
自動車業界を匠の技で支える「職人特集」。第11回は、クルマの生産現場に欠かせない大型原動力設備の補修を自らの手で行う「設備保全の匠」に話を聞く

3DプリンターやAIをはじめとするテクノロジーの進化に注目が集まる現代。だが、クルマづくりの現場では今もなお多数の「手仕事」が生かされている。
トヨタイムズでは、自動車業界を匠の技能で支える「職人」にスポットライトを当て、日本の「モノづくり」の真髄に迫る「日本のクルマづくりを支える職人たち」を特集する。
今回はトヨタの生産インフラを支える「設備保全の匠」彦田浩俊(ひこた ひろとし)の前編をお届けする。
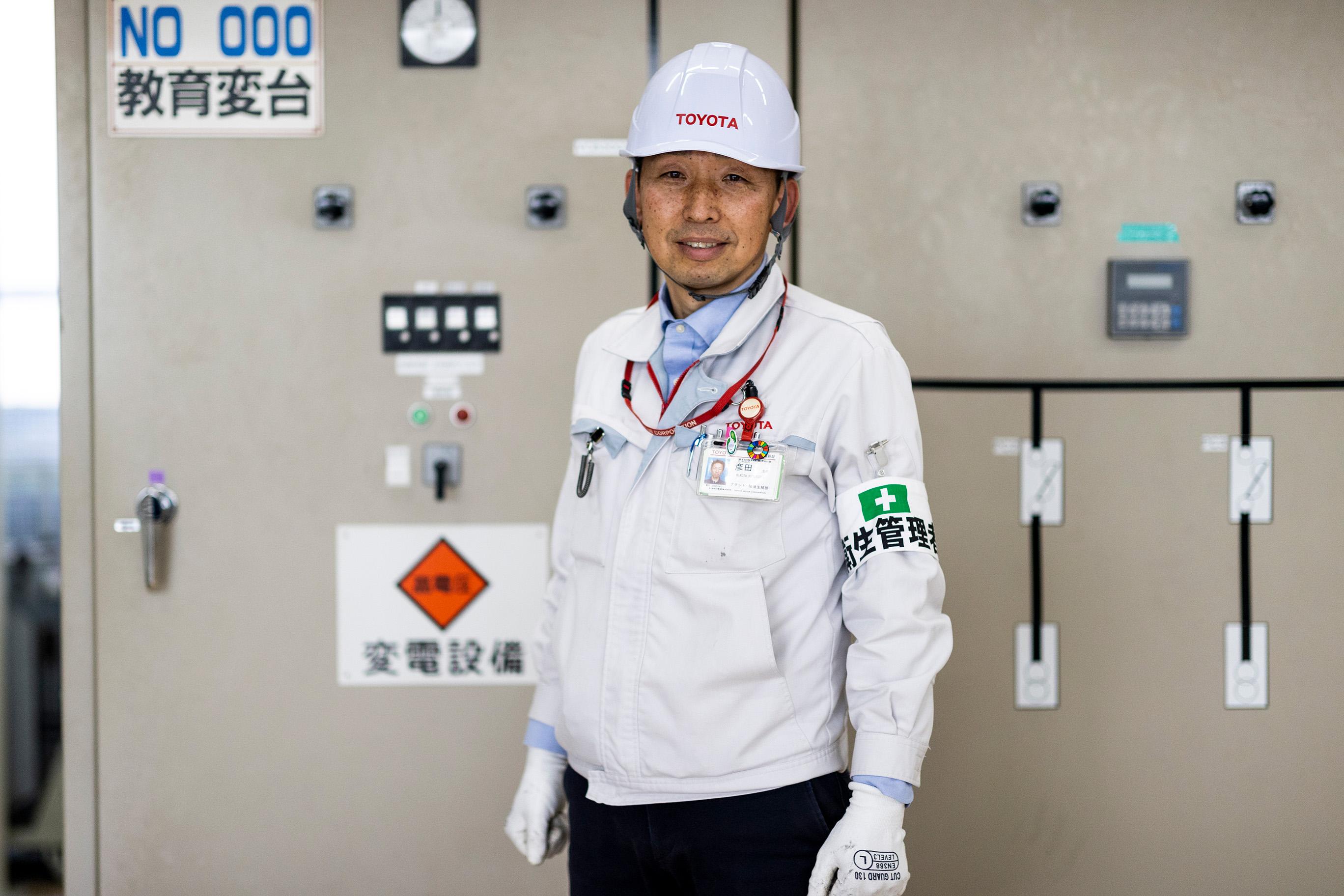
第11回 工場やオフィスに安定したエネルギーを供給する「設備保全の匠」 彦田浩俊
トヨタ自動車 プラント・環境技術部 原動力センター 原動力支援課 課長
クルマの生産を支える「原動力設備」
彦田の所属するプラント・環境技術部、通称PE部は、トヨタの国内外の工場やオフィスビル、社宅や寮なども含む福利厚生施設の計画、設計から建設、さらにその保守や管理を行う部署だ。
トヨタのクルマづくりのメインステージはもちろん工場だ。愛知県豊田市のトヨタ自動車本社工場とその周辺に8つ、愛知県内には11の自社工場があり、数多の工作機械や、製造スタッフが働きやすい環境を整える空調機器、照明機器などの設備が24時間休みなく稼働している。また、その周辺にはオフィスビルや社宅、寮などもある。
工場はもちろん、オフィスビルや寮にも不可欠なのが、原動力となるエネルギー。彦田の所属する原動力センターは、電力会社や石油会社から電力、燃料などの一次エネルギーを受け入れ、工場やオフィスビルなどが必要とする電圧の電力や蒸気、冷水や温水、圧縮空気などの二次エネルギーに変換し、安定的に供給する部署。
PE部の中には、この11の工場と本社、本社地区にあるビルや社宅、寮などに二次エネルギーを供給している5つの「動力課」があり、この動力課を支援するのが、彦田が所属する「原動力支援課」だ。彦田はその原動力センター 原動力支援課100人を率いている。
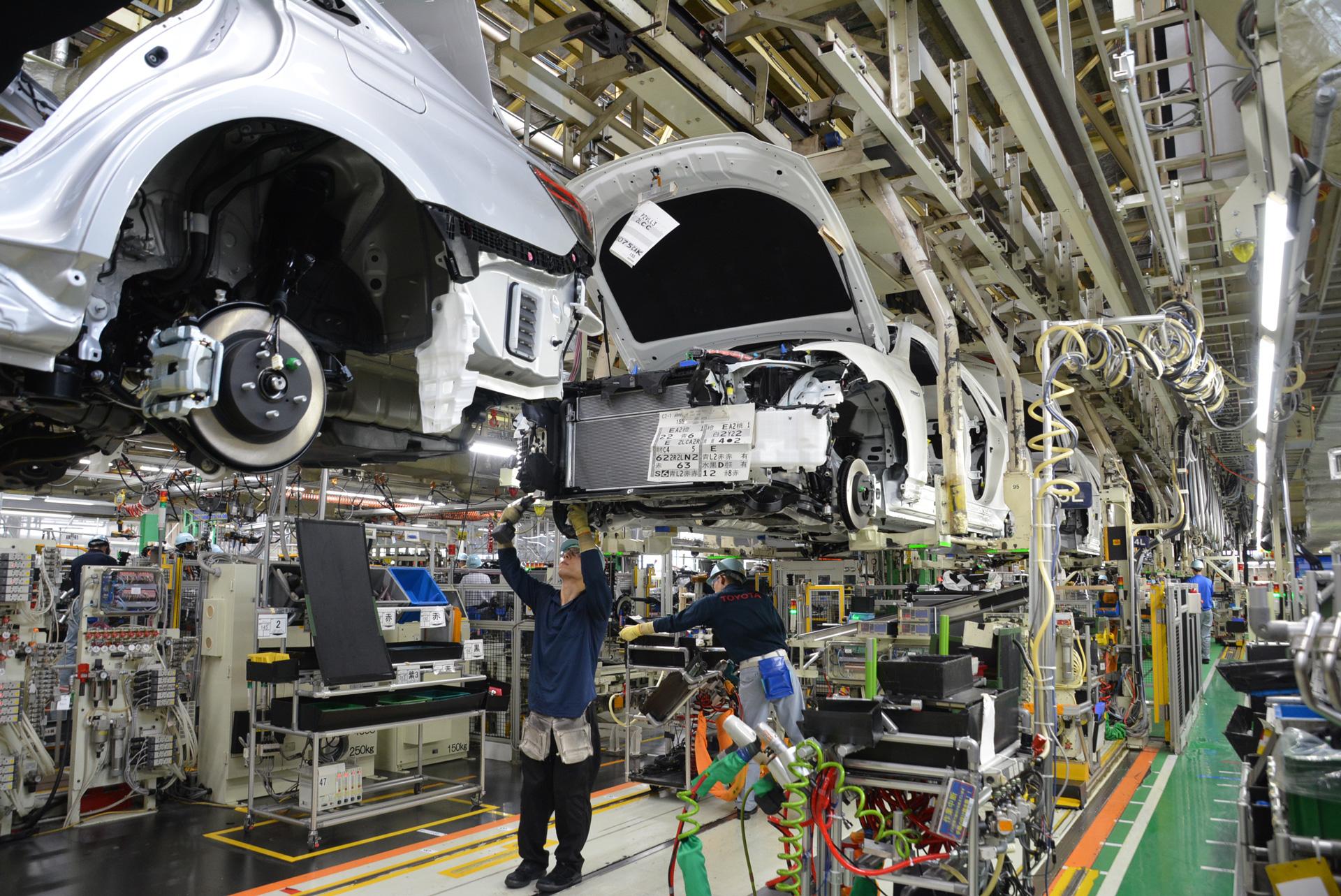
動力課は工場と同様に24時間、8時間ごとの3交替制で原動力設備の運転管理を行っている。彦田の率いる原動力支援課は、この原動力設備の整備・保全を行うのがもっとも大切な業務だ。常に設備の状態を監視し、問題が起きないように予防しつつ、故障などのトラブルに迅速に対処する。現在、100人のメンバーが日夜業務に携わっている。
彦田
私たちは”縁の下の力持ち”。工場の生産現場に安定したエネルギーを供給することが仕事です。それができないと、クルマの生産が滞ったり、現場の安全が損なわれたり、トラブルによっては、工場全体の稼働停止や重大な事故などを招き、お客様に車を届けるのが遅れ多大な迷惑を掛けてしまいます。
とはいえ、原動力設備もやはり機械。機械は使えば使うほど劣化するし、部品には寿命がある。壊れてから直していては時間も費用もかかる。最善の対策とは何か。設備保全を担うエンジニアとして、彦田は入社以来この課題の解決に取り組んできた。
何よりも工作が好きな少年
彦田浩俊は1967年1月、名古屋市生まれ。高校の機械科を卒業して1985年にトヨタ自動車に入社。以来、現在のプラント・環境技術部に所属し、設備保全一筋に取り組んできた。
彦田
昔から工作が大好きな子どもで、実家で父が椅子をつくっていたので、家にある材料を使って、小学校の夏休みの工作に1カ月間かけてディレクターズチェアをつくったりしていましたね。
トヨタ自動車に興味を持ったのは、子どもの頃に工場見学をしたときにいろいろ興味を持ったからだという。
彦田
クルマの生産ラインそのものより、作業者が働きやすい姿勢にする為の工夫された設備の方に興味を持ちましたね。トヨタを第一志望にしたのは、クルマづくりに関わりたいということもありました。モノづくりが好きなので、仲間と一緒にキャタピラを使って「階段を登ることができる車イス」をつくって、社内の「アイデアオリンピック」で表彰されたこともあります。
そんな彦田が最初に配属されたのは、当時の施設環境部 動力課(現在の第5動力課)。社宅や寮の電気設備や機械の保全が仕事だった。
彦田
機械科を出たのに、仕事は電気科のものでした。でも、どんな会社でも入社してみないと、どんな部署に配属されるか分かりません。その頃から「自分で技能を身に付けて、トヨタ以外でも食っていけるプロにならなければ」という意識を持っていました。そんな想いもあって、電気工事や配管工事、いろいろな修理を外部の業者だけに頼るのではなく、自分たちでも手掛けていました。
そして入社4年目の1989年、彦田に飛躍の時がやってくる。現在の職場、原動力支援課に異動して、全社の原動力設備の設備診断を担当することになったのだ。
前述の通り、原動力設備の不具合は、クルマの生産現場にとって大問題だ。ごくわずかな時間でも生産ラインが止まれば、その損失は莫大な金額になる、またトヨタの車を購入して頂いたお客様を待たせることになる。だから機械は可能な限り止めずに稼働させたいし、止めなければならない場合は、できるだけ短時間に済ませたい。
事後保全から予防保全、予知保全へ
彦田が原動力支援課に異動した当時、設備保全の技術は大きく進化する変革期にあった。
設備保全の技術は時代とともに進化してきた。最初に行われていたのが、設備にトラブルが起きたら修理する「ブレイクダウン・メンテナンス」という手法だ。この場合、修理に要する時間をどれだけ短縮できるかが大切になる。

だが故障が起きてから対処するのでは、どうしても損失が大きい。そこで次に導入されたのが「期間を決めて設備を止め、定期的に部品交換や整備を行う」という、予防的な考え方に基づいた「タイムベース・メンテナンス」だ。
とはいえ、設備を止めるのは、やはり損失につながる。センサーなどを用いて設備の状態を常時監視して、できるだけ止めずに整備し、どうしても止める必要があるときだけ、短時間で効率良く修理する「コンディションベース・メンテナンス(状態監視保全)」という考え方が導入され始めた時期に、彦田は原動力支援課に異動したのだ。
そのためには、①日常点検、簡易診断を行って、②トラブルの傾向をつかみ(傾向管理)、必要に応じて③精密診断を行い、すみやかに④オーバホールや定期整備を実施するという仕事のやり方が必要になる。
彦田
故障が起きたら真因を徹底的に究明して、同じことが起きないようにする。そのためには、その機械設備がどんな仕組みでどのように動いているのか、原理原則を理解していなければダメなんです。ただ当時は「仕事は盗んで覚えるもの」という時代でしたね。
自分で勉強している彦田を見て、先輩たちは初めてヒントやアドバイスをくれた。

彦田
コンディションベース・メンテナスでは、憶測ではなくデータからものを考えて設備保全を行うことが大切になります。ただ、この新しいやり方がすんなり導入できたわけではありません。データ解析に時間をかけていると、現場からは「診断しても設備は直らん」と言われたり、「報告書が難しい」と言われたり、データを示しても「本当に修理が必要なのか?」と納得してもらえなかったり……そんな状況でした。
彦田はこうした壁を、研鑽による知識や技能の向上、トラブルを実験で再現してみたりすることなど、地道な努力で一つひとつ乗り越えていった。
彦田
理解してもらえないたびに「なにくそ!」と思って、それが原動力になりましたね。
設備整備の内製化に挑戦
1997年、さらに新しい挑戦に挑んだ。従来は外部の設備業者に任せていた大型設備の補修や修理を社内で行うことだ。

彦田
大型の原動力設備は、診断して不具合が判明したら、仕入先(設備機器メーカー)に修理を依頼してきました。でも、それではどうしても修理完了までに時間がかかってしまいます。そのために、自分でもさまざまな技能資格や国家資格を取得して、大型の原動力設備でも私たち自身で診断し、直せるようにしました。
取材時には、彦田は自分と同様にさまざまな技能資格、国家資格を持つ部下の伊藤弘樹とともに、高圧ケーブルの診断と補修の実際を実演してくれた。

彦田
トヨタの工場には中部電力から77,000又は154,000ボルトという特別高圧の電力が送電線を通じて供給されています。これを工場の建物にある変圧器で、工作機械に最適な電圧に落として供給します。ただ高圧ケーブルは浸水すると劣化しやすく、たとえば絶縁層にわずかに水分が入っただけで「水トリー」と呼ばれる絶縁不良に陥るショートが発生し、危険な事故が起きかねません。
工場では多くの加工機械が電気で動いていていますから、事故が起こると多大な生産被害が出てしまいます。

高圧ケーブルの補修では、漏電を検出する装置を用いて異常を検知。水トリーの存在を確認できたら、すみやかにその位置を特定し、電工ナイフなどを使って該当部分を取り除き、ハンダなどを使って補修、さらに電工テープを巻くなどして再びトラブルが起こらないように処置する。ちなみに、この作業には電気工事士という国家資格と技能が必要だ。
彦田は自ら、その技能を実演してくれた。片刃にカスタマイズした電工ナイフを持ち水トリーの部分を切除。またハンダとハンダごてを使ってこの部分を修復する。その後、2種類の電工テープをテープ幅の半分ずつ重ねながら、丁寧に巻いていく。


彦田
高圧ケーブルには、もし触れてしまったら即死するほどの高電圧が掛かって電流が流れています。それに、配電ボックスの中は狭いので、寝転がって作業することもあります。このテープを巻く作業にも独自のノウハウがあるんです。
修復を終えた高圧ケーブルは一定時間、高電圧をかけて必要な絶縁性能が確保されているかを確認し、作業は終了となる。
彦田が率いる原動力支援課のメンバーは、問題が起きた高圧ケーブルと、問題のない高圧ケーブルの絶縁測定(測定機器を使った絶縁性能の診断)もデモンストレーションしてくれた。こうした診断も含めて、原動力支援課は自分たちだけで行える体制を整えているのだ。
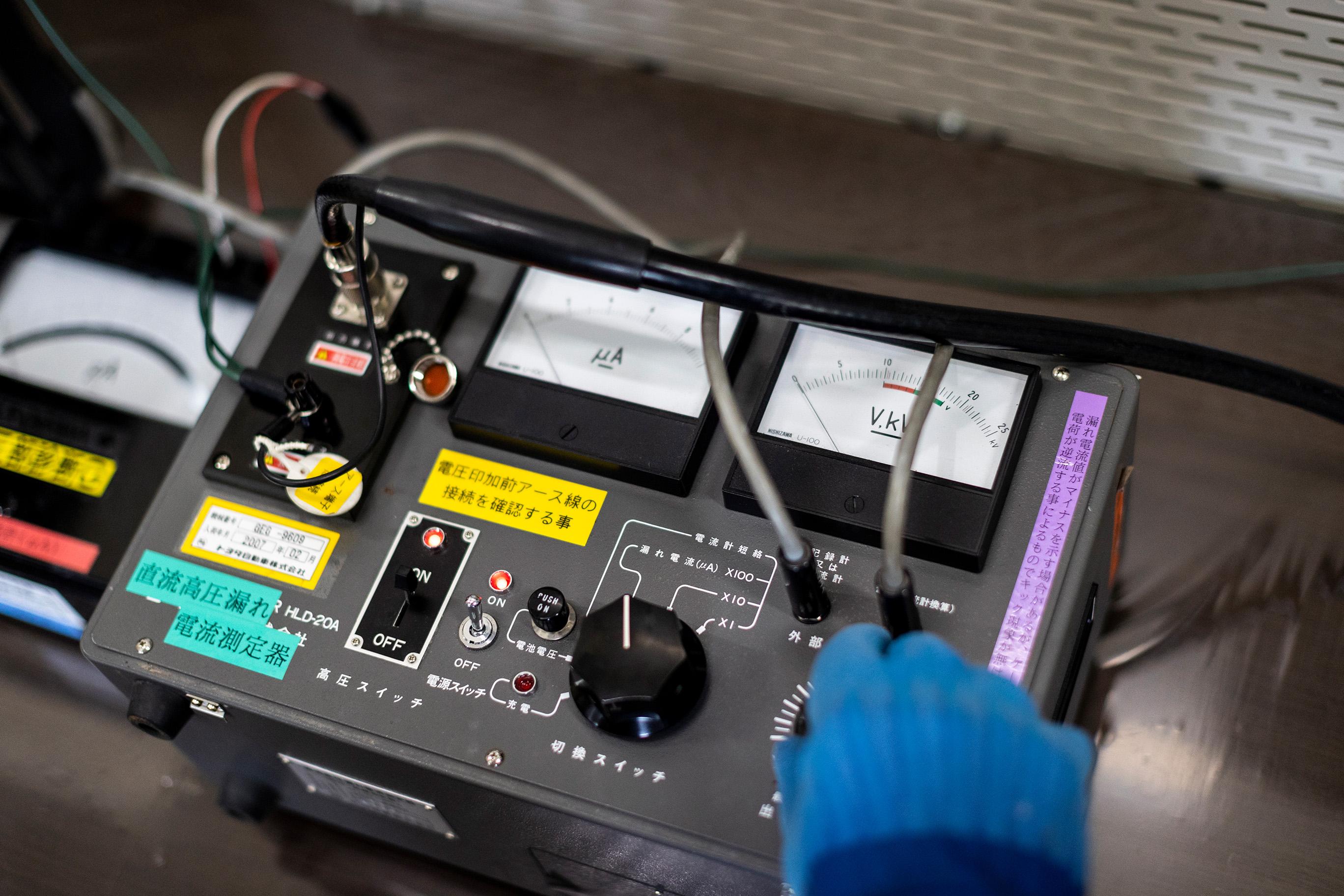
彦田
この内製整備をスタートさせたのは15年前から。上司から「やりなさい」と言われて始めたのではなくて、私たち現場のメンバーが「改善」の一環として行ったものです。今ではほとんどの原動力設備の補修を内部で行えるようになりました。また自分たちで補修したことで、社内の設備の施工基準を、事故が起こりにくいものに見直すこともできました。
彦田は今、原動力設備の管理・保全に加え、災害時の工場設備の復旧対応や、災害発生時の社外のレスキュー活動と、その業務を担う後継人材の育成に取り組んでいる。
後編ではその災害復旧への取り組み、災害発生時の社外への原動力レスキュー隊としての活動、さらに未来に向けての人財育成についてお伝えする。
(文・渋谷 康人、写真・張 宇麒)