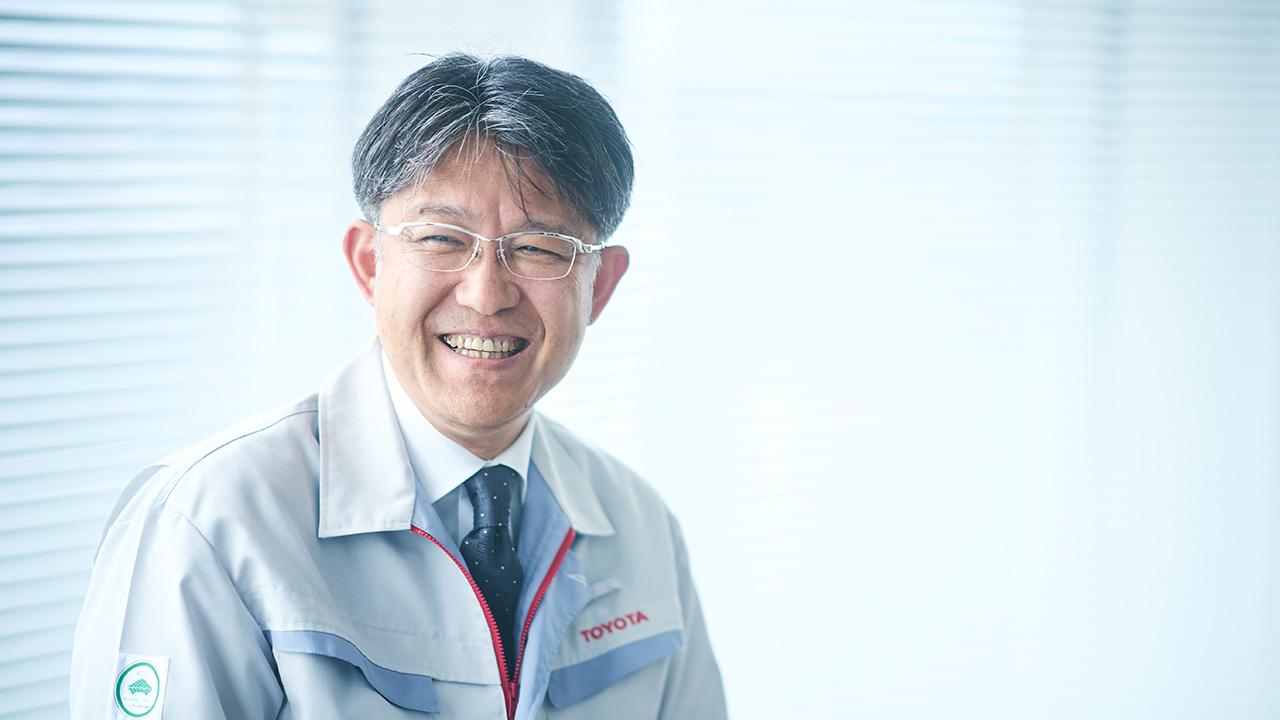
Automotive analyst Shinya Yamamoto goes one-on-one with this year's trio of newly appointed presidents. In this first installment, President Koji Sato delves into his life as a "Toyota man."
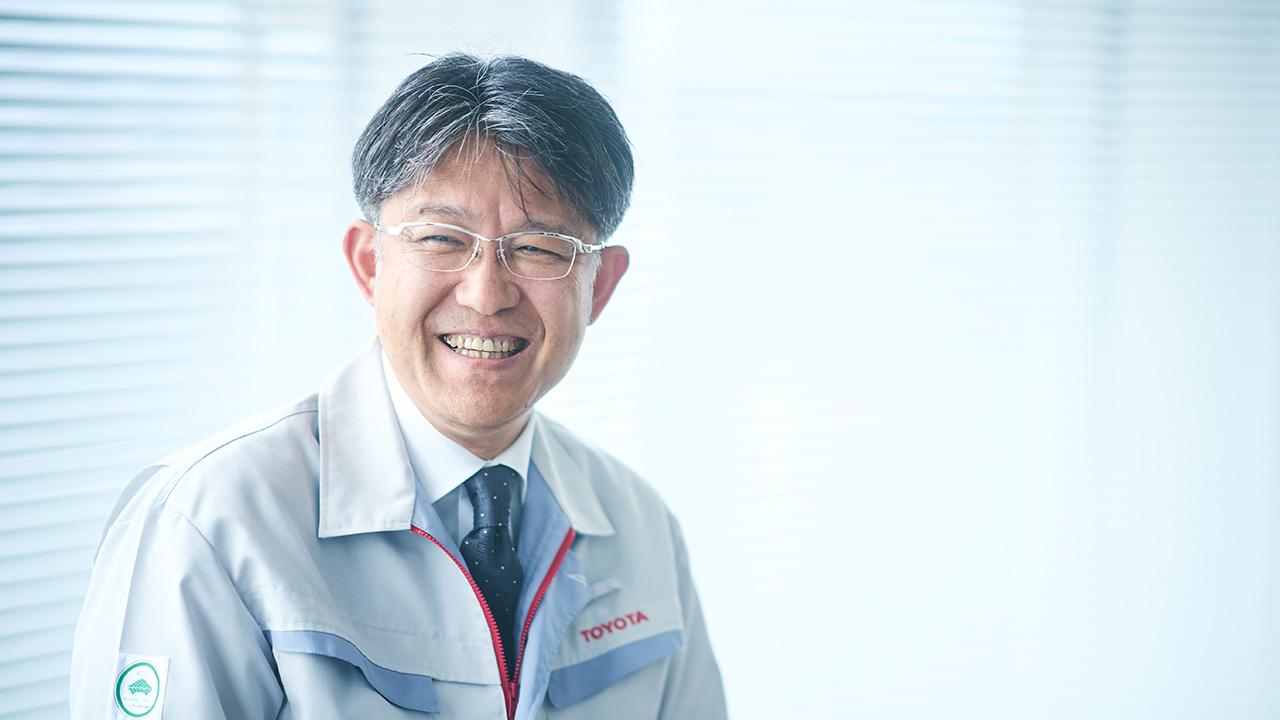
In April, Toyota held a media briefing to announce its direction under the new management structure led by Chairman Akio Toyoda and President Koji Sato. While many of the assembled reporters focused on details in the presentation, particularly battery electric vehicles (BEVs), the final question went in a different direction:
“Although you speak of a leadership ‘team,’ the members each have their own personalities. President Sato has said he loves making cars, but please elaborate on the others’ passion for cars?”
After both executive vice presidents, Hiroki Nakajima and Yoichi Miyazaki spoke of their love for cars, President Sato shared an episode from Toyota’s entrance ceremony, when the company’s officers welcomed new employees by displaying their cherished vehicles. “Please feel free to write a feature on this...” he began.
“A society where everyone can love cars in their own way. I think that kind of diversity is exactly what gives birth to innovation,” said Sato.

Automotive analyst Shinya Yamamoto was the one who posed that slightly offbeat question. He proposed interviews with each of the three newly appointed presidents, focusing on the personalities within the new team.
Although snippets from these interviews have already appeared in magazines and online articles, we asked Yamamoto to write up a special series for Toyota Times.
This first article shines the spotlight on President Sato, to be followed by features on BEV Factory President Takero Kato and Hydrogen Factory President Mitsumasa Yamagata.
Having covered Toyota for many years, Yamamoto shares his unique insights while delving into the three men’s personalities and love of cars, leaving no stone unturned.
The trio tasked with leading the new Toyota
(Text by Shinya Yamamoto)
On January 26, Toyota announced that, as of April 1, Operating Officer Koji Sato would become the company’s president. Then, on April 7, the new management team held a briefing to lay out its policies and direction.
Their theme got straight to the point: “Inheritance and Evolution.” This means honoring the Toyota-isms instilled by Akio Toyoda over his 14-year term while also picking up the speed at which they’re put into practice.
To turn this vision into reality, the company also made major reforms to its internal structure. One such change was the creation of two new dedicated units, the BEV Factory (May 15) and the Hydrogen Factory (July 1).
Each unit brings together all processes—from development to production and business operation—under a single leader to speed up decision-making and execution.
At the helm are BEV Factory President Takero Kato and Hydrogen Factory President Mitsumasa Yamagata.


What these three men have in common is the fact that they have been entrusted with leading new organizations. Of course, Toyota’s vice presidents and operating officers have also been assigned various duties, but only these three have been explicitly tasked with overseeing the new entities.
That is what piqued my interest and the reason why I requested these interviews. As I asked each about their experiences since joining Toyota, I came to see why Akio Toyoda entrusted them with such responsibilities.
Let’s start by hearing about their journeys to this point.
An unexpected appointment
While at university, Sato studied the environmental impact of burning methanol in diesel engines. This research was a forerunner of today’s carbon-neutral technologies, and Sato’s sense of purpose is partly what led him to Toyota.
Naturally, he hoped to work in the engine division but instead found himself assigned to a completely different field: Technology Administration.
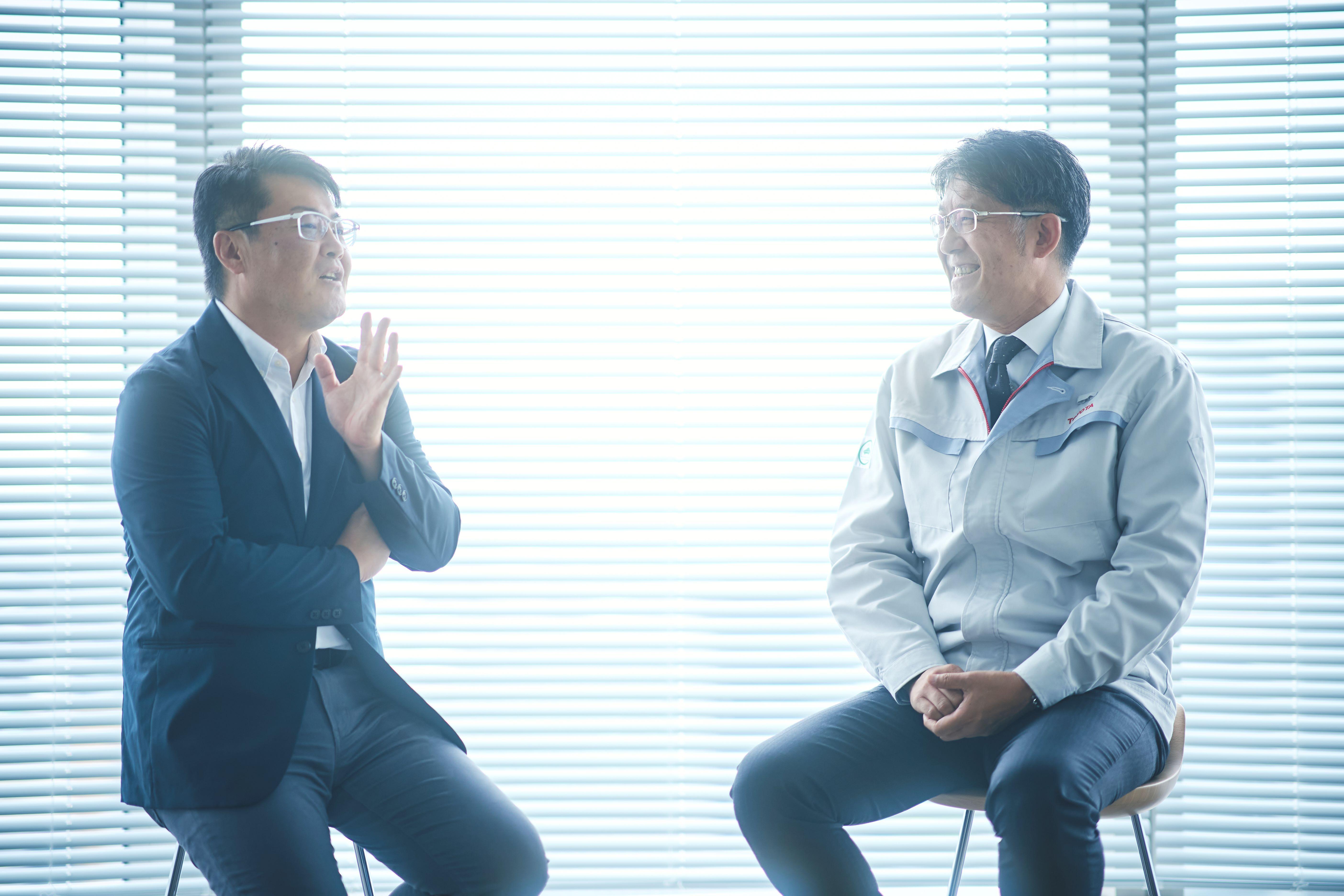
I was in shock for a while because the position was completely removed from my dream role. In those days, I was only interested in engines.
Instead of monozukuri, the Technology Administration Division’s main role was updating work systems. Once there, however, Sato’s senior colleagues showed him the “joy of looking at the whole car,” and his appreciation for the job gradually changed.
Through this job, I came to understand the mechanisms behind Toyota’s carmaking.
It was a great opportunity to learn about the overall workings of an automobile company: what procurement does, how sales works, and how Toyota makes cars.
As it happens, during this period, he worked under Takeshi Uchiyamada, the executive fellow who stepped down as chairman when Sato assumed the top job.
At the time, Uchiyamada was leading the technical department operational reforms, and I was assigned to that part of his administration team.
To keep his sensors sharp, Uchiyamada’s routine included driving various cars two or three times a week, including competitors’ models.
I was tasked with going out and picking up these cars. Under this pretext, I had the chance to ride in many different vehicles on the test course, which got me thinking, “I want to try building cars like this myself.”
The life-changing CE suggestion
Perhaps sensing how Sato felt, one day, Uchiyamada told him:
“I’m not sure that engines are right for you, but how about going for chief engineer (CE)? To be CE, you need a firm grasp of vehicle dynamics, and a good place to learn the fundamentals is chassis engineering.”
Sato says he still remembers that exchange vividly.

At the time, I thought, “Great, so he even decides where I get transferred!” (laughs)
In hindsight, however, it’s fair to say that this advice changed my life.
Sato did indeed get transferred to the Chassis Engineering Division. Though he started out designing small parts, it was here that Sato discovered the joys of monozukuri.
In turn, he was given larger assignments. Still, after submitting drawings for a suspension lower arm (part of the suspension frame) that he had designed for a particular car, Sato received a summons from the genba.
When I got there, around 20 skilled veterans were waiting for me. “You’re the one who drew this?” they asked. “Go ahead and try to weld it as shown.” That’s when I realized that the welding symbols were wrong.
Fixing drawings on the production floor is probably a common practice in manufacturing, but Toyota’s genba instead used these opportunities to enlighten designers.
I was told, “These drawings are everything for us and the basis for monozukuri. When it comes to drawing parts that keep customers safe, you can’t do things by halves!”
This experience taught me to put more thought into the drawings, and I understood firsthand that, ultimately, it is people who make things.
Another time, some older colleagues told me to fetch four lower arms for the Corolla with the bushings (rubber parts) fitted...
As I rushed around the plant, I learned how bushings are fitted, along with the rules for moving things around the company. Seeing how heavy the four arms were, I began to think, “I need to make these lighter.”
Thinking back on it, that was my colleagues' way of encouraging me to learn about monozukuri in a hands-on way.