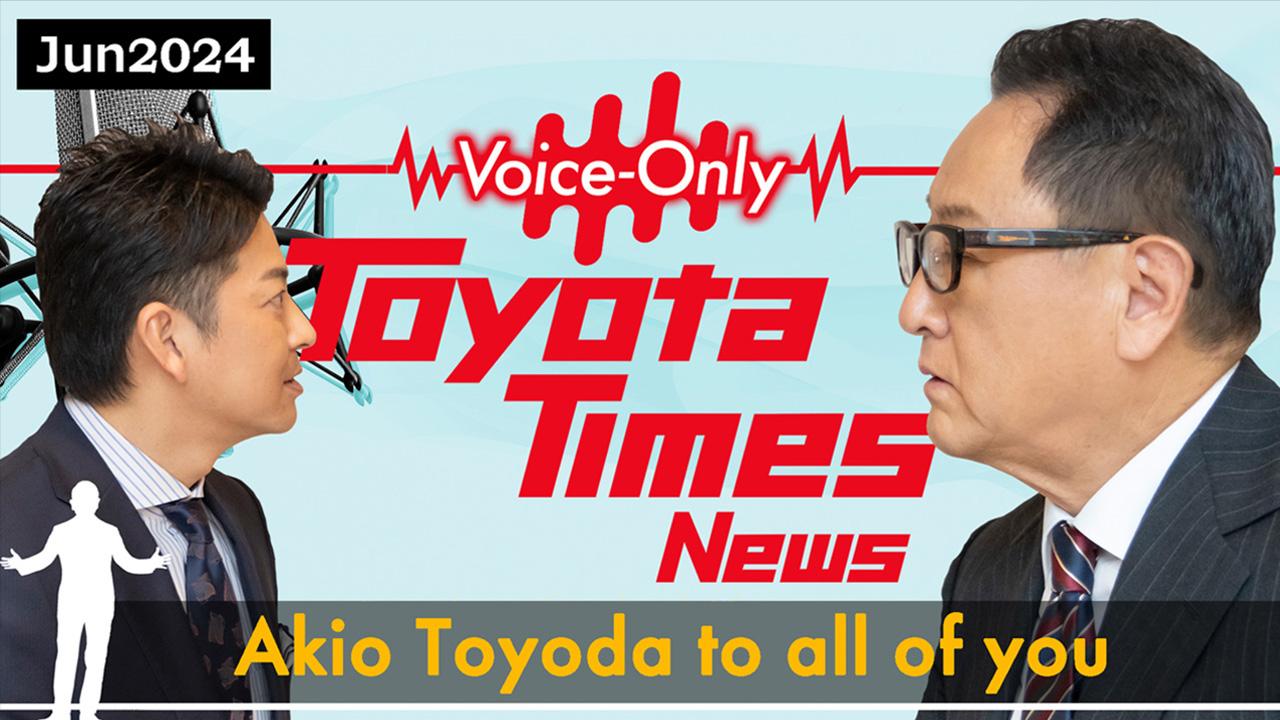
Toyota Motor Corporation held a press conference on June 3 in response to instructions from the Ministry of Land, Infrastructure, Transport and Tourism to investigate applications for model certification. What were Chairman Akio Toyoda's thoughts as he faced this press conference?
6 cases
Tomikawa
To avoid inciting any undue anxieties, I'd like to explain what happened to the best of my ability.
As mentioned at the top, there were six cases in which it was found that tests were conducted using methods different from national standards. The six cases are as follows.
(1) Development test data with airbag timer system applied for certification
(2) Impact angle inconsistent with regulation
(3) Development test data of other measuring points applied for certification; left used for right and vice versa, unilateral used for both sides.
(4) Moving barrier weight inconsistent with regulation
(5) Luggage block inconsistent with regulation
(6) Adjustment of the engine control system during testing
For three of these cases, (1), (2), and (4), stricter conditions than the regulations were used, which was incorrect and thus considered wrongdoing,
just as Akio mentioned earlier.
Of the remaining three cases, (3) involves testing the impact on a pedestrian's head and legs using weights to simulate a human head and legs colliding with either side of the vehicle.
Although it has been confirmed that there is no difference in the results on either side of the vehicle, data from the reverse side was used on the wrong side, or data from a single side was used for both sides.
Case (5) involves testing the damage to the rear seats caused by luggage shifting during a collision. There were additional requirements for luggage blocks due to changes in regulations, but data from old blocks were used. However, it was found that the weight of the old and new blocks is the same.
The last case (6) involves a certification test for engine output. Before certification testing, multiple output tests were conducted during the development stage, meaning there was a clear idea of expected values.
However, because the certification testing somehow failed to produce the expected values, retest data were used in which computer controls were adjusted, rather than finding the cause of the problem and repeating the trial, as should have been done.
It was later found that a crushed exhaust pipe had likely caused the discrepancy, and replacing the pipe achieved the expected values.
In short, there were no issues with the engine's output itself.
These are the cases where tests were conducted using methods different from national standards.
To conclude, I'd like to ask once again, is it safe for those currently driving the cars in question to continue driving them?
Akio
Yes. Certification tests whether a car can be mass-produced in terms of environment and safety.
Ideally, we could make and test prototypes of every single car of the millions sold to ensure each car is safe, but that is completely unrealistic.
That is why the authorities have rules saying, "If you test this vehicle and that vehicle, you can start mass production," and although we didn't follow those rules this time, the cars themselves are safe to drive.
However, since we violated production rules, plant production is temporarily halted until authorities conduct on-site audits and grant approval. This will cause inconvenience and delays for current customers, though some of the affected models date back to 2013 and 2014 and are no longer in production.
So, while most people affected are current users, it is safe for them to drive their vehicles.
Tomikawa
We touched on this a moment ago, but I'd like to ask a simple question about safety.
In certification testing, if a car passes stricter conditions than those designated by regulations, I imagine it would be safer, but this is still considered wrongdoing or false reporting. Is that correct?
Akio
I cannot answer that right now.
Tomikawa
I’m really just asking it as a simple question.
Akio
I do not think I can say "yes" to that right now.
Tomikawa
But there are undoubtedly people who feel that way, so it must be discussed and improved further.
Akio
It will need a little more time. The time to discuss it will come.
TPS Jishuken
Akio
We are currently conducting a TPS Jishuken using the material and information flow diagram. Toyota is often equated with TPS, but many people do not fully understand it. Even within the company.
Tomikawa
There were indeed questions that showed a lack of understanding.
Akio
One reason we use TPS in the form of a TPS Jishuken is that it defines the "three mechanisms of work-in-process."
For example, the "instruction kanban card" specifies what parts to produce and in what quantity. Then, the "order" indicates the sequence in which to produce them. Then there are the "materials" necessary for this. Work must not commence until all three elements are in place.
The kanban card indicates what to produce by when, and the order indicates the order of tasks, so work must be standardized. The third element of materials includes necessary data, tools, parts, and materials.
In a production environment, work should not start until all three elements are completely in place. Starting work without them leads to rework and malfunctions.
Without standardized work, even if you work quickly, you'll have to redo things, causing repeated delays in different processes, and if you make a material and information flow diagram, the total lead time is about three years or at least a year.
Consequently, no one, including myself, grasps the situation.
Focusing on certification alone wouldn’t help. The lead time of 300 to 800 days includes long periods of standstill. Nearly half the time is spent waiting for work or redoing things.
Starting work only when the three elements of work-in-process are in place significantly shortens lead times, which is why it is vital to wait until everything is ready.
Akio
That is why supervisors must properly confirm these three elements. Have the workers do the work and make sure nothing remains ambiguous. I am requesting time to get this in order.
People who hear TPS Jishuken may think it's all about "working more efficiently," but TPS is a mindset.
It is about using the philosophy and skills of TPS in your mindset and work, which is something I hope more people will come to understand over time.
I actually think this was a good opportunity. Having a feature by Toyota Times explaining why Toyota is solving this issue using TPS might reassure more people.
Tomikawa
You recently visited the Toyota Industries work site and heard what workers there had to say. Toyota Times has been edited up to that point, but looking at it, there are a lot of items, and things are rather vague.
Akio
It is vague.
Tomikawa
That is why people leave the decisions to others.
Akio
They do. So, say we try to solve each one in-house first.
But this time, Hino handled large vehicles, Daihatsu handled minivehicles, Toyota handled passenger cars, and Toyota Industries handled engines. This means that certification work has flowed across different fields. If we work together, we can move away from individual and arbitrary ways and establish standardized work across the Toyota Group. If we standardize work, problems will be clearer. We can respond immediately to problems with the proper work methods.
I hope to have the system in place within the year.