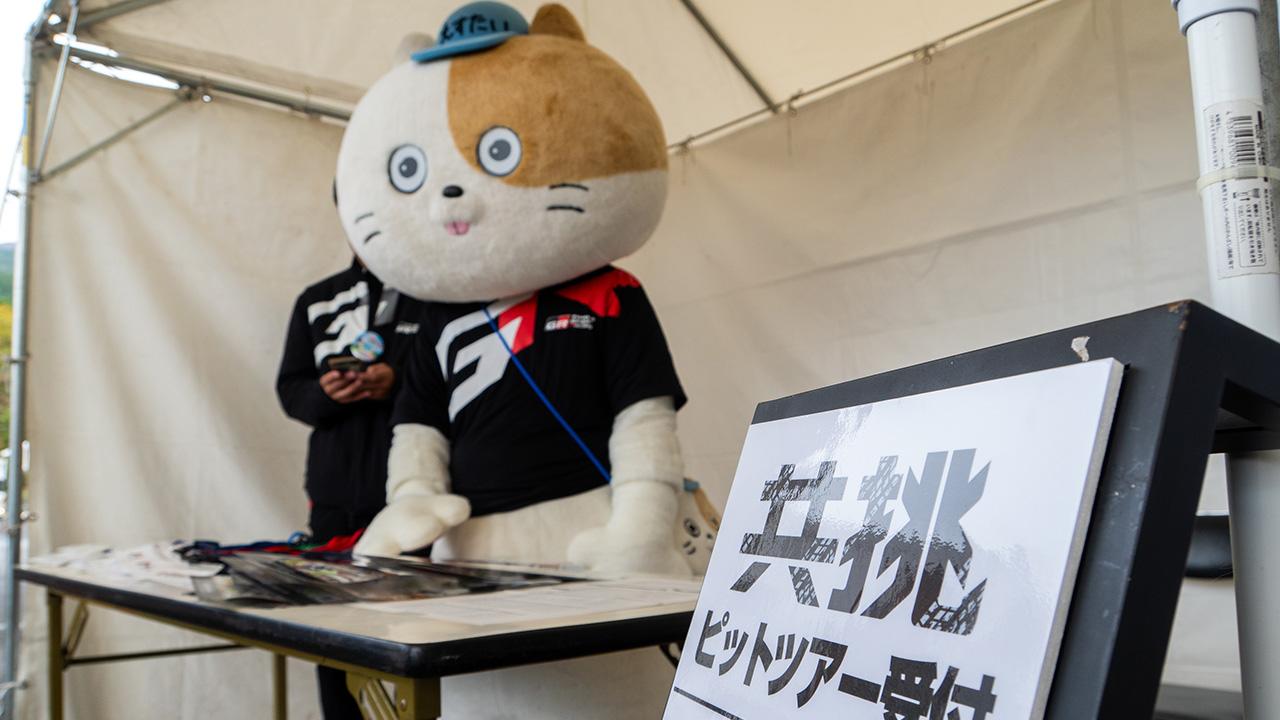
This season, the number of like-minded companies working to create a carbon-neutral society continued to grow through Super Taikyu. We caught up with some of those enjoying themselves while earnestly pursuing carbon neutrality.
Karts offer a taste of hydrogen and carbon-neutral fuels
The event space also featured racing karts powered by hydrogen and carbon-neutral fuel, unveiled for the first time. GR Vehicle Development Division Project General Manager Naoaki Ito explained their purpose.
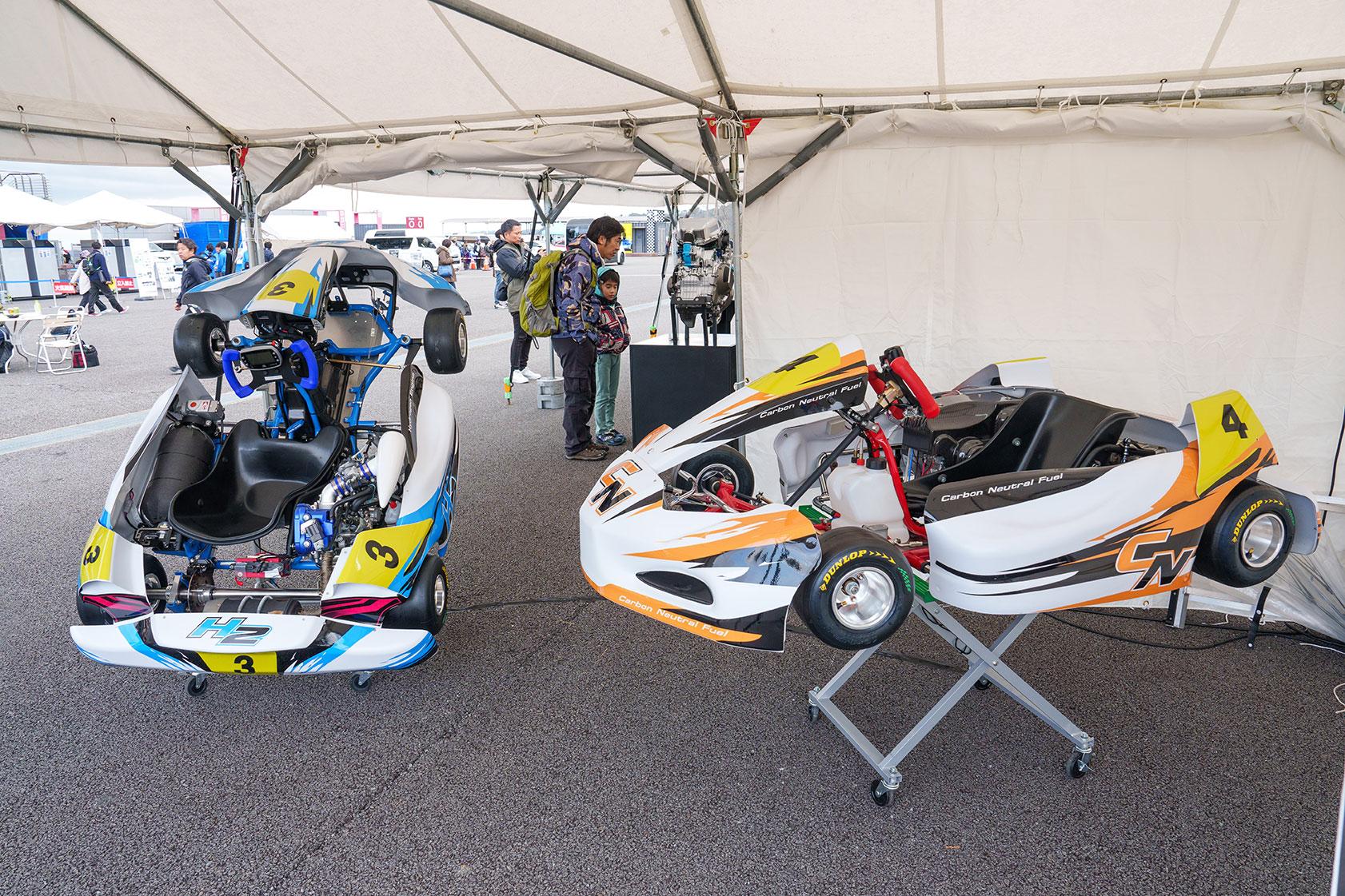
Project General Manager Ito
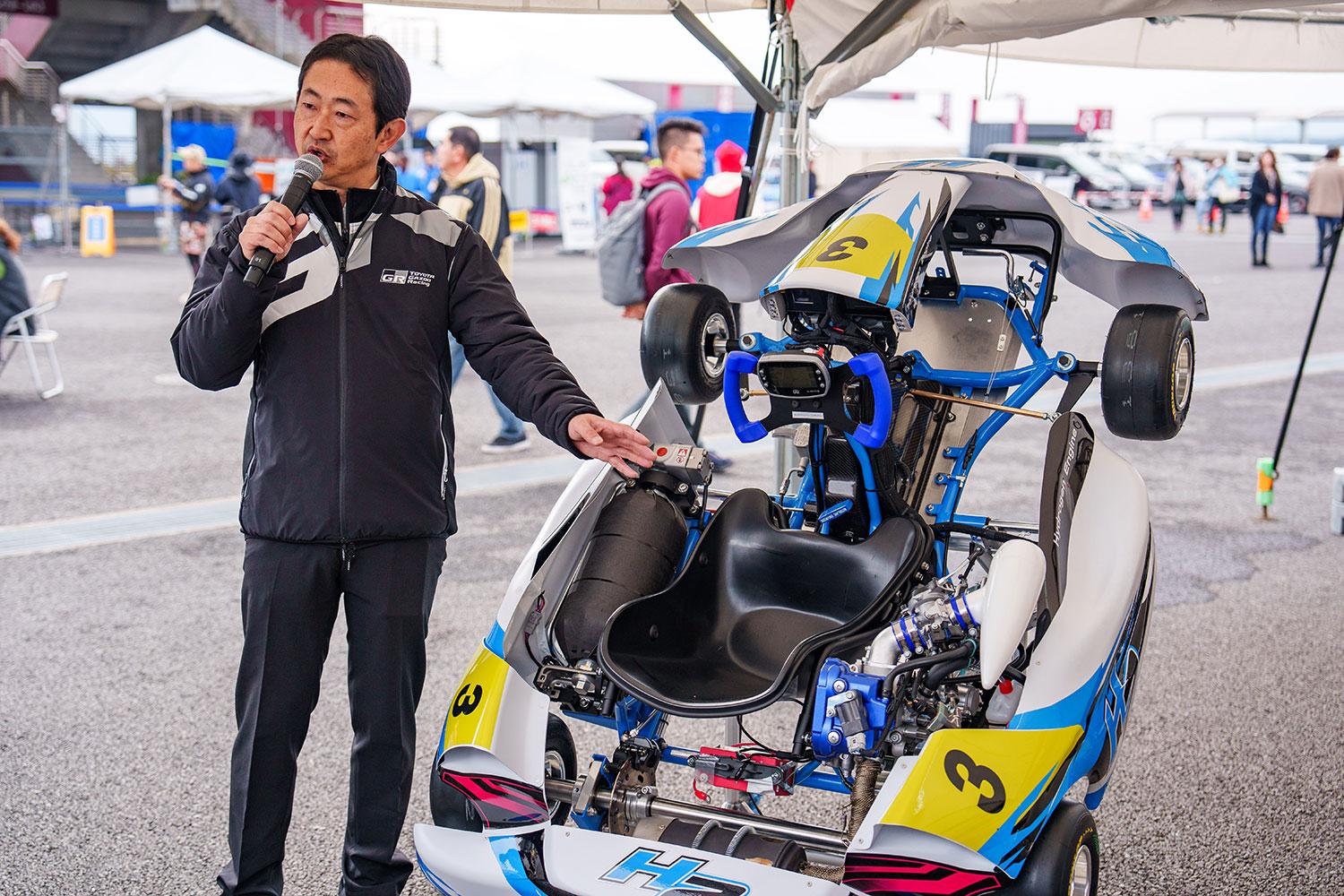
Although you have seen the hydrogen-powered Corolla (#32) and our carbon-neutral fuel GR86 (#28) in Super Taikyu, we wanted to allow regular drivers to try these technologies for themselves. That’s the idea behind these racing karts.
We will bring them to various events in the future and would love everyone to get behind the wheel and experience how hydrogen engines and carbon-neutral fuels really feel.
In terms of the concept, the hydrogen-powered karts are tuned for higher-spec performance, while the carbon-neutral fuel version is geared more towards a level that even children can drive.
The engine was built with assistance from Yamaha Motor, directly incorporating technology from the H2 Corolla. We even use the same injectors as in the Corolla.
The carbon-neutral fuel karts are equipped with Yamaha's MZ engine and can run on either gasoline or carbon-neutral fuel.
We’ve kept these at low power, so they should also serve as a teaching tool for children to learn about carbon-neutral fuel.
During November’s Rally Japan 2023, these karts were also handed over to racing drivers for a demo run at Toyota Stadium.
The new initiatives showcased at Fuji International Speedway don’t end there.
Reusing hydrogen tank scraps as building materials
Also among the displays was a demonstration of the “,” jointly developed by Toyota and builder Obayashi Corporation to promote a circular economy.
Hydrogen tanks for vehicles like the Mirai are made with carbon fiber-reinforced polymers (CFRP). Despite efforts to minimize waste, the manufacturing process inevitably produces scraps and remnants.
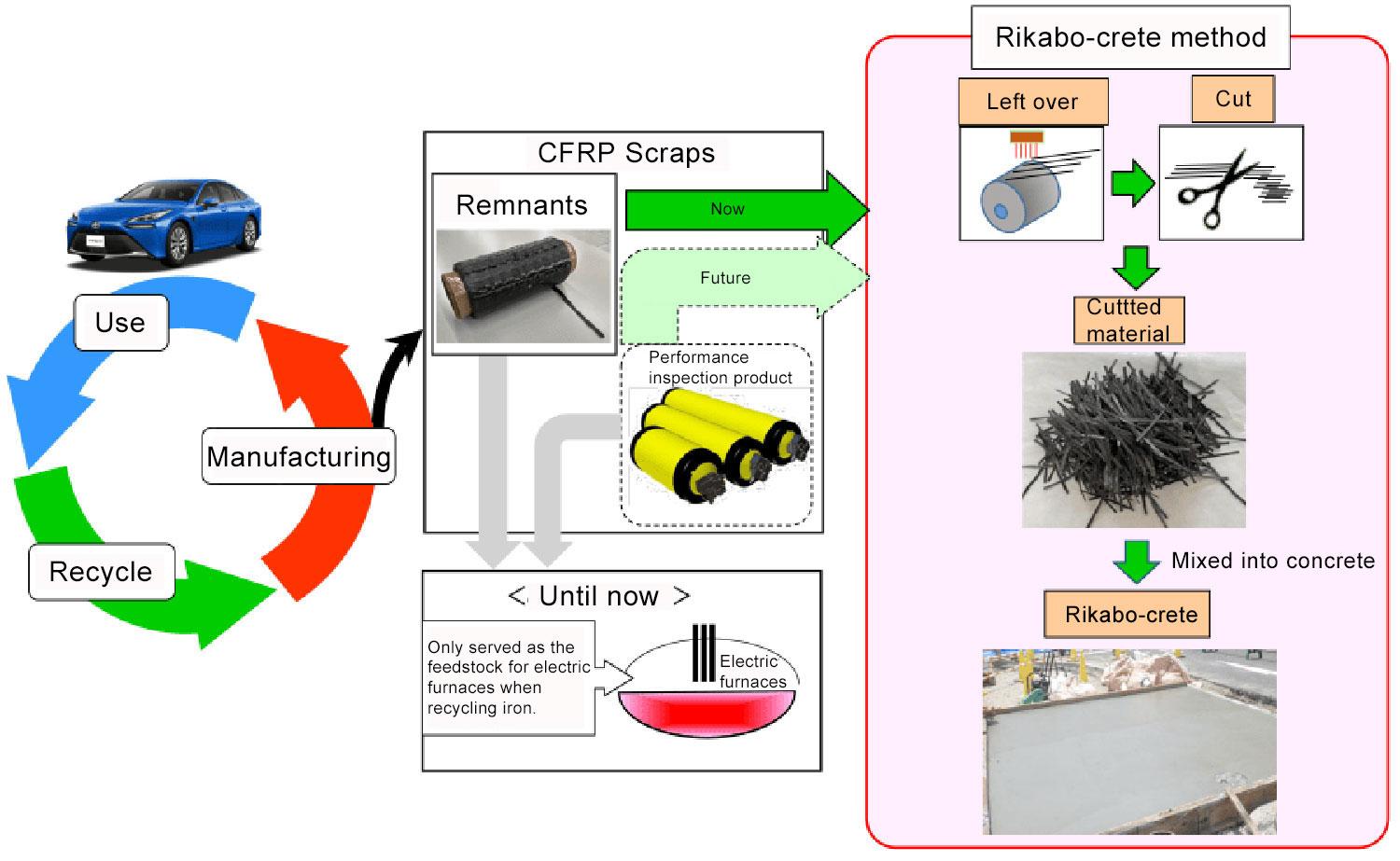
And since these scraps are surface coated with a hardening resin, they have proved difficult to reuse while retaining the properties of CFRP. Until now, they have only served as the feedstock for electric furnaces when recycling iron.
A new way of utilizing these materials is the Rikabo-crete method developed by Obayashi and Toyota. With unique thermal processing, the two companies devised a technology for stripping CFRP from the hardened surface layer in remnants left over after tank fabrication.
The CFRP can be continuously stripped without impacting its properties, allowing it to be easily processed into short fibers for reinforcing concrete.
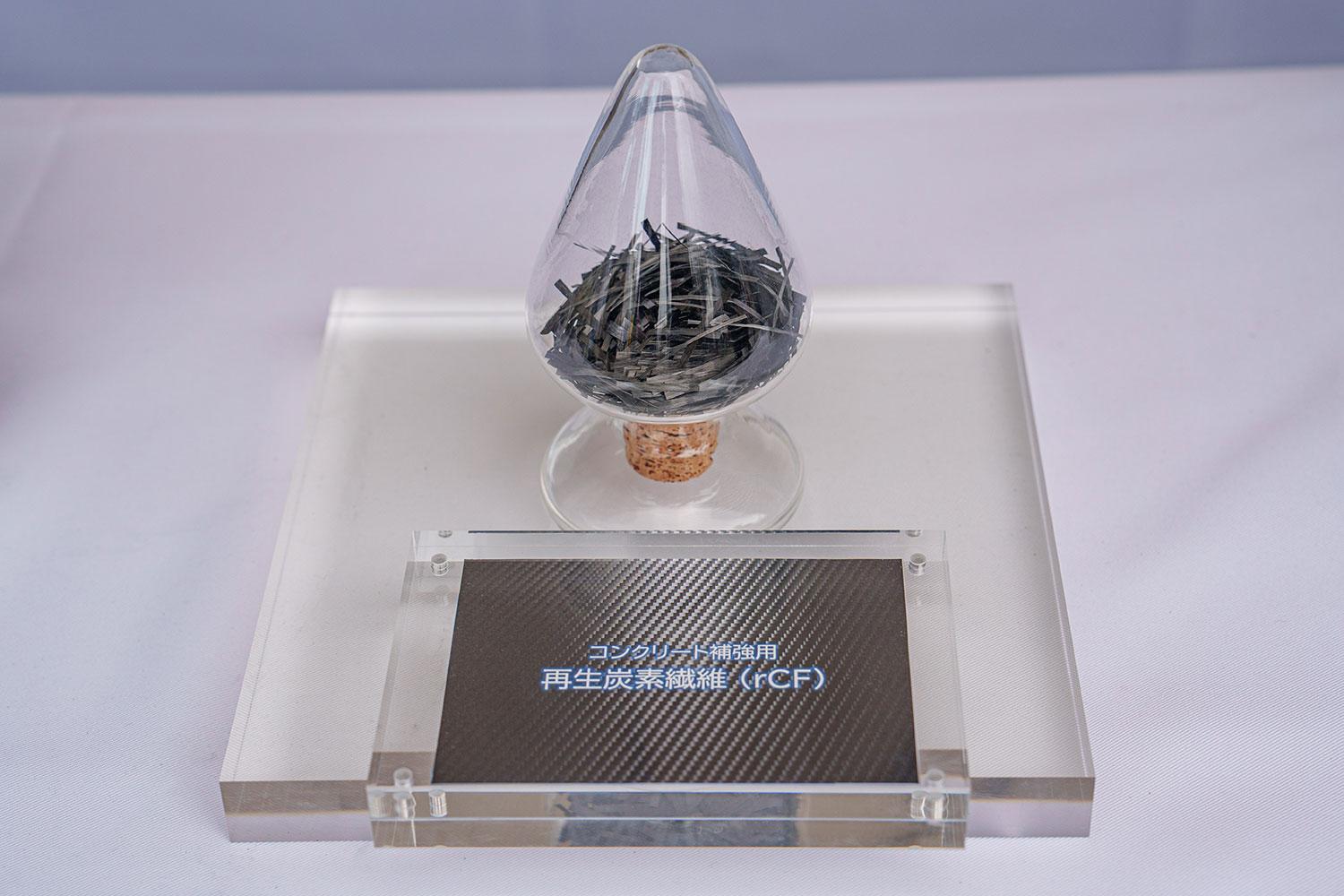
Using CFRP in this way also delivers performance at least on par with the polypropylene fibers conventionally mixed into concrete, while requiring only two-thirds as much to be added. This reduces CO2 emissions to one-fifteenth that of new carbon fiber and one-ninth compared to ordinary rebars.
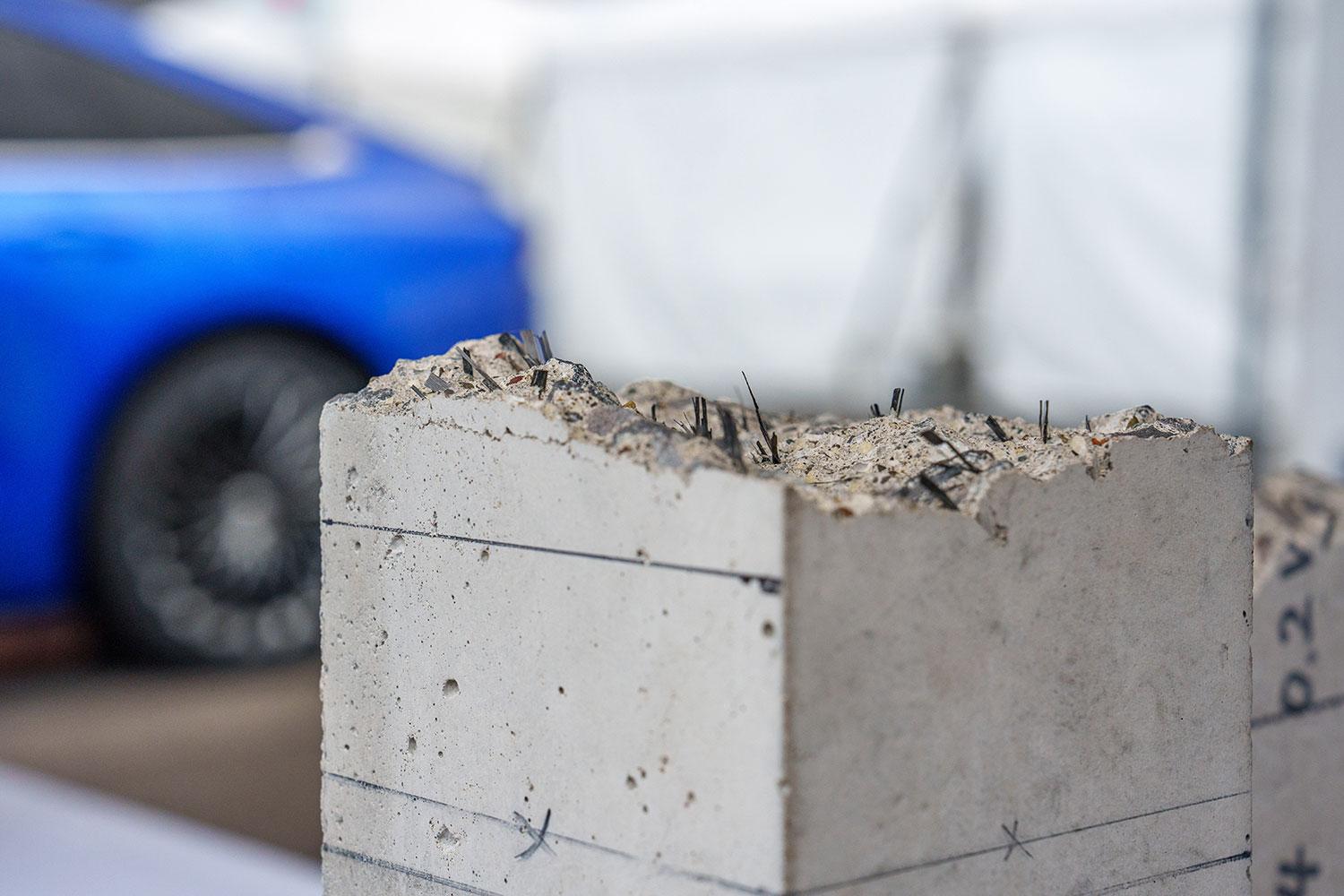
What’s more, whereas rebars can end up destroying the concrete by corroding and expanding over time, CFRP does not corrode, potentially offering greater durability.