
TPSは、システムを取り入れればできるものではない。その道を究めたプロフェッショナルが明かした秘訣とは。

岩手県釜石市、唐丹(とうに)町。世界三大漁場のひとつである三陸沖に面し、リアス式海岸による“天然の良港”をもつ、静かな漁師町だ。
サケ、ウニ、アワビなどの水揚げのほか、ワカメやホタテの養殖も行われ、町民の多くの人が漁業に携わっていた。
しかし、2011年。東日本大震災の津波が、高さ12mの防潮堤を乗り越え、町をのみこんだ。470隻あった漁船もほぼ破壊されてしまった。
そんな中、町の水産業を立て直すために、立ち上がった小さな水産加工会社がある。震災前から存在していた会社ではない。地域の人に働く場と生きがいをつくろうと、震災後に新たに設立された会社である。
今回、トヨタの友山エグゼクティブフェロー(以後、EF)がその会社に足を運ぶと聞き、トヨタイムズの森田記者も同行。その模様をレポートする。
なぜトヨタが、釜石の水産加工会社に?
釜石ヒカリフーズ。従業員51名の小さな会社である。
友山EFが訪れた理由は、“改善活動の共有” だという。友山EFは、トヨタ生産方式(以後、TPS)を推進する生産調査部で、“改善マン”としてキャリアを積み、TPS本部のトップにも就いたその道のプロフェッショナルだ。まず、トヨタと釜石ヒカリフーズに、どのような関係があるのか調べてみた。
2011年、豊田社長は被災地を訪れ、「東北復興の原動力となるには、モノづくりの基盤をつくって雇用を生み、地域の方と一緒に東北の未来をつくることが一番」と考えた。そして翌年、トヨタ自動車東日本が誕生。
その後、岩手県からトヨタ自動車東日本に相談が入る。「被災した三陸の水産加工会社を、TPSの改善手法で救えないか」という内容だ。
多数の水産会社が津波の被害を受けた。さらに、人手不足という深刻な課題だけでなく、原材料の供給不足も重なり、事業を続けることに困難を極めていたという。ただでさえ高齢化や人口流出に悩んでいた漁村から、仕事までなくなる危機だった。
そのような中でも、三陸の人たちは「なんとか、はい上がって頑張ろう」「自分たちも復興の力になろう」と懸命に前を向いていた。
そこで、トヨタ自動車東日本は動き出す。全くの異業種とはいえ、何かできることがあるはずだと考え、“異業種相互研鑽活動”を開始。
なぜ“相互研鑽”なのか。それは、トヨタが一方的に改善を教える、といった構図ではないからだ。
トヨタ自動車東日本の社員にとっても、他社の考えに触れ、一緒に改善活動を進める中で視野が広まるメリットがある。周囲を巻き込んでダイナミックに引っ張れる人材へと成長できれば、場所を問わず活躍が期待できる。
友山EFは、その意義についてこう話す。友山EF
カーカンパニーからモビリティカンパニーへと変革する上で、今後はあらゆる異業種と協業することが増えていく。トヨタの中だけで通用する人材ではいけない。新たな視点や人間関係のつくり方を学び、プロジェクトを遂行することで、(人間性が)鍛えられる。
トヨタ自動車東日本は、東北6県と新潟県の各行政を通して、あらゆる業種と研鑽活動を推進。2020年度末までに延べ119社と改善活動をともにしてきたそうだ。
そんな“異業種相互研鑽活動”に、率先して手をあげたのが、釜石ヒカリフーズだった。水産加工の現場を激変させたTPS
この活動は、トヨタ自動車東日本のTPS推進部署のメンバーが、2人1組となり、研鑽先に出向く。心がけることは、研鑽先の相手に「改善は面白い」と思ってもらうこと。
面白いと思ってもらえると、“さらなる改善”が自発的に生まれてくる。すると、相互研鑽が終わった後も、一過性ではなく、TPSでの改善がしっかりと定着するようになるからだ。
釜石ヒカリフーズでは、この取り組みが始まってから、現場に大きな変化があったという。たとえば、加工現場に入る前から改善は始まった。【改善前】
1日の作業内容は、その日にならないと分からない
▼
【改善後】
1週間分の分担を決め、入口のホワイトボードで役割を確認できる
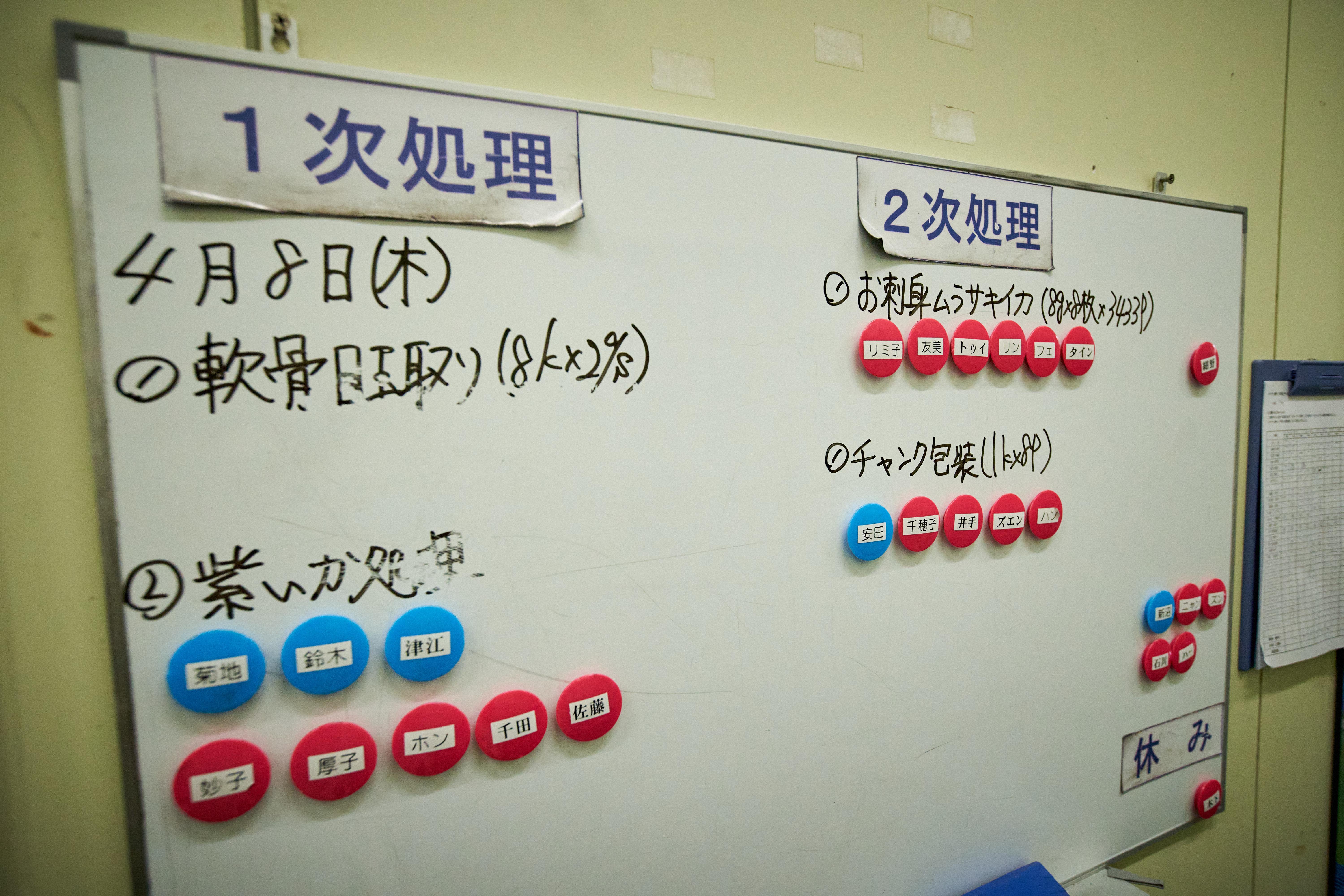
これにより、あらゆることが “見える化”された。一人ひとりの作業が明確になるだけでなく、作業スタッフの負荷もひと目でわかる。
また、各作業に基準時間を設定することで、標準化。さらに、加工途中の“仕掛かり品”が、日をまたぐことがなくなった。これにより、品質のムラや、冷凍庫への出し入れといった余計な動きも削減できた。
【改善前】
全員で1カ所に固まって作業
▼
【改善後】
工程に分けて、ラインで流れるように分業
これにより、処理できる量が格段にアップ。運搬のムダがなくなり、工程ごとに品質基準を決めて検査をすることで、不良品の発生も抑制。従業員51人と小さな会社だが、今では1日最大3トンの食品を加工できるという。
【改善前】
天井のコンセントに、脚立を使って電源コードを挿す
▼
【改善後】
延長コードを垂らし、立ったまま電源コードを挿せる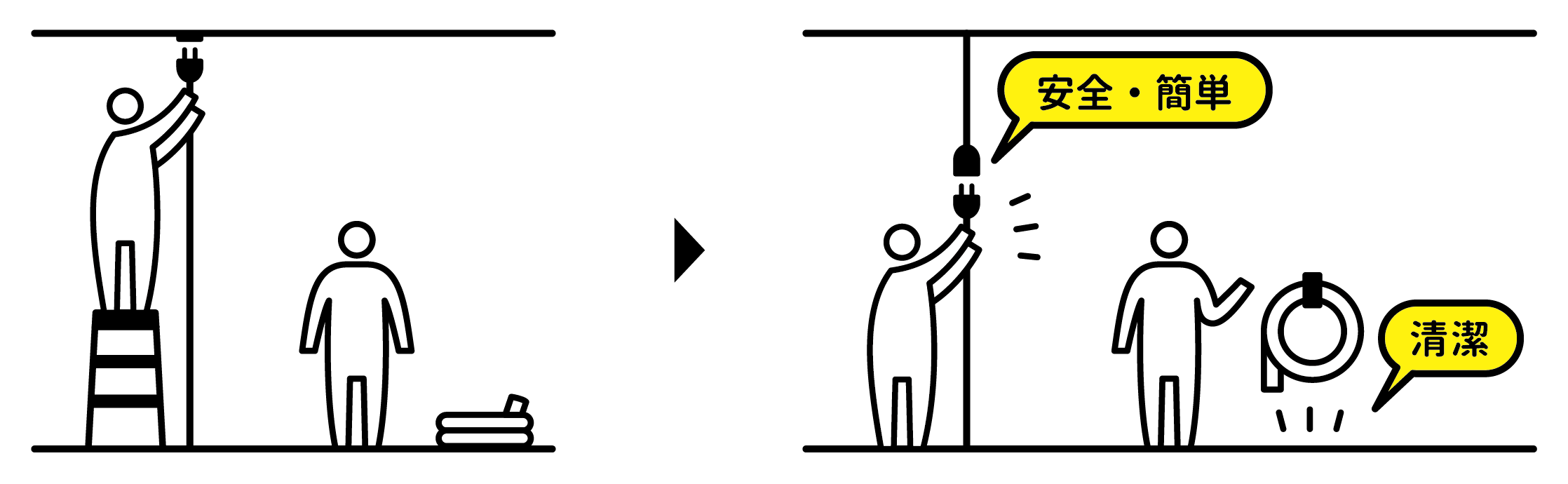
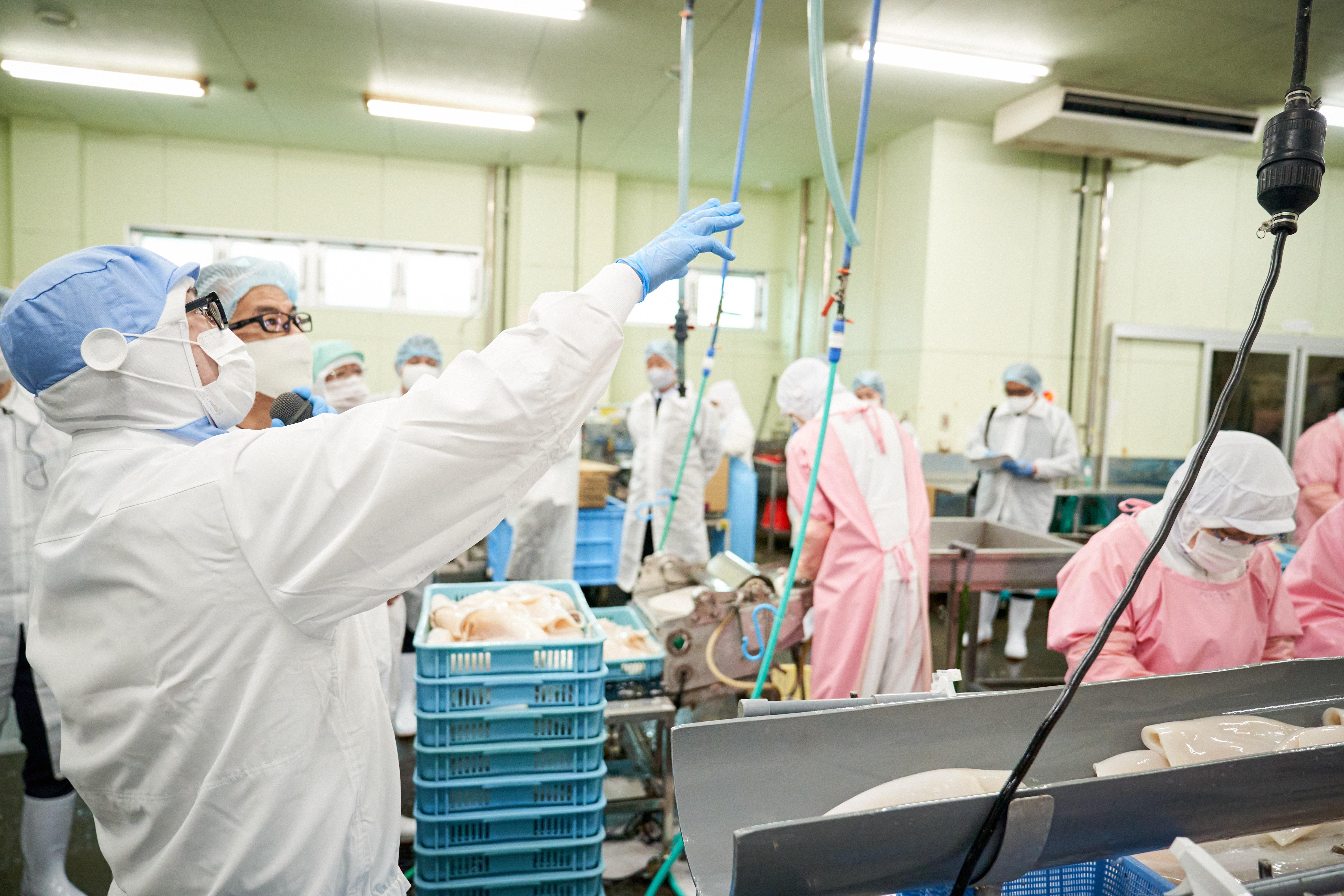
段取り替えの際、脚立の上に立って接続していた電源コードも、手を伸ばすだけで使えるようになった。床が濡れた水産加工の作業場で、脚立に登らなくていいので安全性が向上。また、床に置いていた水道ホースも壁に立てかけることで動線確保、ムダな動きも削減できた。
【改善前】
BGMがなく、無音の加工場で作業
▼
【改善後】
最新のJ-POPから演歌、洋楽まで流している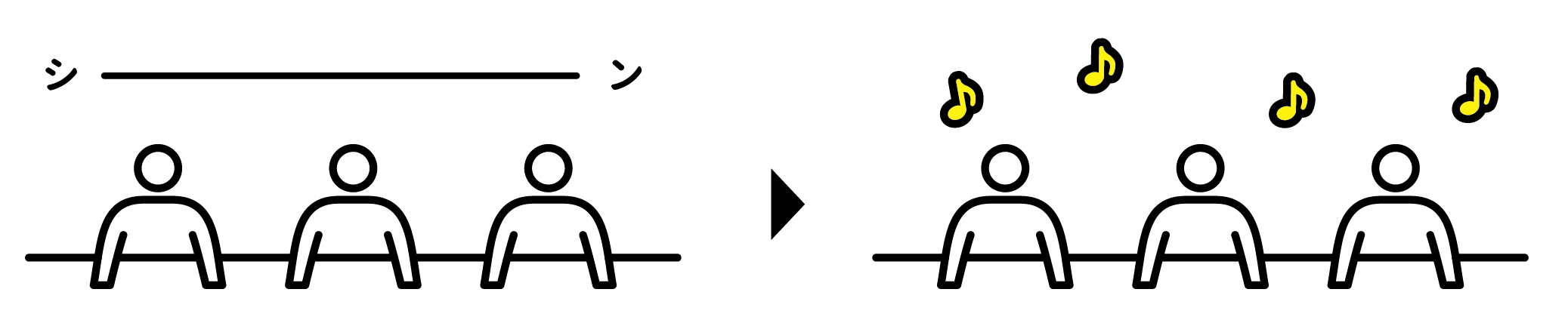
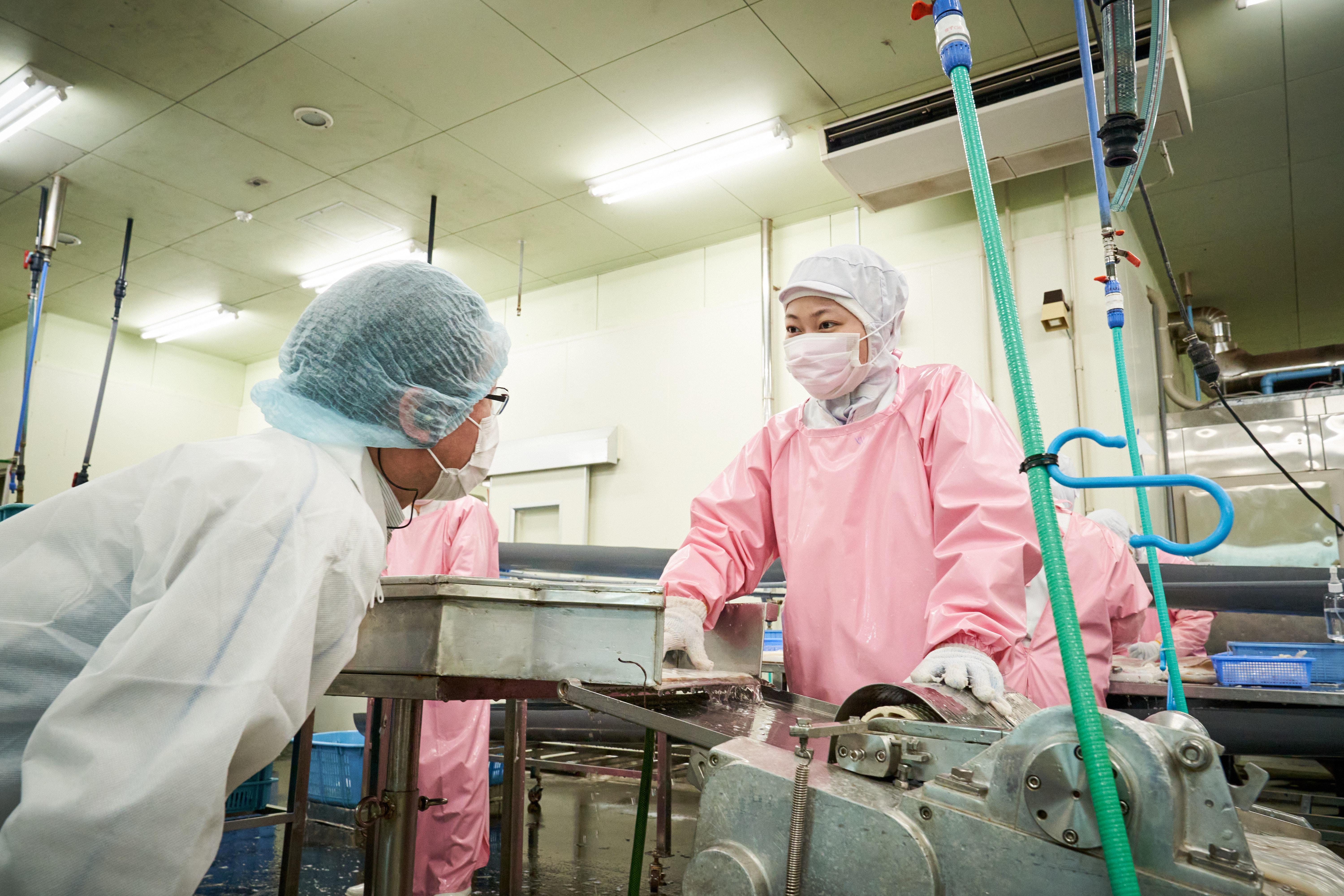
これは、作業スタッフの年齢層が、10代から70代と幅広く、さらに多国籍であることに配慮。仮設住宅で生活していたスタッフも多かったため、楽しくリラックスして働けるよう、スタッフの要望に合わせて毎日BGMを変更。取材したこの日も、懐かしいJ-POPが工場内に流れていた。こうした小さな部分から環境改善に取り組んでいる。
これらはほんの一例に過ぎないが、釜石ヒカリフーズの佐藤正一代表取締役社長によると、TPSの導入により3つの変化が起きたという。

一見あたり前のように感じる改善だが、水産加工業のように、経験値が重視され、代々仕事が受け継がれていく現場では、“改善する”という意識自体が生まれづらい。
そんな中でのTPSによる改善は、確かな結果へとつながった。そして、それは従業員の誇りや、働きがいという目に見えない変化にもつながっている。
働きやすさが高まるにつれ、現場のスタッフからも自発的に「ここをこう変えたい」と改善案がいくつも出るようになったという。作業効率だけでなく、スタッフの意識も変わったのだ。トヨタには、“モノづくりは、人づくり”という言葉があるが、まさにそのことを表すエピソードだと感じた。
2018年10月から、2019年3月まで続いたトヨタ自動車東日本との相互研鑽活動。この活動が終わっても、現場の改善への意識が途絶えることはなかった。
釜石ヒカリフーズの社内の至る所に、「改善・継続・努力」という言葉が掲示されていたのが印象的だ。TPSという共通言語
加工現場に入った友山EFは、なぜか楽しそうに見えた。釜石ヒカリフーズの白土課長から改善内容の説明が始まると、冷凍庫の前に積まれた水産物の箱を見て、早速質問を投げかける。
友山EF「この箱は冷凍庫にいつ入れたかわかるの?」
白土課長「あ、カンバンが必要ですね」
水産物が入った箱は、届いた後そのまま冷凍庫に入れられ、使われるタイミングを待つ状態になっていた。冷凍庫に入れたタイミングを記載したカンバン(生産や運搬に必要な情報が書かれたカード)を箱につければ、先入れ・先出しが管理でき、冷凍庫内で長時間滞留することがなくなる。
そこに目をつけた友山EFの質問、そしてその意図を即座に理解して反応する白土課長。友山EFは「わかってるねぇ」とうれしそうな表情を浮かべていた。このやり取りだけでも、現場にTPSが根付いていることを感じた。
その後も、「取り除いた内臓は(滑らせて移動させる)シュートで下に落とせるようすると良い」「このラインの間隔を詰めればもっと作業がラクになる」「包丁の交換頻度の目安を設定すれば、切れ味が落ちず作業がスムーズになる」など、友山EFからは次々と新たな改善案が出てくる。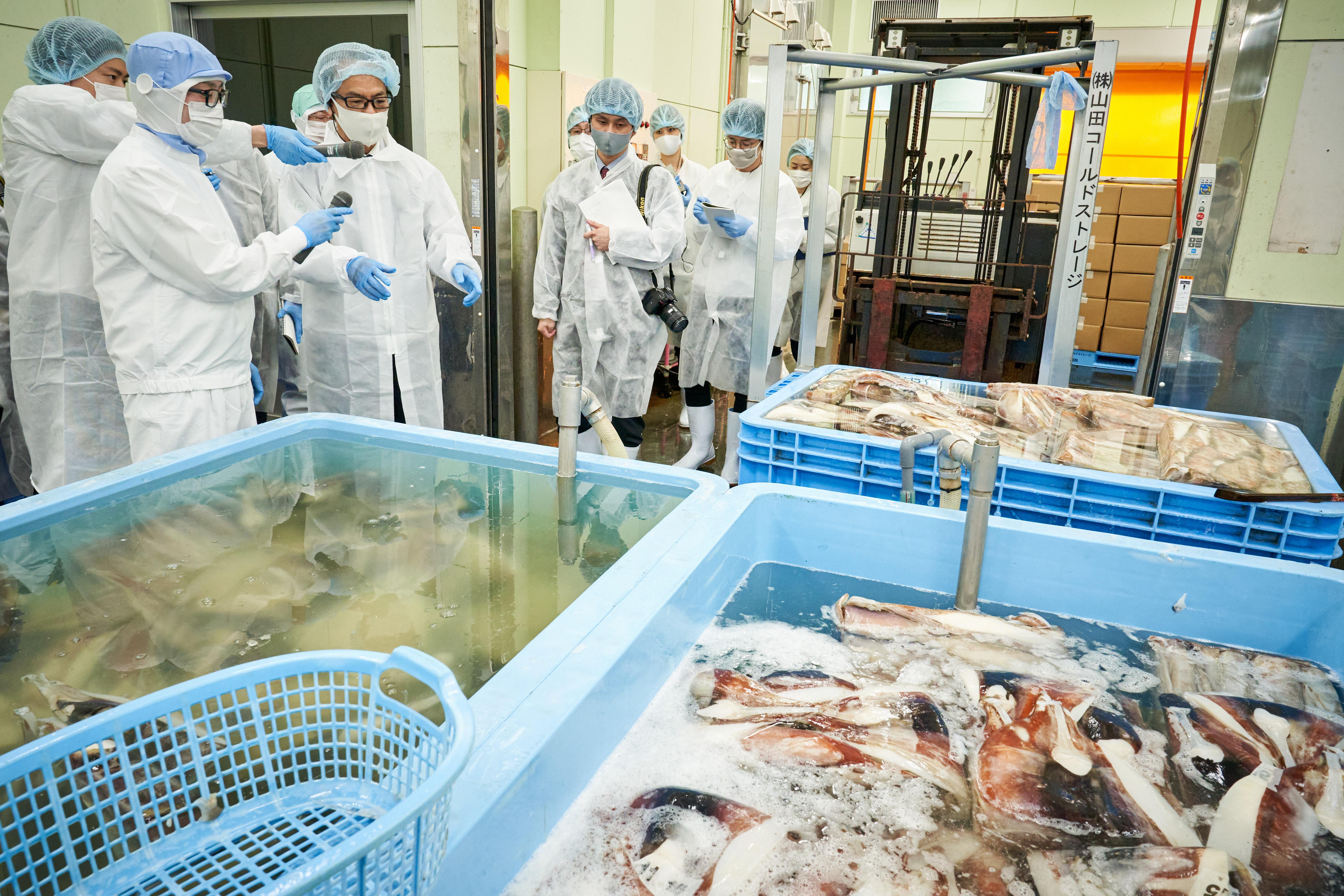
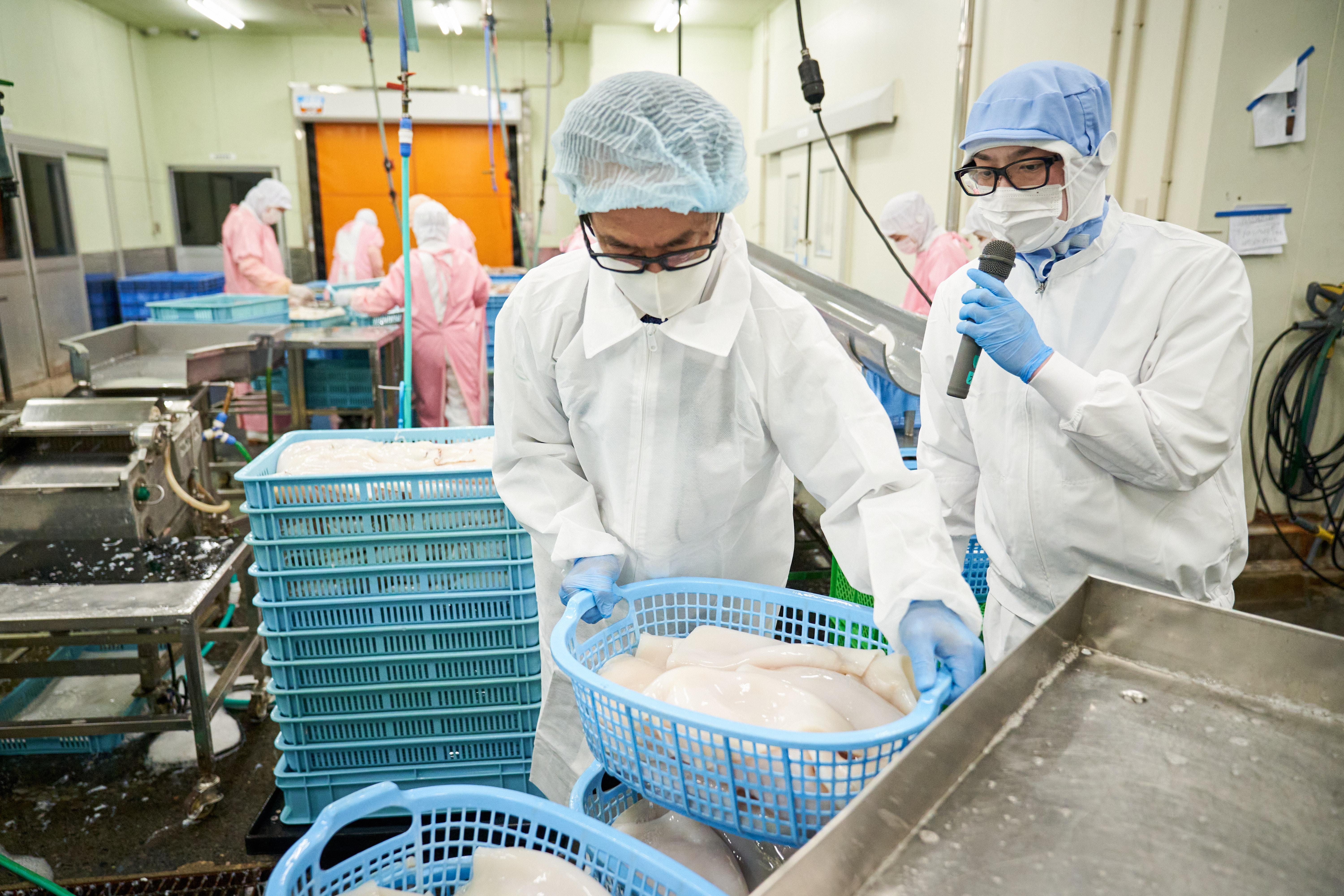
すると、佐藤社長や白土課長が、即座に取り入れる内容を判断する。「カンバン」や「からくり」といったいわゆる“トヨタ用語”が出ても、その意味を理解しているため、意思疎通できるのだ。まさに「現場が生きている」、そんな光景を目の当たりにした。
水産加工業と、クルマづくり。まったくの異業種だが、同じ“モノづくり”だと友山EFは話す。そこには、TPSという共通言語がある。
佐藤社長が、TPSを導入したことによる変化として最初に挙げたのが、従業員の負担軽減だ。 “誰かの仕事をラクにする” “従業員に意味のある仕事をさせてあげたい”というTPSの原点が、しっかりと共有されているように思えた。定着と、停着の違い
加工現場での議論を終えた後、友山EFはこう話した。
友山EF
定着とは、同じことをやり続けることではない。できるかぎり現場で問題を発見し、改善し続けることがTPSの定着。同じことをやり続けるのは、停止の“停着”。
すべての生業(なりわい)には工程がある。それぞれの工程でどういう品質に仕上げるか良品条件を決める。そして工程ごとの標準作業を決める。そういうことを一つひとつやっていくと、おのずと品質や生産性は上がっていく。
すると、業績が上がるだけでなく、お客様にも喜んでいただける。決して製造業だけでなく、すべての生業で成果を出せるのがTPS。
ただし、TPSはシステムを取り入れれば(誰でも)できるものではなく、土壌づくりが重要。土壌とは、会社として目指すべき仕事の仕組みや、目指すべき人材像、目指すべき風土。仕組みは限りなくリーン(ムダがなくスリムな状態)で問題が顕在化する仕組み、人材は自ら改善できる人材、風土はそういうことを美徳とする風土。これこそ他社は一朝一夕ではできないから、コンペティティブ(競争力がある)になれる。
この日、作業していたムラサキイカの加工では、TPSでの改善前と比べ、生産効率が約30%アップしたという。しかし、この日の友山EFのアイデアを生かせば、さらに10%程度、効率改善が期待できるという。
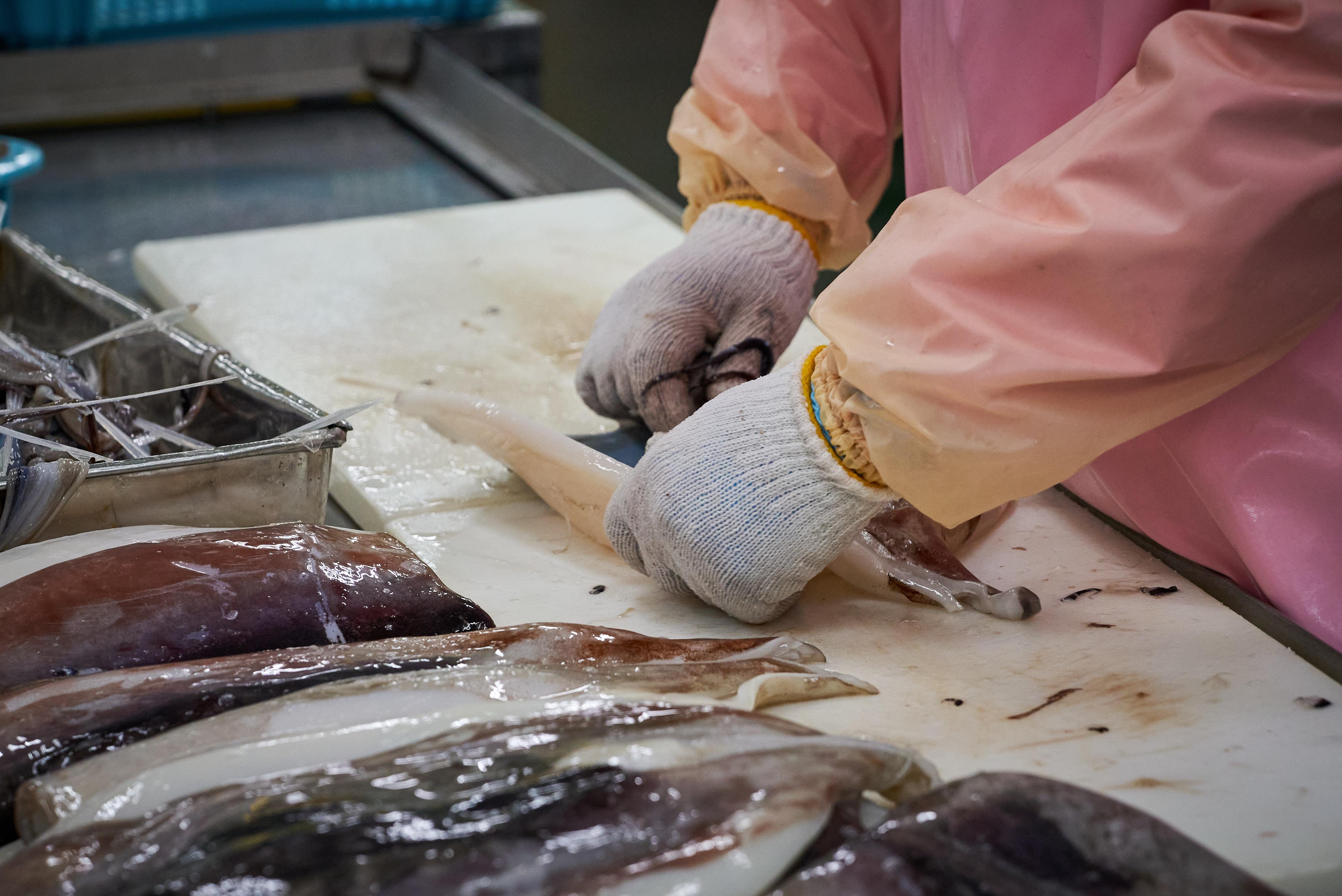
現場で次々と出た、友山EFのアイデア。「改善後は改善前」とよく聞いてはいたが、“TPSに完成形はない”ことを改めて痛感した。
では、なぜトヨタがTPSを自分たちだけでなく、他の業種に広めているのか。
友山EF
トヨタフィロソフィーでは、トヨタのミッションを「幸せの量産」と言っている。
幸せってなんだろうと突き詰めていくと、モノをつくって、それを使ってもらって、水産業では食べてもらって、喜んでもらえる。つまり、お客様も、つくる人もみんなが幸せになれる。
TPSは業種を越えた、共通の価値観を生み出せる資産。それを我々トヨタが広めるのは、社会貢献だけではなく、トヨタが社会にとって、これからも必要だと思ってもらえる意味でも重要。
また、モビリティカンパニーとして異業種と協業していくためにも、他のIT企業と違い、TPSを織り込むことで他と差別化した何かを生み出せるのではないか。だからこそ、そういった人材を育てないといけないし、異業種研鑽活動のような中で育っていくと思う。実際、この場に同席していたトヨタ自動車東日本のTPS推進部で異業種研鑽を推進する工藤グループ長は、メンバーの成長についてこう話す。
工藤グループ長
まったく知らない業種に出ていくので、まずは信頼してもらうところから始めなければならない。経験したメンバーを見ていると、周りを引き込む力が以前とまったく違う。今までなら一人で仕事を抱え込んでいたが、知らない部署に自発的に相談を投げかけて仕事を進めるようになった。
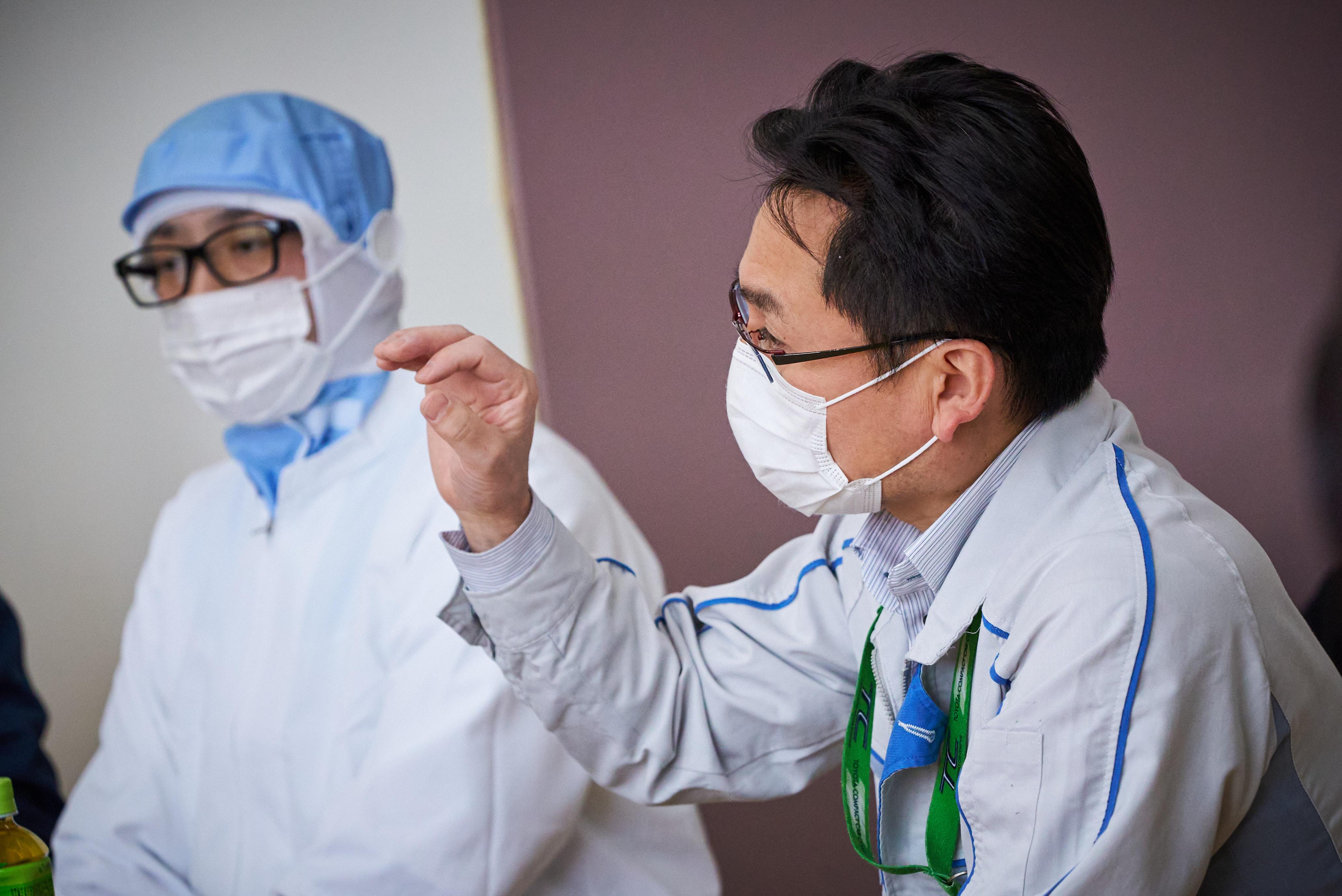
この話を受けて、友山EFは「トヨタの中だけで育つと、それだけ危険だということ」と話す。これには取材陣から思わず笑いがこぼれたが、友山EFはこう続ける。
友山EF
それなりの大学を卒業してトヨタに入ってくる。基本的に上から目線になりがちな人も多い。トヨタの看板がまったく通じない場所を経験することが重要。(異業種に出て)そういう人材を育てていかないと、トヨタが単なる製造業ではなくなっていくこれからはダメだと思う。
この話を聞き、異業相互種研鑽活動の意図が、より明確になった。はじめは、TPSを外部の会社に伝えることがなぜ“相互”なのか、疑問に思っていた。実態は、異業種と仕事を進めるための大切なことを、トヨタが教えてもらっていたのだ。
釜石ヒカリフーズの白土課長は、研鑽活動でやってきたトヨタ自動車東日本の社員が、自分たちのやり方を押し付けるのではなく、相手に寄り添い、同じ目線に立ってくれた、と感謝していた。
友山EFは最後に「誰かのために、何とかしようと頑張る人には、自然に仲間が集まってくるものだ」と力を込めた。TPSを、東北のモノづくりの原動力に
釜石ヒカリフーズ。その名前には、震災でマイナスになった釜石の水産業をゼロに、そしてプラスに戻し、復興の希望の光を灯したいと願いが込められているという。
2011年の会社立ち上げ時は、工場の土地探し、資金集め、人集め…。何もかもがマイナスからのスタートだったが、今では大手居酒屋や回転すしチェーンから仕事を依頼されるまでに成長した。TPSでの小さな改善の積み重ねが、大きな競争力につながっている。
佐藤社長は「釜石の人に安心して水産業に従事してもらい、収入を得て生活が安定すれば、みんなが地元に誇りを持てる。それが、町の再生にもつながっていく。重労働で魚臭いという水産業のイメージを変えたい」と話す。
取材の中で、友山EFが現場に入ってすぐに、受注からモノ・サービスの提供までにかかるリードタイムを「鮮度」と結びつけて語ったことが印象的だった。水産加工業において、それぞれの工程のリードタイムを短くすることは、鮮度を高めることにつながり、それは付加価値の向上をもたらす。TPSとの親和性を感じた。
前回の、岩手県葛巻町の取材と同じで、「困りごとを解決したい」「自分以外の誰かのために」という佐藤社長の強い想いがあり、そこにトヨタグループが関わる姿勢も共通している。
これまでの取材で、震災以降に培われてきた東北のモノづくりの力を見聞きしてきたが、今回はクルマ以外の形が見えた。復興支援の広がり、そしてTPSの普遍性を感じる機会となった。