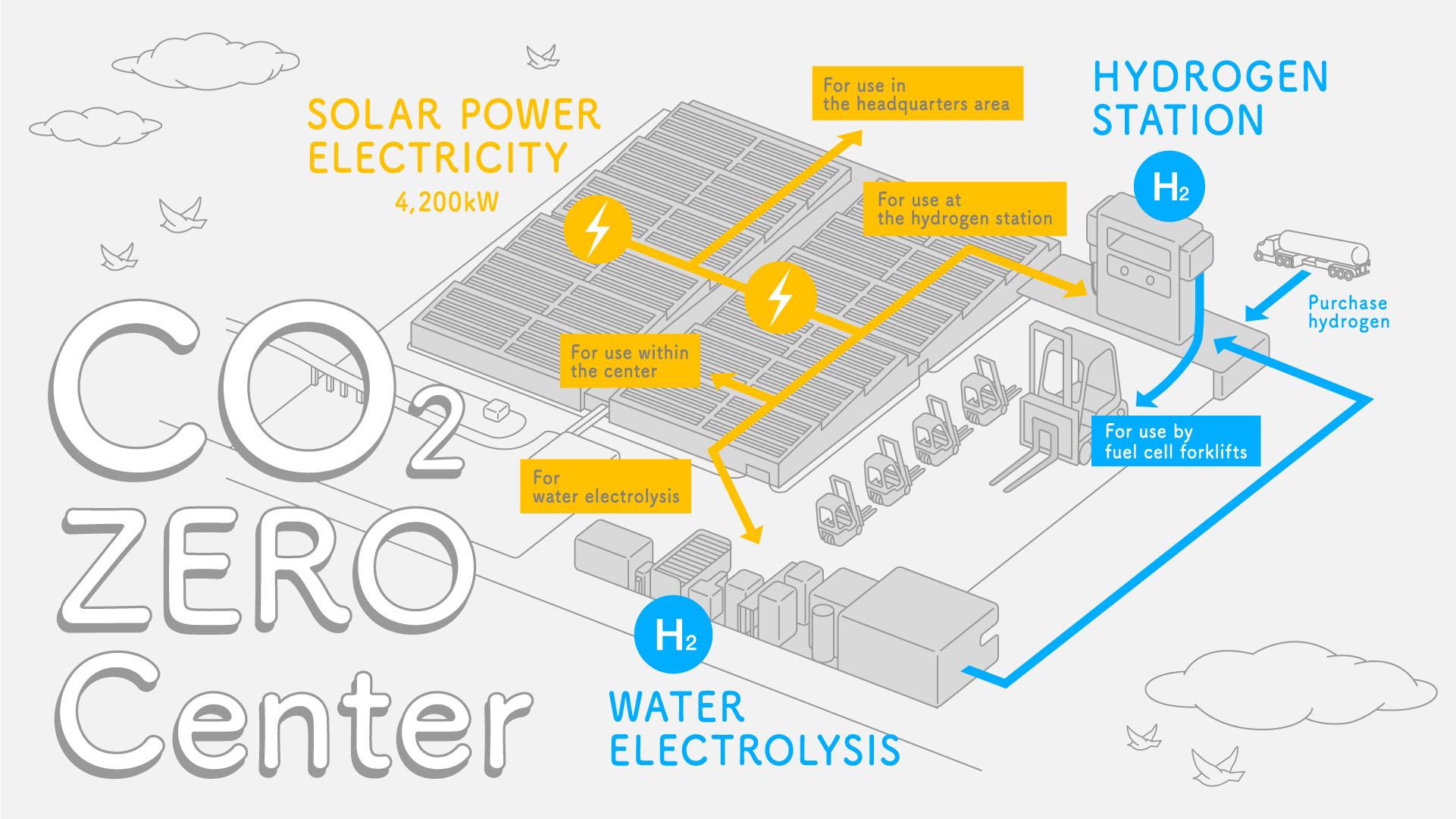
Over the 25 years since launching the world's first mass-produced hybrid car, the Prius, in 1997, Toyota has continued to develop technologies and products to reduce CO2 emissions. At its recent financial results briefing, the company reiterated its firm commitment to achieving carbon neutrality as a company by 2050 or earlier. As part of that commitment, Toyota has also made it clear they will be proactive in investing in new green energy technologies aimed at achieving carbon neutrality.
One such example, among many others, is Oguchi Parts Center No. 2, which opened this spring in Oguchi-cho, in the northern part of Aichi Prefecture. It functions as a CO2 emission free logistics base by operating fuel cell forklifts that utilize electricity generated by solar panels and hydrogen. The Toyota Times editorial team visited the center to find out more.
Toyota's first logistics hub that uses clean energy for all its electricity needs
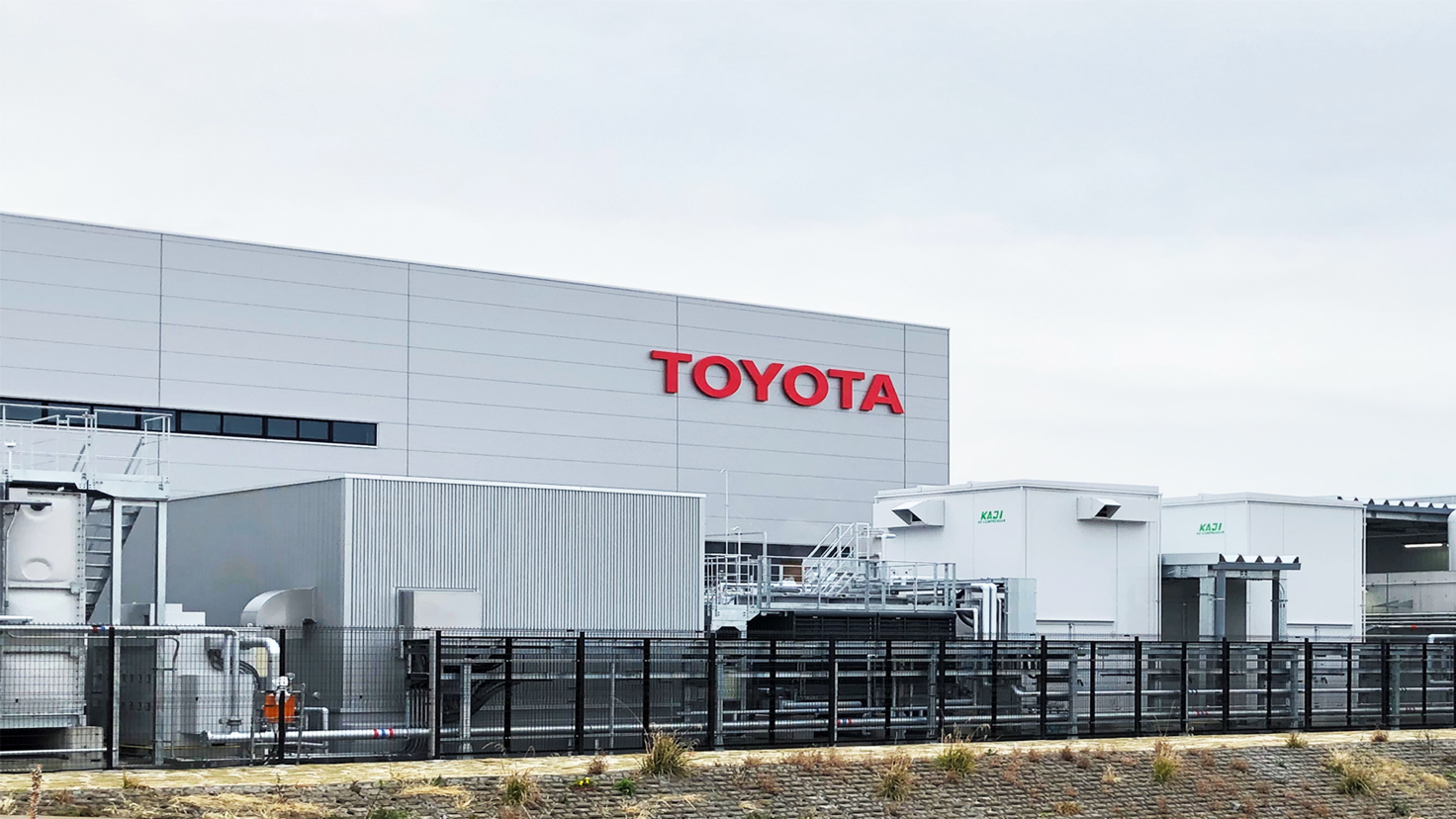
“We mainly manage about 350,000 parts for repair and replacement, ranging from car bumpers and headlamps to bolts and washers, and we have a system in place that allows products to be shipped as soon as orders are placed by the customer,” said one of the members at the center. “Together with the adjacent Oguchi Parts Center No. 1, we have a site area of 200,000 square meters.”
Large solar panels are installed on the roof of the center building. While there are other plants and bases equipped with solar panels at Toyota Motor Corporation's facilities in Japan and overseas, this is the first logistics center that uses solar power for all of its electricity needs.
“Various facilities, such as lighting in the center, are operated using electricity generated by solar panels. We also electrolyze water to produce hydrogen to fuel the forklifts running in the center.”
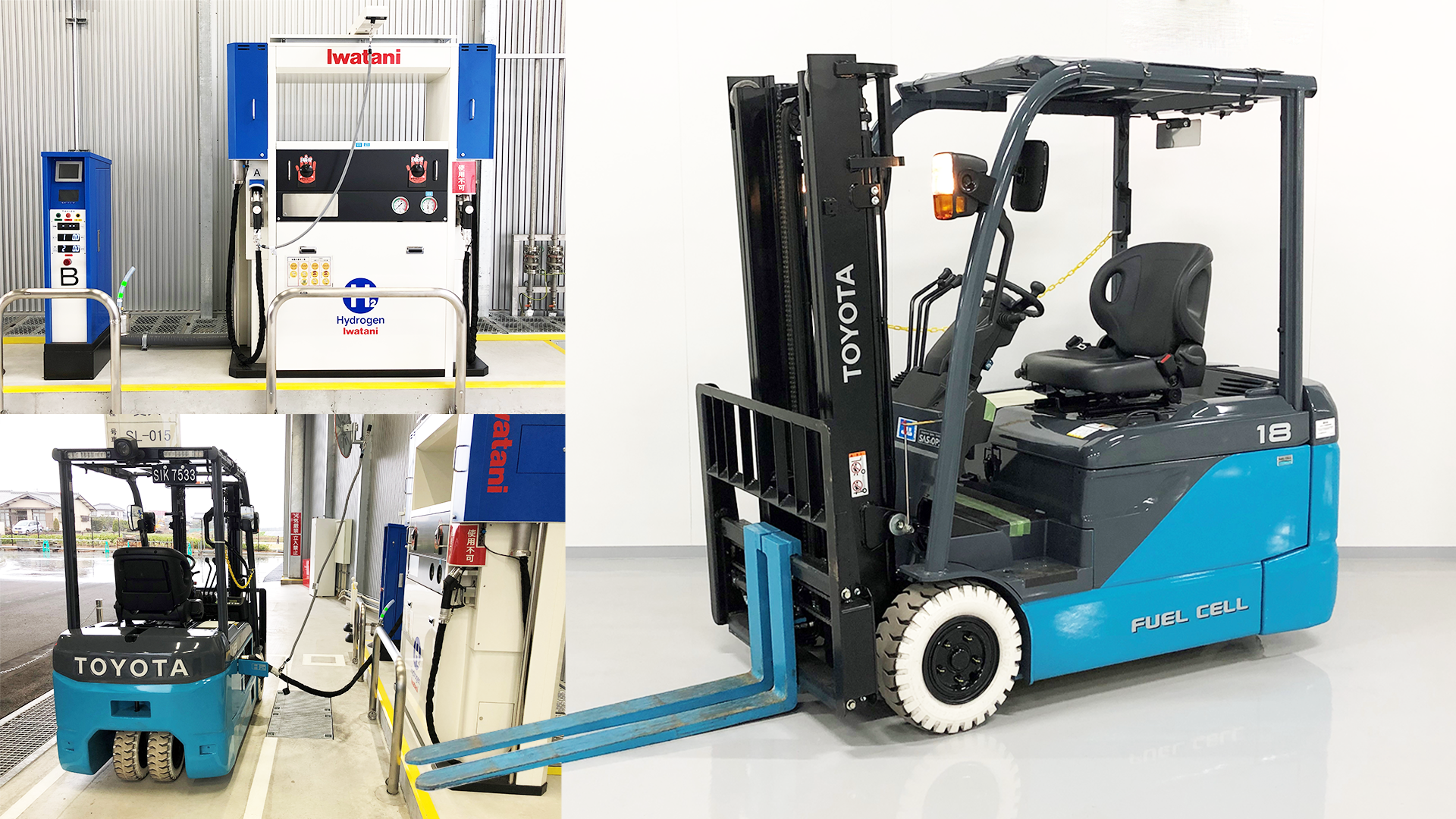
Keeping the air in the center clean ensures a comfortable work environment
The 55 forklifts in operation here are all hydrogen-powered fuel cell forklifts, like the ones already adopted at the Motomachi Plant in Toyota City. Just like the fuel cell electric vehicle “Mirai”, it operates on a fuel cell filled with compressed hydrogen.
The person in charge at the center explained, “Unlike a typical engine forklift, these vehicles emit no CO2 at all. An additional 27 units will be introduced in the future. The compressed hydrogen used as fuel is filled using an on-site compressed hydrogen dispenser similar to a gas filling station.”
As mentioned above, the hydrogen used in this case is produced by electrolyzing water at the center, but if that is not sufficient, hydrogen is purchased from outside. Currently, the price of compressed hydrogen is almost the same as gasoline in Japan, but it is expected that the cost will come down if hydrogen generation technology advances in the future.
“Fuel cell forklifts are quieter than their engine-powered ones and do not pollute the air in the center. Rechargeable battery forklifts would take about 8 hours to fully charge, whereas fuel cell forklifts can be filled with hydrogen in only about 3 minutes, making it easy to get back to work right away. Since there is no impact on the health of employees, people can work with peace of mind, making for good work relationships. I feel that the workplace environment has improved in many ways,” the person said.
Aiming for zero emissions overall
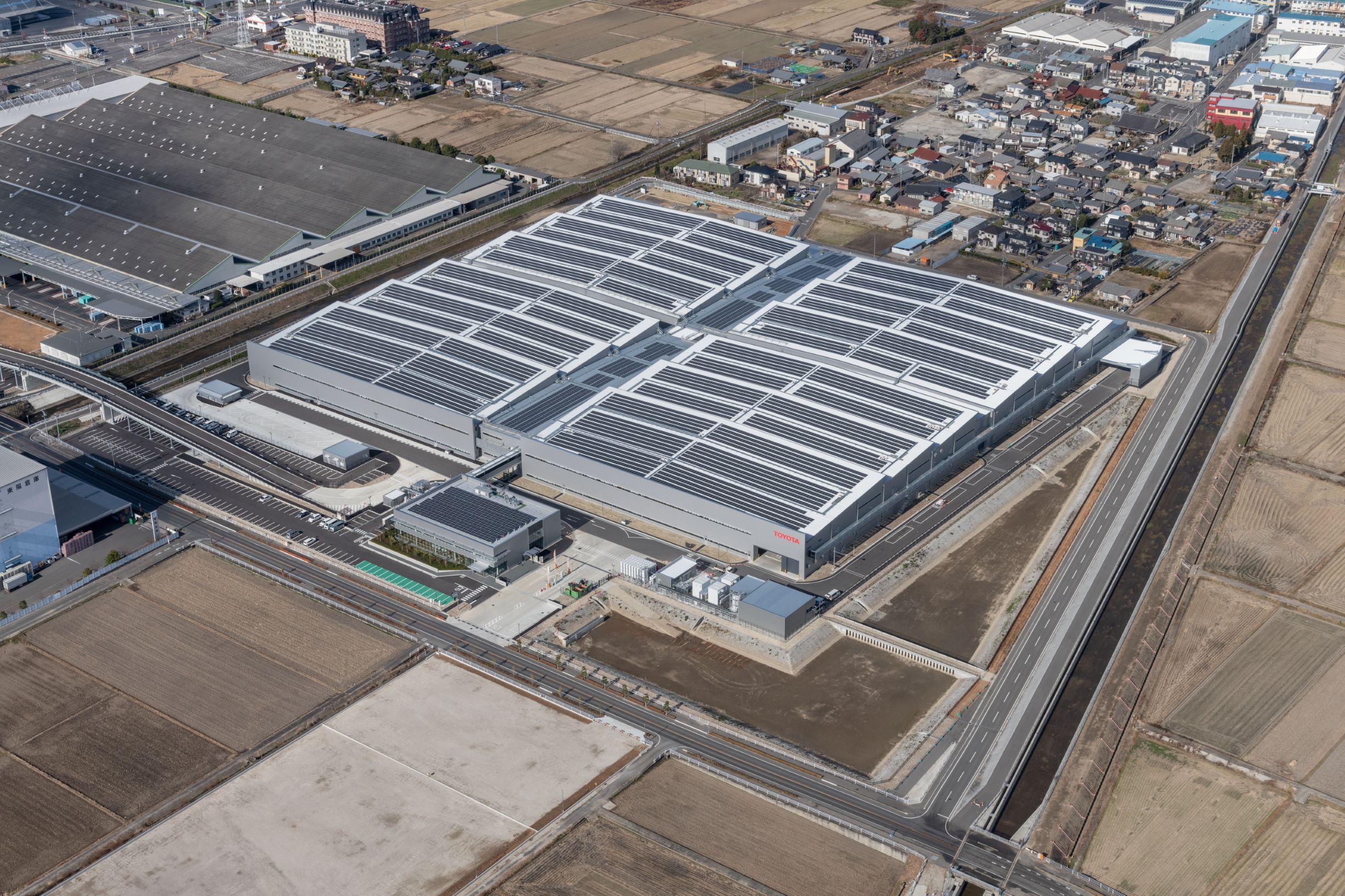
The maximum amount of renewable energy supplied by the solar panels installed on the center’s roof is 3,500kW*, which is enough for the electricity consumed at the logistics center.
*Power generated by solar panels after converting 4,200 kW of DC to AC power using a power conditioner
“As summer approaches, the maximum amount of electricity generated will grow, but the surplus electricity not used here will be distributed through Chubu Electric Power to other plants in the head office area in Toyota City. That said, we expect that there won’t be sufficient power during the rainy season and winter, when the sun doesn’t come out as much. Furthermore, solar power cannot be used during the daytime, in bad weather, at night and the like. That is why we also purchase some electricity from Chubu Electric Power,” explained the person in charge.
Buying electricity from an electric power company means using electricity generated by thermal power, so one may question whether it is truly zero emission. Nevertheless, over the course of the year, the amount of electricity generated by solar panels will be far more than the amount of electricity purchased. So, as it is possible to generate clean energy more than the annual consumption, CO2 generation is calculated as net zero.
20% of the electricity used by Toyota is from renewable energy
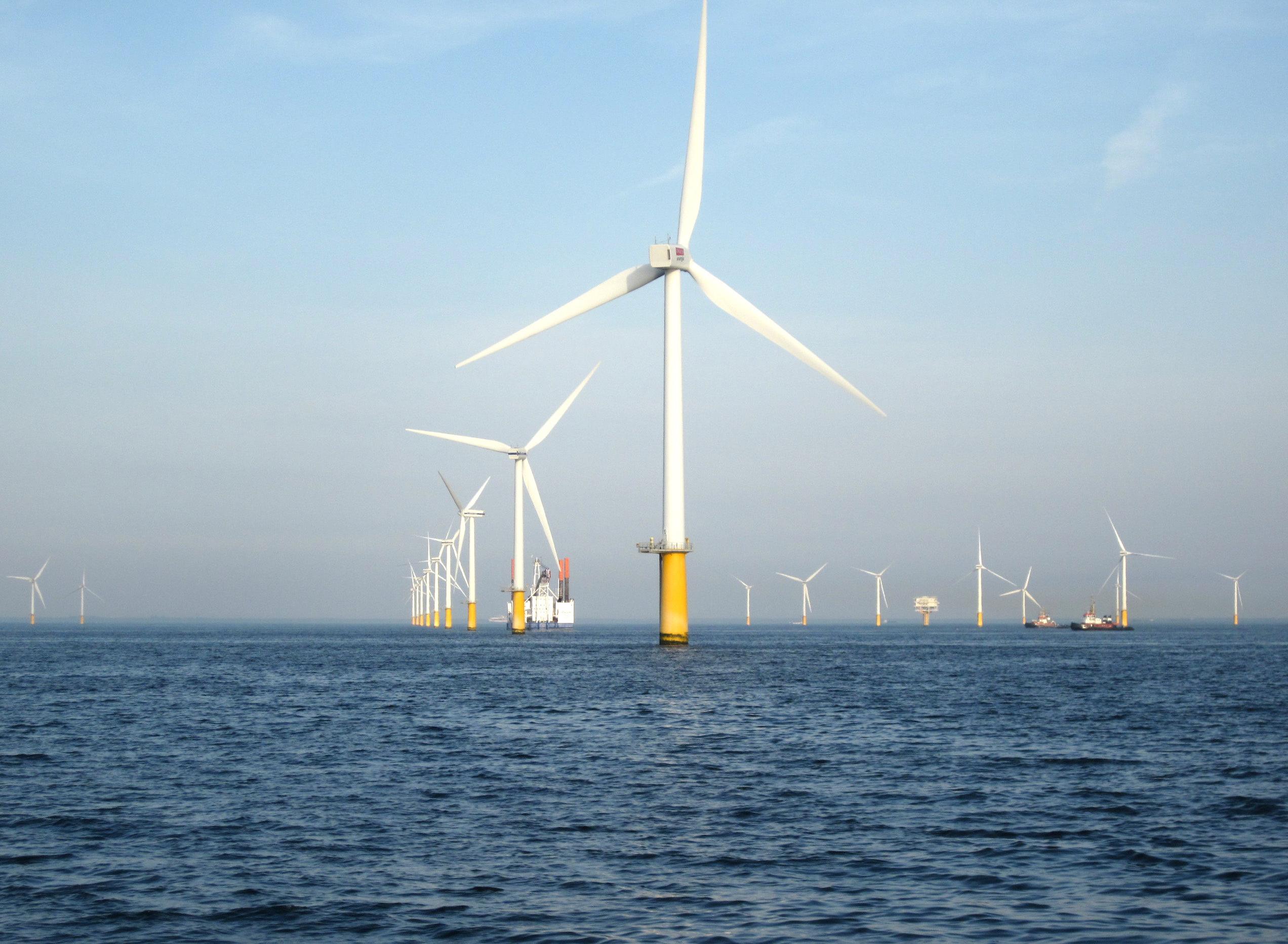
The Japanese government has pledged that it will target a 46% cut in greenhouse gas emissions by 2030 (compared to 2013 levels), and continues to strive toward a higher goal of 50%. While many discussions have focused on how to transition from gasoline-powered to electrified vehicles, as Toyota President Akio Toyoda has reiterated, CO2 emissions must be reduced in all processes: making, transporting, using, and disposal, for the goal of realizing a carbon neutral society.
According to Toyota, solar panels have also been installed at some of its plants overseas, and at some facilities in certain countries where there is sufficient renewable energy, such as Europe and South America, the electricity purchased is even 100% renewable energy. In Japan, currently, 20% of the electricity used by all Toyota facilities (plants, R&D facilities, etc.) is renewable energy.
Currently in Japan, the cost of purchasing electricity from major electric power companies is lower than generating renewable energy by oneself, but the total cost of solar panels and hydrogen facilities is expected to go down in the future thanks to low maintenance costs. The cost of building a hydrogen station is still high today, but it needs to be regarded as a mid-to-long term investment for the future. The Oguchi Parts Center No. 2, which uses clean energy exclusively, is one of the proving grounds toward achieving zero greenhouse gas emissions within Toyota’s facilities.
An opportunity for each one of us to consider energy issues in the future
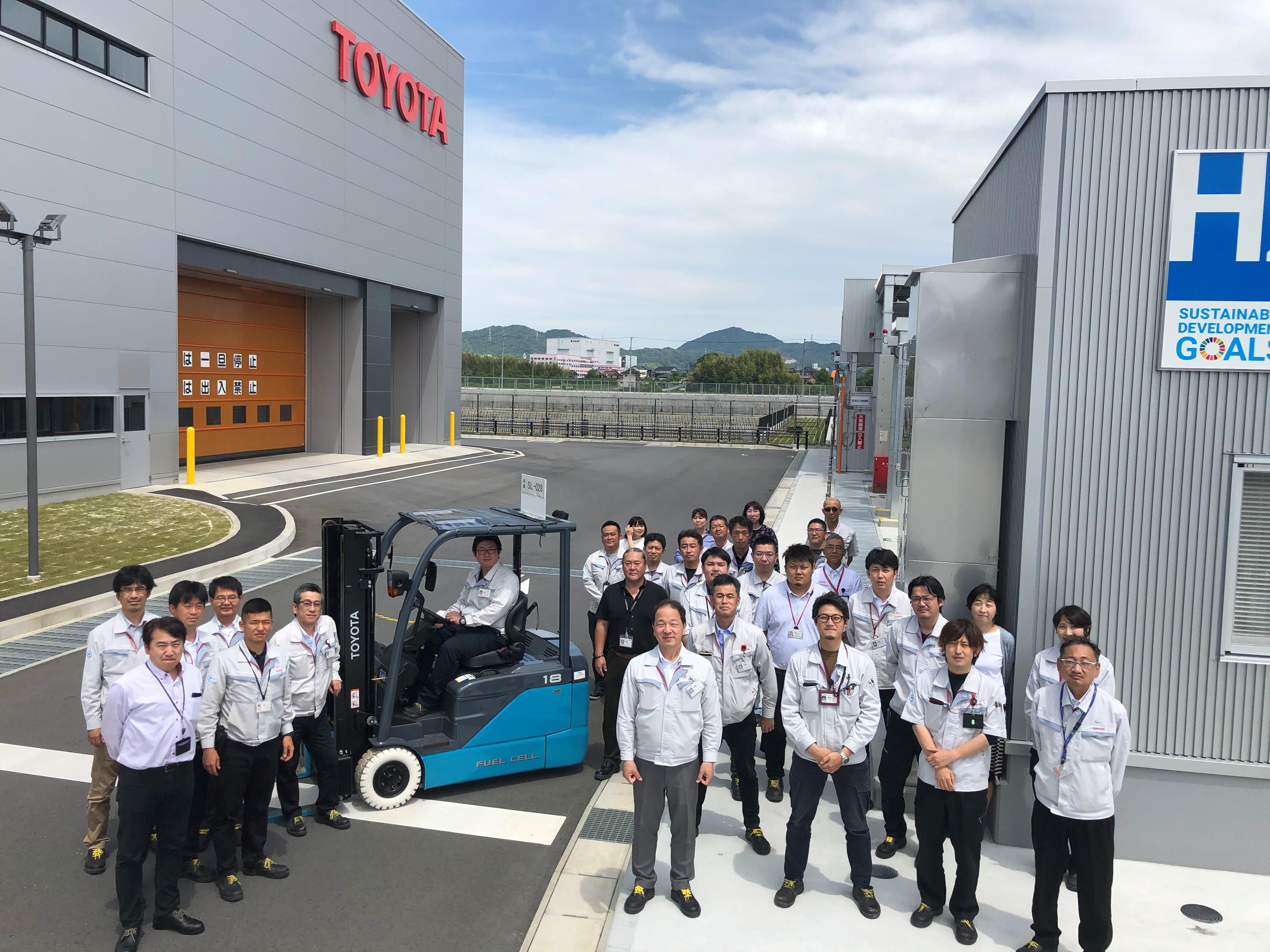
The creation of a clean energy logistics center has not only made it possible to reduce CO2 emissions, but has raised awareness of the need to pursue a carbon neutral society among team members working in the center.
“This is our first attempt to produce solar and hydrogen power on such a scale. I feel that team members’ awareness of what they have to do to tackle a future issue, including cultivating human resources, has grown considerably. They now have more ownership to be part of addressing future energy issues,” a member at the center says.
The hydrogen station installed at the center requires special national security management qualifications to handle high-pressure gases. For this reason, the development of qualified human resources is being promoted at the center, and it has already netted five national qualification holders. The carbon-neutral initiative at the center has not only changed how electricity is generated and consumed in the operation, but also has been a great opportunity for each member to realize what they can do on their part, as they “think globally and act locally.”