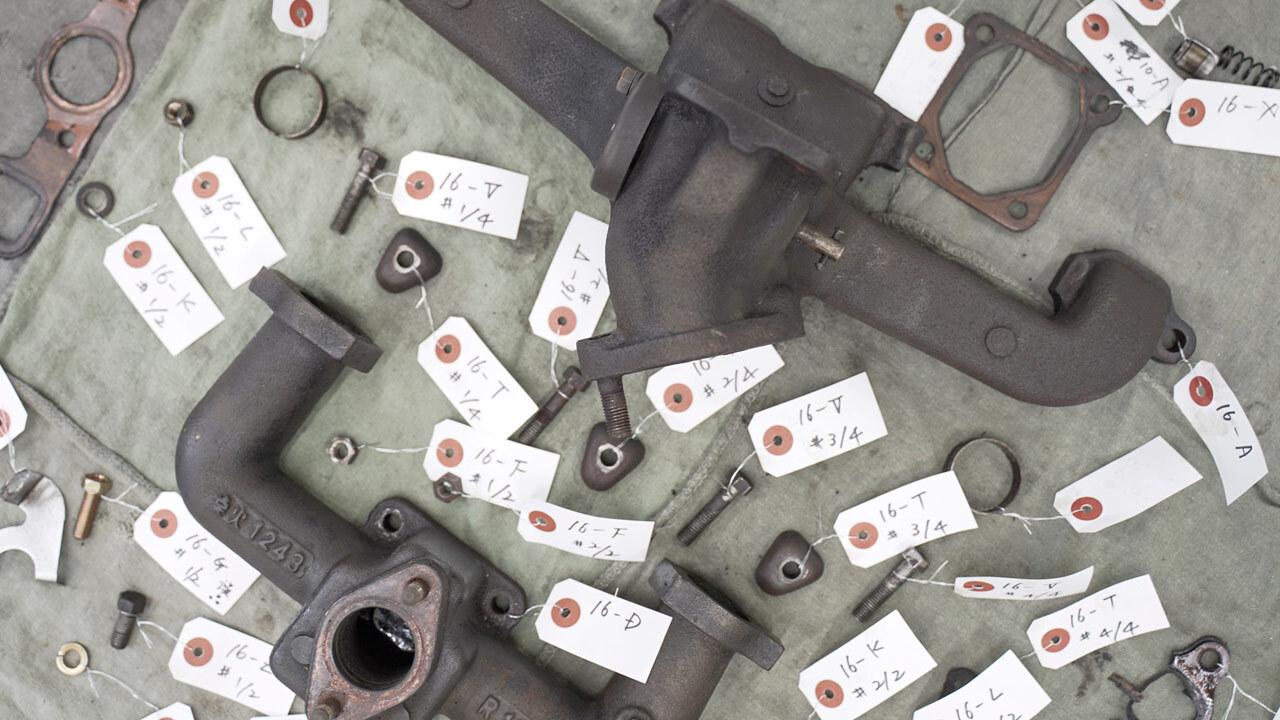
This series explores the project to restore a first-generation Crown, a car that embodies Toyota's origins. Part 5 deals with the issue of model years, an unavoidable factor in the restoration of old cars.
What’s our end goal?
For the many team members who were new to restoration, the model year issue proved all the more agonizing for their lack of experience.
It was not enough to simply make a good car—their choices were dictated by the vehicle’s history.
That said, everyone on the project team approached their work with a shared mindset.
They were determined to fulfill the wishes of the customer who had provided the Crown, who hoped to see it returned perfectly to its former glory as only Toyota could, through the combined efforts of those who make the cars of today.
To achieve this goal, the team would not stop at restoring the car to its original condition. Through modern means, they sought to take the Crown beyond the factory model, ensuring that it can remain on the road for many years to come.
As showcased in Part 4, the cationic electrodeposition coating used on the Crown’s chassis and body is one outcome of the pioneering efforts that came from this mindset. But without setting a clear finish line, the restoration work could go on indefinitely.
And no matter which version of the car they set out to build, above all, the team had to understand that true restoration is about achieving the correct form and specifications.
The project’s coordinators surveyed every existing first-generation Crown they could find, from the restored vehicles on display at the Toyota Automobile Museum to cars that had hardly been touched and remained largely in original condition.
They also worked hard to pin down factory specifications by diligently checking first-generation Crown parts listed on online auction sites and directly visiting the manufacturers who had been supplying genuine parts since the Crown’s earliest days.
Meanwhile, back in the workshops, the various teams set about refurbishing usable parts and fabricating unavailable replacements by hand from the blueprints.
Some parts were too worn to allow reuse. These included the seats, which were completely remade with extensive help from Toyota Boshoku, and the plastic tail lamps, where a lack of reference documents meant much trial and error during production, which involved creating silicon molds of the originals.
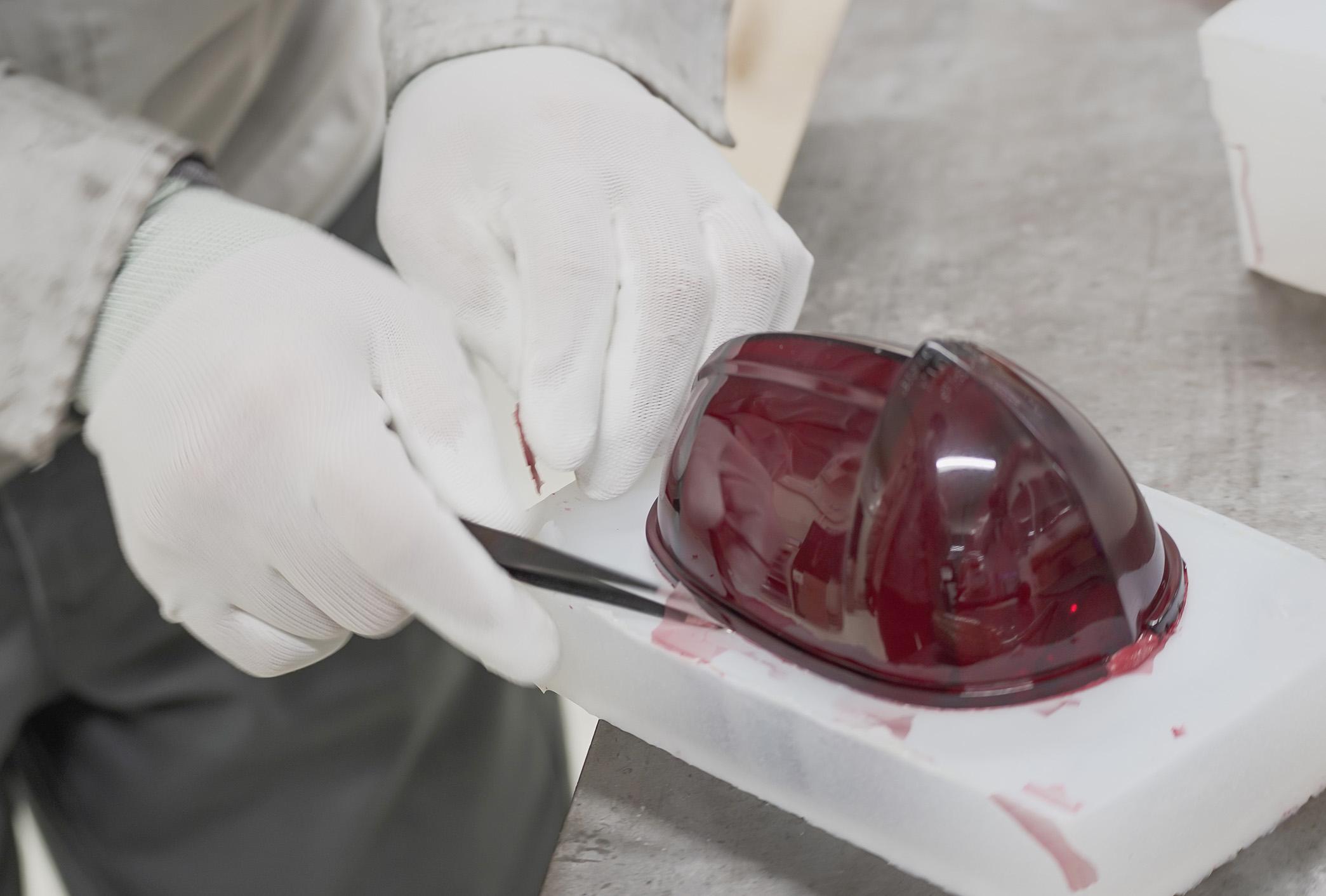
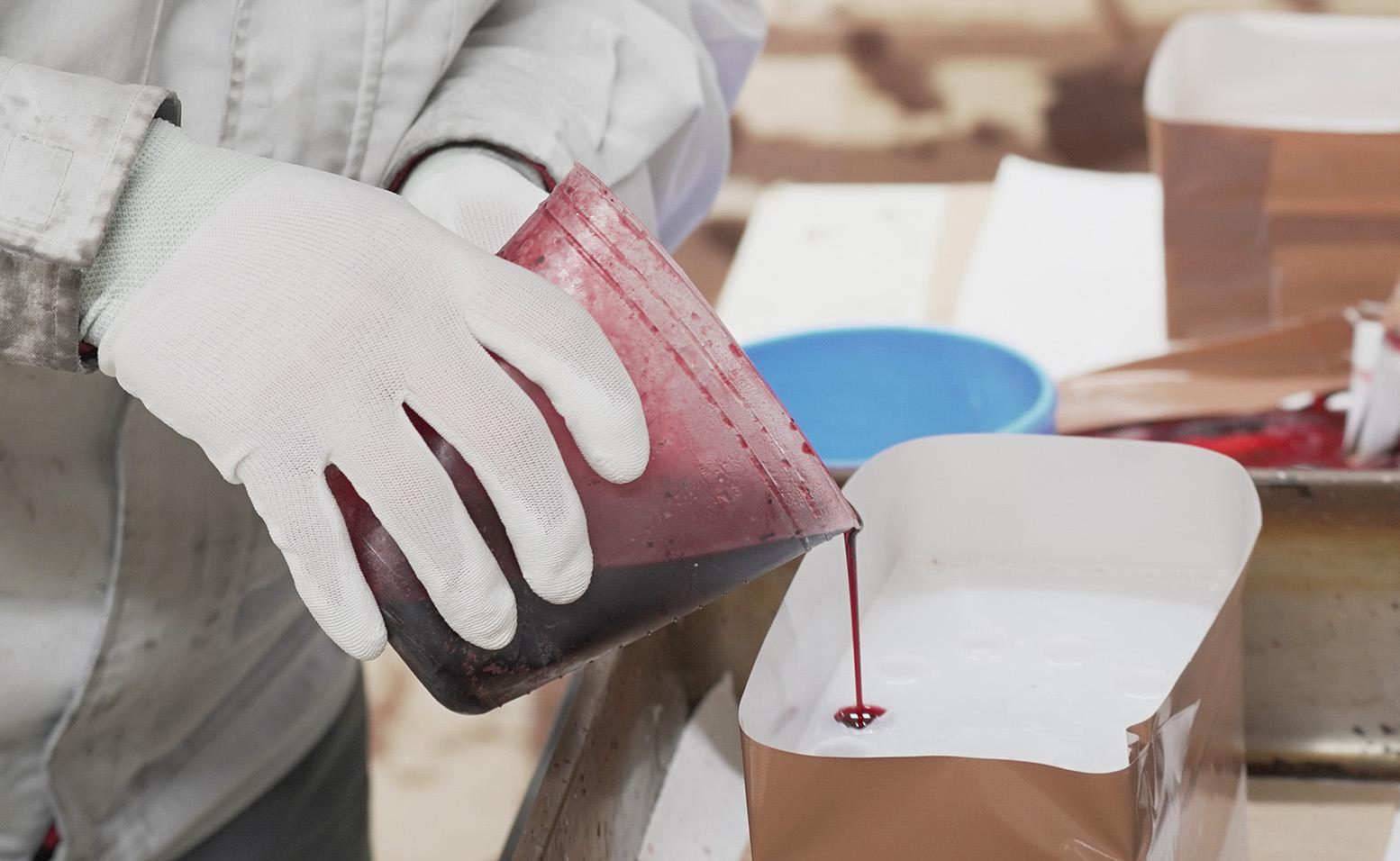
Yoshiaki Mori of Miyoshi Plant Machining Div. 2 was part of the suspension team. He noticed that the balance weight on the propeller shaft was shaped differently from those of modern cars.
Such weights are welded to the driveshaft, which connects the transmission to the differential, to correct any imbalances during rotation.
Whereas today’s balance weights are rectangular, those on the first-generation Crown were ring-shaped. A review of mid-century vehicles revealed that rectangular weights came into use around the 1960s.
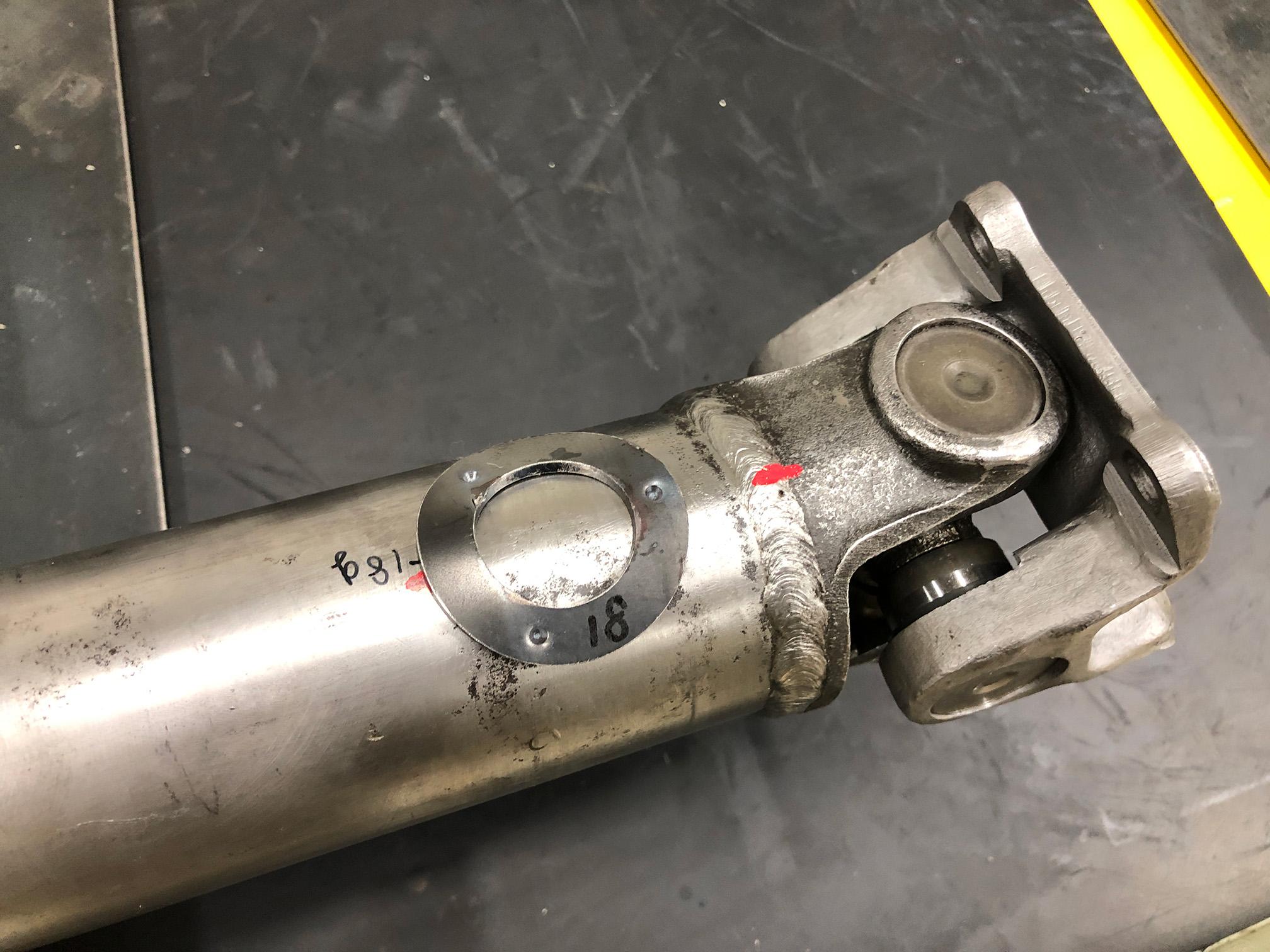

Mori
At first, we didn’t understand why the Crown’s balance weights would be shaped differently from modern vehicles. But when we actually made a ring-shaped weight and welded it on, the mass and angle proved difficult to fine-tune.
Rectangular weights make it easy to adjust the weight and angle by the number that you attach. That’s probably why they replaced rings. I’d say they likely helped to improve the balance of the shaft itself as well. We were witnessing the course of improvements in design and manufacturing.
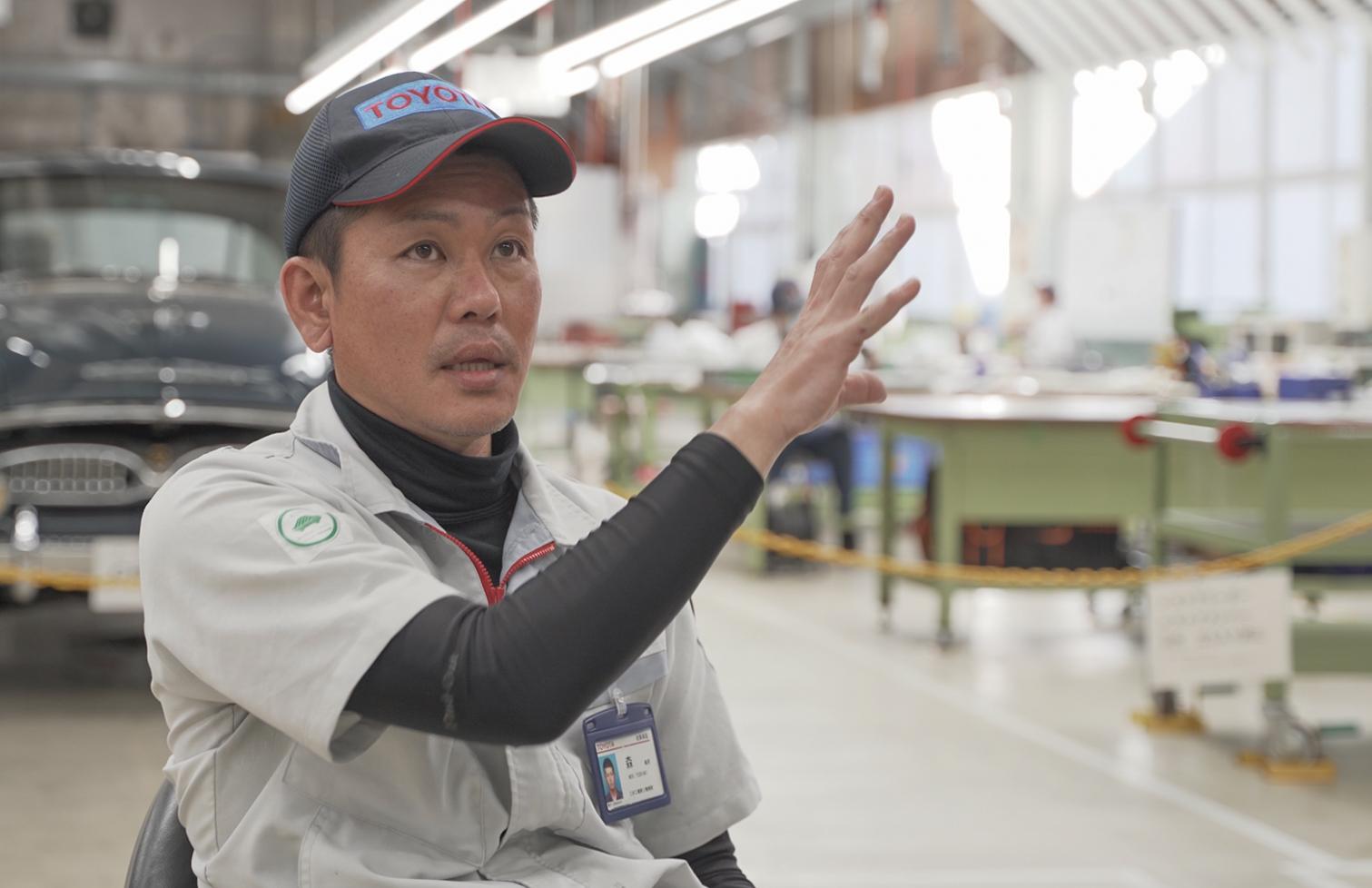
For this restoration, Mori and his colleagues decided to go with the hard-to-tweak ring weight, in keeping with the original Crown. At the same time, they were determined to meet modern standards for balance.
Meanwhile, on the final inspection team, Ryota Utsunomiya (Takaoka/Tsutsumi Quality Control Div.) was overhauling the wiring harness when he discovered that the junction blocks changed in shape between the 1955 and ‘57 models.
Incidentally, the wiring harness refers to the wires that transmit electricity to the car’s lights, horn, and other components, while junction blocks are the parts that connect separate wires together.
Utsunomiya
In the ’55 model, Y terminals were fastened together to make the connection, whereas the ’57 model was designed with joints known as bullet terminals connecting inside a rubber junction block.
I think the design change was driven by safety considerations, trying to lower the risk of a vehicle catching fire because of water-related electrical faults.
In terms of product quality, it would have reduced the risk of shorts caused by an overlooked terminal making contact with the body, or the risk of terminals breaking from over-tightening.
Fastening Y terminals together is also fiddly work, so the use of bullet terminals would probably have boosted efficiency.

Refining tricky or inefficient tasks also helps to make assembly times more consistent. The origins of the Toyota Production System—with its focus on eliminating waste, inconsistencies, and unreasonable requirements from the production genba—could be found within these various design changes.
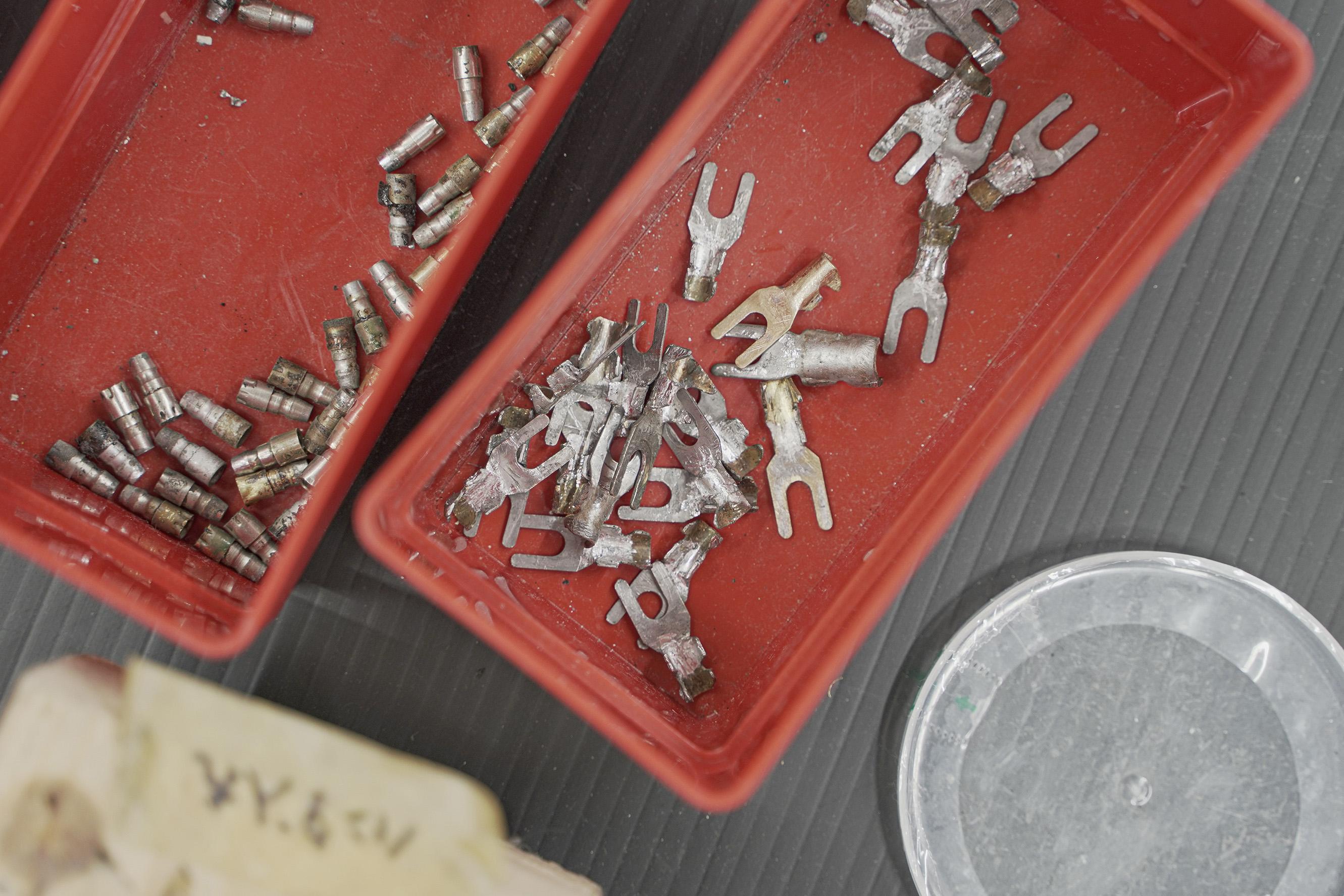

Given all the effort they put into restoring the car to its original condition, each team’s genba members were keenly invested in the spirited debate over model years, which stretched on for several months alongside the daily work.
Ultimately, the project team concluded that the restoration would be completed as an MY1957.
Not everyone working on the restoration agreed with this end goal. As one of the project’s coordinators, Komi arrived at the conclusion after discussing the model issue with each team and taking all counterarguments into consideration.
Komi
After heated discussions, I and the other coordinators decided that the car would be completed as a 1957 model.
One of the reasons we arrived at this conclusion was that the car is registered as an MY1957 and had “1957” in the chassis number inscribed on the ladder frame.
While this numbering is not exactly conclusive, seeing as the car would be driven on public roads, we had to honor what was in the paperwork.
Now we had a clear cause to rally around in our work: restoring the car to MY1957 factory condition.
In retrospect, however, what feels far more important is the process of figuring out the differences between the ’55 and ’57 models, tracking the design changes in the company’s drawings, and examining why these differences arose.
From the body panels to individual bolts, on nearly all the drawings, we could see the checks made by Kenya Nakamura, the first-generation Crown’s chief engineer. Likewise, in the design changes, whether to increase durability or assist assembly and reduce costs, we could sense the history of tireless improvements made by those who came before us.
I think everyone involved in the restoration work recognized that dedication, and it motivated us to continue making the car ever better.
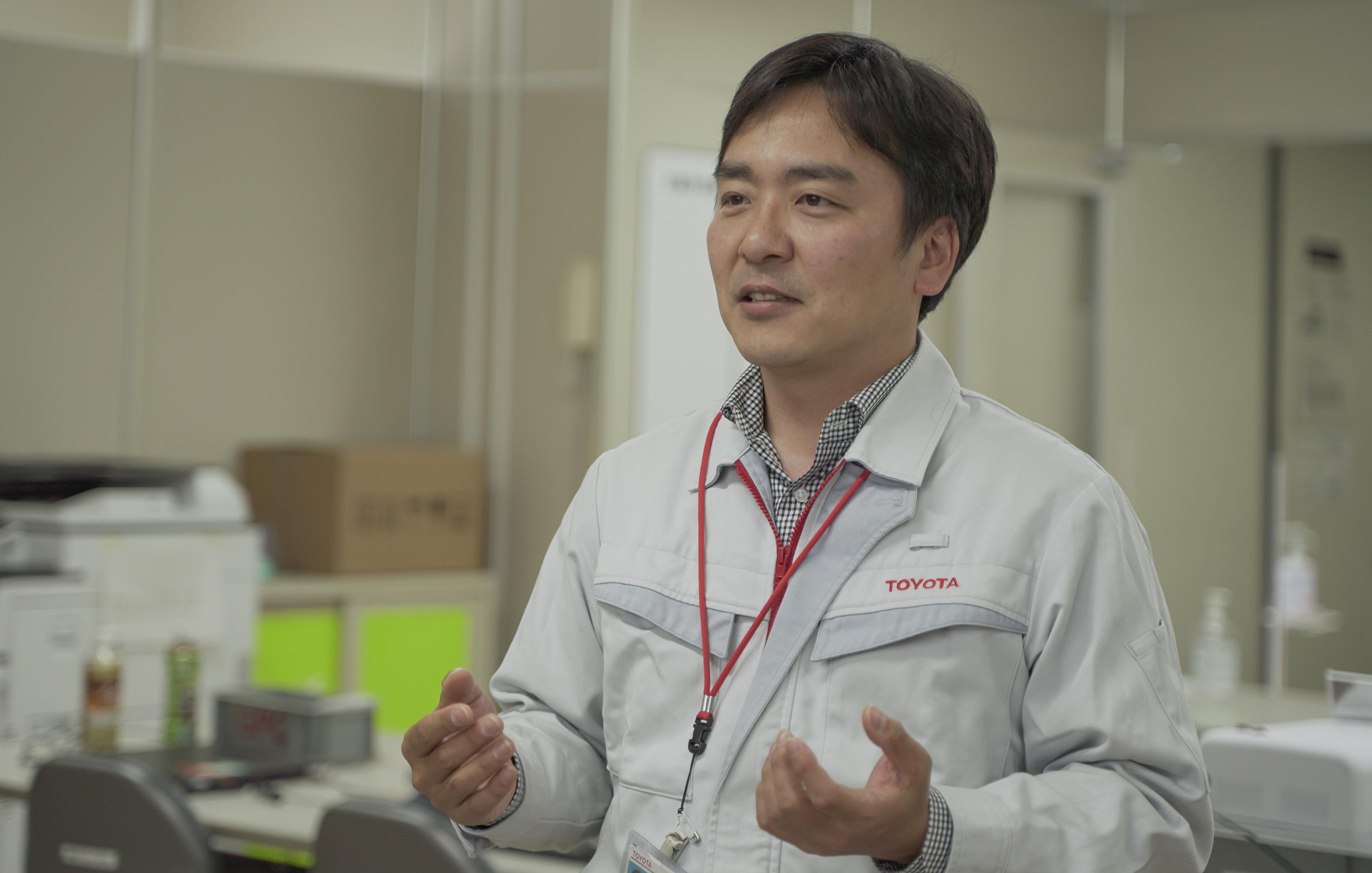
As Komi describes, the project’s members tackled the model year problem head-on, scrutinizing both drawings and actual parts hundreds of times. The process took them beyond correct answers to the ambitious, improvement-driven spirit of the car’s original creators. When it came to the restoration work, they too would brook no compromise.
Sharing their predecessors’ mentality of seeking new challenges and improvements, the team forged ahead in the pursuit of ever-better cars—a process that lies at the very heart of the first-generation Crown restoration project and its mission of passing on skills and developing talent.
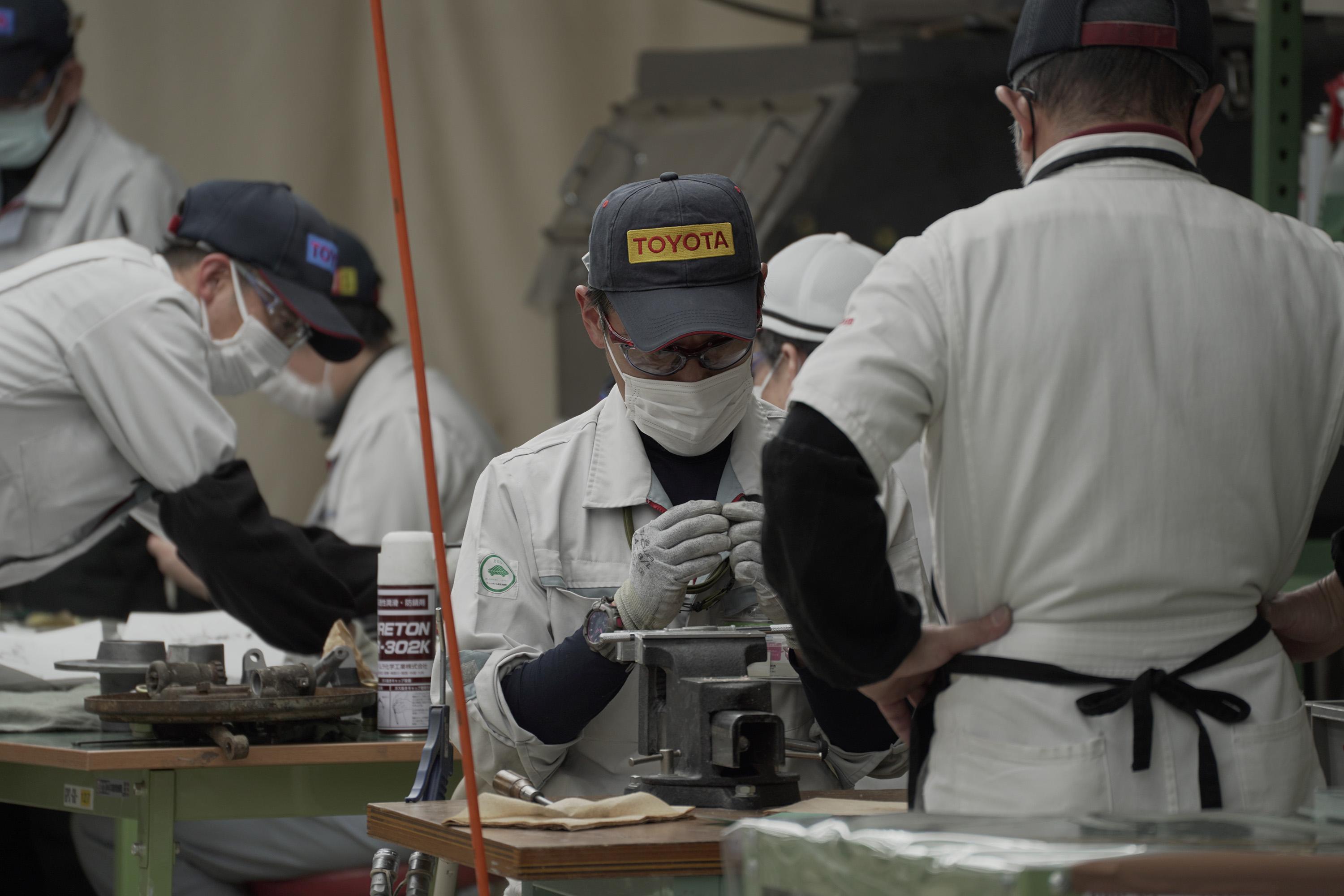
(Text: Yasuhito Shibuya)