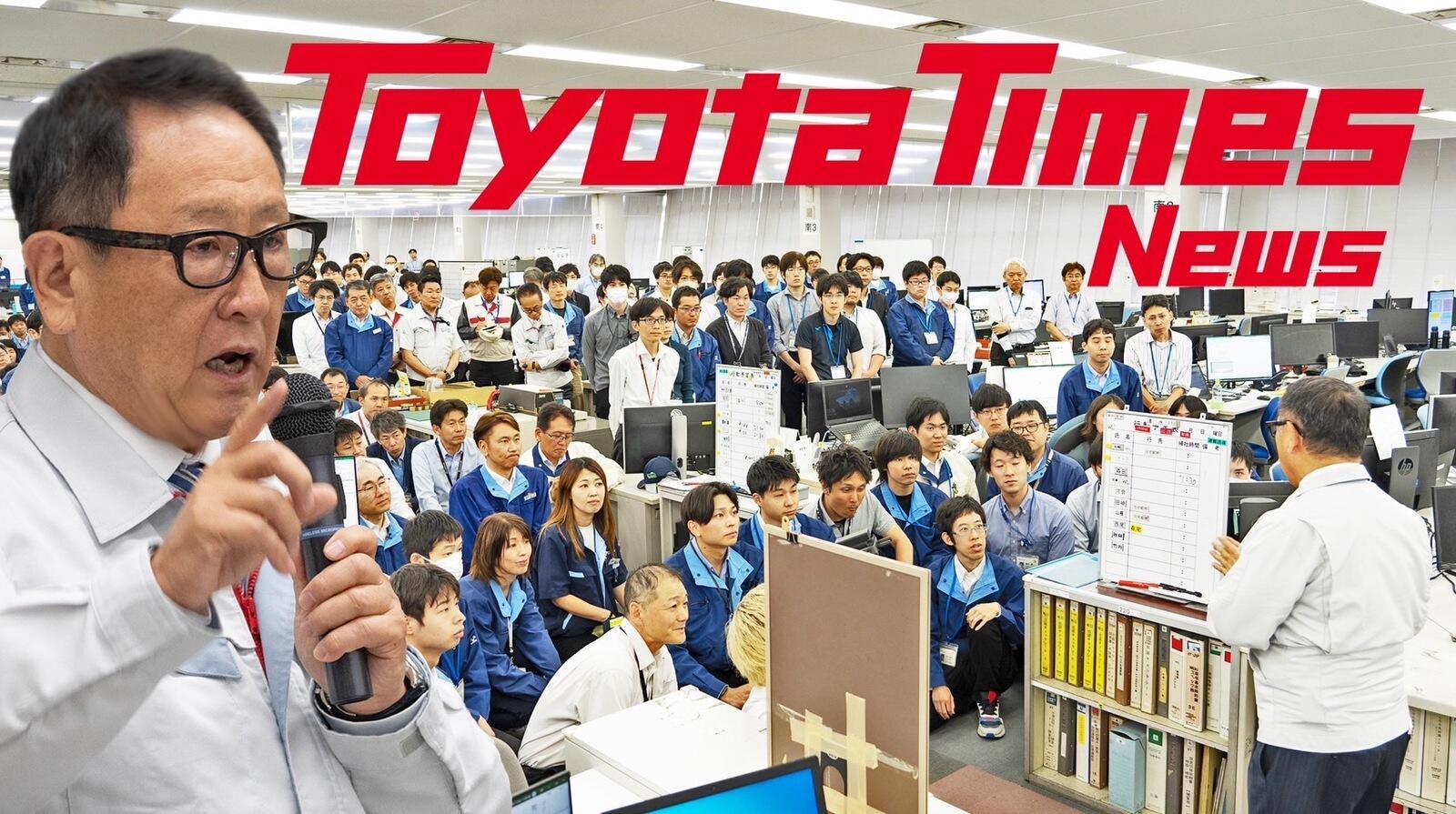
Top management and the employees met onsite and put their heads together to hold a TPS (Toyota Production System) Jishuken (Joint Kaizen Activities) for certification work. We followed the efforts of Group companies to correct their processes.
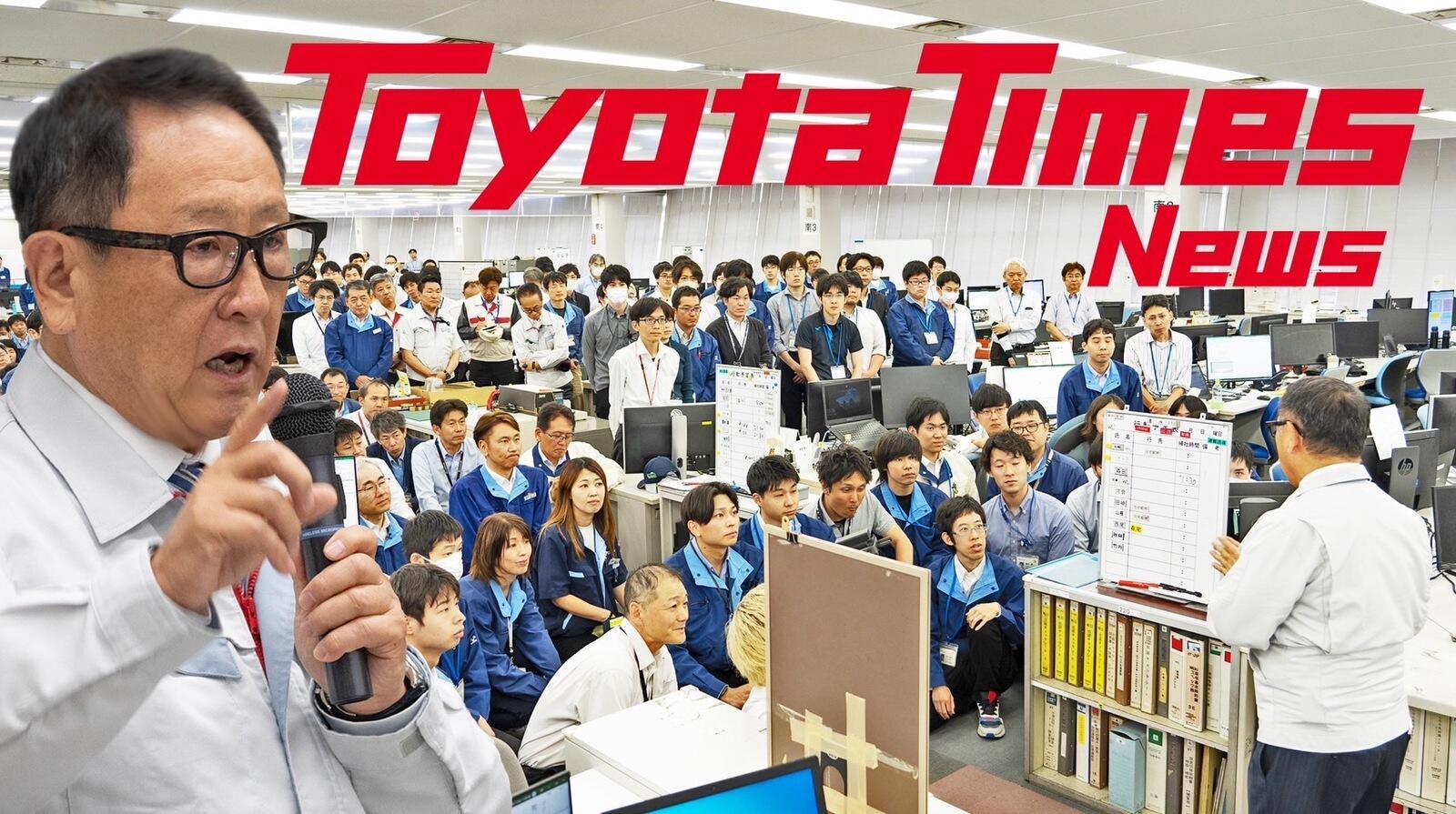
Top management from four Toyota Group companies—Hino Motors, Daihatsu Motor, Toyota Industries Corporation, and Toyota Motor Corporation—together with the employees, donned their work clothes and went to the genba to put their heads together and face the issues.
Since 2022, the Toyota Group has faced ongoing certification issues*. Last February, Chairman Akio Toyoda established Akio Toyoda’s Juku TPS Jishuken for Certification Work to ensure the same mistakes are not made again.
* Group companies were carrying out certification testing necessary to apply for type approval to mass-produce car models using standards that differed from the ones set by the government.
Their goal was to use kaizen to create better systems for work. Their target was not only the certification work itself but the entire process leading up to certification, including planning, development, design, and production preparation.
Using the material and information flow diagram, they clarified the overall system behind their work, making it easy to see delays caused by re-dos and reworkings. This helped identify the true causes and implement countermeasures using genchi-genbutsu.
Early lessons from the TPS Jishuken included that to apply for certification for one model requires 1,300 pages of paperwork, that pressure to stick to the schedule piles up on the certification genba, and that there is anxiety about being able to perform the test correctly in one try due to the extreme pressure.
As the person responsible for guiding the Group, Chairman Toyoda is in charge of the activities. He praised the genba and offered some advice, saying, “I think we came to understand a lot of things we didn’t know before. Starting to understand is the first step forward.” “Don’t look for someone to blame for problems. Look at what happened. That’s the culture we need to create first and foremost.”
The aim is to build a system where it’s possible to find the issue and take action as soon as something happens.
From minivehicles to heavy-duty vehicles to engines, the four companies are deepening their connections and working together, sharing industry issues and developing case studies.
What happened at Toyota? How is the Toyota Group going to make a fresh start? See this effort to overcome Group boundaries and job titles and work together to face issues.