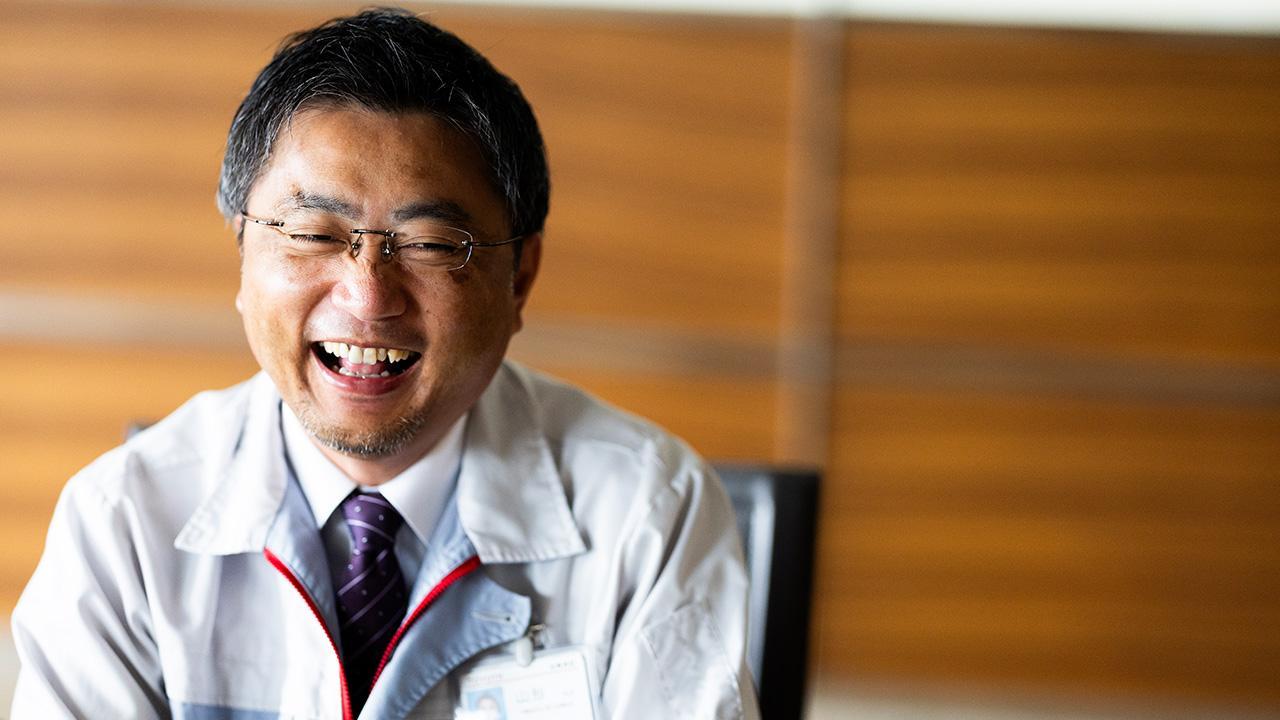
Automotive analyst Shinya Yamamoto has been going one-on-one with this year's trio of newly appointed presidents. In this final interview, Hydrogen Factory President Mitsumasa Yamagata delves into his life as a "Toyota man."
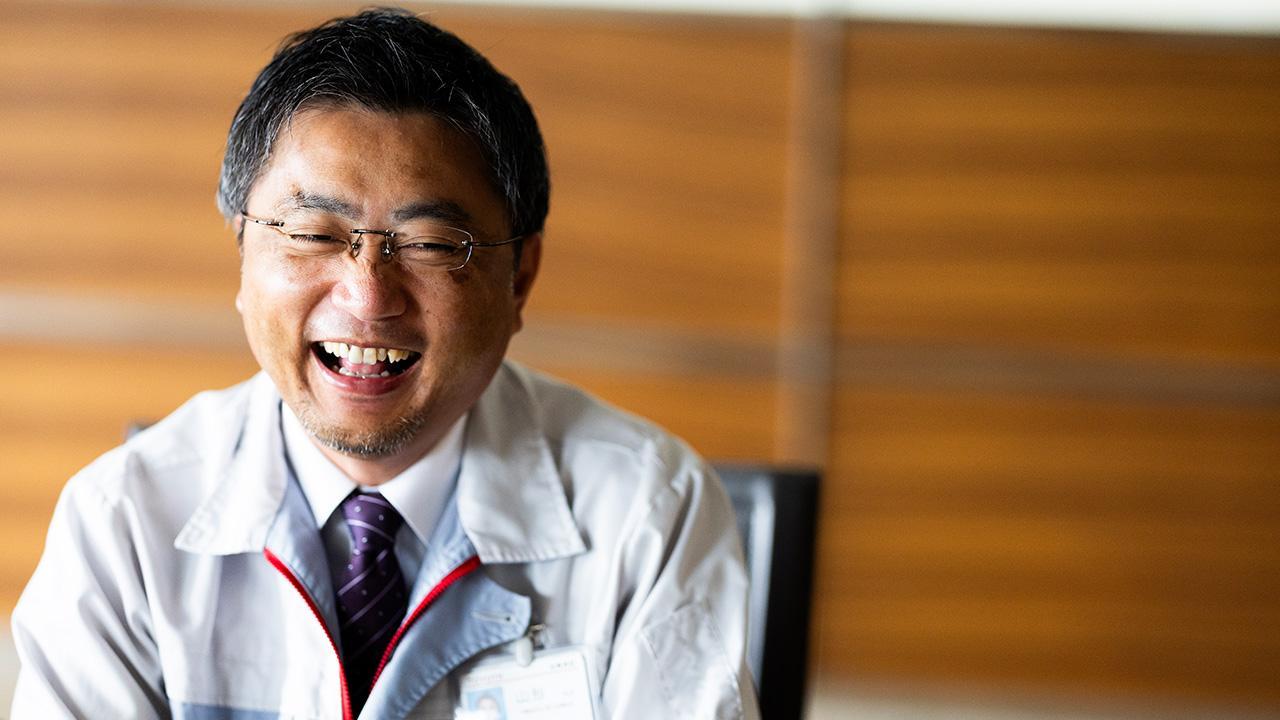
For the final part of this interview series, automotive analyst Shinya Yamamoto speaks with Mitsumasa Yamagata, President of the Hydrogen Factory which launched in July.
Like the previous talks with President Koji Sato and BEV Factory President Takero Kato, this conversation delved into Yamagata’s career, personality, and passion for cars.
Having spent his time at Toyota immersed in engines, how did Yamagata come to oversee the company’s hydrogen unit? As the head of the new organization, what possibilities can he see for hydrogen?
While all three presidents have taken very different career paths, Yamamoto’s interviews also highlighted some common threads.
Lessons from the genba: “Cars are made from behind the wheel”
(Text by Shinya Yamamoto)
Yamagata’s interest in joining an automobile company was sparked in his final year of high school, while watching the pit crews during a broadcast of the 24 Hours of Le Mans.
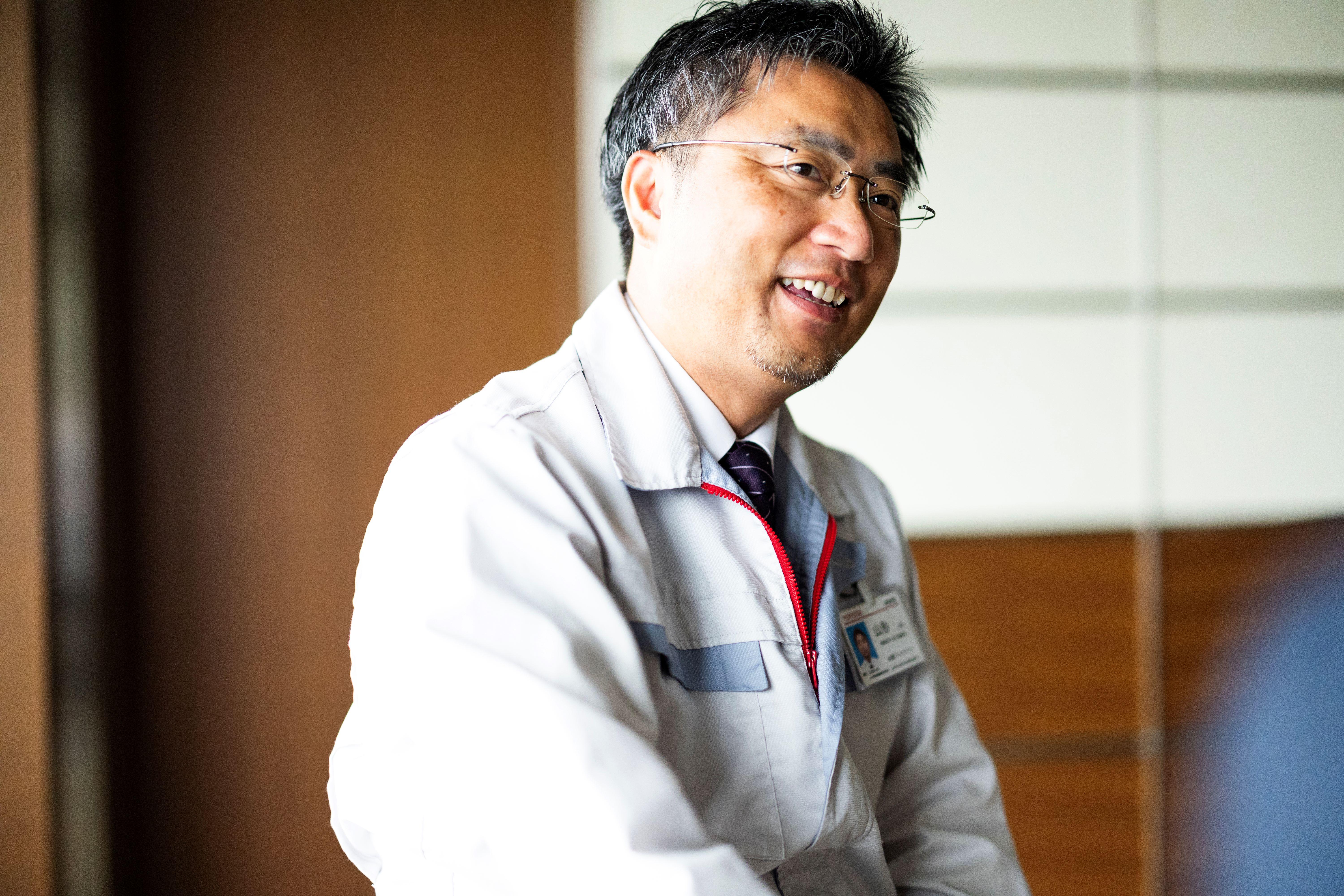
After the race, as I watched them hugging each other and crying with joy, I realized that although I couldn’t be a racer, these really cool jobs existed on the production side. I wanted to be part of that world.
I developed engines all through university and graduate school. When it came time to look for a job, I wanted to join an automobile manufacturer, but only three Japanese companies were competing in Le Mans: Toyota, Nissan, and Mazda.
I vaguely hoped to get into one of them, and as fate would have it, I ended up at Toyota.
Yamagata’s wishes came true when he was posted to the Engine Design Division. His first job, however, did not involve the engine itself but designing the mounting (engine mounts, radiators, etc.).
Back then, that work was handled by the engine team, but now it has been moved over to vehicle design.
In that position, I rarely worked with engine personnel despite being in the same division. Instead, I spent time with people on the evaluation and vehicle side, driving cars and tuning engine mounts.
It was a shock at first, but ultimately, it was for the best.
Being in a section of the engine division that worked with other departments allowed Yamagata to immediately connect with people in different disciplines.
It’s commonly said that in any company, the engine division tends to throw its weight around (laughs). Against this backdrop, I spent more time with the vehicle design people.
At the time, we were responsible for many models, and I looked after about ten myself. I spent my days driving various cars and testing things like idling vibration and ride quality. The evaluation guys took me under their wing and taught me that “cars are made by getting behind the wheel.”
The first component I designed was a radiator bracket for the Vista Ardeo.
With little idea of how things were done, I remember calculating the section modulus and preparing the drawings, but clearly, I didn’t do a great job because the shape was changed before it reached mass production (laughs).
A big job out of the blue
On the other side of this apprenticeship, Yamagata at last found himself working on actual engines. From there, he began designing and planning new engines.
In those days, Toyota was growing fast and there weren’t enough engine personnel, so I was suddenly reassigned. My first project was the three-cylinder KR engine.
We started out with four people, two from Daihatsu and two from Toyota. I was in charge of the cylinder head, air intake, and exhaust system.
Just two or three months after moving from mounting design, I was put to work on the engine itself—and the all-important cylinder head, no less—and I remember being in disarray during development.
It didn’t take long for Yamagata to get into the line of work that had drawn him to Toyota.

In my mind, the cylinder head is the most challenging part of an engine, and I imagined that only the most seasoned veterans eventually reached this point.
However, my supervisor at the Engine Design Division, Kohei Hori laid the matter to rest by telling me off for outdated thinking.
“I’ll teach you,” he told me. Outside of work time on Saturdays, I made drawings under his instruction.
One time, when I came to him because I was having trouble with the shape of an intake port, he replied, “See those materials over there? Look through them and draw it again, then come back to me.”
I spent the entire Saturday reading the materials and doing calculations, but by the time I was finished in the evening, Mr. Hori had already gone home.
I clearly remember thinking to myself as I worked: “Maybe he meant ‘come back to me on Monday...’” (laughs).
This tough love helped Yamagata complete the KR engine, which became part of various Toyota and Daihatsu models. Not only that, three years after launch, it was awarded International Engine of the Year.
That engine has enjoyed a long run and is still used in the Aygo (a Europe-only model). Never mind that I was practically an amateur when I developed it (laughs).
The origin of TNGA
Yamagata went on to be involved in various engines, from planning to launch. Then, around 2009, the time came to start thinking about the next generation.
In those days, the engine team did only engines, and the vehicle people worked only on the vehicle. But my experience in mounting design got me thinking, “Couldn’t we make the best engines by looking at the car as a whole?”
That’s when I received a request from above to get started on packaging for a new engine series. This meant simultaneously creating an entire engine lineup for all FF Toyotas.
Basically, Yamagata was entrusted with the preliminary work for what would become TNGA.
At that stage, Toyota’s transverse four-cylinder engines had a range of mounting angles and exhaust methods. I’m sure those on the vehicle production side were pretty fed up.
Unfortunately, our initial foray was shelved due to the financial crisis, leaving only a three-volume technical report in which I regrettably noted the missed potential.
Needless to say, those documents would prove very useful when TNGA development began in earnest.
Traditionally, we made good engines that reflected the character of their engineers.
I’m glad that we reached a conclusion that prioritized not just engine character but optimized overall vehicle packaging. I was thrilled that others picked up where we had left off.