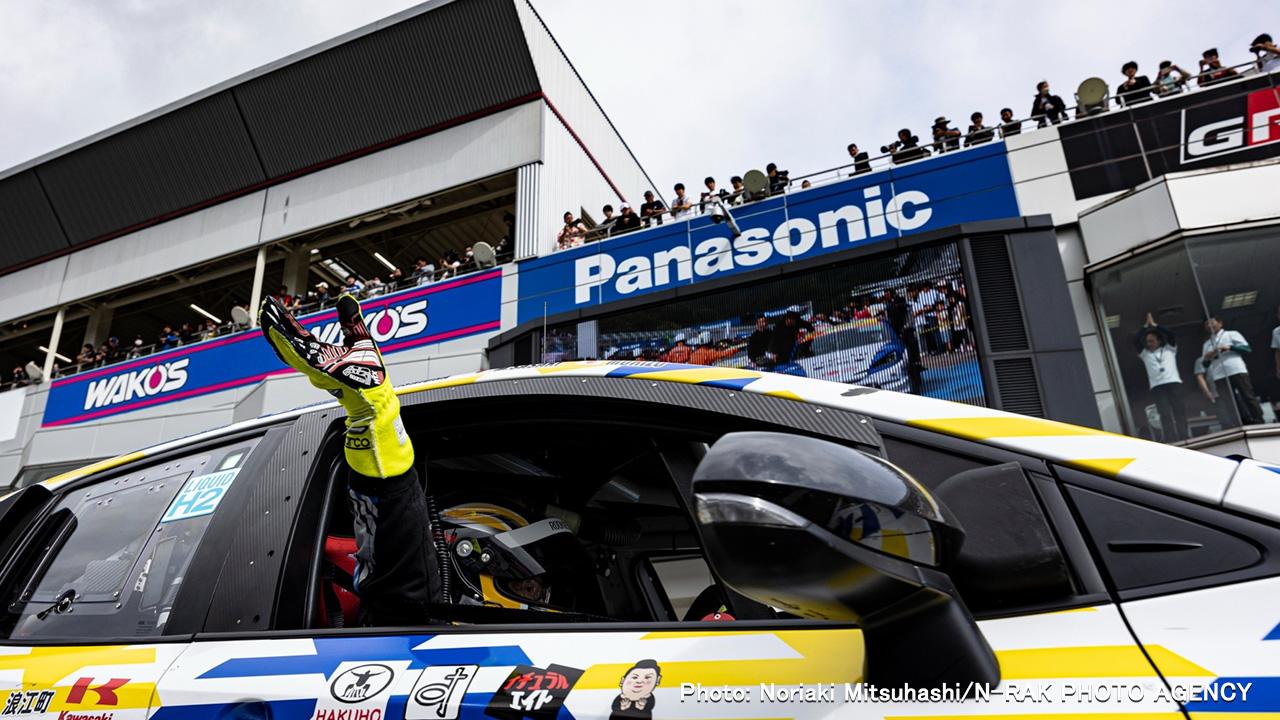
After just 18 months of development, Toyota's liquid hydrogen-fueled GR Corolla completed a 24-hour race. Toyota Times visited the genba to discover how this world-first endeavor succeeded.
Toyota’s “unfathomable” specs
On the flip side, this effort reveals the difficulty of finding collaborators.
And little wonder—the only other examples of liquid hydrogen-fueled mobility were rockets.
Although the team found manufacturers who make large-scale hydrogen tanks, virtually no one was developing compact tanks fit for passenger cars.
Yamamoto and his fellow developers scoured the country in search of someone with the advanced technical capabilities to build their tank—the key to the project’s success—with the speed required for racing.
During this search, they were introduced to Shinko Industries from Ube, Yamaguchi Prefecture.
While the company’s strengths lie in civil engineering, construction, and other large-scale projects, the team selected Shinko for its highly skilled master welders.
The double-shell vacuum-insulation tank had to fit snugly into its allotted space, while also allowing for the hydrogen inlet/outlet nozzle to be installed. Being a single bespoke item, all welding had to be done by hand.
Even with Shinko’s welding prowess, this proved a daunting task. Keiji Kawano, Deputy General Manager of Shinko Plant Service*, explains.
*A Shinko Industries subsidiary that also developed and manufactured the vaporizer for the liquid hydrogen vehicle.
“We had never worked with an automaker before. Normally, we deal with large equipment such as cranes and civil engineering projects. Rather than making dozens of the same items, we are in the business of producing one-off custom pieces. For us, Toyota’s specifications required an unfathomable level of precision.”
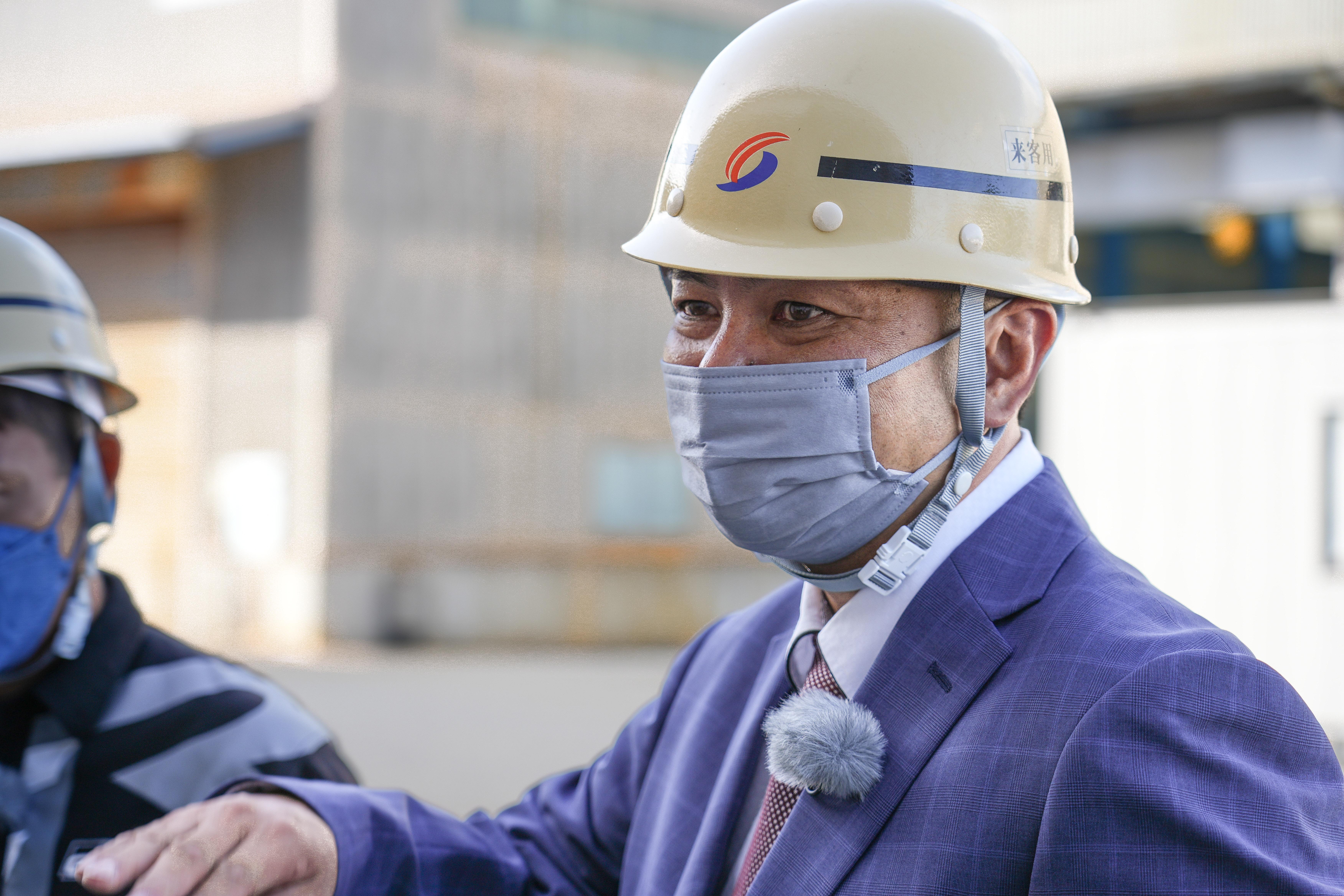
The workmanship had to be accurate down to tenths of a millimeter. Keeping within these specs while factoring in the distortion caused by welding proved a Herculean task.
Completing half a year’s work in three months
There was an added difficulty: the tank gave little leeway for design modifications.
With Toyota aiming to be race-ready in just a year, the “super-speed” development involved numerous parts running in parallel, many of which would be impacted by changes in the tank design.
Things were so tight that even slight tweaks to the nozzle angle would affect other piping.
Given the hurdles involved, why was Shinko so keen to take on this development challenge?
“We saw for ourselves Toyota’s commitment to the future of Japan,” says Kawano. “Being part of that was the biggest motivation.”
“We wanted to prove that a car equipped with the tank we made could race safely before crowds of spectators. We threw everything we had into this project, believing in a future where cars running on liquid hydrogen are part of everyday life.”
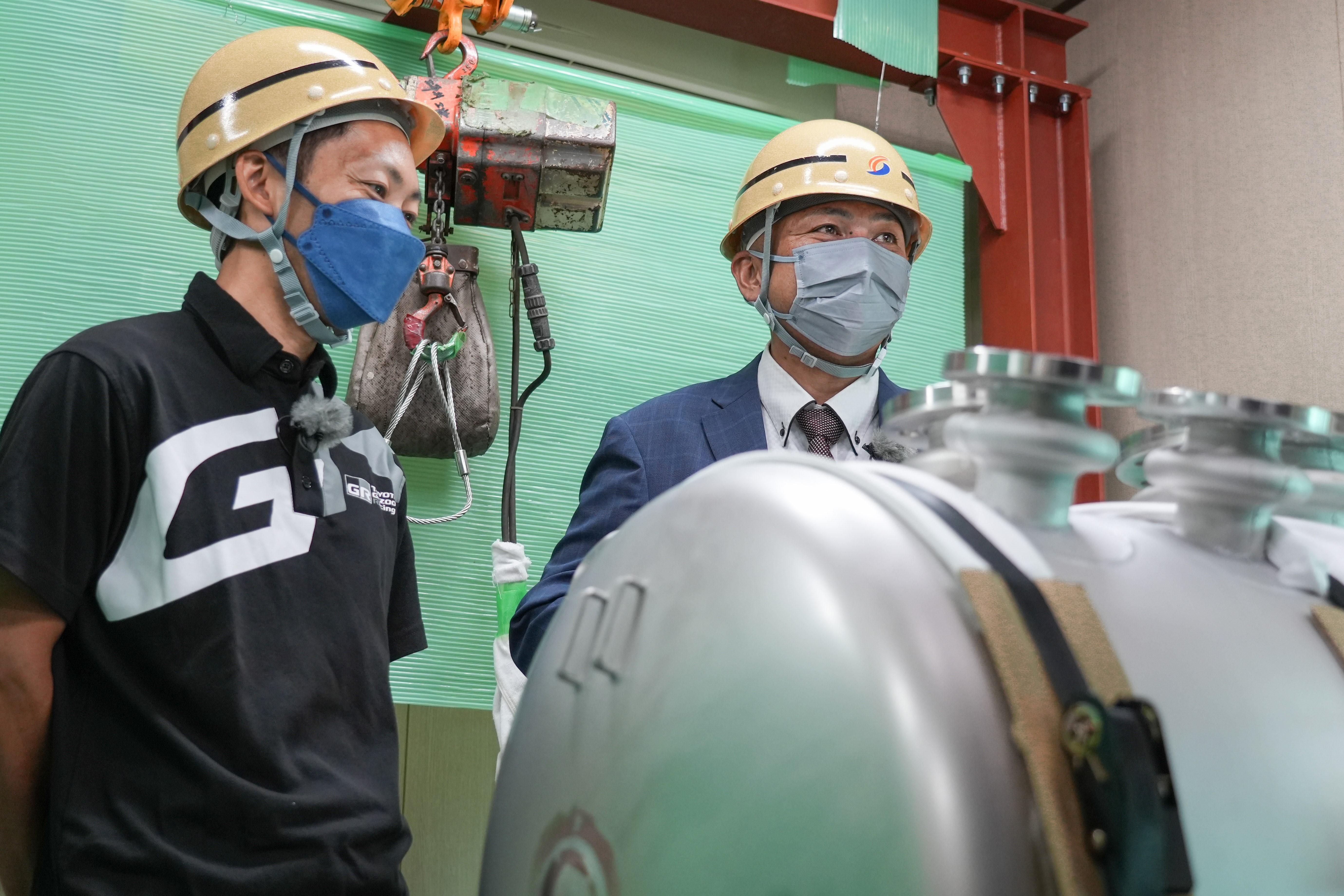
For some of the tank’s components, such as flanges and nozzles, fell short of Toyota’s exacting requirements, even if they met Japan Industrial Standards (JIS).
Such parts were fabricated from scratch, drawing on the combined resources of the Shinko Group to achieve ultra-short turnaround times and high-precision finish.
When the situation called for specialized skills, experienced veterans were called in to the frontlines to join the team.
Alongside manufacturing, 25 members handled areas such as design and obtaining approval. Thanks to this Shinko-wide effort, which included weekend and holiday shifts, work that would normally be expected to take six months was completed in just three.
“Seeing the finished piece was a real thrill,” recalls Yamamoto. “It had an aura beyond anything in my drawings. I’m full of gratitude for everything Shinko achieved despite the difficulties of maintaining precision when crafting by hand.”