
Collaborative efforts of the "Toyota City Model" have shown that combined skills of the medical professionals, government, and private sectors can make a great improvement in COVID-19 vaccination. Toyota has promoted continuous kaizen based on the philosophy of the Toyota Production System.

A familiar looking diagram
The COVID-19 vaccination program began in Japan in February. In Toyota City, home to Toyota’s head office, mass vaccinations for the elderly began on May 30.
There are a total of 18 vaccination venues in Toyota City, of which four are at facilities related to Toyota Motor Corporation. One of them is the welfare facility at Tsutsumi Plant, and hearing that Toyota is involved in smoothing the operation, the Toyota Times editorial team decided to visit the venue on the first day for vaccinations.
There, posted next to the entrance was something that at first glance appeared to be a map. A closer look showed that this map features such processes as “pre-examination form confirmation,” “registration,” and “vaccination,” all linked by arrows and showing “how many seconds” each process takes.
Any Toyota employee and probably any reader of Toyota Times would immediately guess that this “map” is a material and information flow diagram, a key “tool” of the Toyota Production System (TPS).

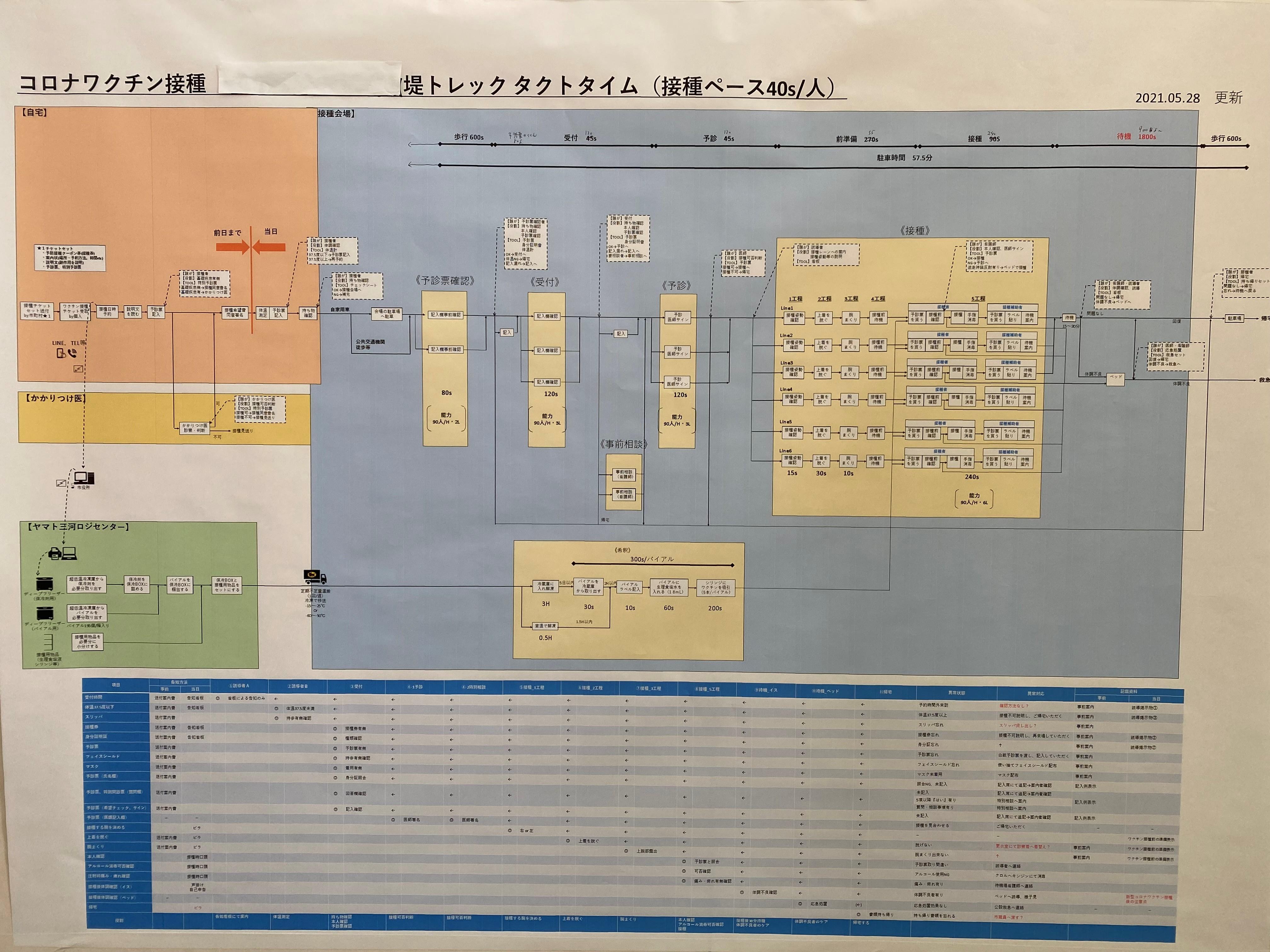
So why is it necessary to post the diagram at the entrance of a COVID-19 vaccination venue? It represents Toyota’s response to the government and medical professionals who have hoped to “provide local residents with safety and peace of mind as quickly as possible.”
Aiming to realize a layout that encourages people to receive their second dose
Hopes are high that the vaccine will be the ace that finally brings the pandemic under control. Since April, Toyota City has been working together with medical associations, Toyota and Yamato Transport Co., Ltd. (Yamato), to promote a “Toyota City Model” that realizes efficient operation of vaccination venues and safe transportation of vaccines.
While many local governments are engaging in vaccination programs centered around individual clinics, with a population of more than 420,000 and being the municipality with the largest total area in the prefecture, Toyota City needed to secure large-scale vaccination venues. The city approached Toyota about the possibility of using the various facilities that the company owns in the city.
Toyota has to date engaged in a diverse range of COVID-19 relief efforts around the world, including the production of masks and face shields, support for the production of medical protective gowns, and production and sale of foot-operated hand sanitizer dispenser “Shodoku Taishi” in Japan.
In response to the request from the city, Toyota made the decision not only to provide the venues , but also to dispatch its own industrial doctors and nurses for assistance. At the same time, the company also launched joint operations with the city and the medical association, dispatching staff involved in the setup and operation of venues to ensure that people could receive vaccinations safely, securely and efficiently. That is the reason why the material and information flow diagram, a key TPS tool, was posted at the entrance of the vaccination venue.
So what does it mean in specific terms to introduce TPS concepts in vaccination venues? A person central to the vaccination support effort is Nobuaki Miyajima, Project Manager at Toyota’s Operations Management Development Division. He explained as follows:
Miyajima
What we do is consider and arrange the various things related to vaccination venues, including parking spaces for people who come by car, the time it takes for vaccination, the personnel required, including doctors and other support staff, and other “necessary items and equipment for vaccination,” and decide just how many or how much of each specific thing is required. This is the way to determine “a basic unit” in TPS, and this “basic unit” can be applied to other venues.
The material and information flow diagram was then compiled based on the pre-determined “basic units” and reflected in the venue layout. However, until the venue went into operation all numbers had only been theoretical. The actual flow of vaccinations was assumed and countermeasures were put in place for any processes where there could be potential logjams.
A look at the simulation showed that at the reception where people present their vaccination ticket and pre-examination form there were likely to be many people at the reception desk who had forgotten something, or who had not filled in everything correctly. That is why a signboard was installed outside the venue, where people can confirm that they have what they need before entering, and also a space was set up separately from the reception desk, where people could fill in forms.
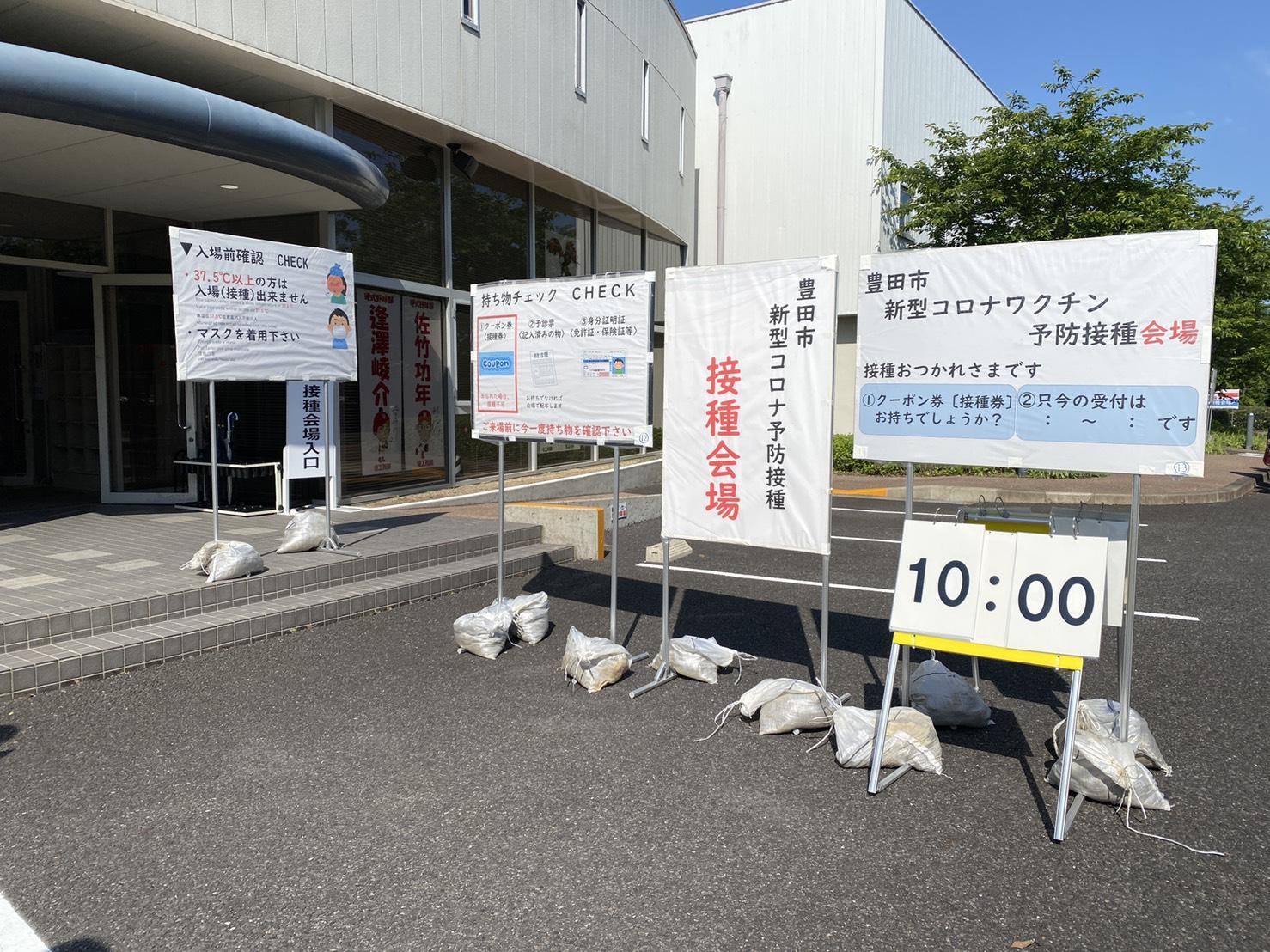

It also became apparent that the pre-examination by a doctor prior to vaccination creates a queue. Various preparations were therefore made to shorten waiting times and ensure that people could receive their vaccinations with peace of mind, including the advance distribution of Q&A sheets, which respond to frequently asked questions to doctors, such as, “Would I feel ill after vaccination?” or, “What effects does the vaccine have?”
One of the medical practitioners involved in the setup of the vaccination venues was Yasuhiro Osugi, Deputy Director of Toyota Kamo Medical Association. He had this to say about Toyota’s efforts to create vaccination venues:
Osugi
I gave various opinions on setting up the venues, but Toyota’s actions were above and beyond our approach of, “If we do this we should be okay.” They engaged in actual simulations and were constantly thinking about and confirming how to make processes better. It was truly a case of genchi genbutsu (going to the source to get the facts) in action.
Osugi has been a truly indispensable presence in Toyota’s COVID-19-related initiatives, including offering frequent opinions when the company was engaged in efforts to support production of medical protective gowns. The use of Toyota terminology like genchi genbutsu without even a second thought hints at the strength of the relationship.
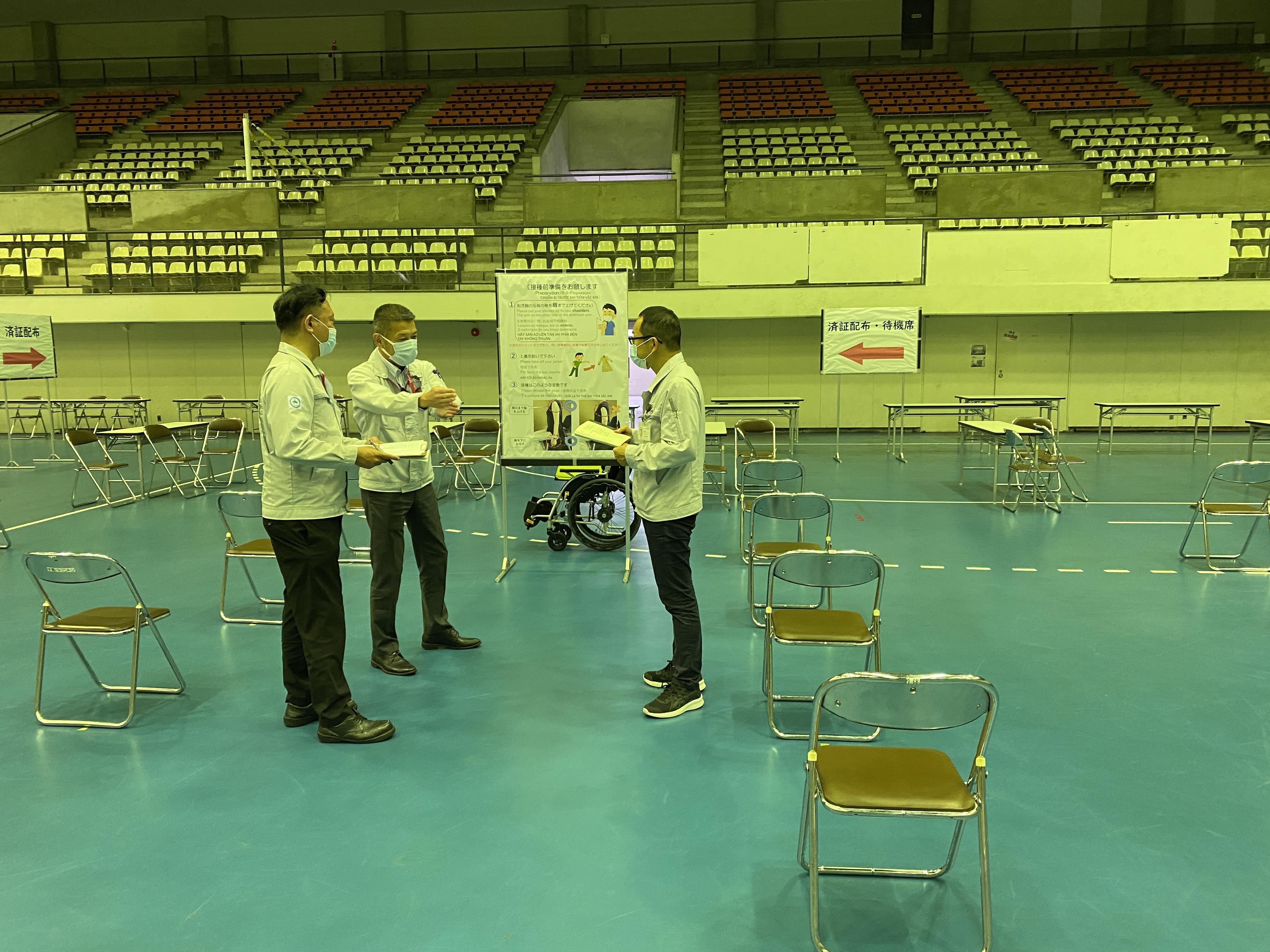
On the other hand, Miyajima emphasizes that creating the venue wasn’t simply a case of enhancing efficiency.
Miyajima
When you say “TPS,” people tend to think of it as “eliminating waste” or “enhancing efficiency,” but it’s not just about that.
Given the fear people have of COVID-19, what we want for people to think when they leave the venue is that they want to come back to the same venue to receive their second dose, as they received their vaccination smoothly without delay or inconvenience. This is the sense of safety and peace of mind that we are prioritizing when we arrange the venue layout.
Listening to this, what comes to mind is the comments made in an internal lecture given by President Akio Toyoda last year, on “Akio Toyoda’s View” of TPS. In those comments he had the following to say:
Akio Toyoda
Often at Toyota, TPS is considered the process of making things efficient, and you talk about changing the way of work as the purpose of applying it in that context. But I think the purpose should be to make someone’s work easier.
What are people worried about when they come to be vaccinated? How can such worries be eased? The way the people involved in the project are using their imaginations to the fullest extent every day as they try to solve each problem is certainly not something that could simply be described as “enhancing efficiency.”
Enabling medical professionals to focus on medical services
One of the essential elements to ensure safe and secure vaccinations is Yamato’s logistical operation that transports vaccines at ultra-low temperatures.
The vaccine being used in Toyota City is recommended to be stored at a temperature between -90℃ to -60℃. This means that for general logistics, large quantities of dry ice are used to maintain the required temperature range, but dry ice is itself a substance that requires various precautions in handling.
In response, what Yamato uses in transportation are ultra-low temperature ice and special cold storage boxes. This combination means that it is possible to maintain the recommended temperature range for a maximum of 30 hours.
Integrating transportation and storage in these cold storage boxes allows the delivery of vaccines to 140 vaccination venues (including individual venues) across Toyota City and store them at mass vaccination sites that are not equipped with refrigeration capacity. It also made it possible to take back unused vaccines, eliminating the risk of disposal.
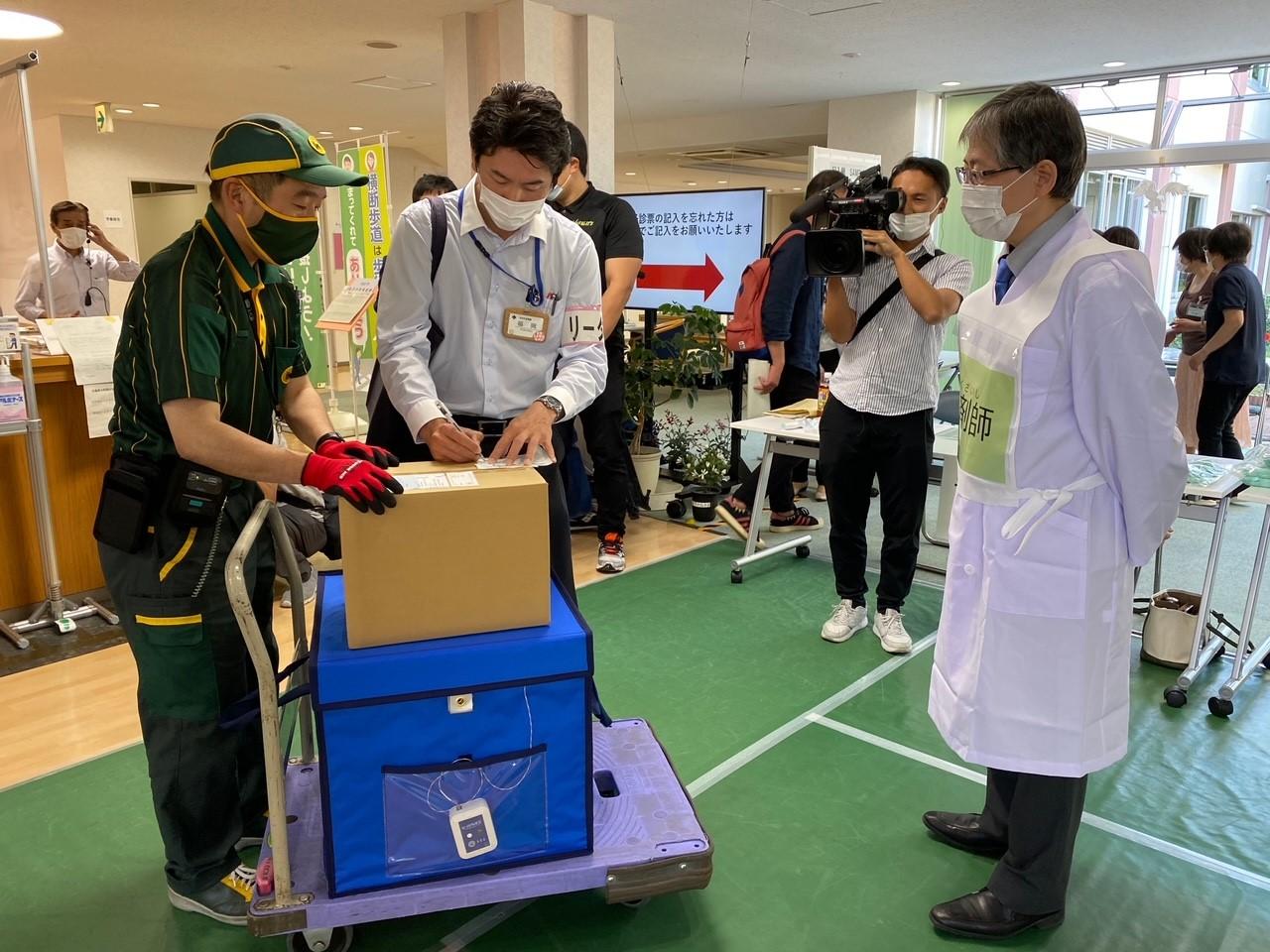
Masahiro Hayashi, General Manager of Sales Planning at the Global SCM Business Division of Yamato, which is spearheading this transportation scheme, spoke about his hopes for the project as follows.
Hayashi
Once the vaccines have been supplied by the central government to local governments, it is up to the local governments to manage their own vaccine deliveries, but it is impossible for local governments alone to control which medical institutions are supplied with the vaccine and when.
Neither can we place any further operational burdens on medical staff at hospitals, who are already under tremendous strain. To ensure that the medical professionals can focus all their energies on delivering the vaccine to people, we consider it to be our job to utilize our experience and capitalize on the results we have achieved to date in the transportation of pharmaceutical products.
In addition to the vaccine itself, equipment necessary for vaccination, such as saline solution for dilution and injection needles, are put together in sets at the distribution point before being shipped as another way of minimizing the burden on the recipients. That is how the Yamato transportation system works.
Another issue raised by the hospitals receiving the vaccines was that they had no idea when the vaccines would be delivered, nor whether they would arrive during standard medical consultation hours or on non-consultation days.
To respond to this issue, information about the medical institutions’ working days and operating hours when it is possible to receive deliveries was converted into data on the Yamato transportation management system and the creation of transportation plans made it clear in advance when vaccines would be arriving. This system also made it possible to change the arrival date and time up to three days before the planned delivery.
Hayashi
Vaccine transportation is a logistical operation, comprising pre-ordering, inventory management, transportation planning, and quality visualization. Yamato already had this system in place for its standard business operations, so we believe that in the field of safe and secure transportation technologies we are well positioned to contribute to efforts to bring COVID-19 under control.
Enabling medical professionals to focus on their primary mission of providing medical services—Yamato’s transportation technologies are another major pillar supporting Toyota City’s vaccination program.
Yamato’s transportation scheme and Toyota’s work to setup venues is almost the two sides of the same coin—the transporting and receiving sides at the vaccination venue—and cooperation is to be expanded to other local governments too.
“Try and see” as the first step to kaizen
There is another key company involved in these efforts. In order to produce the ultra-low temperature ice used in Yamoto’s transportation system, an ultra-low temperature freezer capable of freezing to -120℃ is needed. The company responsible for the development and production of these freezers is ADD Co., Ltd. (ADD), from Numazu in Shizuoka Prefecture. Toyota is also assisting with productivity improvements for this freezer.
ADD has 39 employees. Although small in scale, since its establishment in 2001, the company has built up a track record in specialized fields, including development, sales, repair and maintenance of semiconductor equipment. Looking back at the time when the support team from Toyota was first dispatched, company director Hiroto Shimoda laughs as he says, “There was no benefit in it for Toyota. I thought they must have a secret motive.”
Shimoda
However, I had seen the article in Toyota Times about Toyota’s support for medical protective gowns, and so I understood what Toyota was aiming to achieve, and when Toyota personnel actually arrived here I felt that we could talk to them on an equal footing, without any hierarchical worries. I was also eager to work together with them and absorb anything I could.
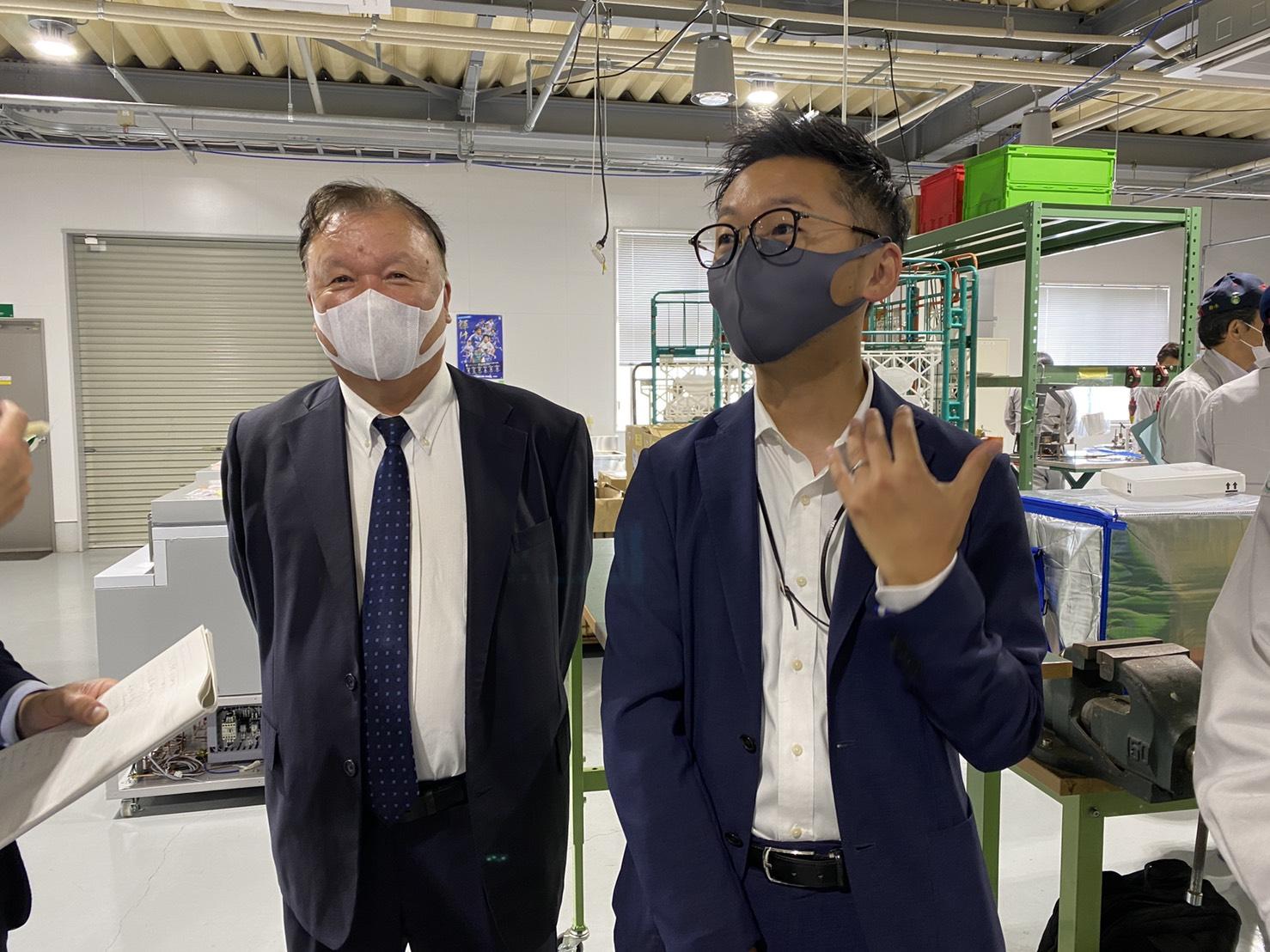

One of the bottleneck processes* in the manufacturing of the freezer was the use of brazing in the assembly of the key component known as a multi-stage evaporator (a device for vaporizing and evaporating chlorofluorocarbon gas required to achieve ultra-low temperatures). Until recently the assembly work was done by a single experienced technician, which limited the number of devices produced a day to two as it took approximately 270 minutes to complete one device.
*A process that takes the longest time and has the lowest production capacity and efficiency.
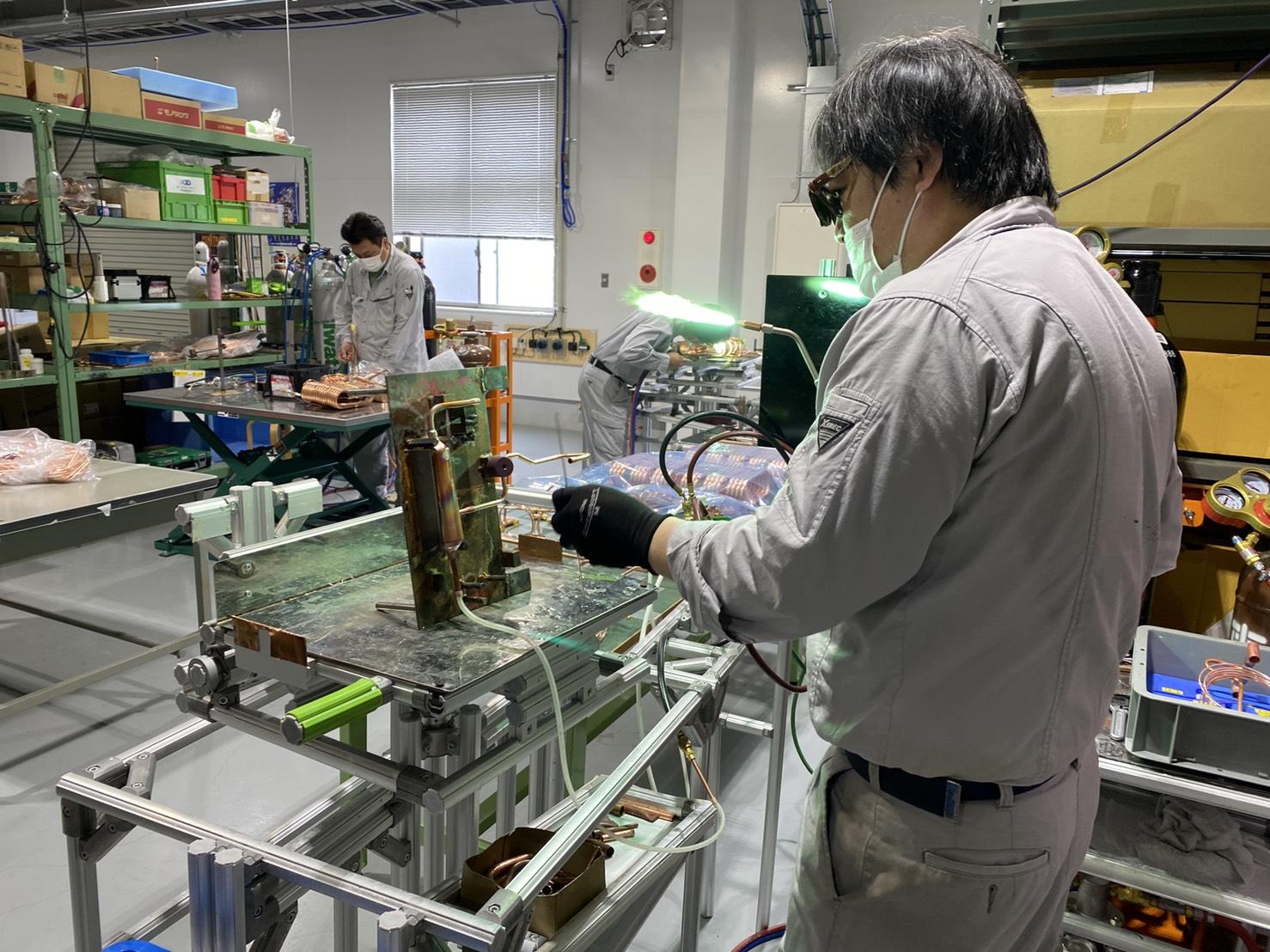
Miyajima from Toyota recalls his impression when he first entered the ADD workplace.
Miyajima
The actual operating time for one brazing operation is about five seconds, but the preparation time can be anything from 10 to 20 minutes. I thought it a waste of resources for a skilled person to be spending so much time. I wanted them to be able to spend more time on development (which is what the assembly technician is expected to be doing). Eliminating waste and fully leveraging the skills of the person is all part of the “respect for humanity” in the concept of TPS.
However, no-one in the Toyota support team had any experience of brazing. So they returned to Aichi, and set up a production line at Toyota, recreating the process.
Miyajima says, “What we did first was to try doing the job ourselves. Unless we did this we would never have understood the points that were causing the technician trouble.” He then laughs and adds, “But it was difficult and we couldn’t do it at all.” Seeing the Toyota staff all working with such dedication in this way eased any doubts the ADD technicians may have had initially.
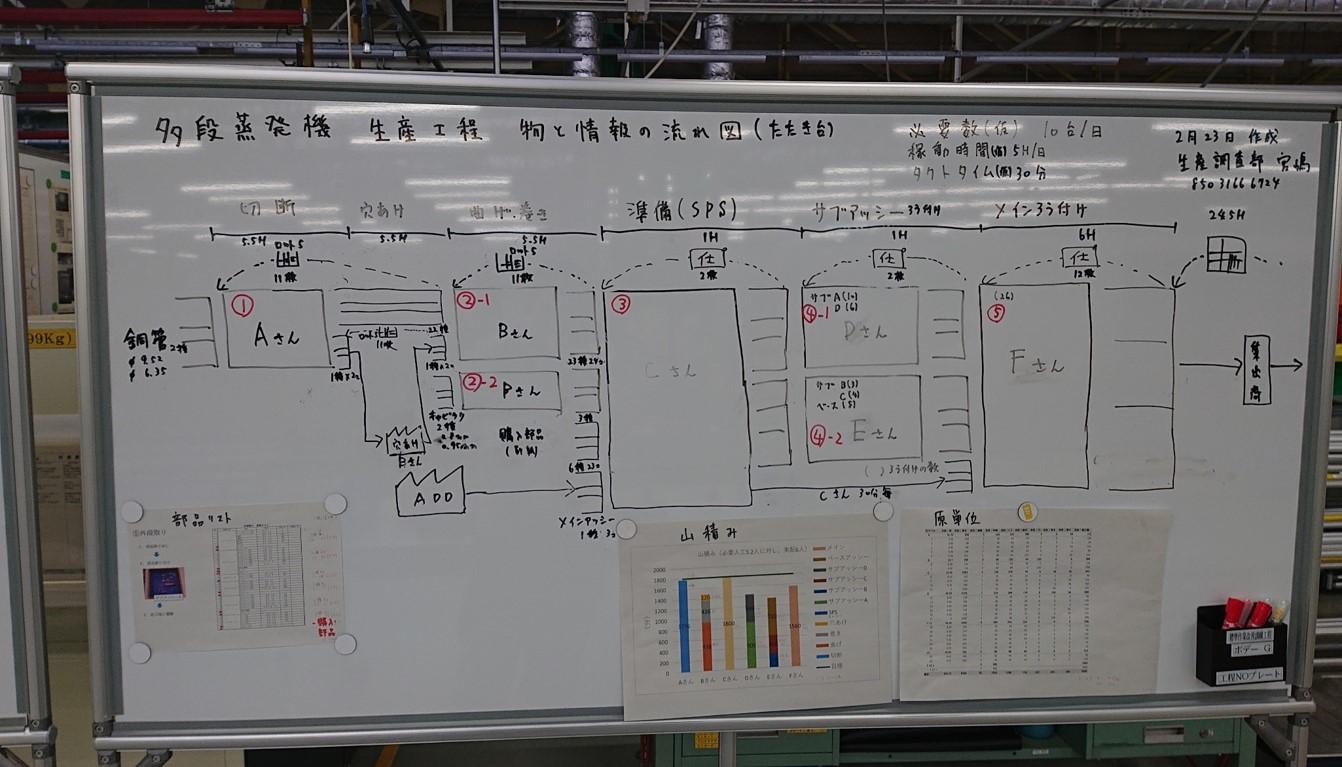
By engaging in discussions with the technician responsible for assembly work, it was possible to put a number of kaizen activities into practice. For example, in the past, the parts required for brazing were stored separately, which meant that they were often misplaced or had to be moved back and forth between storage and assembly locations. However, by organizing the set of parts to be made into a product in a specially dedicated box, it was possible to shorten preparation time.
The height of the workbench, which was not suited for the work and was forcing technicians to bend over, was increased, and was also made to rotate so that the technicians no longer had to move around.

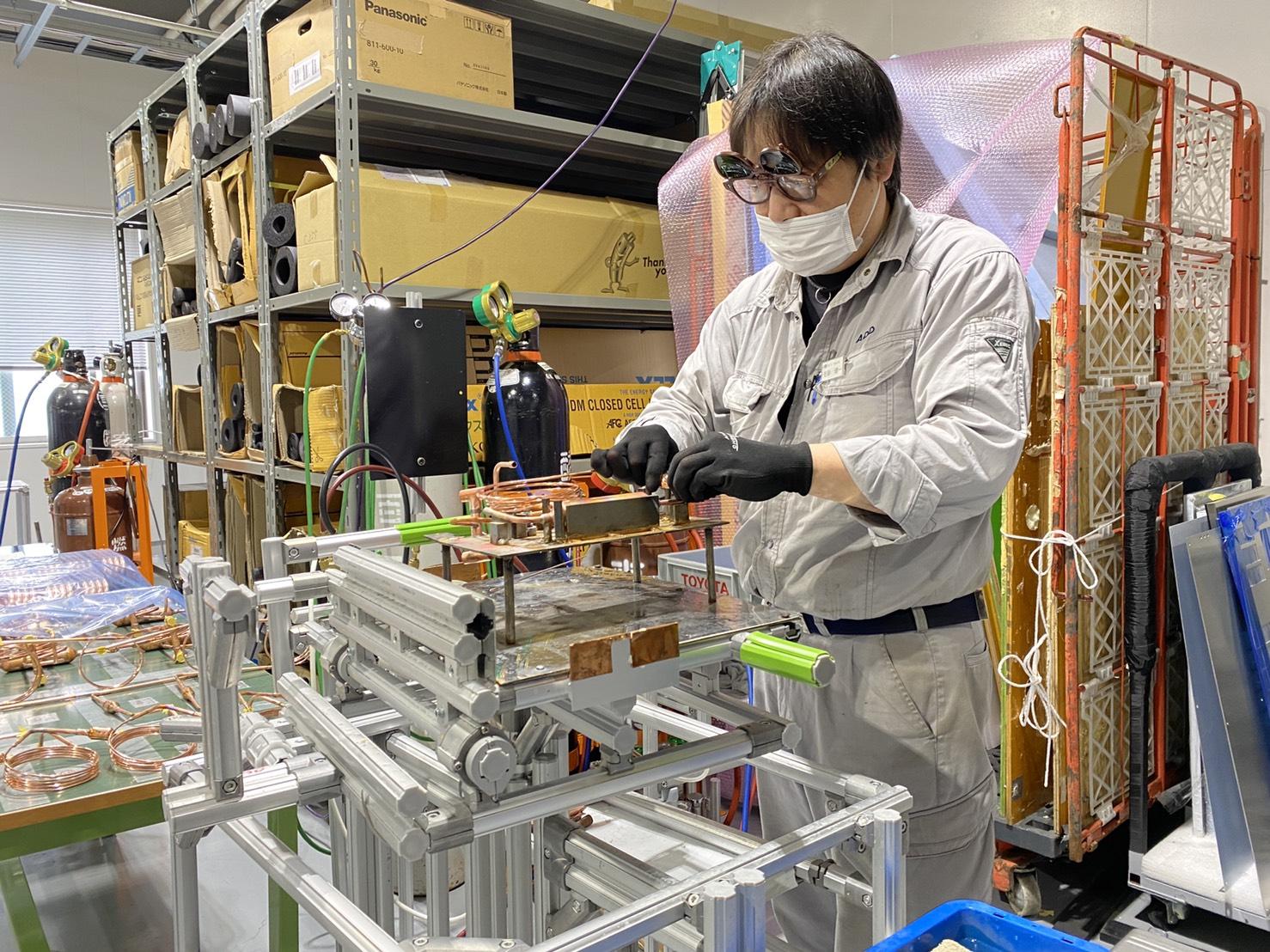
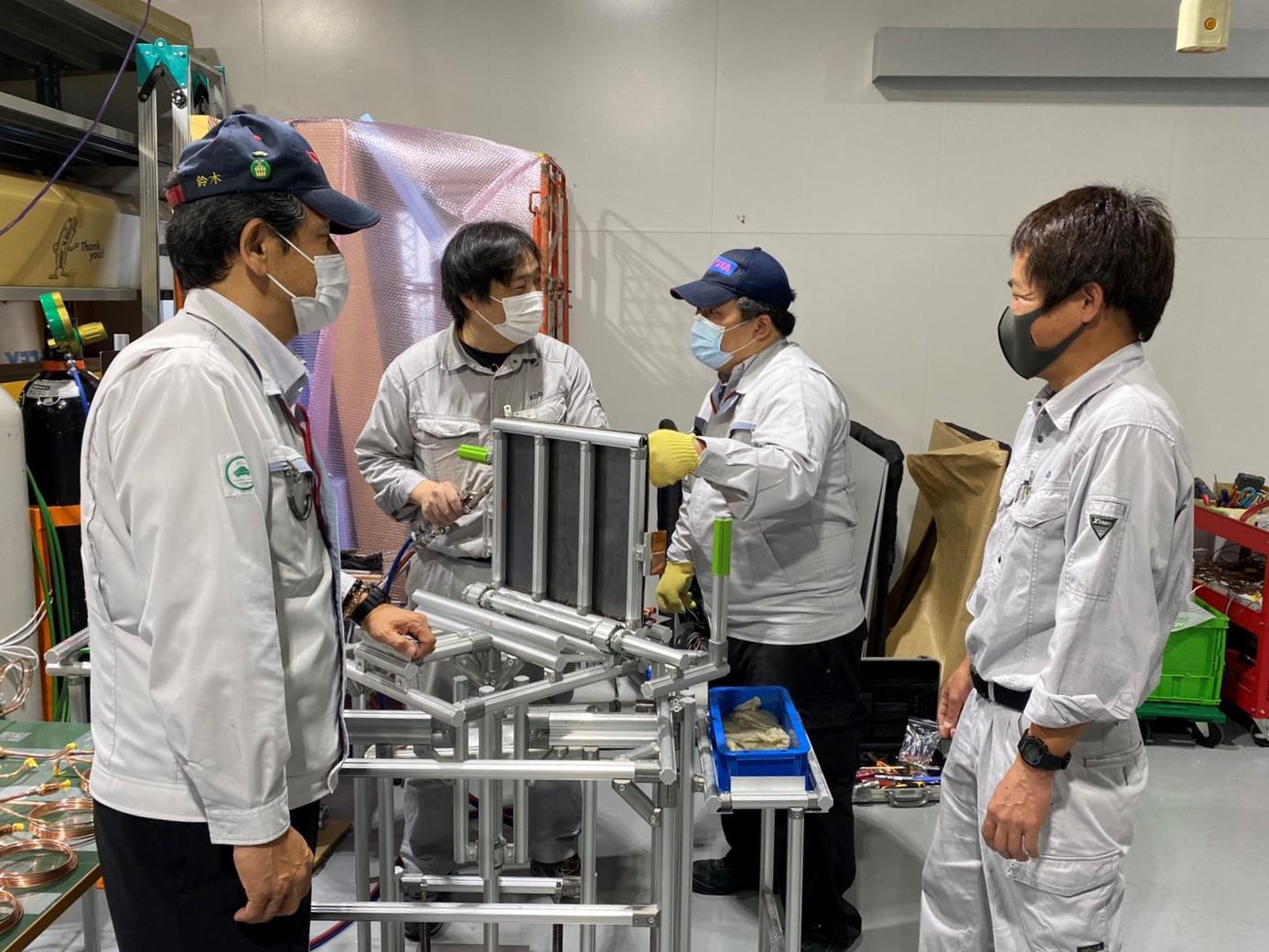
One of the members of the support team for this project was Hiroshi Suzuki, General Manager of the Global Production Center at Toyota. He spoke about the ways in which improvements were approached.
Suzuki
If you think that the person is bending over too much, you need to ask, “Shall we raise the bench? How would that be?” Arbitrarily going ahead with kaizen activities is only a “change for the worse.” Any improvements should not be top-down, but implemented through interactions and communication between people.
Thanks to the various kaizen activities that have been introduced, by the end of May, the time required to produce one device had been reduced from 270 to 120 minutes, shortened by more than half. Also, by increasing the number of technicians from one to two, a production structure has been created that enables up to 15 devices to be produced each day. “Interactions and communication between people” really do have the potential to enhance productivity.
Ensuring that citizens can return to daily life
So, returning to May 30, and the launch of mass vaccinations in Toyota City, when a blue cold storage box was delivered to the welfare facility at Tsutsumi Plant, representing the hopes and wishes of so many people involved.
At 10 a.m. people start arriving for their vaccination and entering the venue in swift succession. Although there don’t seem to be any major delays, Miyajima says enthusiastically, “There’s still much to do. We must continue to implement kaizen activities with the participation of everyone, including medical professionals, city hall officials, and venue managers. At Toyota it’s often said that, ‘After kaizen is the state of before kaizen.’ Today we actually altered the layout ten minutes after opening, and until the very last person has been vaccinated on the last day of the vaccination program, the process of kaizen will never end.”
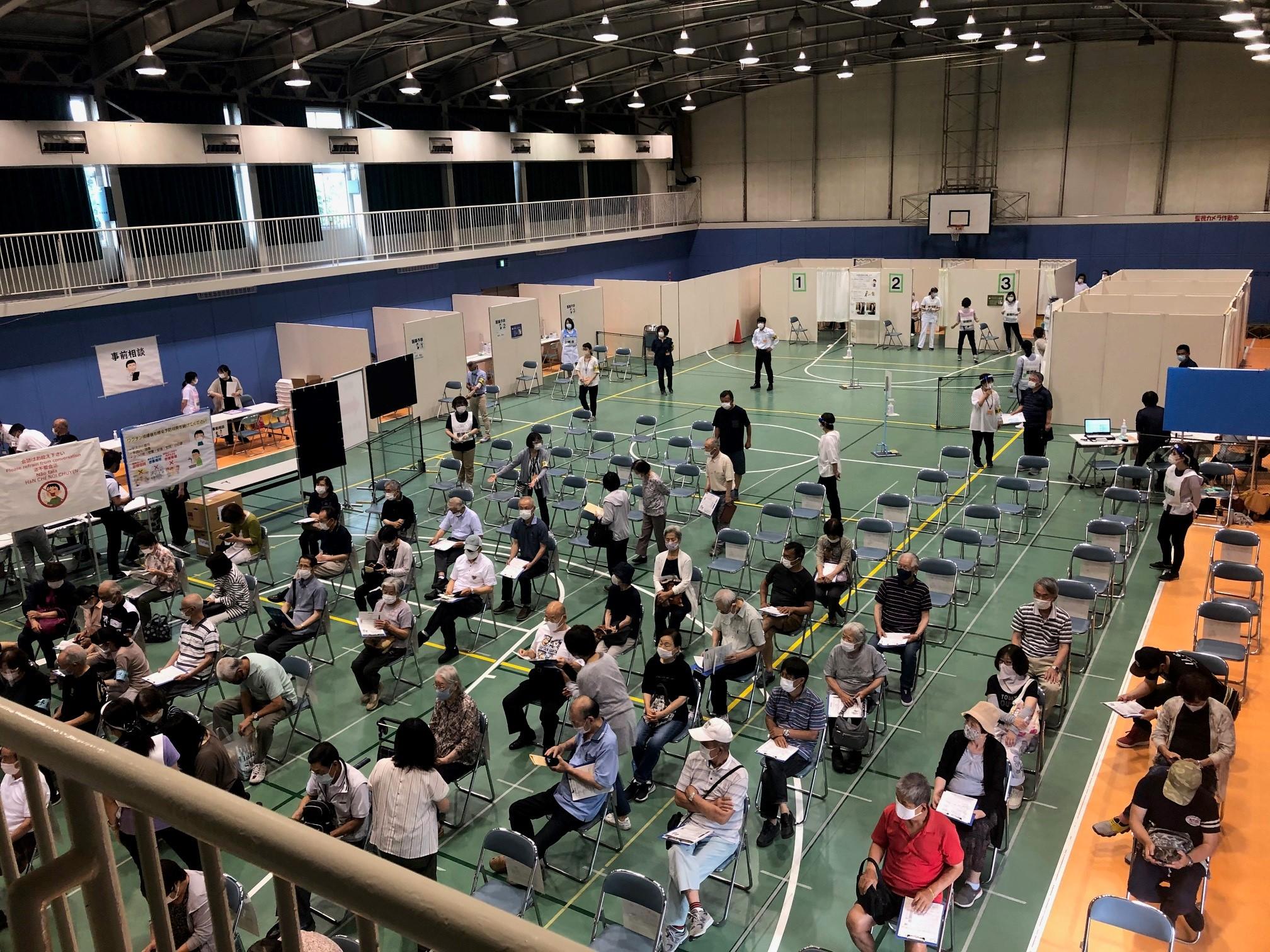
Vaccinations have now been continuing for two weeks. Changes have been made to the layout as well as the actions of the people working in the venue, especially medical personnel. As a result, the time required for each person to receive their vaccine, which used to be 30 to 40 minutes, has been shortened to 20 to 30 minutes from the time when they register at reception to when they leave the venue, including the over 15-minute waiting time after vaccination.
Also, the total number of people able to receive vaccinations at Toyota-owned facilities a day has increased from an initial 540 people at one venue, to 2,700 people across three venues.
However, the project is still a work in progress. With further kaizen activities, the ultimate target is to fix the time required for vaccination at 20 minutes per person, and increase daily vaccination capacity to more than 4,000 people across the three venues.
Moving forward, more mass vaccination venues using Toyota’s facilities will be set up in the areas surrounding Toyota City, and at the same time, the number of people to receive vaccination at each site will also be increased. The “Toyota City Model” has only begun, bringing together the combined power of the medical, government and private sectors. Kaizen will continue until the day when all citizens can return to their daily life with a peace of mind.